大众汽车标志件注塑模具设计Word格式文档下载.docx
《大众汽车标志件注塑模具设计Word格式文档下载.docx》由会员分享,可在线阅读,更多相关《大众汽车标志件注塑模具设计Word格式文档下载.docx(18页珍藏版)》请在冰豆网上搜索。
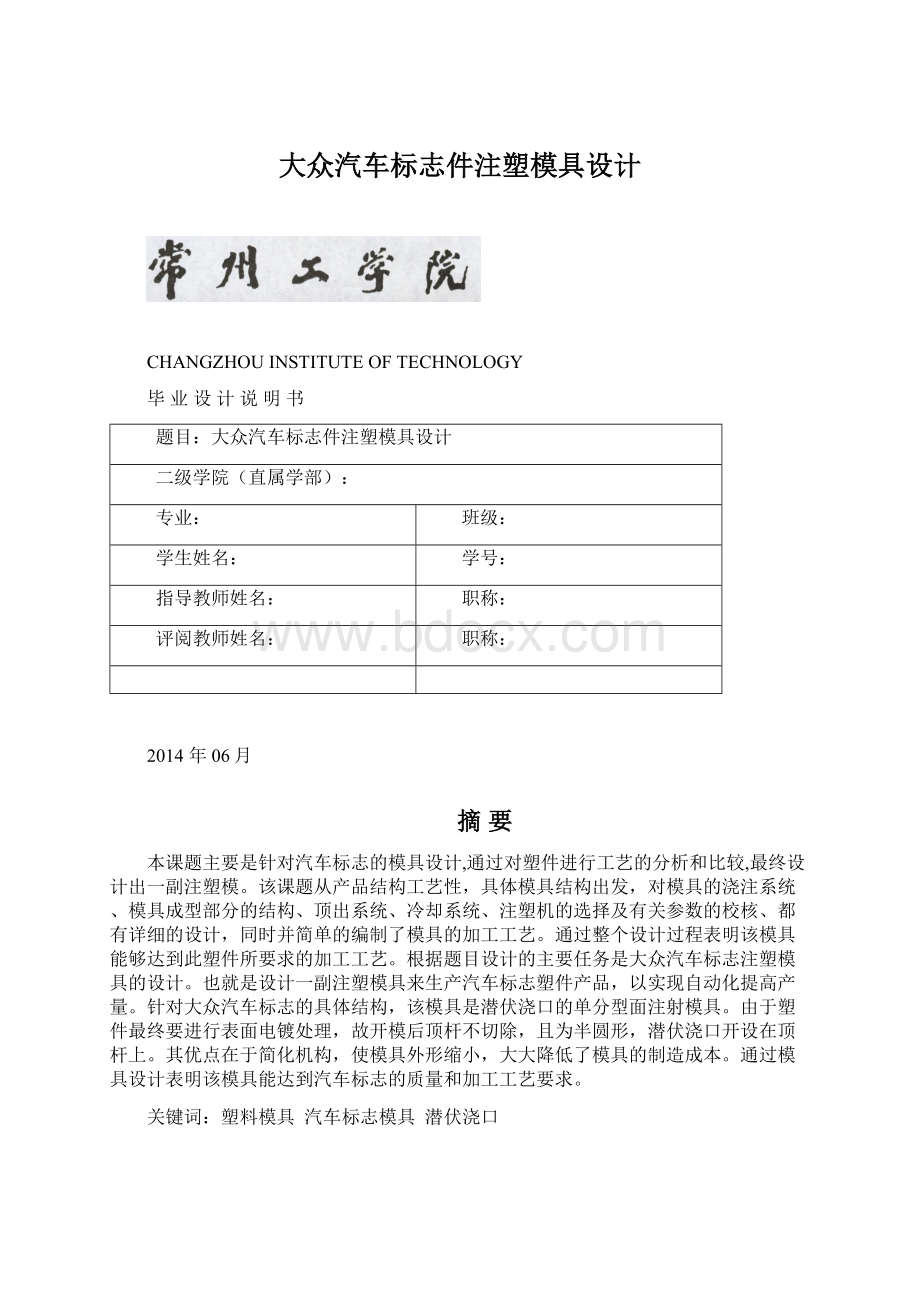
本次毕业设计的主要任务是汽车标志注塑模具的设计。
也就是设计一副注塑模具来生产大众汽车标志塑件产品,以实现自动化提高产量。
针对大众汽车标志的具体结构,通过此次设计,使我对潜伏浇口模具的设计有了较深的认识。
同时,在设计过程中,通过查阅大量资料、手册、标准、期刊等,结合教材上的知识也对注塑模具的组成结构(成型零部件、浇注系统、导向部分、推出机构、排气系统、模温调节系统)有了系统的认识,拓宽了视野,丰富了知识,为将来独立完成模具设计积累了一定的经验。
第2章完成零件材质及注塑工艺性分析
2.1塑件材料特性
ABS塑料(丙烯腈-丁二烯-苯乙烯共聚物)是在聚苯乙烯分子中加入了丙烯腈、丁二烯等异种单体而成的改性共聚物,也可以成为改性聚苯乙烯,具有比苯乙烯更好的使用性能和工艺性能。
ABS塑料是一种常用的具有良好的综合力学性能的工程材料。
他具有一定的耐磨性、耐寒性、耐水性和耐油性、化学稳定性。
不透明,无毒,无味,成型塑件的表面有较好的光泽。
其缺点是耐热性不高,耐气候性较差,在紫外线的作用下易变硬、发脆。
ABS的物理及力学性能
密度/(g/cm
)
1.03~1.07
断裂伸长率/%
35
熔点/℃
抗弯曲强度/MPa
80
-40
拉伸弹性模量/GPa
1.8
抗拉强度/MPa
38
缺口冲击韧度
11
抗压强度
53
无缺口冲击韧度
261
屈服强度
50
弯曲弹性模量
1.4
2.2塑料成型工艺参数
由塑件材料ABS查表取工艺参数:
料筒温度/℃:
后段150~170中段165∽180前段180∽200
模具的温度℃:
50∽180
注射压力MPa:
60∽100
注射时间t/s:
20∽90
高压时间t/s:
0∽5
冷却时间t/s:
20∽120
总生产时间t/s:
50∽220
2.3塑件材料成型性能
(1)该塑件尺寸较小,一般精度等级,为降低成型费用,采用一模多腔,并不对该制品进行后加工。
为了满足制品高光亮及零件表面最终要电镀的要求与提高成型效率采用潜伏式浇口。
(2)为了方便加工和热处理,型腔与型芯部分采用拼镶结构。
(3)为零件最终要进行表面电镀处理,故开模后顶杆不切除,且为半圆形,潜伏浇口开设在顶杆上。
(4)ABS有极好的抗冲击强度、机械强度和一定的耐磨性,有一定的硬度和尺寸稳定性,易与成型加工。
(5)ABS在升温时粘度增高,所以成型压力较高,故塑件上的脱模斜度宜较大;
ABS易吸水,成型加工前应进行干燥处理;
ABS易产生熔接痕,故应尽量减少浇注系统对料流的阻力;
在正常的成型条件下,壁厚、熔料温度对收缩率影响较小。
此注塑模为汽车标志要求塑件有光泽,模具温度应控制在60~80℃。
产品设计图及技术要求见图2-1
图2-1产品设计图
第3章完成浇口位置确定及浇注系统的设计
3.1确定分型面的位置
如何确定分型面,需要考虑的因素比较复杂。
