套筒铸造工艺设计.docx
《套筒铸造工艺设计.docx》由会员分享,可在线阅读,更多相关《套筒铸造工艺设计.docx(8页珍藏版)》请在冰豆网上搜索。
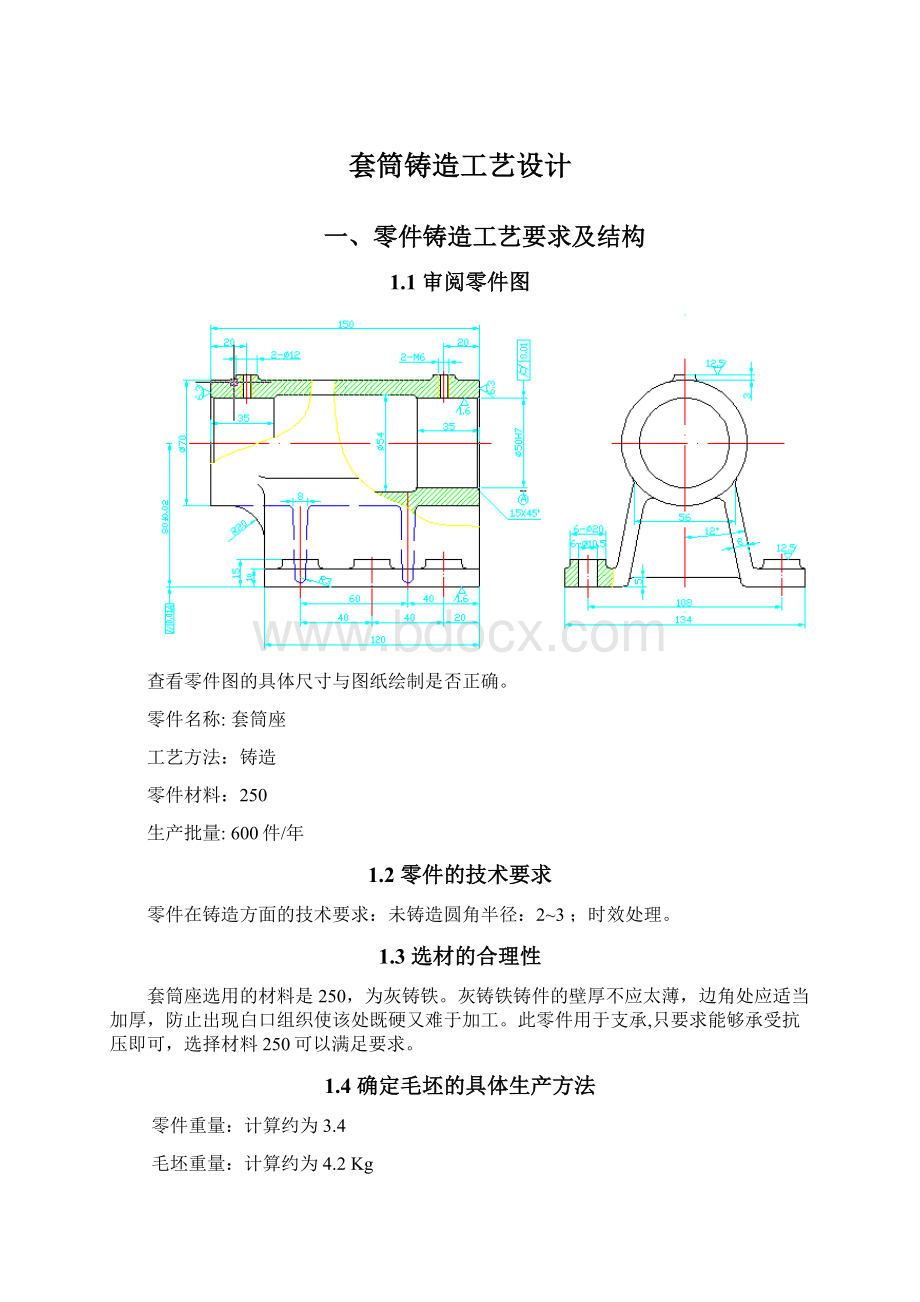
套筒铸造工艺设计
一、零件铸造工艺要求及结构
1.1审阅零件图
查看零件图的具体尺寸与图纸绘制是否正确。
零件名称:
套筒座
工艺方法:
铸造
零件材料:
250
生产批量:
600件/年
1.2零件的技术要求
零件在铸造方面的技术要求:
未铸造圆角半径:
2~3;时效处理。
1.3选材的合理性
套筒座选用的材料是250,为灰铸铁。
灰铸铁铸件的壁厚不应太薄,边角处应适当加厚,防止出现白口组织使该处既硬又难于加工。
此零件用于支承,只要求能够承受抗压即可,选择材料250可以满足要求。
1.4确定毛坯的具体生产方法
零件重量:
计算约为3.4
毛坯重量:
计算约为4.2Kg
生产批量:
600件/年
因为3.4《100,所以判断零件为轻型零件。
由于零件的生产产量为600件/年,所以初步确定为中、小批生产。
由于砂型铸造适用范围广,生产范围广,零件形状比较简单,壁厚比较均匀。
故确定生产方法为砂型铸造。
1.5审查铸件的结构工艺性
铸件轮廓尺寸为150×134×115,查表得砂型铸造的最小壁厚约等于6,套筒座的壁厚符合其要求。
二、铸造工艺方案的确定
2.1铸造、铸型方法的选择
零件形状比较简单,壁厚比较均匀,故毛坯生产方法为砂型铸造,砂型类型为湿砂。
采用湿型粘土砂造型灵活性大,生产率高,生产周期短,便于组织流水生产,易于实现机械化和自动化,材料成本低,节省烘干设备、燃料、电力等,还可延长砂箱使用寿命。
因此,采用湿型粘土砂机器造型,模样采用金属模是合理的。
在造芯用料及方法选择中,如用粘土砂制作砂芯原料成本较低,但是烘干后容易产生裂纹,容易变形。
在大批量生产的条件下,由于需要提高造芯效率,且常要求砂芯具有高的尺寸精度,此工艺所需的砂芯采用热芯盒法生产砂芯,以增加其强度及保证铸件质量。
选择使用射芯工艺生产砂芯。
采用热芯盒制芯工艺热芯盒法制芯,是用液态固性树脂粘结剂和催化剂制成的一种芯砂,填入加热到一定的芯盒内,贴近芯盒表面的砂芯受热,其粘结剂在很短的时间内硬化。
而且只要砂芯表层有数毫米的硬壳即可自芯取出,中心部分的砂芯利用余热可自行硬化。
选择造型方法为手工造型,具体为三箱造型;造芯方法为芯盒造芯。
2.2浇注位置的确定
确定浇注位置应注意以下原则:
1.铸件的重要部分应尽量置于下部
2.重要加工面应朝下或直立状态
3.使铸件的答平面朝下,避免夹砂结疤内缺陷
4.应保证铸件能充满
5.应有利于铸件的补缩
6.避免用吊砂,吊芯或悬臂式砂芯,便于下芯,合箱及检验
选择将浇注位置确定为套筒中心对称面。
2.3分型面的确定
分型面是指两半铸型相互接触的表面。
分型面的优劣在很大程度上影响铸件的尺寸精度、成本和生产率。
而选择分型面时应注意一下原则:
1.应使铸件全部或大部分置于同一半型内
2.应尽量减少分型面的数目
3.分型面应尽量选用平面
4.便于下芯、合箱和检测
5.不使砂箱过高
6.受力件的分型面的选择不应削弱铸件结构强度
