影响制粒机效率的各方面因素学习资料文档格式.docx
《影响制粒机效率的各方面因素学习资料文档格式.docx》由会员分享,可在线阅读,更多相关《影响制粒机效率的各方面因素学习资料文档格式.docx(27页珍藏版)》请在冰豆网上搜索。
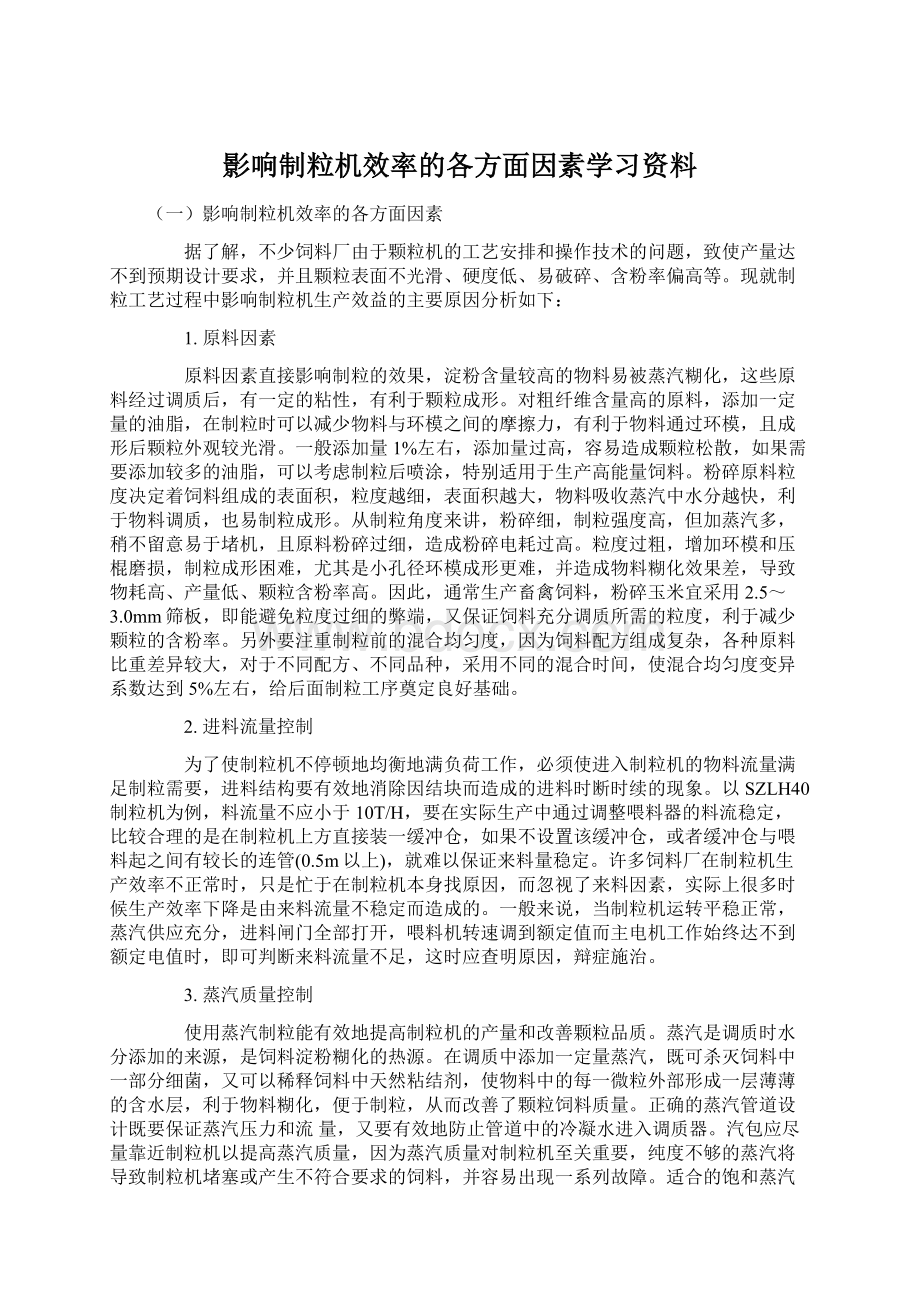
一般畜禽饲料调质温度在85度左右,冬季室温低,调质温度应低一些,夏季室温高,调质温度高一些。
蒸汽压力高,物料吸收的蒸汽量少,而糊化差,适合含水分高的物料。
蒸汽压力低,物料吸收的蒸汽量多,吸收水分也多,糊化好,适合于含水分低的物料。
4.生产操作
正确控制压辊与压模间隙。
辊模间隙太小,压模与压辊容易磨损,并且超噪音大;
间隙太大,则影响物料挤压。
一般控制在0.05~0.30mm。
调整时可用塞尺测量,无塞尺目测也可以。
以新模新辊为例,目测压模压辊似靠非靠,但无物料时主机转动压模不能带动压辊为宜,特别强调新模应配新辊,间隙应小些。
另外压辊要加足黄油(通常选用耐高温7号锂基脂),避免因温度过高烧坏轴承。
同时也要对喂料刮刀进行调整,否则会使物料难以进入压辊与压模之间,一部分物料会从压模罩船串出,形成颗粒粉化粒高,调整结果应是刮刀上部边缘曲线与压模、压模罩间隙基本控制在2~3mm之间,刮刀前端伸入压模位置不宜超过压模内孔的沉割槽。
制粒机各部位调整好后,可以开机制粒。
先开制粒机、调质器、喂料器,此时喂料器应处于小供料状态。
为防止机内杂物进入压模,应该打开操作门上的机外排料门,排净机内混有杂物的料。
待杂物料干净后,即可将物料导入压模。
为慎重起见,手应握住机外排料门手柄,先让部分料进入压模,然后观察是否有颗粒顺利出模,并同时注意电流变化。
如果颗粒能正常制出,电流较平稳,波动幅度不大,没有达到额定电流,那么可以加大物料流量,并同时增加蒸汽量,直至达到额定电流为止。
假如物料进入制粒室,但没有颗粒出模,并且电流不断升高,这是要打开机外排料门,观察不断续进料时,电流是否下降。
如果电流下降,同时有部分颗粒出模,可以握住机外排料门手柄,让部分料导入压模,部分料排外,观察电流是否平稳,压模出粒是否顺当,如正常可将物料全部导入压模。
假如停止进料后电流仍不下降,甚至继续上升,就应停机检查原因,辩症施治。
值得提醒的是,在初下料时,切勿急于加蒸汽,因为此时物料少,蒸汽难以加到理想量,蒸汽多,物料少,极易堵机,不如待料加到一定量时才加蒸汽来的稳妥。
另外制粒机下班停机前必须将油性物料替代物料添进压模内,其目的是防止模孔内物料变硬,以便下次开机压模能顺利出粒。
5.环模
制粒过程中物料能否被挤压通过压模取决于模孔中所能产生的压力和摩擦力的大小。
这跟物料与压模壁之间的摩擦系数、水分含量、原料粒度、温度、物料可塑性变形部分的缓冲时间和物料的可压缩性有关,这些特性与压模孔深和孔径密切相关。