由于分型面受到塑件在模具中的成型位置、浇注系统设计、塑件的结构工艺性及精度、嵌件位置形状以及推出方法、模具的制造、排气、操作工艺等多种因素的影响,因此在选择分型面时应综合分析比较,从几种方案中优选出较为合理的方案。
选择分型面时一般应遵循以下几项原则:
(1)保证塑料制品能够脱模
这是一个首要原则,因为我们设置分型面的目的,就是为了能够顺利从型腔中脱出制品。
根据这个原则,分型面应首选在塑料制品最大的轮廓线上,最好在一个平面上,而且此平面与开模方向垂直。
分型的整个廓形应呈缩小趋势,不应有影响脱模的凹凸形状,以免影响脱模。
(2)使型腔深度最浅
模具型腔深度的大小对模具结构与制造有如下三方面的影响:
1)目前模具型腔的加工多采用电火花成型加工,型腔越深加工时间越长,影响模具生产周期,同时增加生产成本。
2)模具型腔深度影响着模具的厚度。
型腔越深,动、定模越厚。
一方面加工比较困难;
另一方面各种注射机对模具的最大厚度都有一定的限制,故型腔深度不宜过大。
3)型腔深度越深,在相同起模斜度时,同一尺寸上下两端实际尺寸差值越大。
若要控制规定的尺寸公差,就要减小脱模斜度,而导致塑件脱模困难。
因此在选择分型面时应尽可能使型腔深度最浅
(3)使塑件外形美观,容易清理
尽管塑料模具配合非常精密,但塑件脱模后,在分型面的位置都会留有一圈毛边,我们称之为飞边。
即使这些毛边脱模后立即割除,但仍会在塑件上留下痕迹,影响塑件外观,故分型面应避免设在塑件光滑表面上,塑件割除毛边后,在塑件光滑表面留下痕迹。
1)尽量避免侧向抽芯
塑料注射模具,应尽可能避免采用侧向抽芯,因为侧向抽芯模具结构复杂,并且直接影响塑件尺寸、配合的精度,且耗时耗财,制造成本显著增加,故在万不得己的情况下才能使用。
2)使分型面容易加工
分型面精度是整个模具精度的重要部分,力求平面度和动、定模配合面的平行度在公差范围内。
因此,分型面应是平面且与脱模方向垂直,从而使加工精度得到保证。
如选择分型面是斜面或曲面,加工的难度增大,并且精度得不到保证,易造成溢料飞边现象。
3)使侧向抽芯尽量短
抽芯越短,斜抽移动的距离越短,一方面能减少动、定模的厚度,减少塑件尺寸误差;
另一方面有利于脱模,保证塑件制品精度。
4)有利于排气
对中、小型塑件因型腔较小,空气量不多,可借助分型面的缝隙排气。
因此,选择分型面时应有利于排气。
按此原则,分型面应设在注射时熔融塑料最后到达的位置,而且不把型腔封闭
综上所述,选择注射模分型面影响的因素很多,总的要求是顺利脱模,保证塑件技术要求,模具结构简单制造容易。
当选定一个分型面方案后,可能会存在某些缺点,再针对存在的问题采取其他措施弥补,以选择接近理想的分型面。
结构是典型的单分型面结构,分型面设于产品背面的平面,分型面与产品正面部分设置在模具定模部分,另外一侧设于动模部分,顶杆设于动模上。
3.2确定浇口形式及位置
3.2.1内浇口的确定
浇口的形式众多,通常都有边缘浇口、扇形浇口、平缝浇口、圆环浇口、轮辐浇口、点浇口、潜伏式浇口、护耳浇口、直浇口等。
由于产品的外观质量要求较高,所以就不能直接将浇口设置在产品的正面或周边,即不能使用侧浇口、点浇口等形式,故采用潜伏浇口,把浇口通过,在分型面的动模一侧上进入顶杆,在顶杆顶端部位设置潜伏式浇口的进料方式。