7.注意减轻铸件清理和机械加工量
分型面应确定为套筒中心对称面和铸件下表面,以便顺利起模、下芯、充型。
三、铸造工艺参数的确定
铸造工艺设计参数通常是指铸型工艺设计时需要确定的某些数据,这些工艺数据一般都与模样及芯盒尺寸有关,及与铸件的精度有密切关系,同时也与造型、制芯、下芯及合箱的工艺过程有关。
这些工艺数据主要是指加工余量、起模斜度、铸造收缩率、最小铸出孔、型芯头尺寸、铸造圆角等。
工艺参数选取的准确、合适,才能保证铸件尺寸精确,使造型、制芯、下芯及合箱方便,提高生产率,降低成本。
3.1砂芯设计
1)套筒座圆筒部分
对于套筒座圆筒部分,其可以用一个整体砂芯来形成,因此为该孔单独设一个砂芯,以便下芯后检查并调整四周壁厚至均匀。
芯头设计:
由《课程设计资料》得,芯头长度确定为40,水平芯头顶面与芯座的间隙为S1=0.3。
2)中箱支承部分
对于中箱支承部分,两边砂芯采用相同的水平芯头来定位和固定。
芯头设计:
由《课程设计资料》得,芯头长度确定为40,水平芯头顶面与芯座的间隙为S1=0.3。
说明:
其余两处凹槽采用自带砂芯方式。
3.2工艺参数的确定
工艺参数的确定包括以下几个方面的内容
1.加工余量
1)尺寸公差
铸件尺寸公差是指铸件公称尺寸的两个允许的极限尺寸之差。
在两个允许极限尺寸之内,铸件可满足机械加工,装配,和使用要求。
此零件为砂型铸造机器造型大批量生产,由《铸造工艺设计》查表1-10得:
铸件的加工余量的公差等级:
13~15。
又由表3-49《铸造手册》选择加工余量等级为14H。
2)加工余量
机械加工余量是铸件为了保证其加工面尺寸和零件精度,应有加工余量,即在铸件工艺设计时预先增加的,而后在机械加工时又被切去的金属层厚度。
套筒为砂型铸造机器造型大批量生产,由《铸造工艺设计》查表1-13得:
单边加工余量为9,双边的加工余量为6
2.起模斜度
为了方便起模,在模样、芯盒的出模方向留有一定斜度,以免损坏砂型或砂芯。
这个斜度,称为起模斜度。
起模斜度应在铸件上没有结构斜度的,垂直于分型面的表面上应用。
由《铸造工艺设计》查表1-15得:
模样外表面的拔模斜度为:
1º25´;内表面的拔模斜度为:
2º50´。
3.铸造圆角
选择铸造方法“砂型铸造”,材料“250”,查表得铸造圆角的值为3,(铸造圆角计算公式1/5~1/10()) 。
4.铸造收缩率
铸造收缩率又称铸件线收缩率,用模样与铸件的长度差除以模样长度的百分比表示:
ε=[(L12)1]*100%
ε—铸造收缩率
L1—模样长度
L2—铸件长度
支座受阻收缩率由《铸造工艺设计》查表1-14得:
受阻收缩率为0.9%,自由收缩率为1.0%。
5.最小铸出孔
零件上的孔、槽、台阶等,究竟是铸出来好还是靠机械加工出来好,这应该从品质及经济角度等方面考虑。
一般来说,较大的孔、槽等应该铸出来,以便节约金属和加工工时,同时还可以避免铸件局部过厚所造成热节,提高铸件质量。
较小的孔、槽或则铸件壁很厚则不易铸出孔,直接依靠加工反而方便。
由《铸造工艺设计》查表1-5得:
直径为15~30。
6.灰铸铁的机械加工余量等级为H级。
四、浇注系统设计
浇注系统的一般设计内容有:
浇口杯、直浇道、横浇道和内浇道。
