任务焊缝超声探伤Word下载.docx
《任务焊缝超声探伤Word下载.docx》由会员分享,可在线阅读,更多相关《任务焊缝超声探伤Word下载.docx(34页珍藏版)》请在冰豆网上搜索。
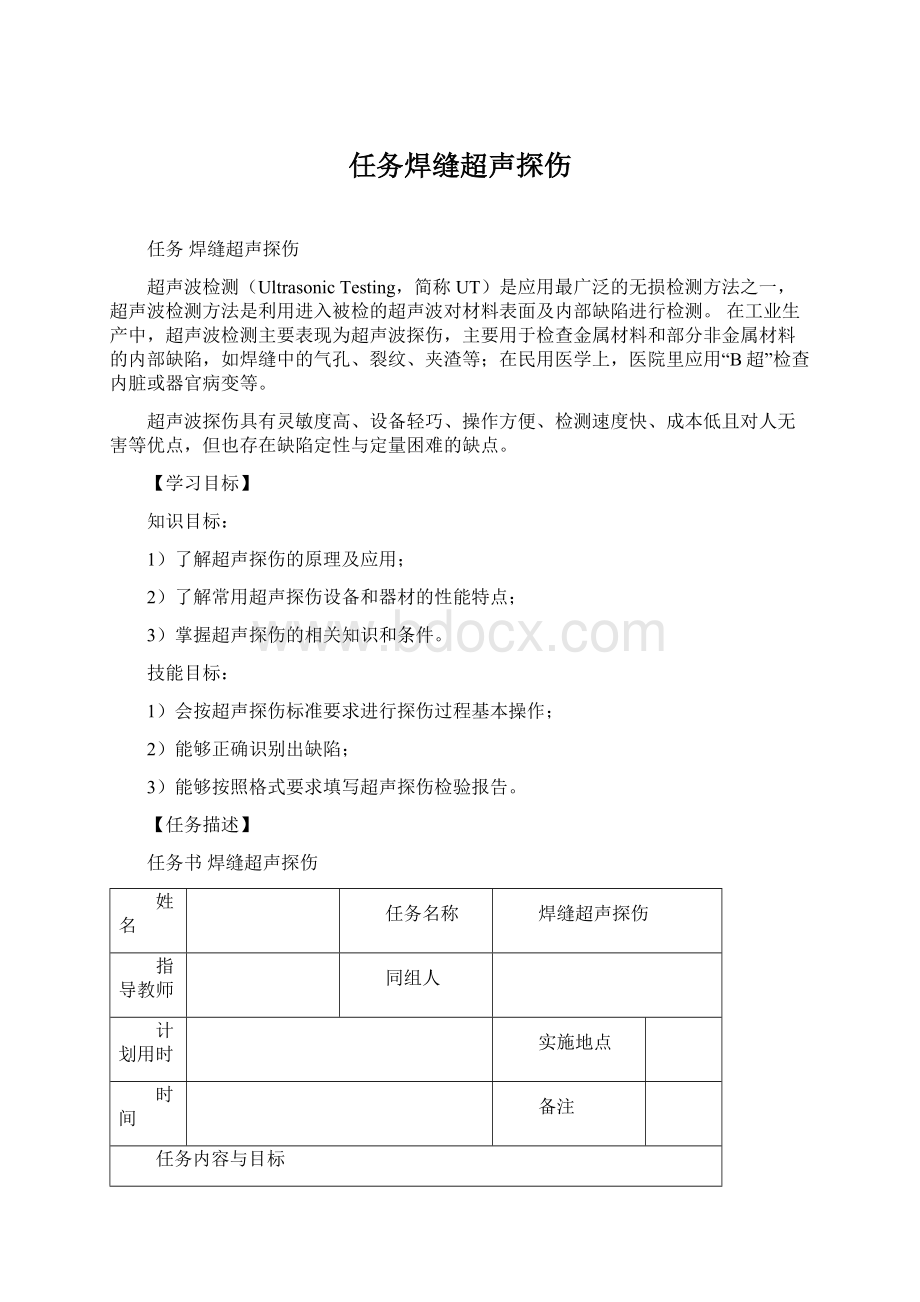
部件名称
厚度(mm)
部件编号
规格(mm)
检测项目
【】板材【】管材【】锻件【】焊缝
材料牌号
检测部位编号
破口型式
检测时机
【】焊后【】返修后【】机加后【】轧制后【】热处理后
表面状态
焊接方法
【】手工焊【】自动焊
【】氩弧焊
器
材
及
参
数
仪器型号
检测方法
【】纵波检测
【】横波检测
探头型号
表面补偿
试块型号
检测面
【】单面单侧
【】双面单侧
【】双面双侧
【】轧制面
耦合剂
【】水【】机油【】甘油【】工业浆糊
扫查速度
技术
要求
检测标准
检测比例
合格级别
检测规程编号
渗透剂型号
去除剂型号
显像剂型号
扫描线调节及说明
灵敏度校准及设定
扫查方式及说明
缺陷的记录
不允许的缺陷
扫差方式或
扫查部位示意图
编制人(资格):
年月日
(二)超声探伤操作步骤
现以对接焊缝为例介绍探伤时的具体的操作步骤和方法,其它接头的探伤也可以借鉴。
1.确定检验区宽度和探头移动区
检验区宽度应是焊缝宽度加上焊缝两侧相当于母材厚度30%的一段区域,这个区域最小为5mm,最大为10mm,探伤时,探头必须在探伤面上做前后左右的移动扫查,且应有一定的移动区宽度,以保证声束能扫查到整个焊缝截面。
移动区宽度因采用的探伤方法不同也有差别。
如图3—1所示。
直射法探伤时,移动区宽度L﹥0.75P;
一次反射法时,移动区宽度L﹥1.25P
式中P—跨距(mm)。
去除余高的焊缝,应该将余高打磨到与邻近母材平齐,保留余高的焊缝,如果焊缝表面有咬边、较大的隆起和凹陷等也要进行的适当的修磨,并作圆滑的过渡以免影响检测结果的评定。
图3—1检测和探头移动区
2.检测时机的确定
焊接接头区域的危害性缺陷,特别是延迟裂纹,是焊接件在焊后冷却到室温时所产生的裂纹,具有延迟现象,它并不是在焊接件焊后立即产生,通常是在焊后数小时或者更长时间产生。
