小轴的加工工艺设计与加工论文.docx
《小轴的加工工艺设计与加工论文.docx》由会员分享,可在线阅读,更多相关《小轴的加工工艺设计与加工论文.docx(14页珍藏版)》请在冰豆网上搜索。
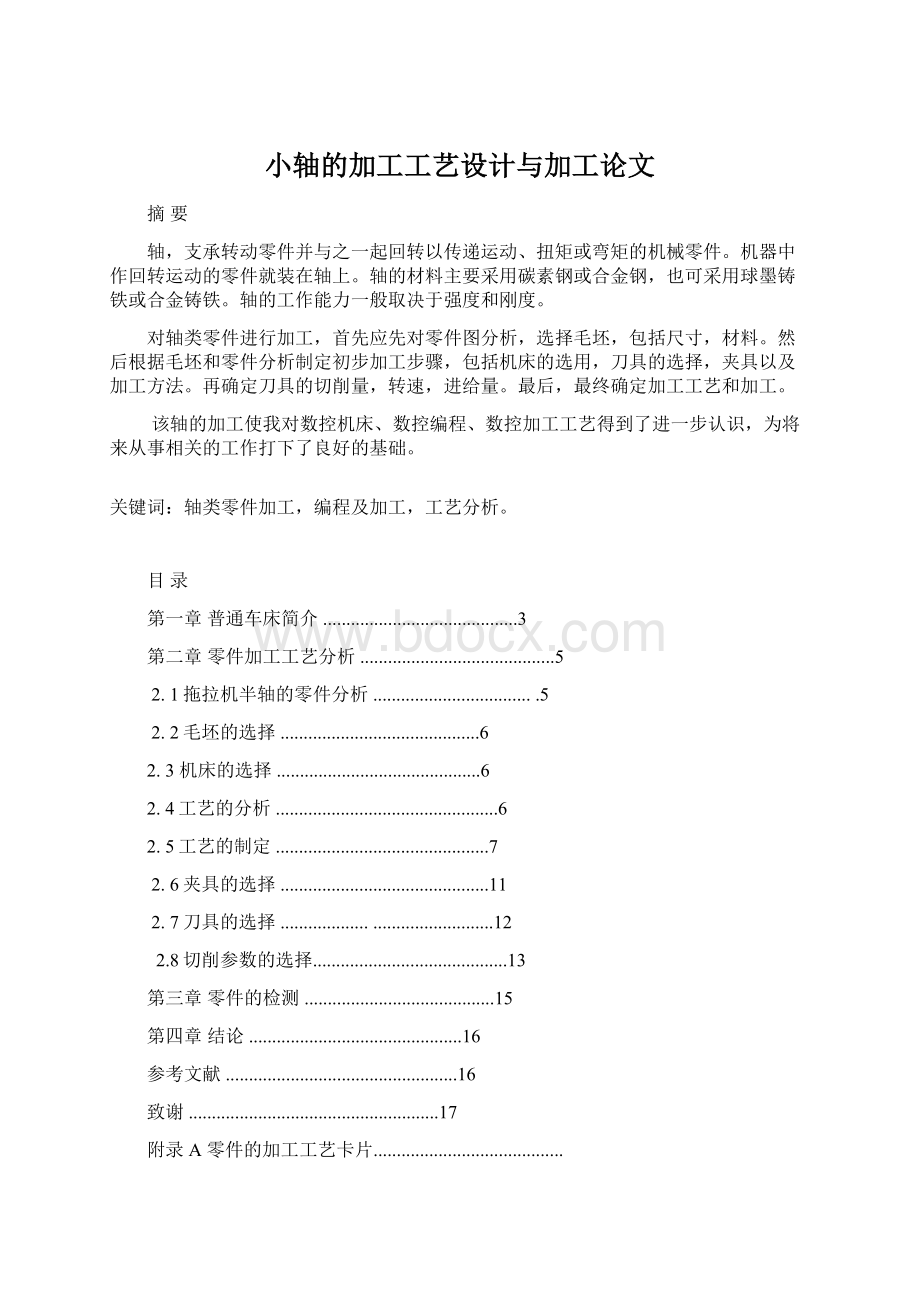
小轴的加工工艺设计与加工论文
摘要
轴,支承转动零件并与之一起回转以传递运动、扭矩或弯矩的机械零件。
机器中作回转运动的零件就装在轴上。
轴的材料主要采用碳素钢或合金钢,也可采用球墨铸铁或合金铸铁。
轴的工作能力一般取决于强度和刚度。
对轴类零件进行加工,首先应先对零件图分析,选择毛坯,包括尺寸,材料。
然后根据毛坯和零件分析制定初步加工步骤,包括机床的选用,刀具的选择,夹具以及加工方法。
再确定刀具的切削量,转速,进给量。
最后,最终确定加工工艺和加工。
该轴的加工使我对数控机床、数控编程、数控加工工艺得到了进一步认识,为将来从事相关的工作打下了良好的基础。
关键词:
轴类零件加工,编程及加工,工艺分析。
目录
第一章普通车床简介..........................................3
第二章零件加工工艺分析..........................................5
2.1拖拉机半轴的零件分析...................................5
2.2毛坯的选择...........................................6
2.3机床的选择............................................6
2.4工艺的分析................................................6
2.5工艺的制定..............................................7
2.6夹具的选择.............................................11
2.7刀具的选择.............................................12
2.8切削参数的选择..........................................13
第三章零件的检测.........................................15
第四章结论..............................................16
参考文献..................................................16
致谢......................................................17
附录A零件的加工工艺卡片.........................................
