模具设计与制造专业毕业设计Word文件下载.docx
《模具设计与制造专业毕业设计Word文件下载.docx》由会员分享,可在线阅读,更多相关《模具设计与制造专业毕业设计Word文件下载.docx(16页珍藏版)》请在冰豆网上搜索。
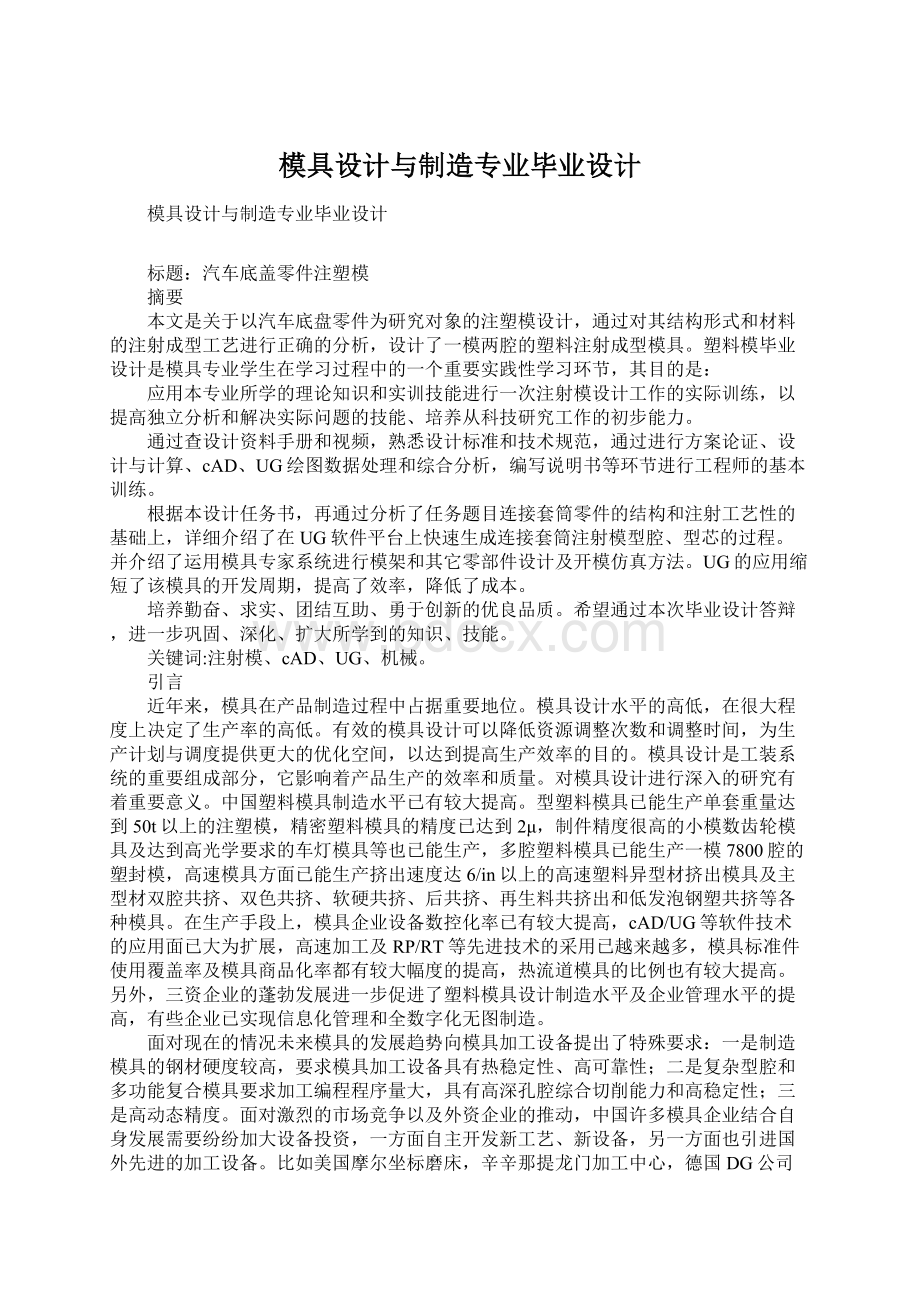
一是让学生掌握查阅资料手册的能力,能够熟练的运用cAD、UG等软件进行模具设计;
二是掌握模具设计方法和步骤,了解模具的注射工艺过程。
本书是根据《塑料成型工艺与模具设计》、《注塑成型及模具设计实用技术》、《塑料制品与模具设计》、《中国模具设计大典》等诸多参考资料编写而成。
运用UG、cAD软件设计出选定的塑料制品的图纸,由于缺乏经验、知识有限、时间仓促,该书难免出现一些不足之处,请老师和同学们多多指教,谢谢大家的支持。
本说明书由株洲职业技术学院模具设计与制造专业1201班宋平主编,谢冬和老师审核。
在编写过程中,参考了大量资料,也得到了多位老师指导和帮助,同时还得到了同学们的提示,特在此表示衷心的感谢!