而检测必须在延迟裂纹产生后进行,因此,把握好焊后的检测时机,防止延迟裂纹的漏检是十分重要的。
对于一般材质的焊接接头,检测规定在焊后一定时间实施。
但如果焊接接头很厚,刚度和焊接应力比较大及对有延迟倾向的材料,焊后实施检测的时间应该适当延长;
低合金高强钢焊接件,检测时机一般规定在焊接完成的24小时以后;
对于强度更高的低合金高强钢焊接件,或者刚度和焊接应力极大的焊接件,焊后实施检测的时间可以延长至5-7天以后。
上述规定也适合于焊缝返修以后的焊缝。
3.探头的扫查方法
为了发现缺陷和对缺陷进行准确定位,必须正确放置和移动探头。
图3—2锯齿形扫查
(1)锯齿形扫查如图3—2所示,为检测纵向缺陷,探头以锯齿形轨迹往复移动,同时探头还在垂直于焊缝中心线位置上做±
10°
~15°
的左右转动,探头的每次扫查率应大于探头直径的15%,声束尽可能垂直于缺陷。
该扫查方法常用于焊缝粗探伤。
(2)基本扫查基本扫查方式用四种,如图3—3所示。
其中,转角扫查的特点是探头做定点转动,用于确定缺陷方向并区分点、条状缺陷。
同时,转角扫查的动态波形有助于对裂纹的判断;
环绕扫查的特点是以缺陷为中心,变换探头位置,主要是用于估判缺陷形状,尤其是对点状缺陷的判断;
左右扫查的特点是探头做平行于焊缝或缺陷方向做左右移动,主要是通过缺陷沿长度方向的变化情况来判断缺陷形状,尤其是区分点、条状缺陷,并用此法来确定缺陷长度;
前后扫查的特点是探头垂直于焊缝前后移动,常用于估判缺陷形状及估计缺陷高度。
采用定量灵敏度针对全面扫查发现的缺陷或异常部位,通常采用这些方式,因此,也叫精确扫查方式。
图3—3斜探头基本扫查方式
三、缺陷定位与缺陷性质估判
(一)缺陷位置的测定
测定缺陷在工作或焊接头中的位置称这为缺陷定位。
缺陷定位实际上是确定缺陷与探头的相对位置。
定位时是以探头入射点或前沿长度为基准,根据反射波在示波屏上的位置及扫描速度来确定缺陷距离基准点的水平距离L和距离探伤面的垂直距离Z(深度)。
1.垂直入射法时缺陷定位