浇注系统截面积的大小对铸件质量也有很大影响。
截面积太小,浇注时间长,可能产生浇不足、冷隔、砂眼等缺陷;截面积过大,浇注速度快,又可能引起冲砂,带入熔渣和气体,使铸件产生渣孔、气孔等缺陷。
为了使金属液以适宜的速度充填铸型,就必须合理确定浇注系统的面积。
4.1浇注系统类型的选择
浇注系统分为封闭式浇注系统,开放式浇注系统,半封闭式浇注系统和封闭-开放式浇注系统。
因为封闭式浇注系统控流截面积在内浇道,浇注开始后,金属液容易充满浇注系统,呈有压流动状态。
挡渣能力强,但充型速度快,冲刷力大,易产生喷溅,金属液易氧化。
适用于湿型铸件小件。
而套筒就是采用湿型的铸件小件,所以选择封闭式浇注系统。
4.2浇注系统的设计与计算
按照铸件的基本尺寸(包括加工余量在内)计算出铸件的体积和铸件的质量。
此铸件为4.2kg,金属液总质量G为铸件的1.3倍,则金属液总质量为:
G=4.2×1.3=5.46kg
根据公式:
式中浇注时间
浇注重量,此时5.46
系数
查《课程设计资料》得,S=2.2
代入和S相应数值计算可得浇注时间:
t=5.141s
平均静压头的确定:
选择μ=0.42,此数据由《课程设计资料》查得。
选择浇注方式为中间注入式,运用平均静压力头高度计算公式:
H08
其中:
H0-浇口杯顶面到分型面的距离;铸件在铸型中的总高度。
08=70-115/8=70-14.4=55.6mm。
运用灰铸铁件浇注系统内浇道的最小横截面积计算公式:
代入G、、μ、t相应数值计算,得内浇道的最小控流截面积为F内=3.46cm²。
对于封闭式浇注系统,中、小型铸铁件(砂型)直浇道截面积为内浇道截面积的1.15倍,横浇道截面积为内浇道截面积的1.1倍,即F直=1.15×3.46=3.98cm²,
F横=1.1×3.46=3.81cm²。
查表得各浇道的具体尺寸:
F内=4cm²,a=38mm,30mm,12mm
F直=4.9cm2,直径25
F横=4cm²,a=20mm,15mm,23mm
五、冒口设计
冒口是铸型内用于储存金属液的空腔,在铸件形成时补给金属,有防止缩孔、缩松、排气、集渣的作用。
支座所用的蠕墨铸铁在凝固时其体积变化情况与一些工业上常用的金属及合金不同,其特点是在液态冷却时发生收缩,冷却至共晶温度时停止收缩,由于析出石墨而发生膨胀,在接近凝固终了时余下的液态金属凝固时又开始收缩,直至凝固结束。
所以其凝固时的膨胀和液态收缩趋于互相补偿。
故蠕墨铸铁补缩时需要的铁水量少,而且支座壁厚均匀无厚大壁,所以可利用浇注系统进行补缩不设置冒口。
为了防止铸件浇不足和产生气孔缺陷,须设计出气孔,以排除型内的气体。
六、铸件工艺图
七、铸件图
一、零件铸造工艺要求及结构1
1.1审阅零件图1
1.2零件的技术要求1
1.3选材的合理性1
1.4确定毛坯的具体生产方法2
1.5审查铸件的结构工艺性2
二、铸造工艺方案的确定2
2.1铸造、铸型方法的选择2
2.2浇注位置的确定3
2.3分型面的确定3
三、铸造工艺参数的确定4
3.1砂芯设计4
3.2工艺参数的确定4
四、浇注系统设计6
4.1浇注系统类型的选择6
4.2浇注系统的设计与计算6
五、冒口设计8
六、铸件工艺图9
七、铸件图9