一、对汽车底盘零件进行成型工艺分析分析
1塑料性能分析
塑料
品种:
ABS
基本特性:
ABS塑料)
典型应用范围
汽车,电冰箱,大强度工具,,娱乐用车辆如高尔夫球手推车等。
注塑模工艺条
干燥处理:
ABS材料具有吸湿性,要求在加工之前进行干燥处理。
建议干燥条件为80~90℃下最少干燥2小时。
材料湿度应保证小于0.1%。
熔化温度:
210~280℃;
建议温度:
245℃。
模具温度:
25-70℃。
。
注射压力:
500~1000Pa
注射速度:
中高速度
化学和物理特性
ABS是由丙烯腈、丁二烯和苯乙烯三种化学单体合成。
每种单体都具有不同特性:
丙烯腈有高强度、热稳定性及化学稳定性;
丁二烯具有坚韧性、抗冲击特性;
苯乙烯具有易加工、高光洁度及高强度。
从形态上看,ABS是非结晶性材料。
三中单体的聚合产生了具有两相的三元共聚物,一个是苯乙烯-丙烯腈的连续相,另一个是聚丁二烯橡胶分散相。
ABS的特性主要取决于三种单体的比率以及两相中的分子结构。
这就可以在产品设计上具有很大的灵活性,并且由此产生了市场上百种不同品质的ABS材料。
这些不同品质的材料提供了不同的特性,例如从中等到高等的抗冲击性,从低到高的光洁度和高温扭曲特性等。
ABS材料具有超强的易加工性,外观特性,低蠕变性和优异的尺寸稳定性以及很高的抗冲击强度。
2塑件造型及成型工艺性分析
产品分析与UG三维造型
图1为汽车底盖零件的产品图,材料为ABS,该零件属于中等批量生产,未注公差采取TS级精度,该零件对称性好,主体拉伸,抽壳,倒角等.
应用UG软件对该零件进行三维造型,基本操作步骤与过程为:
先进行71、122的拉伸,然后长边25°
,短边20°
的拔模,从上表面造型出R19与边相切的草图并向下拉伸13,后倒R4的角,在倒R8的角,最后拉伸上表面上的4个直径6的圆和两边直径6的圆。
图1汽车底盘零件产品图
成型工艺方案分析
该零件有上下通孔和两侧孔,,需要侧向抽芯。
成型零件的设计主要考虑型芯的嵌人式处理方法。
根据零件的结构特点,拟定如下工艺方案进行比较分析,最终确定设计方案。
分型面的确定。
选取分型面时,应考虑塑件脱模顺利,简化模具结构,使得设计出来的结构零件便于加工,并且保证塑件表面精度。
分型面如图1所示为A-A分型面,塑料为上下分模动模,这使模具的结构变得简单,因而选定该方法为此模具的分型设计方案。
因此模有侧空,故侧型芯设在定模上,所以此模分为三部分,动模、定模和侧型芯合。
型腔布局。
由于该零件尺寸较大,又是中等批量生产,可采用1模2腔,模具型腔和结构较简单,可以降低模具制造成本。
浇注系统。
浇注系统是塑料熔体自注射机的喷嘴射出后,到进入模具型腔以前所流经的一段路程的总称。
它的作用是使来自喷嘴的熔体平稳而顺利地冲模、压实和保压。
正确设计浇注系统对获得优质的塑件极为重要。
浇口形式的设计,应使塑件的各向异性最小。
该成型模可设计为如图2所示潜伏式浇口,从塑件上端孔进料,模具型腔的加工简单、浇口容易去除,不影响塑件外观,模具的结构也相对较简单。
图2潜伏式浇口
推出机构。
由于该塑件相对深度较大,塑件对动模型芯的包紧力不大,因此设计一副由推杆推出的推出机构。
因为此零件斜面较多,推杆能更好的实现对此零件的应用,就能平稳顶出塑件,这样塑件不易发生顶出变形,且能确保塑件质量,因此推杆推出为本次模具设计的优选方案。
3成型设备选用及校核
注塑机的选用
计算塑件的体积、质量