用垂直入射法探伤时,缺陷就在直探头的下面,缺陷定位只需确定缺陷在工件中的深度即可。
当探伤仪按1:
n调节纵波扫描速度时,则有
Z∫=nτ∫
式中Z∫——缺陷在工件中的深度(mm);
n——探伤仪调节比例系数,即超声波声程与屏幕显示距离的比值。
图3—4垂直入射法时缺陷定位
τ∫——示波屏上缺陷波前沿所对水平刻度值。
示例探伤仪按1:
2调节纵波扫描速度,探伤中示波屏上水平刻度“75”处出现一缺陷波,求此缺陷在工件中的深度Z∫。
解Z∫=nτ∫=2×
75mm=150mm
2.斜角探伤时缺陷定位
用斜探头探伤时,缺陷在探头前方的下面,其位置可用入射点至缺陷的水平距离L∫、缺陷到探伤面的垂直距离Z∫两个参数来确定。
(1)水平调节法定位(母材厚度δ<
20mm采用此法)探伤仪按水平1:
n调节横波扫描速度时,则有;
直射法探伤L∫=nτ∫(3—1)
Z∫=nτ∫/K
一次反射法探伤L∫=nτ∫(3—2)
Z∫=2δ-nτ∫/K
式中L∫——缺陷在工件中的水平距离(mm);
Z∫——缺陷在工件中的深度(mm);
τ∫——缺陷波前沿所对水平刻度值;
n——探伤仪调节比例系数;
δ——探伤厚度(mm);
K——探头K值(K=tgγ)。
示例用K2横波斜探头探伤厚度15mm的钢板焊缝,仪器按水平1:
1调节横波扫描速度,探伤中在水平刻度τ∫=45mm处出现一缺陷波,求此缺陷位置。
解由于Kδ=2×
15mm=30mm,2Kδ=60mm,Kδ<
τ∫<
2Kδ,可以判定此缺陷是二次波发现的,因此
L∫=nτ∫=1×
45mm=45mm图3—5斜角探伤时缺陷定位
Z∫=2δ-nτ∫/K=(2×
15-1×
45/2)mm=7.5mm
(2)深度调节法定位(母材厚度δ≥20mm采用此法),
探伤仪按深度1:
n调节横波扫描速度时,则有
直射法探伤L∫=Knτ∫(3—3)
Z∫=nτ∫
一次反射法探伤L∫=Knτ∫(3—4)
Z∫=2δ-nτ∫
示例用K1.5横波斜探头探伤厚度20mm的钢板焊缝,仪器按深度1:
1调节横波扫描速度,探伤中在水平刻τ∫=40mm处出现一缺陷波,求此缺陷位置?