第一章、普通车床简介
普通车床
普通车床是能对轴、盘、环等多种类型工件进行多种工序加工的卧式车床,常用于加工工件的内外回转表面、端面和各种内外螺纹,采用相应的刀具和附件,还可进行钻孔、扩孔、攻丝和滚花等。
普通车床是车床中应用最广泛的一种,约占车床类总数的65%,因其主轴以水平方式放置故称为卧式车床。
卡盘
普通车床的主要组成部件有:
主轴箱、进给箱、溜板箱、刀架、尾架、光杠丝杠和床身。
主轴箱:
又称床头箱,它的主要任务是将主电机传来的旋转运动经过一系列的变速机构使主轴得到所需的正反两种转向的不同转速,同时主轴箱分出部分动力将运动传给进给箱。
主轴箱中等主轴是车床的关键零件。
主轴在轴承上运转的平稳性直接影响工件的加工质量,一旦主轴的旋转精度降低,则机床的使用价值就会降低。
进给箱:
又称走刀箱,进给箱中装有进给运动的变速机构,调整其变速机构,可得到所需的进给量或螺距,通过光杠或丝杠将运动传至刀架以进行切削。
丝杠与光杠:
用以联接进给箱与溜板箱,并把进给箱的运动和动力传给溜板
活顶尖
箱,使溜板箱获得纵向直线运动。
丝杠是专门用来车削各种螺纹而设置的,在进工件的其他表面车削时,只用光杠,不用丝杠。
同学们要结合溜板箱的内容区分光杠与丝杠的区别。
溜板箱:
是车床进给运动的操纵箱,内装有将光杠和丝杠的旋转运动变成刀架直线运动的机构,通过光杠传动实现刀架的纵向进给运动、横向进给运动和快速移动,通过丝杠带动刀架作纵向直线运动,以便车削螺纹。
刀架:
刀架部件由几层刀架组成,它的功能是装夹刀具,使刀具作纵向、横向或斜向进给运动。
尾座:
安装作定位支撑用的后顶尖、也可以安装钻头、铰刀等孔加工刀具进行孔加工。
床身:
在床身上安装着车床各个主要部件,是他们在工作是保持准确的相对位置。
第二章零件加工工艺分析
2.1零件的分析:
零件图是制订工艺规程最主要的原始资料。
只有通过对零件图和装配图的分析,才能了解产品的性能、用途和工作条件,明确各零件的相互装配位置和作用,了解零件的主要技术要求,找出生产合格产品的关键技术问题。
零件图的分析包括三项内容:
(1)检查零件图的完整性和正确性
主要检查零件视图是否表达直观、清晰、准确、充分;尺寸、公差、技术要求是否合理、齐全。
如有错误或遗漏,应提出修改意见。
(2)分析零件材料选择是否恰当
零件材料的选择应立足于国内,尽量采用我国资源丰富的材料,尽量避免采用贵重金属;同时,所选材料必须具有良好的加工性。
(3)分析零件的技术要求
包括零件加工表面的尺寸精度、形状精度、位置精度、表面粗糙度、表面微观质量以及热处理等要求。
分析零件的这些技术要求在保证使用性能的前提下是否经济合理,在本企业现有生产条件下是否能够实现。
对于该零件的分析包括以下几点:
1)该零件结构简单,轴的外圆需要磨削加工,为了保证轴同轴度的要求,所以选择两双顶尖孔定位。
