液膜脱硫醇与碱液富氧再生组合工艺的应用Word格式.docx
《液膜脱硫醇与碱液富氧再生组合工艺的应用Word格式.docx》由会员分享,可在线阅读,更多相关《液膜脱硫醇与碱液富氧再生组合工艺的应用Word格式.docx(14页珍藏版)》请在冰豆网上搜索。
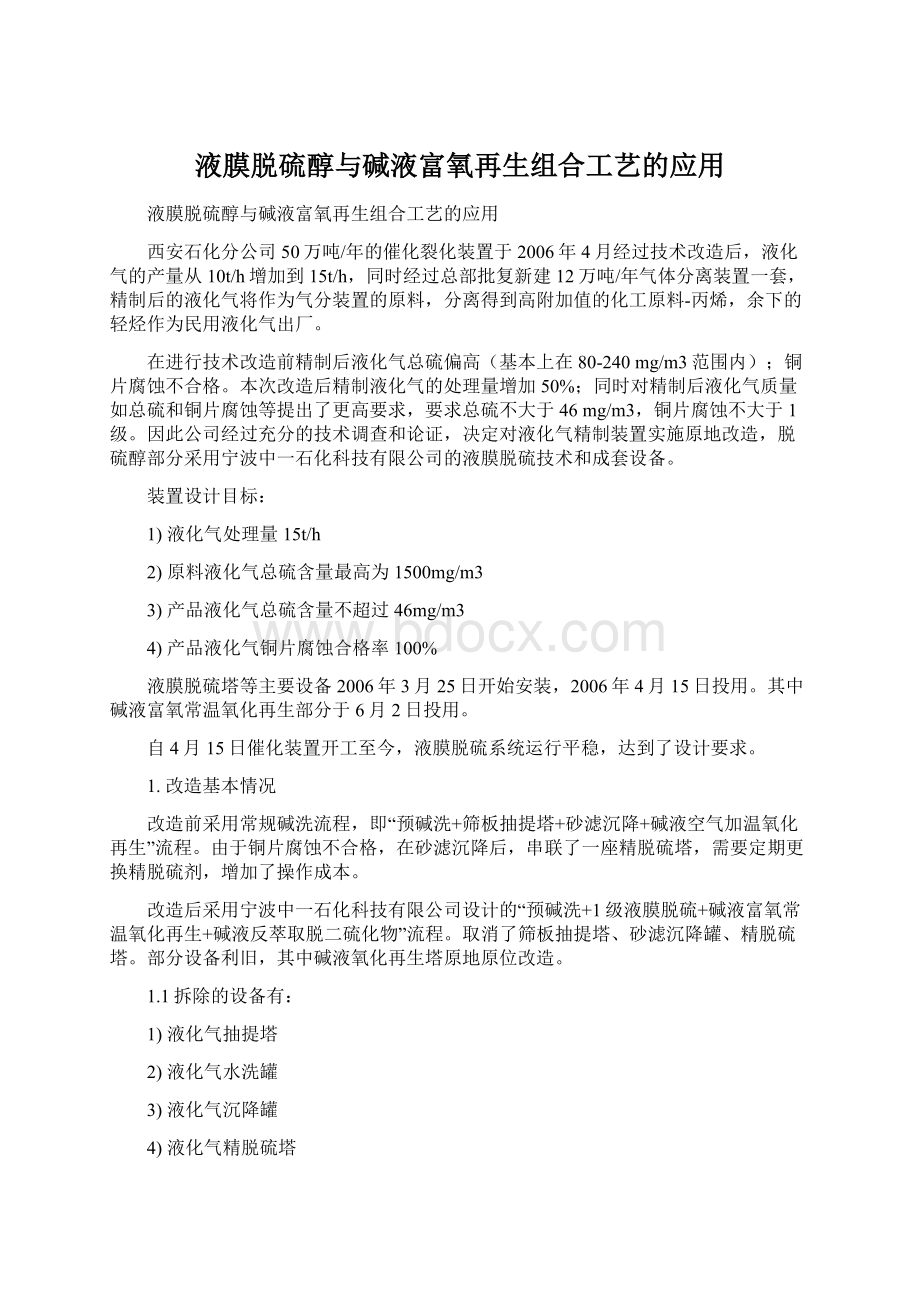
分析方法:
序号
项目
分析方法
1
液化气总硫
SH/T0233-92
2
液化气铜片腐蚀
SH/T0232-92
3
碱液总碱度
酸碱滴定法
4
碱液中硫醇钠
电位滴定法,ZYSK0201-06
5
液化气夹带碱液量
李森科瓶挥发法,ZYSK0203-06
6
尾气中氧含量
OX100A测氧仪
7
尾气中二硫化物含量
微库仑法,ZYSK0205-06
3.开工初期情况
开工初期,由于碱液循环泵的扬程偏小、原碱液储罐未吹扫干净等原因,碱液精细过滤器经常堵塞需要频繁切换吹扫再生。
碱液循环量上不去,经常达不到设计要求。
约2周后更换同型号的滤芯后,过滤器使用周期逐步恢复正常。
碱液循环量控制也恢复正常。
液化气过滤器使用情况正常,压差一般在0.05MPa左右。
液膜塔的阻力降小于0.05MPa。
由于开工初期催化装置加工的低硫原油,原料液化气中总硫含量不高,基本在150mg/m3以下,精制后产品的总硫则大多在10-50mg/m3之间。
因此,碱液浓度也控制在15-20%;
碱液富氧氧化再生暂缓投用。
碱液未氧化,循环利用至今。
4.液化气脱总硫情况
主要工艺条件:
液化气处理量
t/h
预碱洗碱液循环量
液膜塔碱液循环量
(顶端)
(顶侧端)
碱液浓度
%wt
碱液再生用富氧浓度
%v
富氧空气进料量
NM3/H
10-13
0.8-1.0
0.3-0.40
15-20
45
操作温度:
35℃左右
操作压力:
1.0-1.2MPa
主要分析数据表参见表1
表1:
主要分析数据表
日期
(每日上午
9:
00样)
未精制液化气总S
精制液化气总S
碱液中NaRS浓度
铜片腐蚀
备注
(mg/m3)
(%)
20060416
\
52
20060417
62
20060418
56
20060419
43
20060420
153
28
12.8
20060421
109
13.8
碱液循环不正常
20060422
73
11.1
20060423
64
14.7
20060424
74
12.9
0.1
合格
20060425
33
13.4
20060426
83
16.6
20060427
15.7
20060428
55
24.7
补充30%的新碱10吨
20060429
51
21.8
20060430
91
20060501
63
18.6
20060502
65
20060503
23
18.4
20060504
20060505
20060506
50
17.2
20060507
20
20060508
24
20060509
27
18.1
20060510
17
20060511
18.5
0.87
20060512
11
17.7
20060513
21
17.5
20060514
95
17.4
20060515
60
18
20060516
13
20060517
12
18.2
20060518
17.9
20060519
15
17.6
1.27
20060520
20060521
20060522
1.37
20060523
8
1.51
20060524
16.8
20060525
1.62
20060526
17.1
20060527
20.8
20060528
20060529
<
20.5
1.7
20060530
20.4
20060531