经UG软件测得塑件的体积V=20440.849577337^3,=0.160064934g。
确定模具型腔数量
塑件的生产批量为中等批量生产,且塑件精度要求不高,因此,应采用一模多腔,为使模具尺寸紧凑,确定型腔数目为一模两腔。
选择注射机
根据公式Vax=
式中Vax——模具的最大注射量
n——型腔数量
Vs——塑件体积
Vj——浇注系统凝料体积
——注射机最大注射量利用系数,一般取=0.8
已知n=1,Vs=20.44c3,估计Vj=3.066c3
则Vax=c3
=43.946c3
查教材中表3-3,初步选择注射机XS-Zy-125
明确注射机的规格参数:
最大注射量60c3
注射压力122Pa
最大开模行程180
模板尺寸330×
440
锁模力500n`
模具厚度最大200、最小70
拉杆空间190×
300
喷嘴尺寸圆弧半径R12、孔直径φ4
定位孔直径φ100
顶出形式顶杆顶出
制定注射成形工艺参数
查表3-1,PS的注射成形工艺参数如下:
温度
喷嘴温度160~170
料筒温度前段170~190,中段~,后段140~160
模具温度20~60
压力
注射压力60~100
保压压力30~40
时间
注射时间0~3
保压时间15~40
冷却时间15~30
成形周期40~90
注射机的校核
注射量的校核
在模具设计时,必须使得在一个注射成型周期内所需注射熔体质量在注射机额定注射量的80%内。
在一个注射成型内需注射入塑料熔体的质量为塑件质量和浇注系统质量的总和:
最大注射量是指注射机一次注射塑料的最大容量。
设计模具时,应保证成型塑件所需的总注射量小于所选注射机的最大注射量,即
n+1≤p
经算得符合要求!
锁模力的校核
为了防止在注射成型时因锁模不紧而发生溢边、跑料现象,在高温熔体充满型腔时产生的轴向推力T应小于注射机的额定锁模力T。
锁模力可按下式校核:
F≥P
式中:
P——塑料注射压力N经查阅资料
ABS注射成型所型腔压力30Pa既P=30/80%=37.5Pa
A——单个塑件在分型面上投影面积
A——浇注系统在分型面上的投影面积
F——注射机额定锁模力1000N
投影面积计算:
估算:
nA=2×
8.6=17.2
A=
P=
同样,XS-Zy-125的额定注射压力120Pa>37.5Pa,
故能满足ABS的注射压力要求。
模具厚度H与注射机闭合高度校核
H<H<H
H——模具的闭合高度,H=285
H——注射机允许最小模具厚度,H=200
H——注射机允许的最大模具厚度,H=300
经校核满足要求。
注射机开模行程的校核
注射机开模行程应大于模具开模时取出塑件所需开模距。
即满足下式:
S------模具所需开模距离
H——塑料脱模需要的顶出距离,H=21
H——塑件厚度,H=35.5
a------取出浇注系统凝料所需浇口板与固定模板之间的距离,
a=40
S---注射机的最大开模行程,为300
则S=H+H+a+8=21+35.5+40+8=104.5<S
二、塑件分模设计
1模具型腔布局设计
建立模具工程目录叶新建模具型腔,选择公制模板→定位参照零件,改变其坐标方向,使模具坐标系统的Z轴沿零件的轴线指向正方向升增加毛坯工件升设置收缩率,如图3所示。
利用主分型面分割出上、下型腔模具体积块,再从上型腔模具体积块中分别分割出2个侧抽芯体积块。
然后对侧抽芯镶件进行处理,增加定位台阶。
如图4所示。
图3创建模具零件型腔图4侧抽芯镶
2分型面的设计