解由于δ<
2δ,可以判定缺陷是二次波发现的,因此
L∫=Knτ∫=1.5×
1×
40mm=60mm
Z∫=2δ-nτ∫=(2×
30-1×
40)mm=20mm
(二)缺陷大小的测定
测定工件或焊接接头中缺陷的大小和数量称为缺陷定量。
工件中的缺陷是多种多样的,但就其大小而言,可分为小于声束截面和大于声束截面两种。
对于前者缺陷定量一般使用当量法;
而对于后者缺陷定量常采用探头移动法。
1.当量法
其原理是把缺陷波与同声程的已知形状和尺寸的人工缺陷(平底孔或横孔)回波相比较,与缺陷反射波高相同的人工缺陷的尺寸即认为是该缺陷的当量。
值得注意的是,“当量”仅表示缺陷与该尺寸人工缺陷对声波的反射能量相同,并不表示缺陷尺寸与人工缺陷尺寸相等。
因为工件中缺陷所处的情况是千变万化的,缺陷倾斜度、表面粗糙度及包含物等不同,都会影响到缺陷对声波的反射,因此可能使大缺陷的反射波反而很小。
当量法主要有当量曲线、当量计算法等。
对于焊缝探伤常采用当量曲线法,即利用具有同一孔径、不同距离的横孔试块制作的距离—波幅曲线(DAc曲线),对照检查出缺陷区域和当量。
示例探伤用距离—波幅曲线如图3—6所示,若探伤中在深度Ay=45mm处有一缺陷回波,可将其先调到最高,再调到基准高度(例如满刻度的40%),图3—6当量曲线法
此时dB读数为Vx=20dB,这时过Ay=45mm和纵坐标Vx=20dB分别作相应坐标的垂线,交于图3—6中一点。
据此可以求得该缺陷的区域和当量。
2.探头移动法
对于尺寸或面积大于声束直径或断面的缺陷,一般采用探头移动法来测定其指示长度或范围。
GB/T11345—1989规定,缺陷指示长度的测定推荐采用以下二种方法。
1)当缺陷反射波只有一个高点或高点起伏小于4dB时,用降低6dB相对灵敏度法测长,如图3—7所示。
图3—7相对灵敏度测长法
2)在测长扫查过程中,如发现缺陷反射波峰值起伏变化,有多个高点,则以缺陷两端反射波最大值之间探头的移动长度确定为指示长度,即为端点峰值法,如图3—8所示。
图3—8端点峰值测长法
(三)缺陷性质的估判
判定工件或焊接接头中缺陷的性质称之为缺陷定性。
到目前为止,在超声波探伤中对缺陷定性仍是个难点,因为不同性质的缺陷其反射回波波形区别不大。
对缺陷定性在很大程度上要靠检验人员的实际经验和操作技能,并根据缺陷波的大小、位置及探头移动时波幅的变化特点,结合焊接工艺情况进行综合判断,结果往往存在较大误差。
因此,这里仅简单介绍焊接缝中常见缺陷的波形特征。
1.气孔
单个气孔回波高度低,波形为单峰,较稳定,当探头绕缺陷转动时,缺陷波高大致不变,但探头定点转动时,反射波立即消失;
密集气孔会出现一簇反射波,其波高随气孔大小而不同,当探头作定点转动时,会出现此起彼伏现象。
2.裂纹
缺陷回波高度大,波幅宽,常出现多峰。
探头平移时,反射波连续出现,波幅有变动;
探头转动时,波峰有上下错动现象。
3.夹渣
点状夹渣的回波信号类似于单个气孔。
条状夹渣回波信号多呈锯齿状,由于其反射率低(原因是固体夹渣可以传播超声波),波幅不高且形状多呈树枝状,主峰边上有小峰。
探头平移时,波幅有变动;
探头绕缺陷移动时,波幅也会发生变化。
4.未焊透
由于未焊透对超声波的反射率高(厚板焊缝中该缺陷表面类似镜面反射),波幅均较高。
探平头移时,波形较稳定。
在焊缝两侧探伤时,均能得到大致相同的反射波幅。
5.未熔合
当声波垂直入射该缺陷表面时,回波高度大。