2)φ22(上偏差+0.03;下偏差+0.015)的外圆,尺寸的公差等级为IT5-IT6,对公共轴心线的圆跳动公差为0.01。
3)φ17(上偏差—0.006;下偏差—0.013)的外圆,尺寸的公差等级为IT6-IT7,对公共轴心线的同轴度公差为0.01。
4)M8的螺纹孔的尺寸精度要达到H7。
5)粗糙度要求:
φ22和φ17的外圆粗糙度要求较高为1.25um,所以要进行磨削加工,切槽部分的粗糙度要求为2.5um,其余为10um。
分析哪些部分需要加工,一些具有粗糙度要求的地方即是要加工的地方。
分析完零件图样后,根据各表面的结构形状、尺寸、精度和表面粗糙度等技术要求,确定加工方法、加工阶段,划分工序和安排加工顺序。
2.2毛坯的选择
正确选择毛坯类型有着重要的技术经济意义。
轴类零件可根据使用要求、生产类型、设备条件及结构,选用棒料、锻件等毛坯形式。
对于外圆直径相差不大的轴,一般以棒料为主(本零件的外圆直径相差不大);而对于外圆直径相差大的阶梯轴或重要的轴,常选用锻件,这样既节约材料又减少机械加工的工作量,还可改善机械性能。
根据该零件的要求,毛坯材料为棒料,具体为40Cr合金钢,经调质后具有良好的综合力学性能,是使用最广泛的钢种之一。
用于制造中速、中载的零件,如机床齿轮,轴,蜗杆,花键轴等等,它可以代用40MnB,45MnB,35SiMn,42SiMn,40MnVB等等。
零件总长为100mm,粗车φ22(上偏差+0.03;下偏差+0.015)的外圆留加工余量1mm,φ17(上偏差—0.006;下偏差—0.013)的外圆留加工余量0.2——0.3mm,掉头车φ22(上偏差+0.03;下偏差+0.015)的外圆留加工余量0.2——0.3mm,切槽两处至尺寸,所以选择的零件的毛坯尺寸为φ25×104棒料。
2.3机床的选择
综合考虑成本和我厂的现有条件,粗车和精车外圆选用的机床型号为CET112。
该车床备有刀库,具有自动换刀功能,是对工件一次装夹后进行多工序加工。
工件装夹后,数控系统能控制机床按不同工序自动选择、更换刀具、自动对刀、自动改变主轴转速、进给量等,可连续完成多种工序,因而大大减少了工件装夹时间、测量和机床调整等辅助工序时间,对加工形状比较复杂,精度要求较高,品种更换频繁的零件具有良好的经济效果。
钻孔攻丝的设备型号为C620,该车床可在床面上车削400毫米直径的工件,能担任各种不同的车削工作,加工件精度可达二级,它结构合理,操纵灵活,维护调整方便,只需变换操纵手柄,便可车削公制、英制、模数及径节螺纹。
零件两端外圆及端面粗糙度要求要达到1.25,所以要选择磨床加工。
MK1320C外圆磨床是一种可采用多种磨削方式的磨床,适用于小轴这种高精度的零件。
2.4工艺分析
零件的结构工艺性是指所设计的零件在不同类型的具体生产条件下,零件毛坯的制造、零件的加工和产品的装配所具备的可行性和经济性。
零件结构工艺性涉及面很广,具有综合性,必须全面综合地分析。