一般来讲,压模孔径压缩比宜采用1:
8~1:
13(即模孔与压模的有效厚度比),压模的压缩比小,压模孔的有效长度短,物料在压模孔中形成的压力小,容易挤出环模,因此,产量高,但制出的颗粒松散,含粉率高,外观不光滑;
反之压缩孔的有效长度越长,物料在压模孔中的压力越大,相应制出来颗粒紧密度高,颗粒光滑质量好,可降低含粉率,但制粒机产量会下降,当然吨电耗也相应增加。
因此,饲料厂家在生产不同规格与品种的颗粒料时,所选用的环模孔径比会有所不同。
(二)影响颗粒料加工质量因素的分析和解决方法
1颗粒饲料加工质量优劣的鉴定颗粒料加工质量的好坏,主要表现在以下几个方面:
①颗粒的稳定性。
主要指颗粒料在成型后在冷却、分级、转运、储存过程中保持原有几何形状的特性。
②颗粒的外观质量。
主要指颗粒表面是否光滑,颗粒的颜色、长度是否一致等。
③颗粒的硬度。
饲喂不同的动物,对颗粒料的硬度要求是不一样的。
例如猪料的硬度要求较低,鸭料、鱼料的硬度要求较高。
④颗粒熟化程度。
颗粒的熟化程度高有利于动物消化吸收,常通过检测淀粉的糊化度来评判。
⑤颗粒的水分。
合理的水分有利于提高饲料的适口性和企业的经济效益;
而较低的水分是饲料安全储存的必要条件。
2影响颗粒加工质量的因素
根据美国大豆协会饲料技术顾问熊易强博士的研究表明,在颗粒质量的影响因素中配方占40%,粉碎粒度占20%,调质效果占20%,制粒过程控制占15%,冷却条件占5%。
我们在生产实践中得到的经验数据基本符合这个观点。
2.1配方配方是保证颗粒质量的重要因素。
其中水分、淀粉、蛋白质、脂肪粗纤维对颗粒的质量影响尤其明显。
2.1.1水分原料混合以后综合样的理想水分夏季12%~14%,冬季10%~12%,通过调质原料吸收蒸汽后达到水分15%~17%。
一般添加原料重量1%的蒸汽物料对应升高13~15℃。
笔者通过测量在四川的气候条件下使用“逆流式冷却器”如果蒸汽饱和度较高,夏季通过制粒冷却后颗粒水分会比原料降低0.5%~1.5%,冬季如果不对调质器和冷却器,保温水分会上升0.5%~1.5%。
只要蒸汽的饱和度足够,不管是冬季还是夏季添加较多的蒸汽使物料调质充分成品料的水分反而比低温调质低。
所以要控制成品水分必须控制原料水分。
原料水分过高还会导致制粒过程中堵塞环模,产生片状的锅巴了混入成品,甚至导致生产无法连续进行。
如果原料水分过低,饲料成品颗粒易产生干脆现象,粉化率会提高;
同时为提高企业的经济效益和动物的适口性,可有条件地人工添加水分,详细规定在“调质效果”中阐明。
2.1.2淀粉生淀粉表面粗糙,制粒阻力大,粘结性能差但通过蒸汽调质、环模压辊挤压,淀粉会部分糊化。
糊化淀粉粘结性能好,颗粒质量好。
所以有时为了满足工艺上的要求而非营养指标的要求也要在配方中添加一定量的淀粉原料。