浇口位置如下图1所示
图3-1浇口位置
浇口直径根据经验值取d=1.2mm
浇口锥角取ß
=15。
浇口倾斜角取à
=45。
浇口尺寸如图3-2所示
图3-2浇口尺寸
3.2.2横浇道的确定
浇注系统可分为普通浇注系统和热流道浇注系统两大类。
浇注系统控制着塑件成型过程中充模和补料两个重要阶段,对塑件质量关系极大。
浇注系统是指从注塑机喷嘴进入模具开始,到型腔入口为止的那一段流道。
普通模具的浇注系统由主流道、分流道、浇口、冷料井几部分组成。
采用圆形分流道截面,加工较容易,且热量损失与压力损失均不大,为常用形式。
圆形截面分流道的直径可根据塑料的流动性等因素确定,该塑料件采用ABS塑料,流动性为中等,所以选用圆形截面的分流道。
根据经验值分流道的直径d可以取5~6mm。
根据型腔在分型面上的排布情况可分为一次分流道和二次分流道。
3.2.3主流道的设计
主流道与喷嘴的接触处多作成半球形的凹坑。
二者应严密接触以避免高压塑料的溢出,凹坑球半径比喷嘴球头半径大1-2mm;
主流道小端直径应比喷嘴孔直径约大0.5-1mm,常取Ф4-8mm,视制品大小及补料要求决定。
大端直径应比分流道深度大1.5mm以上,其锥角不宜过大,一般取2°
~6°
,内壁粗糙度Ra取0.4mm。
主流道、分流道及型腔在模具中的位置尺寸如图3所示
图3-3位置尺寸图
第4章完成模具成型零部件尺寸计算和设计
型腔是模具上直接成型塑料制件的部位。
直接构成模具型腔的所有零件的所有零件都称为成型零件,通常包括:
凹模、凸模、成型杆、成型环、各种型腔镶件等。
鉴于制件的特殊结构,凹模镶块采用铣床加工,凸模采用电火花加工。
4.1成型零件的计算
查文献[1]表6-4ABS塑料的收缩率是0.3%~0.6%。
平均收缩率S=(0.3%+0.6%)/2=0.45%
型腔径向尺寸Lm0+бz=[(1+s)Ls-xΔ]+бzo
型腔深度尺寸Hm+бz0=[(1+s)Hs-xΔ]+бz0
型芯径向尺寸lm0-бz=[(1+s)ls+xΔ]0-бz
型芯高度尺寸hm0-бz=[(1+s)hs+xΔ]0-бz
中心距尺寸(Cm)±
бz/2=(1+S)Cs±
бz/2
式中Ls——塑件外型径向基本尺寸的最大尺寸(mm)
ls——塑件内型径向基本尺寸的最小尺寸(mm)
Hs——塑件外型高度基本尺寸的最大尺寸(mm)
Hs——塑件内型深度基本尺寸的最小尺寸(mm)
Cm——中心距的基本尺寸(mm)
X——修正系数,取0.5~0.75。
Δ——塑件公差
бz——模具制造公差,取(1/3~1/4)Δ
未注公差采取MT5级精度。
Ф40→Ф400-0.64
Ф32→Ф32+0.560
18→18±
0.19
2→2+0.20
R3→R30-0.20
3→3±
0.10
10→10±
0.14
5→50-0.44
则
S=0.45%бz=△/3бc=△/6X=0.75
4.2成型尺寸分类
型腔尺寸:
Ф400-0.64、50-0.44、R30-0.20
型芯尺寸:
Ф32+0.560 、2+0.20、5+0.440
中心距尺寸:
3±
0.10、10±
0.14、18±