探头平移时,波形稳定。
焊缝两侧探伤时,反射波幅不同,有时只能从一侧探测到。
另外,在焊缝探伤中,示波屏上常会出现一些非缺陷引起的反射信号,称之为假信号。
产生假信号的原因是多方面的,对假信号的识别主要靠探伤人员的实际经验和操作技能,故这里不予介绍。
(四)、焊缝质量评定
按照JB/T4730.3-2005标准进行质量评定
1.缺陷评定
1)超过评定线的缺陷信号应注意其是否具有裂纹等危害性缺陷特征,如有怀疑应采取改变探头角度、增加探伤面、观察动态波形的探伤方法并结合焊接工艺特征作出综合判断,或辅助其它检验方法(如射线照相法)作综合判定。
2)缺陷指示长度小于10mm时,按5mm计。
3)相邻两缺陷在一直线上,其间距小于其中较小的缺陷长度时,应作为一条缺陷处理,以两缺陷长度之和作为其单个缺陷的指示长度(间距不计入缺陷长度)。
2.检验结果的等级分类
见下表3-4表3-4焊接接头质量分级
五、记录与报告
焊缝超声波探伤后,应将探伤数据、工件及工艺概况归纳在探伤的原始记录中,并签发检验报告。
检验报告是焊缝超声波检验的存档文件,经质量管理人员审核后,正本发送委托部门,其副本由探伤部门归档,一般应保存7年以上。
探伤记录和报告的格式可参考表3—5和表3—6。
表3—5焊缝超声波探伤记录
工件名称:
工件编号:
检验次序:
○首次检验○一次复验○二次复验
探测条件
探头
反射体
基准波高满幅%
反射体波幅dB
传输
修正
dB
探伤灵敏度dB
探测深度
mm
序号
角度
(γk)
频率
MHz
尺寸
形状
(φ)
深度
试块
1
2
3
焊缝
编号
检验区段号
探头
缺陷
位置
mm
指示
长度
波幅
评定
检验人
备注
→
表3—6焊缝超声波探伤报告
报告编号
报告日期年月日
产品名称:
令号:
材料:
厚度:
焊缝种类:
○平板○环缝○纵缝○T形○管座
焊接方法:
焊缝数量:
探伤面:
检验范围:
%
探伤面状态:
○修整○轧制○机加○其它
检验规程:
验收标准:
探伤时机:
○焊后○热处理后○水压试验后○其它
仪器型号:
耦合剂:
○机油○甘油○浆糊○其它
探伤方式:
○垂直○斜角○单探头○双探头○串列探头
扫描调节:
○深度○水平
比例:
试块:
探伤部位示意图:
探伤位置:
探伤结果及返修情况
焊缝编号
检验长度
显示情况
一次返修缺陷编号
二次返修缺陷编号
说明:
NI:
无应记录缺陷
RI:
有应记录缺陷
UI:
有应返修缺陷
○NI○RI○UI
检验焊缝总长:
mm,一次返修总长:
mm,
二次返修总长:
mm,同一部位经次返修后合格
附:
检验及复验记录页
备注:
结论:
○合格○不合格
检验:
UT级审核:
UT级
六、焊缝超声波探伤的一般程序
焊缝超声波探伤可分为探伤准备和现场探伤两部分,其一般程序如图3—9所示。
这里仅对前面没有提到的某些问题作一简要解释。
图3—9焊缝超声波探伤的一般程序
(1)委托检验委托检验单内容应有工件编号、材料、尺寸、规格、焊接方法种类、坡口形式等,同时也应注明探伤部位、探伤百分比、验收标准、级别或质量等级,并附有工件简图。
(2)指定检验人员超声波探伤一般安排二人同时工作,并因超声检验通常要当即给出检验结果,故至少应有一名Ⅱ级人员担任主探。
(3)了解焊接情况是探伤前的一项重要准备工作。
探伤人员了解工件和焊接工艺,以便根据材质和工艺特征,预计可能出现的缺陷及分布规律。
