容器放样下料工艺规程文档格式.docx
《容器放样下料工艺规程文档格式.docx》由会员分享,可在线阅读,更多相关《容器放样下料工艺规程文档格式.docx(11页珍藏版)》请在冰豆网上搜索。
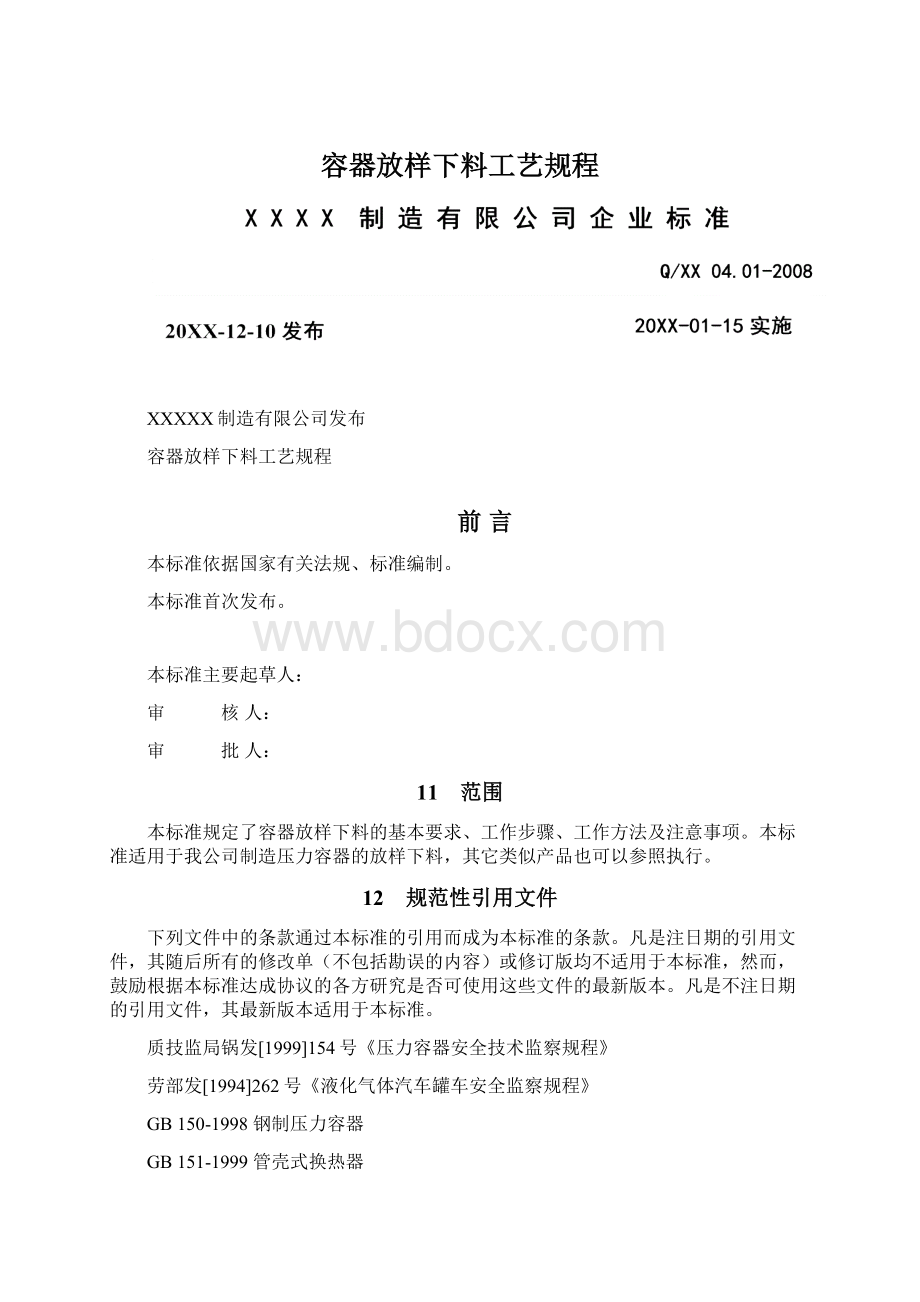
JB/T4710-2005钢制塔式容器
JB/T4731-2005钢制卧式容器
JB/T4746-2002钢制压力容器用封头
JB4744-2000钢制压力容器产品焊接试板的力学性能检验
13 一般要求
13.1 容器放样下料除满足本标准外,还应符合产品有关标准及设计图样的规定。
13.2 铆工必须看懂工程图纸,对图形尺寸、材质、数量要清楚掌握。
13.3 严格执行容器专用技术条件及图纸和工艺技术要求。
13.4 下料必须做到“四不”、“四检”。
“四不”:
a)图纸不清不放样;
b)材料不清不号料;
c)材料不经检查员检查合格不号料;
d)代料没有通知单不号料。
“四检”
a)检查图纸尺寸和放样抄料尺寸;
b)检查所用材料的规格、钢号和材料标记;
c)检查样板和图形尺寸;
d)检查抄料与号料尺寸、数量。
13.5 施工中的图纸修改,必须由工艺员修改,修改者在修改处签字,对于修改部分如已经下完料,要重新下计划。
14 压力容器焊接接头位置的一般要求
14.1 凡我公司制造的液化气体汽车槽车等压力容器产品,筒节长度下料最短尺寸除符合本标准要求外,还应符合相关标准的相应条文的规定和相应的专用技术文件。
14.2 筒体焊接位置应符合以下要求
筒节长度应不小于300mm,组装时,相临筒节A类接头焊缝中心线间外圆弧长以及封头A类接头焊缝中心线与相临筒节A类接头焊缝中心线间外圆弧长应大于钢材厚度的3倍,且不小于100mm。
内件与筒体焊接的焊缝边缘与筒体纵环A、B类接头焊缝边缘的距离应不小于筒体厚度,且不小于50mm。
4.2.3卧式容器环向B类焊接接头应尽量位于支座之外,纵向A类焊接接头位于壳体下部140°
范围之外,支座焊缝边缘与筒体A、B类接头焊缝边缘距离应大于筒体壁厚且不小于50mm。
4.3封头拼接接头焊缝的布置应符合以下要求:
4.3.1封头由二块或左右对称的三块钢板拼接制成时,其拼接焊缝与封头中心线的距离应小于公称直径的1/4。
(见图1)
图1
4.3.2封头各种不相交的拼接焊缝中心线间距离至少应为封头钢板厚度的3倍,且不小于100mm,封头由成型的瓣片和顶圆板拼接制成时,焊缝方向只允许是径向和环向的(见图2),先拼板后成形的封头拼接焊缝,在成形前应按要求打磨。
4.3.3瓣片应用整板制造,不得拼接。
图2
4.4应尽量避免在容器焊接接头及边缘附近开孔,如必须开孔,则应对以开孔中心为圆心,1.5倍开孔直径为半径的圆中所包容的焊接接头,进行全部射线或超声波检测合格(但被检测的位置应由铆工通知检查员,做第一次无损检测),并在号料板料上做上标记。