这在水产料的配方设计中尤其重要,例如在幼鱼料的配方设计中,从营养的角度幼鱼对淀粉的消化率极低,但为了保持幼鱼料在水中的稳定性配方中必需添加一定量的淀粉,或其它粘结剂。
不同原料的淀粉糊化后粘结性能不同。
例如大麦和小麦的粘结性能比玉米好,烘干玉米不如自然风干玉米好。
2.1.3蛋白质配方中蛋白质含量适量时,易于制粒,颗粒质量也较好,因为蛋白质受热后变性、粘性增大,制粒机产量提高、质量好。
蛋白质含量过高时,吸收蒸汽能力严重下降,调质温度降低,制粒的效果下降。
2.1.4脂肪:
适量的脂肪能减小物料和环模的摩擦阻力,从而减小环模磨损;
也能使产量提高,能耗降低,颗粒表面光滑。
但要控制在3%以内,脂肪含量过高颗粒质量会下降,特别易脆。
如果配方需要的脂肪含量超过5%可采用后喷涂工艺。
2.1.5粗纤维:
粗纤维含量不宜超过10%~15%。
因为它自身的粘贴性差,使饲料粒子间的结合力下降;
同时也影响饲料吸收蒸汽的能力,使饲料的硬度升高、成型率和产量降低,也使设备磨损量和设备的振动严重增大。
2.2原料的粉碎粒度粉碎细度是影响颗粒品质和生产效率的一个重要环节。
粉碎细度决定着饲料组份的表面积。
粒度细,表面积大,吸收蒸汽的水分均匀而快速,原料中淀粉糊化度高。
粉碎度越细致越均一,制出的颗粒质量越好,环模和压辊磨损越小。
相反粉碎粒度粗的原料由于含有大颗粒,会引起制出的颗粒破裂和断开,导致粉料增加。
2.2.1调质效果调质是制粒前的重要环节,好的调质效果能极大地提高产量,降低制粒机振动、降低能耗,提高颗粒质量。
调质效果的好坏可以用三个指标来反映,一是调质后原料的温度:
一般要求猪料不低于80℃;
水产料不低于90℃;
禽料不低于65℃。
根据熊易强博士的研究:
在不堵机的条件下调质温度越高越有利于保证颗粒质量,和营养成份尽量少的被破坏。
二是水分:
通常配合饲料调质后水分可达15%~17%。
不同物料对水分的吸收能力不一样;
如果物料对水分的吸收能力差,加入过多的蒸汽,转变成游离水后易造成堵机。
三是时间:
物料在调质室内需要30~40s以上的停留时间。
影响调质效果的因素有3个方面:
①物料本身的特性;
②蒸汽的品质;
③调质设备的性能和参数调节。
2.3环模和制粒机因素
环模影响颗粒饲料质量的因素主要是环模的压缩比、孔径、孔壁粗糙度、减压孔的直径和深度以及维护使用状况等。
不同品种饲料对环模的压缩比及模孔直径的要求有所不同,压制不同品种的饲料,需要选用相应的压缩比和孔径,以获得所需质量的饲料颗粒。
环模的维护使用状况也会影响颗粒饲料质量,如出现如下情况,颗粒饲料质量将会明显下降:
环模的工作面不均匀的磨损、过多的蜂窝孔、有效厚度降低和模孔内表面出现斑点或刻痕等。
制粒机的因素主要是转速。
环模在制粒机上的线速度一般为4~8m/s(线速度在外径上测量),能提供两种压模转速的制粒机在生产品种广泛的饲料时可获得最佳效果。