塑料在模具型腔凝固形成塑件,为了将塑件取出来,必须将模具型腔打开,也就是必须将模具分成两部分,即定模和动模两大部分。
定模和动模相接触的面称分型面。
通常有以下原则:
分型面的选择有利于脱模:
分型面应取在塑件尺寸的最大处。
而且应使塑件流在动模部分,由于推出机构通常设置在动模的一侧,将型芯设置在动模部分,塑件冷却收缩后包紧型芯,使塑件留在动模,这样有利脱模。
如果塑件的壁厚较大,内孔较小或者有嵌件时,为了使塑件留在动模,一般应将凹模也设在动模一侧。
拔模斜度小或塑件较高时,为了便于脱模,可将分型面选在塑件中间的部位,但此塑件外形有分型的痕迹。
分型面的选择应有利于保证塑件的外观质量和精度要求。
分型面的选择应有利于成型零件的加工制造。
此模具成型零件包括:
上、下2个型腔、4个侧型芯,分型面为分割上下型腔的主分型面。
主分型面的设计稍微复杂些,可先用复制和拉伸生成单个曲面,然后再通过多次合并而得,如图5所示:
图5主分型面
3浇注系统设计
普通浇注系统由主流道、分流道、浇口等组成。
在设计浇注系统之前必须确定塑件成型位置,可以才用一模一腔,浇注系统的设计是注塑模具设计的一个重要的环节,它对注塑成型周期和塑件质量都有直接的影响,设计时必须按如下原则:
浇口开设部位力求对称,防止模具承受偏载而造成溢料现象。
浇口的排列要尽可能地减少模具外形尺寸。
系统流道应尽可能短,断面尺寸适当:
尽量减少弯折,表面粗糙度要低,以使热量及压力损失尽可能小。
满足型腔充满的前提下,浇注系统容积尽量小,以减少塑料的耗量。
浇口位置要适当,尽量避免冲击嵌件和细小型芯,防止型芯变形浇口的残痕不应影响塑件的外观。
主流道的设计
注射机喷嘴到分流道的进料通道,是塑料熔体进入模具最先经过的部位,其形状、大小直接影响塑料的流动速度和填充时间,主流道的形状为圆锥形,以便熔体的流动和在开模时凝料的顺利取出。
主流道的尺寸:
)主流道的长度:
模具L应尽量合理,本次设计中初选95进行设计。
)主流道小端的直径:
d=注射机的喷嘴尺寸+==3.5
)主流道大端直径:
d=d+2Ltan5式中
)主流道球面半径:
)球面的配合高度:
h=3
)为使主流道中的熔料顺利的流入分流道,可在出料口的末端设计半径r=3。
分流道的设计
分流道是连接主流道和浇口的进料通道,其作用是通过浇道截面及方向变化,使熔体平衡地转换流向,进入模具型腔,分流道的截面应尽量使比表面积小、热量损失小、摩擦阻力小。
分流道的布置形式在设计时应考虑尽量减少流道内的压力损失尽可能的避免熔体的温度降低,同时还要考虑分流道的压力平衡,应此采用平衡式分流道。
分流道的形状
流道的截面形状会影响到塑料在浇道中的流动以及流道內部的熔融塑料的体积。
常用的有圆形、梯形、U形、六角形,为了便于加工和凝料脱模分流道大多设计在分型面上。
本设计采用U形截面,其加工工艺好且塑料熔体的热量散失,流动阻力均不大。
分流道的长度
分流道的长度应尽可能短,且弯折少,以便减少压力损失和热量损失。
当分流道设计得比较长时,其末端应有冷料穴,以防前锋冷料堵塞浇口或进入模腔,造成充模不足或影响塑件的熔接强度。
根据结构设计取其长度
分流道的表面粗糙度
由于分流道中与模具接触的外层塑料迅速冷却,只有内部的熔体流动状态比较理想,因此分流道表面粗糙度不能太低,一般了Ra1.6u左右,这可增加对外层塑料熔体的流动阻力,使外层塑料冷却皮层固定,形成绝热层。
浇口的设计
浇口是连接流道与型腔之间的一段细短通道,调节控制料流速度、补料时间、及防止倒流等作用。