4.5容器A、B类接头焊缝被支座垫板或开孔步强圈、内件等部件覆盖时,焊缝被覆盖部分应打磨至与母材齐平,且经全部射线检测合格(其检测的位置应由线图通知检查员,做第一次无损检测),并在号料板料上做上标记。
15 零部件加工裕量
零部件经火焰切割后需加工,尺寸加工裕量见表1。
表1
钢板厚度
mm
火焰切口宽度
加大量
火焰切割后,只经加工,不经火曲煨制的零部件尺寸加大量
火焰切割后,经火曲煨制又经加工的零部件尺寸加大量
零部件尺寸
总加大量
14~25
6
φ400以下
12
φ400~φ1000
18
14
φ1001~φ2000
22
φ1001以上
16
φ2001~φ3500
26
26~36
8
20
24
28
37~45
9
15
21
17
25
19
29
46~60
10
30
15.1.1.1.1 注:
(1)总加大量,系指零件外径尺寸加大部分或此零件内径减少部分。
(2)凡法兰或垫圈其加工后之内径小于φ50,火焰不切割其内孔。
(3)凡需剪切或铣制的零部件,周边需要加工时,可留出3~5mm为加工裕量。
(4)凡是火焰切割的型钢(角钢、槽钢、工字钢、管子等)不需要加工时,留出5mm火焰口裕量。
16 样板的制作
6.1在放样时,应熟悉并进一步了解图纸各部图形、工艺及工料计划(包括代料)三者有无不符之处。
6.2制作的样板应平直,做完后避免锤击以免变形,做样板时,直角尺应与样板贴严,并以通用代号标在样板上。
6.3制作火曲的零部件长样板时,没有其他孔时,在样板上以草图注明详细加工尺寸,由火曲划线切断。
6.4放样和样板制做后,应再进一步核实尺寸,如果利用旧样板时,必须擦净原有的字样和图形,以免发生差错。
6.5按照工件的实际情况,做出适当的内卡、外卡、角度卡样板或模型卡等样板,并详细地标注工程号(产品编号)、图号、件号、材质、规格、数量和反正面等。
6.6在外轮廓尺寸面积为500mm2之范围内做出零件的实形样板转下序切割,不必号料,100mm以下的角钢不号料(端面有角度的提供样板),样板尺寸应清晰易懂,不得用铅笔写。
6.7所有的角度卡样板和其它卡样板,在样板上和板料上无法用文字表示清楚者,必须直接向操作工序的操作人详细交代清楚。
6.8一般不是整圆或半圆的奇形样板,小形的零部件均做全型卡样板(即在样板上有曲线、切线、中心线等),不能做全型的要在样板上划草图表示各部尺寸,并在样板的有效部位上,涂以铅油表示。
6.9制作盘簧管、蛇管的卡样板时,一律做内卡或实形样板,并在样板上注明清楚按图施工,样板规格均以实际情况选择大小及铁皮厚度。
6.10封头需要做卡样板,一般可做五个:
1)打凸内卡样板;
2)翻边外卡样板;
3)翻边胎外卡样板;
4)圆周外卡样板;