一般来说,制粒机的转速越高,饲料颗粒的质量越差。
2.4冷却因素
颗粒饲料离开环模时的温度达70℃~100℃,水分达15%~18%,为了安全储存和输送,确保颗粒的耐久性,减少颗粒的破碎,颗粒料温度要降低到不高于室温5℃,最好控制在3℃以内。
水分降低到10%~12.5%,这一过程是通过冷却器来完成的。
一般空气温度每升高约11℃,其持水能力就可提高一倍,故当半成品水分高时,可以通过提高进入冷却器的空气温度来调节颗粒成品的水分。
目前被广泛地与环模制粒机配套使用的是逆流式冷却器,这种冷却器自动化程度高,颗粒冷却后表里如一、无裂缝、外观光滑。
3颗粒料异常外观的产生原因及改进办法
生产中,颗粒饲料产品有时会出现不同程度的外观质量缺陷。
现将颗粒饲料中常出现的加工缺陷归纳如下,并分析缺陷产生的原因,提出各种改进措施。
3.1颗粒弯曲且一面呈现许多裂纹
3.1.1产生原因:
这种现象通常是在颗粒离开环模时产生的。
原因有:
①当切刀刀口位置离环模与压辊啮合区表面较远或切刀平面与啮合区切线角度不合理或刀口较钝时,颗粒从模孔挤出时是被切刀碰断的或撕裂而非被切断的;
②减压孔过大。
这2种情况会造成有部分颗粒弯曲且一面呈现许多裂纹。
3.1.2改进措施:
①增大环模的压缩比,增大环模、压辊对物料的压缩力;
从而增加颗粒料的密度、硬度和强度;
②提高粉碎细度;
③如果添加了糖蜜或油脂应控制添加量并改善糖蜜或油脂的散布均匀度。
以提高饲料的密实度,防止饲料松软;
④调节切刀与环模表面的距离和角度;
⑤使用较比较薄的切刀(1~1.2mm厚的锰钢片性能较好)并且生产过程中磨损后要及时磨锋利;
⑥必要时使用粘结剂,改善颗粒料内部的结合力;
⑦减压孔直径与有效孔直径差应控制在0.2~0.4mm。
3.2水平裂纹横向贯穿整个颗粒
3.2.1产生原因:
与颗粒弯曲显现类似,裂纹发生于颗粒的横切面,只是没有弯曲。
其产生原因主要:
①含有较多纤维的蓬松饲料制粒时,由于其中含有比孔径长的纤维,当颗粒被挤出后,因纤维的膨胀作用使颗粒在横切面上产生贯穿的裂纹。
②调质温度低或时间短,调质不充分,饲料熟化度不够。
③粘结性原料含量过少。
④调质后水分高。
3.2.2改进措施:
①增大环模的压缩比,增大环模压辊对物料的压缩力;
②提高粉碎细度,使其中最长的纤维长度不超过粒径的三分之一;
③降低产量以减小饲料通过模孔的速度,增加密实度。
④提高调质质量:
加长调质时间,或使用多层调质器或高效调质器。
⑤当粉料的水分过高或含有尿素时,也可能产生枞树皮状的裂纹,应控制添加的水份和尿素含量。
3.3颗粒产生纵向裂纹
3.3.1产生原因:
①配方中含有蓬松而略带弹性的原料,在经过调质是会吸水膨胀,经过环模压缩制粒后,会因水分的作用及原料本身的弹性而弹开,产生纵向裂纹。