4.3零部件尺寸的计算
①Ф400-0.64Lm0+бz=[(1+s)Ls-xΔ]+бz0=[(1+0.45%)x40—0.75x0.64]+0.64/30=39.7+0.2130mm
验证(Smax-Smin)Ls1+бz+бc<0
(0.6%-0.3%)x40+0.64/3+0.64/6=0.12+0.213+0.107=0.44<0.64成立
②50-0.44Hm+бz0=[(1+s)Hs-xΔ]+бz0=[(1+0.45%)x5-1/2x0.44]+0.44/30
=4.803+0.1470mm
验证(Smax-Smin)Hs+бz+бj<△
(0.6%-0.3%)x5+0.44/3+0=0.162<0.44成立
③R30-0.20Lm0+бz=[(1+s)Ls-xΔ]+бzo=[(1+0.45%)x3-0.75x0.2]+0.20/30
=2.864+0.070mm
(0.6%-0.3%)x3+0.2/3+0.2/6=0.009+0.07+0.033=0.112<0.2成立
④Ф32+0.560lm0-бz=[(1+s)ls+xΔ]0-бz=[(1+0.45%)x32+0.75x0.56]0-0.187
=32.5640-0.187mm
验证(Smax-Smin)ls+бz+бc<△
(0.6%-0.3%)x32+0.56/3+0.56/6=0.376<0.56成立
⑤2+0.20lm0-бz=[(1+s)ls+xΔ]0-бz=[(1+0.45%)x2+0.75x0.2]0-0.2/3
=2.1590-0.067mm
(0.6%-0.3%)x2+0.2/3+0.2/6=0.106<0.2成立
⑥5+0.440hm0-бz=[(1+s)hs+xΔ]0-бz=[(1+0.45%)x5+1/2x0.44]=5.24250-0.147mm
验证(Smax-Smin)hs+бz+бj<△
(0.6%-0.3%)x5+0.44/3+0=0.162<0.44成立
⑦3±
0.10(Cm)±
бz/2=(1+0.45%)x3±
0.1/2
=3.0125±
0.05mm
验证(Smax-Smin)Cs<△
(0.6%-0.3%)x3=0.009mm<0.10mm成立
⑧10±
0.14(Cm)±
бz/2=(1+0.45%)x10±
0.14/2
=10.045±
0.07mm
验证(Smax-Smin)Cs<△
(0.6%-0.3%)x10=0.03<0.14成立
⑨18±
0.19(Cm)±
бz/2=(1+0.45%)x18±
0.19/2
=18.081±
0.095mm
(0.6%-0.3%)x18=0.054<0.19成立
第5章完成模具结构零部件计算、设计及选用(支撑零部件、标准模架等)
5.1选用模架
5.1.1型腔强度和刚度的计算
型腔为整体式,因此型腔的强度和刚度按型腔为整体式进行计算,由于型腔壁厚计算比较麻烦也可参照经验推荐数据。
查文献[1]表6-16型腔侧壁厚δ=20mm
5.1.2选用标准模架
根据以上分析、计算以及型腔尺寸及位置尺寸可确定模架的结构形式和规格。
查文献[1]表7-1、7-3选用A4—200250—08—Z2GB/T12556.1—1990.