5)圆周胎外卡样板。
6.11样板的写法与做法以图3为例:
6.11.1该设备结构由椭圆形封头、锥形封头、筒体、设备法兰、角钢圈、翻边锥形、蛇形管、盘簧管、人孔、弯管等组成,是具有代表性的设备。
6.11.2以图3为例说明样板的制作和表示方法,具体方法见表2和图4。
图3
表2
件号
样板名称
规格
1
锥形底
S=8
2
角钢圈
∠652×
6×
φ999
3
筒体
Dn1000S=8
4
弯管
φ57×
5
法兰
φ1100/φ1018S=25
人孔
φ520/φ418S=20
7
人孔法兰
封头
∠752×
8×
φ1018
翻边锥形底
11
蛇形管
盘簧管
φ32×
3×
φ800
17 号料要求
7.1号料前检查好样杆、样板是否弯曲和其它缺陷,并检查预号料的材料牌号规格、表面质量、厚度等,不满足图纸要求不得号料,并做好材料标记转移工作。
7.2检查和熟悉样杆、样板、抄料所注明的一切字样,样板上如有原始字迹及符号要擦净后再号料。
图4
7.3放样下料的四检制度
7.3.1核实总图、部件图及节点放大图的尺寸是否一致,图纸中的材料与计划表的要求是否一致。
7.3.2抄料、放样、样杆、样板等尺寸与图纸尺寸是否一致,样板、样杆与实样对照。
7.3.3检查号完的零部件尺寸,不得凭记忆,如3150,误记为3510等造成差错。
7.3.4检查后续的开孔位置,并注意组对的差错,如筒节四个中心,设备法兰密封面型式和螺栓孔位置。
7.4拉粉线式,两端应拉紧,提稳后垂直向下弹,如有模糊不清之处,擦掉重弹,划的尺码粉线不能有偏差,使用的各种尺类,如盘尺、卷尺等都应检查是否完好且在检定周期内。
7.5号料之前应确认材料标记,专料专用,符合图纸要求,特别是特殊的图形,要求先号大料后号小料,便于穿插套号互相颠倒,合理用料(注意是否能切)。
7.6号料时所有的焊接接头坡口,均按焊接接头坡口暂行规定或焊接工艺卡要求执行,并用符号表示,特殊按图面要求。
7.7钢板有曲线时,可用曲线符号表示,不加注明为反曲,正曲必须注明。
7.8经射线检测和工程数量两台以上的设备号料时要注明第一、二、三……台,对于试件的尺寸规定按JB4744-2000标准要求和焊接工艺要求执行。
7.9对称的设备和零部件。
必须注明分开,数量较多的零件,制造上又无经验的,应先提出试制,试制数量按实际情况确定,合格后大批号料。
7.10直径较大的储罐,号料时应分八个中心,便于组装检查,凡属部件交货的工程,所有的零件用钢印打上字头,便于安装组对;
筒体、锥体分片交货应适当地留出非加工余量。
7.11无折边球形封头的齐边,使用地规或划规,划完之后,按计算的圆周长度用盘尺检查一次,如装在设备之内,直径应缩小2mm~4mm。
7.12气割的厚钢板筒体下料,当连续切割时应留有足够的断口余量。