20060601
1.71
20060602
1.74
16点投用氧化再生,碱液反抽提未投用
20060603
1.2
20060604
0.8
8:
00停制氧机
20060605
103.59
138.59
22.7
/
因6月5日早班化验分析错误,10:
00补碱导致碱液过滤器频繁杜塞,在6月12日对滤芯进行清理后碱液循环恢复正常,总硫恢复正常
20060606
92.86
22.4
20060607
87.45
20.0
20060608
67.77
19.7
20060609
100.13
20060610
88.91
20060611
87.46
19.9
20060612
94.36
20060613
33.22
19.5
20060614
36.63
19.3
20060615
29.57
20060616
37.66
20060617
32.38
18.8
20060618
31.7
19.2
20060619
25.08
20060620
22.69
19.6
20060621
32.63
18.7
20060622
109.66
13.45
19.0
20060623
29.62
20060624
27.50
20060625
35.33
20060626
28.66
从表1可以看到,这段时间原料总硫不高,基本在150mg/m3以下。
在开工初期由于对装置操作条件处于摸索阶段,故总硫稍高于设计值,但在开工正常后,精制后液化气的总硫含量基本保持在5-20mg/m3之间。
但在6月5日由于化验分析错误,向脱硫系统补了10吨浓碱,因该碱较脏,遂导致碱液过滤器多次杜塞,影响到了液膜塔的脱硫效果,在6月12日,被迫对碱液过滤器采取清洗措施,再次投用后系统恢复正常,精制液化气的总硫含量维持在40mg/m3以下。
在开工后的生产过程中,整个系统的总碱浓度只达到了20%左右,没有达到25~30%设计指标,且一直没有开碱液反抽提设施,今后若将碱浓度提高到30%,将碱液反抽提设施投入使用,预计在原料总硫含量高于1000mg/m3时脱硫率将会有大幅度提高,可能达到95%以上。
(碱浓度越高,原料液化气总硫越高,脱硫率也越高)
在6月1日,碱液中的硫醇钠含量达到1.71%,为了检验富氧氧化再生工艺的效果,下午16:
00投氧化再生工艺,在6月4日早8:
00碱液中的硫醇钠含量下降到0.8%,遂停该富氧再生工艺。
从4月15日装置投用后至6月5日,共运行50天。
其中的硫平衡测算如下:
液化气平均处理量t/h
装置实际运行时间h
液化气总处理量t
碱液中总含硫kg
反推算到
液化气平均脱硫量g/t
相当于平均硫含量mg/m3
1200
14400
45*1000*1.8%
=810
56.3
128
备注:
系统中碱液总量为45吨,6月5日碱液中硫含量分析值为1.8%
从硫平衡分析数据可以看到,近2个月中,平均脱硫率可达到128mg/m3,产品总硫维持在10mg/m3以下。
而改造前精制产品总硫大多在100mg/m3上下,且碱渣排放量大,因此本次技术改造效果明显。
5.液化气铜片腐蚀情况
开工后,对精制后液化气在液膜塔后进行了采样分析,铜片腐蚀均为1级。
而改造前基本在2-4级,效果明显。
对液膜塔后的液化气的碱液夹带情况也进行了分析。
采用精度达0.02ml的李森科瓶挥发试验分析方法进行分析,未检出碱液。
(PH试纸试验值在7-8之间,基本为中性)。
表明液膜塔对碱液的分离效果很好,无须进一步的沉降和水洗。
6.碱液使用及排放情况
原工艺中,预碱洗和抽提脱硫醇碱液分别使用,预碱洗的碱液不再生,循环使用几次后即成为废碱液排放。
抽提脱硫醇碱液也是定期更换。
碱渣排放量大。