②环模压比过低。
③调质温度低或时间短,调质不充分,饲料熟化度不够。
3.3.2改进措施:
①如果有必要而且配方成本允许,调整配方。
②使用较饱和的干蒸汽降低粉料调质后的水分。
③降低产量或加大压缩比,尽可能地延长饲料在环模中的时间;
④有必要时添加粘结剂,也可以减少颗粒产生纵向裂纹。
⑤提高调质质量:
⑥必要时增加后熟化工序。
3.9颗粒料含粉多3.9.1养殖户经常因为饲料中料粉过多而投诉。
粉料产生原因有3类:
①因为饲料颗粒表面不光滑、颗粒松散、切口不整齐等在运输过程中饲料易粉化;
②分级筛粉料口被堵塞,制粒冷却产生的粉料没有被筛分出来。
③成品仓中物料是呈漏斗型下料的,颗粒料的流动性好会先下,粉料流动性差会积聚,到一定的时候会坍塌,这种坍塌下来的颗粒料含粉特别高。
如果接料时不注意检查将这种料清出来,会造成一批料中有个别的几包粉料特别重。
3.9.2改进措施:
①针对饲料颗粒表面不光滑、颗粒松散、切口不整齐等原因,产生的粉料可以采取如下措施:
根据原料的特性和颗粒要求选择合适的环模开孔面积、压缩比和喂料量;
在设计配方时考虑颗粒粉化的影响适当减少脂肪、纤维的含量,增加淀粉含量;
通过延长调质时间、增加调质水分和温度等措施提高调质质量,提高饲料熟化度;
提高粉碎细度:
调整或修磨切刀使颗粒切口整齐。
②清理或检修分级筛。
③接料过程中注意检查饲料含粉率;
将含粉率,超标的料重新筛分;
针对鱼料等对含粉率,有严格要求的颗粒料,必要时在成品仓下,接料称前加一台震动筛,对饲料进行二次筛分。
3.10颗粒长短不一
3.10.1产生原因长短不一的饲料颗粒影响饲料的整体外观,另外也会导致饲料不能充分被动物利用,造成浪费。
颗粒长短不均匀的原因有:
①在同一时刻制粒室内物料分布不均匀;
②制粒机的喂料量不均匀,调质效果波动很大;
③模辊间隙不一致;
④压辊磨损不一致;
⑤环模导料口的磨损量,沿轴向不一致或环模上被堵死的孔较多;
⑥沿环模的轴向,两端的出料速度小于中间的速度。
⑦设计环模时减压孔相比有效孔过大,有的颗粒在减压孔中被摔断;
小粒径的环模因减压孔长,尤其易产生颗粒长短不均匀的现象。
⑧切刀的位置或角度不合理。
3.10.2改进措施:
①调整布料刮刀的长短、宽窄或角度。
②刚开设生产和快结束生产时喂料量小且不均匀,导致颗粒长度偏短,如果要求高要接出来。
生产过程中要保持喂料量、蒸汽调质的稳定,投入的切刀数量要和产量相匹配,必要时要牺牲产量保证得到合适的颗粒长度。
③调节压辊调节螺丝使每个模辊间隙一致。
④新环模要配新压辊,使用中的每个压辊磨损量要一致;
如果压辊、环模轴向磨损不一致,必要时要将高的地方打磨掉。
⑤修理环模的导料口;
及时清理,环模上被堵死的孔。
⑥在设计环模时,沿环模的轴向,两端的3排孔压缩比可以比中间的小1~2mm(根据配方和粒径选择)。