——厚度在S=25mm~36mm,每条切缝加大5mm。
——厚度在S=37mm~45mm,每条切缝加大6mm。
——厚度在S=46mm~60mm,每条切缝加大7mm。
7.13如因板料小,为防止变形和焊缝收缩等,可先号成毛坯料,拼接平直后再次号料,对于筒体、方箱等号料,便于组装检查;
容器筒体号料,四周边缘均需划50mm标准线,打上冲印,较大的矩形板料,四角打上50mm标准点。
7.14用样杆号孔及在角钢、筒体上号在一条基准线的孔时,必须先由开始点,按增加数字计算,其尺寸以连锁方式,将其全长算好,不得单独分段进行。
7.15圆形罐体、管件号料时标四个中心线,如圆直径较小的图形管件均以卷圆符号表示。
7.16凡是架于所有的铆钉孔,均按铆钉直径加大1.5mm~2mm,凡是重要的有压设备,如锅炉、汽包等所用的铆钉孔应按铆钉杆直径缩小2mm~3mm,为二次铰孔找正用,并需规孔。
7.17线图号料通用符号:
表3
序号
号料线形
号料符号
中心线
正或反曲面
卷圈曲线
打凸
位置线
要求一边的切线
要求两边的切线
7.18排版图的划法:
1)划设备坐标线(中心线);
2)划设备上下两端线;
3)有了以上轮廓线则将其所有接管位置和其它位置线均划好;
4)根据板料规格,再进行排版,注意错开焊缝。
7.19塔体划线:
1)先用样板检查塔节的椭圆度;
2)塔节放在平台上,用直尺或划线盘检查上下两端的平行度,平行度的公差为±
2mm,如果超差应划齐边线,并铲掉磨平。
3)为便于组对塔盘支承圈,在与封头相焊的两端塔节内部划出50mm基准线,使其与设备中心线垂直,同时将四条中心线返到筒体内部。
4)划线时应划支承圈水平线,不应划塔板水平线。
7.21号矩形板料四边应互相垂直,其两条对角线长度差小于2mm。
8有色金属下料
8.1不锈钢、铜、铝在计算下料上可和碳钢相同,但对不锈钢法兰条的号料应考虑车削加工余量,在施工转票上写清注明切割后的尺寸。
8.2凡需用等离子切割而又经线图号料的不锈钢零件,号料时所号两零件之间必须留20mm余量。
8.3铜板、铝板软性材料号料时,为保持材质表面不受任何损伤,故使用铅笔划中心线、标准线和曲线。
切割线使用划针划线,所有的划线必须能划清楚便于下序操作。
8.4有色金属在号料之前,须检查材料表面是否符合图纸要求,如有凸凹不平或皱褶沟纹等缺陷,不准号料。
8.5不锈钢的号料一律不准用样冲打标准线,四个角冲上轻微的50mm标准点即可,更不准用扁铲打字头。
8.6带有拔孔的有色金属号料,切孔需划线,较大的管孔则用展开号孔样板,并用草图在板料上表示出拔孔后的直径,为了避免拔孔后的裂纹,减薄缺陷,故在下料时,在φ50mm以内者,均按内直径缩小4mm,铜铝板不准打冲印。
8.7有色金属号料,在专用垫板上进行,并将板上的杂物打扫干净,不得在钢板上和水泥地面上号料。