浇口形状、尺寸和进料位置直接影响塑件成型质量。
因此正确设计浇口是提高塑件质量的重要环节。
总的要求是:
使熔料以较快的速度进入并充满型腔,同时在充满后能适时冷却封闭,因此浇口截面要小,长度要短,这样可以增大料流速度,快速冷却封闭,且便于塑件与浇口凝料分离,不留明显浇口痕迹,从而保证塑件外观质量.此外浇口设计需遵循下述原则:
浇口尺寸及位置选择应避免熔体破裂而产生的喷射和蠕动。
浇口位置应有利于流动、排气和补料。
浇口位置应使流程最短,料流变向最少,并防止型芯变形。
浇口位置及数量应有利于减少熔接痕和增加熔接强度。
浇口位置应考虑定位作用对塑件性能的影响。
浇口位置应尽量开设在不影响塑件外观的部位如浇口开设在塑件的边缘、底部和内侧。
根据分析结果,可以采用如下几种浇口类型。
方案一:
在塑件顶部中心位置采用直接浇口直接进料,熔体压力损失小,成型容易,常用于成型大而深的塑件。
由于该注塑件外观要求光滑、美观。
而直接浇口一般用于一模一腔,且浇口处易产生裂纹,浇口凝料切除后在塑件上所留疤痕较大,故塑件成型后塑件表观质量不是很好。
方案二:
采用侧浇口直接开设在模具分型面上,从注塑件的边缘进料。
其截面形状简单、易于加工、便于试模后修正,但易在塑件的外表面留有浇口痕迹。
且浇口不是开设在注塑件的最佳浇口区域,故塑件成型质量不是很好,内部易产生,气孔、气泡等缺陷。
方案三:
采用潜伏浇口,即在推杆上开设二次浇口,使二次浇口的未端与塑件内壁相通,可避免浇口痕迹,成型后塑件处观质量较好,但浇口压力损失大,必须提高注射压力。
且浇口加工困难。
方案四:
采用点浇口进料,浇口附近变形小,容易平衡浇注系统,浇口截面小,成型后对塑件外观质量影响不大,适合三板式模具,宜用于成型流动性能较好的热塑件塑料。
在本设计中塑料制件质量较大,ABS流动性较好,有较好注射工艺性,所以为了确保各制件的质量,塑件利用旋转在上型腔上切出主流道,再利用流道设计分别生成潜伏式分流道及浇口。
如图7所示。
图7潜伏式浇口
4排气系统的设计
塑料熔体在注入型腔的同时,必须置换出型腔内的空气和从熔体中逸出的挥发性气体。
注射模组成部分的排气槽如果设计不合理,将会产生如下弊病:
增加熔体充模流动的阻力,是型腔无法被充满,导致制件棱边不清晰。
在制件上呈现明显可见的流动痕和熔接痕,使制件的力学性能降低。
滞留气体使制件产生银纹、气孔、剥层等表面质量缺陷。
型腔内气体受到压缩后产生的瞬时局部高温,使熔体分解变色。
甚至炭化烧焦。
由于排气不良,降低了熔体的充模速度,延长了注射成形周期。
通常有三种排气方式:
①利用配合间隙排气;
②在分型面上开设排气槽;
③利用排气塞排气。
该模具可采用间隙排气的形式。
5模具成型零件工程图设计
型腔二维工程图
因此零件除了型腔外还有4个侧型芯,故型腔二维工程图有2个图。
如图9、图10。
图9型腔二维工程图
图10侧型芯二维工程图
型芯二维工程图
图11型芯二维工程图
三、导向机构及脱模机构的设计
1导向机构设计
导向机构的作用有:
定位作用
在模具装配过程中也会起到定位的作用,即便于模具的装配和调整。
导向作用
合模时,首先是导向零件接触,引导动、定模或上、下模准确闭合,避免型芯进入型腔造成成型零件的损坏。
承受一定的侧向压力
塑料熔体在充型过程中可能产生单向侧向压力或受成型设备精度低的影响,导柱将承受一定的侧向压力,以保证模具的正常工作。
除了动模、定模之间设导柱、导套外,一般还在动模座板与推板之间设置导柱和导套,以保证推出机构的正常运动。