⑦在设计环模时对颗粒长短要求严格的产品,例如鱼料有效孔直径与减压孔直径差要控制在0.2~0.4mm范围内。
⑧切刀厚度控制在1.5mm内,刀口锋利,刀口位于压辊和环模的啮合线上,切刀平面于压辊环模啮合面切线上翘3~5度角。
⑨定期检查环模与制粒机的同轴度,超标时要修配环模、调节主轴承间隙或更换主轴和空轴轴承。
3.11成品水分过高
3.11.1产生原因:
饲料颗粒水分过高,不利于饲料的储存,易发霉发酵。
造成颗粒料水分过高的原因有:
①原料水分过高。
②蒸汽饱和度不够,调质后水分过高。
③调质温度过低。
④烘干或冷却时间不够。
⑤烘干或冷却设备产能不足或发生故障。
⑥环境温度低和相对湿度高。
3.11.2改进措施:
①控制原料水分夏季12%~14%,冬季10%~12%。
②调质后水分控制在15%~17%,冬季取下线;
控制调质温度,特别是冬季调质温度最好控制在80℃以上。
③提高蒸汽的饱和度。
④延长烘干或冷却时间。
⑤控制制粒机产量,使之与烘干机或冷却器产能相匹配。
⑥检查冷却风网是否有短路或堵塞显现;
检查冷却器的布料和下料是否均匀。
⑦在冬季对冷却器进行保温或加蒸汽盘管加热冷却风。
提高颗粒饲料产品水分探析
1、降低锅炉供气压力和生产使用压力正常情况下,锅炉供汽压力为7kg/cm2~9kg/cm2,生产使用压力为3kg/cm,压力越高,湿度越低;
反之,压力越低,湿度越高,蒸汽含水量高。
因此只要满足生产需要,压力越低越好,建议锅炉供汽压力调整为4kg/cm2~6kg/cm2,生产使用压力调整为2kg/cm2。
2、增加调质时间增加物料在调质器内的停留时间,使物料与蒸汽充分混合,有利于淀粉糊化,提高畜禽消化吸收率,也能使物料充分吸收蒸汽中的水分,从而增加产品的水分。
增加调质时间,可以采取降低调质器的转速或调整调质器的桨叶等方法。
3、关闭所有疏水阀在分气包和蒸汽供汽管道中一般均安装了很多疏水阀,其目的是排除蒸汽管道中的冷凝水,防止蒸汽带入过多的水分,而造成制颗机堵机,但是夏季由于原料水分较低,蒸汽含水量也较低,调质后的物料水分很难达到16%。
因此关闭疏水阀,决不会造成堵机,反而有助于增加产品水分。
4、选择合适规格的压模压模的孔径和厚度大小,不仅是影响制粒机产能的主要因素,同时也影响颗粒饲料产品的水分。
孔径小的压模,由于其颗粒直径较大,冷却风量不容易穿透颗粒。
因此冷却时带走的水分多,产品水分低;
反之,孔径大的压模,其颗粒直径较大,冷风不容易穿透颗粒,冷却时带走的水分少,产品水分高。
对于厚度较大的压模,在制粒过程中,磨擦阻力较大,物料不容易通过孔径,挤压制粒时,磨擦温度高,水分散失大,其颗粒产品水分低,因此建议选用压模时,压模的孔径、厚度要合适。
5、选择合适的冷却风量冷却过程的目的一方面是降低颗粒饲料的温度,使其不超过室温3℃~5℃;