零件的结构对机械加工工艺过程的影响很大,不同结构的两个零件尽管都能满足使用要求,但它们的加工方法和制造成本却可能有很大的差别。
所谓具有良好的结构工艺性,应是在不同生产类型的具体生产条件下,对零件毛坯的制造、零件的加工和产品的装配,都能以较高的生产率和最低的成本、采用较经济的方法进行并能满足使用性能的结构。
该零件的工艺分析:
1、定位基准选择
工件在加工时,用以确定工件对机床及刀具相对位置的表面,称为定位基准。
最初工序中所用定位基准,是毛坯上未经加工的表面,称为粗基准。
在其后各工序加工中所用定位基准是以加工的表面,称为精基准。
该零件属于小轴类零件,结构简单,轴的外圆面需要磨削加工,为了保证轴的同轴度要求,选择双顶尖孔定位。
2、零件表面加工方法的选择
零件表面的加工,应根据这些表面的加工要求和零件的结构特点及材料性质等因素选用相应的加工方法。
在选择某一表面的加工方法时,一般总是首先选定它的最终加工方法,然后再逐一选定各有关前道工序的加工方法。
3、加工顺序的安排
按加工性质和作用的不同,工艺过程一般可分为三个加工阶段:
(1)粗加工阶段。
主要是切除各加工表面上的大部分余量,所用精基准的粗加工则在本阶段的最初工序中完成。
此轴在加工过程中需粗车φ22外圆,留加工余量1mm。
(2)半精加工阶段。
为各主要表面的精加工做好准备(达到一定精度要求并留有精加工余量),并完成一些次要表面的加工。
此轴在加工过程中需粗车φ22、φ17外圆,留加工余量0.3—0.5mm。
(3)精加工阶段。
使各主要表面达到规定的质量要求,部分精密零件还需精磨后达到尺寸要求,如此轴需经过粗磨留0.1mm余量用于精磨从而达到图面要求。
此外,某些精密零件的加工时还有精整(超精磨、镜面磨、研磨和超精加工等)或光整(滚压、抛光等)加工阶段。
下列情况可以不划分加工阶段,加工质量要求不高或虽然加工质量要求较高,但毛坯刚性好、精度高的零件,就可以不划分加工阶段,特别是用加工中心加工时,对于加工要求不太高的大型、重型工件,在一次装夹中完成粗加工和精加工,也往往不划分加工阶段。
轴的左端有M8X17H螺孔为达到双顶尖定位的目的,螺孔加工的步骤是:
先钻φ5mm的孔,接着是螺纹孔的小径深8mm,但不攻螺纹孔,而增加忽口孔
倒角90。
工步。
在后面的工序中就可以用60.倒角定位了。
划分加工阶段的作用有以下几点:
(1)避免毛坯内应力重新分布而影响获得的加工精度。
(2)避免粗加工时较大的夹紧力和切削力所引发的弹性变形和热变形对精加工的影响。
(3)粗、精加工阶段分开,可较及时地发现毛坯的缺陷,避免不必要的损失。
(4)可以合理使用机床,使精密机床能较长期地保持其精度。
2.5工艺制定
机械加工工艺路线的拟订是制定工艺过程的总体布局,其主要任务是选择各个表面的加工方法和加工方案,确定各个表面的加工顺序以及整个工艺过程中工序数和各工序内容。
拟定过程中应首先确定每步工序的加工定位基准和装夹方法。
然后再将所需的调质处理等工序合理插入工序表中,