导柱结构的技术要求
导柱的导向部分的长度应比凸模端面的高度高出8~12,以免出现导柱未导正方向而型芯先进入型腔的情况。
导柱前端应做成锥台形或半球形,以使导柱能顺利地进入导向孔。
由于半球形加工困难,所以导柱前端形式以锥台形为多。
导柱应具有硬而耐磨的表面和坚韧而不易折断的内芯,因此多用20钢或者T8、T10钢,硬度为50~55HRc。
导柱固定部分的表面粗糙度为Ra0.8u,导向部分的表面粗糙度为Ra0.8~0.4u。
导柱的配合与安装
导柱固定端与模板之间一般采用H7/6或H7/6的过渡配合,导柱的导向部分通常采用H7/f7或H8/f7的间隙配合。
2脱模机构设计
脱模机构的设计原则
脱模机构是注射成型后,使塑件从凸模或凹模上脱出的机构。
它是由一系列推出零件和辅助零件组成,可具有不同的的脱模动作。
其设计原则:
保证塑件不因顶出而变形损坏及影响外观。
在设计时必须分析正确分析塑件对模具粘附力的大小和作用位置,以便选择合适的脱模方式和恰当的推出位置,使塑件平稳脱出。
同时脱出位置应尽量选择塑件内表面或隐蔽处,使塑件外表面不留推出痕迹。
为使推出机构简单、可靠,开模时应使塑件留在动模,以利于注射机移动部分的顶杆或液压缸的活塞推出塑件。
推出机构运动要准确、灵活、可靠,无卡死和干涉现象。
机构本身应有足够的刚度、强度和耐磨性。
脱模力的计算
推出方式的确定
本模具制件脱模方式采用顶杆推动滑块脱模,
脱模力包括两部分,一部分为制品对型芯抱紧的脱模阻力Qc,一部分为封闭壳体脱模需克服的真空吸力Qb。
Qc=
式中E——塑料的拉伸弹性模量,可取2.1pa;
——塑料的平均成型收缩率,取0.68%;
υ——塑料的泊松比,取0.42;
f——脱模斜度的修正系数,f=≈0.6;
f——制品与刚才表面之间的静摩擦因数,取0.3;
t——制品厚度,t为2;
h——型芯脱模方向的高度,h为21;
计算结果Qc=286.2N。
Qb=0.1Ab=16N
式中Ab——型芯的横截面积,可取1602。
所以,总的脱模力为2X=604N。
3推杆的设计与计算
推杆脱模机构是最简单、最常用的一种形式,具有制造简单、更换方便、推出效果好等特点。
推杆的截面形状;
可分为圆形,方形或椭圆形等其它形状,根据塑件的推出部位而定,最常用的截面形状为圆形;
推杆又分为普通推杆和成型推杆两种,前者只是起到将塑件推出的作用,后者不仅如此还能参与局部成型,所以,推杆的使用是非常灵活的。
)推杆尺寸计算:
本设计采用的是推杆推动哈夫块将制件推出,在求出脱模力的前提下可以对推杆直径预算并进行强度校核。
本设计采用的是圆形推杆,圆形推杆的直径由欧拉公式简化为:
d=≈5.2
式中d——推杆直径;
n——推杆的数量,取6;
——安全系数,取=1.5;
L——推杆长度,根据模架高度,大约取80;
E—推杆材料的弹性模量,取E=2.1×
10P
F—总的脱模力,F=604N。
对其进行强度校核,推杆材料为45号钢,式中许用应力为[]=58pa
d≥即d≥
)推杆的固定形式:
推杆的固定形式有多种,但最常用的是推杆在固定板中的形式,此外还有螺钉紧固等形式。
此设计利用固定板固定。
)推出机构的复位:
脱模机构完成塑件的顶出后,为进行下一个循环必须回复到初始位置,目前常用的复位形式主要有复位杆复位和弹簧复位。
本设计采用复位杆复位机构。
所以,实际设计时推杆的直径采用6。
推杆的长度
--型芯固定板的厚度60
--推杆顶出制件的