另一方面也可以带走饲料中的水分,使产品水分符合规定的标准。
从生产角度分析产品不合格的原因
一、花料
花料就是成品中有其他颜色的物料。
花料的观察方法,要逆光观察。
花料的产生原因及处理方法
1,制粒机塞机会造成较长、较硬、颜色较深的料。
此料出现在成品颜色为白色浅黄色的成品中较易发现,处理方法:
可重新制粒处理;
在颜色黑的成品中不易从颜色的角度发现,处理方法:
可直接倒入冷却器中稀释。
2,交叉污染造成花料。
制粒时上一品种尾料或管道中有残留的粉料与下一品种交叉污染,制粒是会造成花料。
处理方法:
重新制粒。
3,管道中成品未及时清理,如冷却器中有残留成品未清理与下一品种成品交叉污染造成花料。
二、浓缩料料中有颗粒料
1,混合机有颗粒料,再做浓缩料时混合机清理不干净,处理方法:
过筛把粒料筛除后再混合。
2,浓缩料与颗粒料共用一个成品仓时,仓体死角有颗粒料的残留。
做浓缩料时把残留的粒料冲下,造成浓缩料料中有颗粒料,过筛后再混合。
注:
生产浓缩料时要洗仓并且前几袋成品要过筛。
三、成品化验蛋白高
1,查看是否是上一品种高蛋白成品混入本品种中。
2,查看是否有蛋白质原料混入其中。
如窜仓等
四、成品化验灰分高、钙高、磷高、盐分高等
查看是否是石粉等钙质原料混入其中。
如果同时磷的指标也高,查看是否是磷酸氢钙等含磷含钙原料混入其中。
如盐分高,查看是否是盐类原料混入其中 以上是生产过程中较易出现的造成不合格成品的原因粗略分析
饲料加工中交叉污染的原因及处理方法
由于我国饲料标准体系建设滞后,许多操作技术规范尚未建立,对于饲料添加剂和违禁药物的检验,缺少权威性高、通用性强的方法。
所以对于我国大多数饲料厂家来说,建立一套有效的饲料安全保障措施和方法势在必行。
为某种目的而添加到目标饲料中的药物,在加工过程中因各种原因而出现在非目标饲料中,即为交叉污染。
饲料交叉污染存在于所有饲料厂中,降低饲料交叉污染是保证饲料安全的重要措施。
笔者现从饲料加工的角度分析出现药物交叉污染的原因,并提出建议性的改进措施,以供饲料生产厂家参考。
1饲料加工中产生污染的原因分析
饲料的药物污染在饲料加工、转运和储存等过程中均可能发生。
其中,加工过程中的污染主要有以下几个方面:
1.1吸尘系统在大中型饲料厂的加工车间,吸尘系统分布在加工过程中的各个主要环节,目的是减少加工环节产生的粉尘,净化生产环境。
对所收集的粉尘,从经济方面考虑,一般将其返回到饲料中,但灰尘的延迟回落或集尘系统设计不合理可导致药物添加剂被过多地吸取。
1.2配料系统准确配料是严格执行生产配方的前提和保证。
药物添加剂的计量一旦出现差错而又没有及时发现,后续工段是无法弥补的,将会带来严重污染。
1.3混合系统混合过程是使各种成分分布均匀的过程,也是产生药物污染的主要环节。
其原因是:
对混合时间设定不合理,未达到预期的混合效果,