定模板厚度:
A=25mm
动模板厚度B=20mm
垫块厚度:
C=50mm
模具厚度:
H模=197mm
模具外形尺寸:
250mmx250mmx186mm
5.2支撑零部件的设计
5.2.1支撑板的设计
支撑板应具有高的平行度和必要的硬度和强度,应结合动模成型部分受力状况进行厚度计算。
由于支撑板厚度计算比较麻烦,也可参考经验推荐数据。
由文献[2]表7.3动模支撑板厚度h=32mm。
5.2.2垫块设计
对于外形为圆形的模具,垫块单独设计成一个零件比较经济。
图5-1尺寸h1提供了推出元件安装及其运动空间,它是由推杆、固定板、推板及推出行程确定的其值确定为50mm。
H1的尺寸按模具的具体结构要求选用标准值,H1的尺寸为40mm。
L1是连接动模座板、垫块、支撑板及动模板采用内六角螺钉直接固定是两螺钉穿过孔之间的距离,其尺寸大小为176mm。
D是装配动模部分是内六角螺钉穿过孔,尺寸L长度适中,可采用2个螺钉过孔,d是动模部分装配时定位销孔L2的尺寸大小为2.6cm见图5-1。
图5-1垫块零件
5.2.3定模座板、动模板的设计
(1)选用的模板在注射机上的安装
在选用设计时应注意模板外形尺寸不受注射机拉杆间距的影响;
动、定模安装孔的位置和孔径与注射机固定模板及移动模板的一系列螺孔相匹配以便安装压紧模具。
(2)动、定模座板的厚度
动、定模座板是分别与注射机的移动工作台面和固定工作台面接触的模板,对刚度和强度要求不高,一般可采用Q235或45钢材料,也不需要对其进行热处理。
为了把模具固定在注射机上,动、定模座板的两侧均需比动、定模板的外形尺寸加宽25~30mm。
5.2.4合模导向机构的设计
(1)导柱设计
模具结构较小,同时为了能够顺序合模,决定选用带头导柱,为避免出现导柱未导正方向而型芯先进入型腔的情况,导柱导向部分高度应比凸模端面的高度高出8~12mm。
由于导柱前端做成半球形加工困难,所以导柱前端做成锥台形,以使导柱能顺利地进入导向孔。
综上所述导柱的尺寸选用Φ20x40x20GB/T4169.-1984。
导柱采用20钢,表面渗碳淬火处理,硬度为50~55HRC。
导柱固定部分的表面粗糙度为Ra=0.8μm导向部分的表面粗糙度为Ra=0.4~0.8μm。
采用4根导柱,导柱固定在动模部分,合理均布在模具分型面的四周,导柱中心至模具边缘的距离为20mm以保证模具的强度。
其安装尺寸见图5-2
图5-2安装尺寸
导柱固定端与模板之间一般采用H7/m6或H7/k6的过渡配合,导柱的导向部分通常采用H7/f7或H8/f7的间隙配合。
(2)导向孔的设计
导向孔采用有导套式的,导套采用带头导套。
为使导柱顺利进入导套,导套的前端应倒圆角。
导向孔最好作成通孔,以利于排出孔内的空气。
导套的材料可用与导柱相同的材料或铜合金等耐磨材料材料制造,但其硬度应略底于导柱硬度,这样可以减轻磨损,以防止导柱或导套拉毛。
带头导套用H7/m6或H7/k6过渡配合镶入模板,导套固定部分的粗糙度为Ra=0.8μm,导向部分粗糙度为Ra=0.4~0.8μm
第6章完成推出机构设计
从大众标志的具体形状和结构来看,其尺寸不大,但标志的内部有许多的胫肋,若其上不加推杆在推出时很容易将其胫肋变形或拉断因此,采用10杆推出。
根据制品的结构特点,确定在四个活动镶件上设置四根普通的半圆顶杆其位置在两根短胫的结合位置同时潜伏浇口的位置位于其上,在制件的外圆环上设置.4根普通的圆形顶杆,由于塑料件的内侧有四个长的胫,所以在每根胫上设置一根普通圆形顶杆其位置位于两根短胫的结合处,此外在一次横流道和二次横流道中的凝料也需要用推杆将其推出,考虑到一次横流道和二次横流道的长度,确定采用4根推杆所以如图6-1所示
图6-1推杆固定板示意图
普通的圆形顶杆按GB/T1298——1984选用,均可以满足要求。