同时,向焊工了解在焊接过程中偶然出现的一些问题及修补等详细情况,可有助于对可疑信号的分析和判断。
(4)粗探伤主要目的是发现缺陷。
主要内容是探测各种方向的缺陷,并做好标记;
以及鉴别结构的假信号等。
(5)精探伤针对粗探伤中出现的缺陷,进一步确切测定缺陷的大小及位置。
(6)评定缺陷系指对缺陷反射波幅的评定、指示长度的评定、密集程度的评定及缺陷性质的估判。
根据评定结果给出受检焊缝的质量等级。
但是,焊缝超声波探伤有其特殊性。
有些评定项目并不规定等级概念,而往往与验收标准联系在一起,直接给出合格与否的结论。
【相关知识】
一、超声探伤原理
超声波(以焊缝为例)的检测原理如下:
超声波探伤仪产生电信号,通过超声波探头产生超声波,通过耦合剂(机油或者甘油),进入焊缝表面
如果碰到缺陷,超声波返回再通过探头产生电信号,经过超声波探伤仪转换成回波,观察回波来定位定量缺陷。
图3—10焊缝超声波探伤原理
二、超声探伤方法分类
在超声波探伤中,由于探头与工件接触方式不同,超声波探伤方法也不同。
主要有以下方法。
1按照原理可分为:
脉冲法、穿透法、共振法,目前主要应用脉冲反射法。
2按操作方式:
手工检测法、自动检测法。
3按探头个数:
单探头法、双探头法和多探头法。
4按探头与试件的接触方式,可分为接触法和液浸法。
工业探伤中,主要根据工件情况确定检测方法,因此,重点介绍接触法和液浸法。
一、直接接触法超声波探伤
由于超声波的性质,一般认为超声波不能在空气中传播,因此使用直接接触法应在探头和被探工件表面之间使用耦合剂,作为传声介质。
常用的耦合剂有机油、变压器油、甘油、化学浆糊、水及水玻璃等。
焊缝探伤多采用化学浆糊和甘油。
由于耦合剂层很薄,因此可以认为探头与工件直接接触。
直接接触法主要采用A型脉冲反射法探伤仪的工作原理,由于操作方便,探伤图形简单,判断容易且探伤灵敏度高,因此在实际生产中得到最广泛应用。
但该法对工件探侧面的表面粗糙度要求较高,一般要求在Ra6.3μm以下。
垂直入射法和斜角探伤法是直接接触法超声波探伤的两种基本方法。
1.垂直入射法
垂直入射法(简称垂直法)是采用直探头将声束垂直入射工件表面进行探伤。
由于该法是利用纵波进行探伤,故又称纵波法,如图3—11所示。
当直探头在工件探伤面上移动时,经过无缺陷处探伤仪示波屏上只有始波T和底波B,如图3—11a。
如探头移到有缺陷处,且缺陷的反射面比声束小时,则示波屏上出现始波T、缺陷波F和底波B,如图3—11b。
若探头移至大缺陷(缺陷比声束大,超声波全部被反射)处时,则示波屏上只出现始波T和缺陷波F,如图3—11c。
图3—11垂直入射法探伤
a)无缺陷b)小缺陷c)大缺陷
可以看出,垂直法探伤能发现与探伤面平行或近似于平行的缺陷,适用于磨平的焊缝,厚钢板、轴类、轮等几何形状简单的工件。
2.斜角探伤法
斜角探伤法(简称斜射法)是采用斜探头将声束倾斜入射工件表面进行探伤。
由于它是利用横波进行探伤,故又称横波法,如图3—12所示。
当斜探头在工件探伤面上移动时,若工件内没有缺陷,则声束在工件内经多次反射将以“W”形路径传播,此时在示波屏上只有始波T,如图3—12a。
当工件存在缺陷,且该缺陷与声束垂直或倾斜角很小时,声束会被缺陷反射回来,此时示波屏上将显示出始波T、缺陷波F,如图3—12b。
当斜探头接近板端时,声束将被端角或端面反射回来,此时在示波屏上将出现始波T和端角(面)波B,如图3—12c。
图3—12斜角探伤法