查[文献1]表7-13,选用Φ2.5mmx78mm型号的圆形顶杆40根;
选用φ2.5mm×
75.5mm型号的圆形顶杆4根。
第7章完成冷却系统设计
由于制品平均壁厚为5mm左右,制品尺寸不大,确定水孔的直径为5mm。
由于冷却水道的位置、结构形式、表面状况、水的流速、模具的材料等很多因素都会影响模具的热量向冷却水传递,精确计算比较困难。
实际生产中,通常都是根据模具的结构来确定冷水水路,通过调节水温、水速来满足要求。
由于动模中由型芯和固定板和件组成,受结构限制,冷却水路布置如下图7-1。
图7-1水流道示意图
第8章完成注塑机床的选择(合模尺寸、注塑机克数等)
本次设计与实际在工厂中的设计有所不同。
工厂中的注塑机是已有固定的,模具设计人员通常都是根据车间内的注塑机来确定最大的之间产量,即是说厂中的注塑机选择是有限的。
而在本次设计中,我们选择注塑即的原则则是按我们想象中的产品产量和实际的塑件形状来选择任何一款注塑机,最后校核能满足使用要求即可。
这样同样也可以达到训练的目的。
8.1初选注射机
8.1.1注射量
按照图示尺寸近似计算:
塑件体积Vs≈3.25cm3
查文献[1]表6-1塑料ABS的密度为1.02~1.05g/cm3(注射级密度为1.05g/cm3)
单件塑件重量ms=3.25x1.05g=3.4125≈4g
浇注系统重量的计算可根据图3浇注系统的尺寸先计算浇注系统的体积
Vj≈∏R2L=3014x2.52x115+3014x1.752x47.5
≈2.7mm3
总体积V塑件=(4x3.25+2.7)cm2=15.7cm3
总重量M=15.7x1.05g≈16.49g
聚苯乙烯的密度为1.054g/cm3,ABS塑料密度为1.02~1.05g/cm3
满足注射量V机≥V塑件/0.80
式中V机——额定注射量(cm3)
V塑件——塑件与浇注系统凝料体积和(cm3)
V塑件/0.80=15.7/0.80=19.63cm3
或满足注射量M机≥M塑件ρ1(ρ2x0.8)
式中M机——额定注射量(g)
M塑件——塑件与浇注系统凝料的重量和(g)
ρ1——聚苯乙烯的密度(g/cm3)
ρ2——塑件采用塑料的密度(g/cm3)
M塑件ρ2/ρ1x=16.49x1.05/1.054x0.8g=17.3145/0.8432=20.53g
8.1.2注射压力
P注≥P成型
查文献[1]表6-5ABS塑料成型时的注射压力P成型=70~90Pma
8.1.3锁模力
P锁模力≥PF
式中P——塑料成型时型腔压力,ABS塑料的型腔压力P=30Mpa
F——浇注系统和塑件在分型面上的投影面积和(mm2)
各型腔及浇注系统在分型面上的投影面积(尺寸参照图3)
F1=(L1+L2)b+3x∏R2=(75+2x20)x5+3x3.14x2.52=115x5+58.875=633.88mm2
F2=4∏R2=4x3.14x202=5024mm2
F总=F1+F2=633.88+5.24mm2=5657.88mm2
PF=30x5657.88N=169.74KN
根据以上分析、计算查文献[1]表6-24,初选注射机型号为:
XS-Z-30
注射机XS-Z-30有关技术参数如下:
最大开合模行程S160mm
模具最大厚度180mm
模具最小厚度60mm
喷嘴圆弧半径12mm
喷嘴孔直径2mm
动、定模板尺寸250mmx280mm
拉杆空间235mm
8.2注塑机相关参数的校核
8.2.1注塑压力的校核
查《模具设计与制造简明手册》P47表3-1常用热塑性塑料注射成型工艺参数
注射压力
80MPa<
119MPa(选择的注塑机实际注射压力),合乎要求。
8.2.2锁模力的校核
锁模力是指当高压熔体充满模具型腔时,会在型腔内产生一个很大的力,力图使模具分型面涨开,其值等于塑件和流道系统在分型面上总的投影面积乘以型腔内塑料压力。
作用在这个面上的力应小于注塑机