a)无缺陷b)有缺陷c)接近板端
显然,斜角探伤法能发现与探测表面成角度的缺陷,常用于焊缝、环状锻件、管材的检查。
用斜角法探伤焊缝,缺陷位于探头前面斜下方,但对缺陷的准确定位,需要根据探头与缺陷的几何关系来确定,如图3—13所示。
图3—13焊缝斜角探伤用语
二、液浸法
液浸法是将工件和探头头部浸在耦合液体中,探头不接触工件的探伤方法。
根据工件和探头浸没方式,分为全没液浸法、局部液浸法和喷流式局部液浸法等。
其原理如图3—21所示。
液浸法探伤由于探头与工件不直接接触,因此它具有探头不易磨损、声波的发射和接收比较稳定、探测速度快等优点。
常用于坯材和型材(无缝钢管、不锈钢管等)、特殊工件(双金属的粘结层、复合材料等)和焊缝的精密探伤。
其主要缺点是,它需要一些辅助设备,如液槽、探头桥架、探头操纵器等。
同时,还由于液体耦合层一般较厚而声能损失较大。
图3—14液浸法探伤
a)全没液浸法b)局部液浸法c)喷流式局部液浸法
三、超声探伤法应用
超声探伤在焊接中主要应用在以下方面:
1)中厚板对接接头的超声探伤;
2)管座角焊缝和T型焊接接头的超声探伤;
3)堆焊层的超声探伤;
4)铝对接接头的超声探伤;
5)钢制承压设备管子和压力管道环向焊接接头的超声探伤;
6)船体的焊接接头的超声探伤;
7)钢结构的焊接接头的超声探伤;
四、超声探伤主要设备
在超声探伤过程中要用到许多设备和器材,其性能将直接影响探伤的结果,现将生产中用的主要探伤设备介绍如下。
(一)超声波探伤仪
超声波探伤仪是探伤的的主体设备,其主要功能是产生与超声波频率相同的电振荡,激励探头发射超声波;
同时,它又将探头接收到的回波转换成电信号并予以放大、处理,再以一定方式在示波屏上显示出来。
(1)超声波探伤仪的分类
(1)按超声波的连续性分类
按超声波的连续性可将超声波探伤仪分为脉冲波、连续波和调频波探伤仪三种。
图3—15数字超声波探伤仪
由于后两种探伤仪的灵敏度低,缺陷测定有较大局限性,故在焊缝探伤中不采用。
(2)按显示缺陷的方式按显示缺陷的方式可将探伤仪分为A型显示(缺陷波幅显示)、B型显示(缺陷侧视图象显示)、C型显示(缺陷俯视图象显示)和3D型显示(缺陷三维图象显示)超声波探伤仪。
(3)按超声波的通道数目按超声波的通道数目又可将其分为单通道和多通道两种。
前者是由一个或一对探头单独工作;
后者是由多个或多对探头交替工作,而每一通道相当与一台单通道探伤仪,适用于自动化探伤。
目前,焊缝探伤中广泛使用的是A型显示脉冲反射式单通道超声波探伤仪。
(2)A型脉冲反射式超声波探伤仪
该探伤仪相当与一台专用示波器。
这里只简单介绍其工作原理及与探伤结果有直接关系的性能。
1.工作原理
A型脉冲反射式超声波探伤仪电路原理框图如图3—13所示。
接通电源后,同步电路产生的触发脉冲同时加在扫描电路和发射电路。
扫描电路受触发后产生的锯齿波电压加到示波管水平轴(x轴)上,从而在示波屏上产生一条水平扫描基线,又称时间基线。
与此同时,发射电路受触发后产生高频脉冲加至探头,激励压电晶片振动而产生超声波,超声波经耦合剂导入工件,在工件中传播时遇到缺陷或底面即发生反射,反射回波被同一探头接收并被转换成电信号,经接收电路放大和检波后加到示波管垂直轴(y轴)上,在示波屏水平扫描线的相应位置上产生始波T(表面反射波)、缺陷波F、底波B。
实际上,该探伤仪示波屏上横坐标反映了超声波的传播时间,纵坐标反映了反射波的振幅,因此通过