新工艺中,预碱洗和液膜脱硫醇均采用同一浓度的再生循环碱液(催化剂为W803高效脱硫催化剂(双核酞菁钴磺酸铵))。
碱渣排放量大大减少。
系统碱液储量达到45吨。
开工初期由于原料液化气中总硫浓度低,运行40天,因碱液系统中杂质多,更换过15吨碱液。
自2006-4-27日至2006-6-1,碱液总浓度维持在19%左右;
没有开碱液氧化再生,碱液中硫醇钠逐步累积到1.7%。
液化气脱硫正常,未更换过碱液。
到2006-6-2日,碱液常温富氧氧化再生开始投用。
投用前,制氧机经过单机现场验收合格后,先试运行2天,富氧浓度设定并稳定在45%;
进口非净化风压力0.65MPa,出口富氧空气压力0.55MPa,流量设定并稳定在5.1NM3,全自动正常运行。
投用前,富氧空气分布头以0.6MPa的小流量除盐水反冲洗,时间5分钟。
冲洗结束后,即关闭进水阀,开富氧空气进料阀。
投用初期的主要条件和结果如表2、表3:
表2:
碱液富氧常温氧化主要条件
非净化风进料量nm3/h
25
富氧浓度%
富氧进料量nm3/h
5.3
二硫化物分离罐
氮气进料量nm3/h
系统内碱液总量t
碱液总碱度%wt
19-20
碱液温度℃
25-30
氧化塔压力MPa
0.32
氧化塔体积m3
7.4
碱液循环速率t/h
表3:
碱液富氧常温氧化主要结果
采样时间
硫醇钠浓度%wt(以硫计算)
碱液脱硫时间h
上段时间区间
碱液脱硫量kg
碱液平均脱硫速率kg/h
上段时间区间氧化塔内
氧气平均利用率%
尾气中的氧浓度%v
尾气取样分析时间
氧气即时利用率%
★
尾气中的二硫化物浓度mg/m3
2006-06-02-16:
2006-06-03-09:
00
16.7
225
13.5
98
2.8
2006-06-03-08-50
82
不太臭
2006-06-03-15:
1.07
58.5
9.8
69
8.2
2006-06-03-14-50
46
2006-06-04-08:
17.8
121.5
6.8
10.8
2006-06-04-08-40
2006-06-05-08:
0.67
2.5
11.3
2006-06-05-07-50
★根据进气浓度和尾气浓度计算
用传统液化气碱液空气氧化再生工艺时,碱液需加热到55℃以上,氧气的利用率一般在15-20%(碱液中硫醇钠含量在2%以上时)。
尾气中夹带大量的二硫化物,一般在3%以上;
尾气中的氧含量达15%以上。
由于碱液中夹带的二硫化物也较多,因此需要频繁换碱,才能满足正常工艺生产的需要。
但从表3可以看到,即使在常温下,富氧对碱液中硫醇钠的再生效率也很高,碱液中硫醇钠含量在1.7%时氧气利用率可达到98%以上。
在设计量12NM3的氮气流量下,尾气中的氧含量只达到了2.8%。
尾气中夹带的二硫化物降到了约100mg/m3以下。
二硫化物分离罐尾气中二硫化物浓度很低,大大减轻了后续尾气处理装置的压力。
随着碱液中硫醇钠浓度的逐步降低,氧气利用率也逐步下降。
硫醇钠浓度在1.07%时,氧气的利用率仍达到46%。
当硫醇钠浓度下降到0.8%时,氧气的利用率持续下降到25%。
在这时候,降低富氧空气进料量将有利于提高氧气的利用率。
在用制氧机产生富氧时,对非净化风中的氧气提取率为46%。
液化气脱硫量与富氧空气进料量的关联,参见表4。
表4:
液化气脱流量与富氧空气进料量的关联
数值
液化气中的总S浓度mg/m3
100
300
500
700
1000
1390
液化气中的S浓度g/t
44
132
220
308
440
612
液化气流量t/hr
液化气中硫流量kg/hr
0.66
1.98
3.3
4.62
6.6
9.2
需要的对应氧气流量(理论值)Nm3/hr
0.17
0.50
0.83
1.16
1.65
2.29
需要的对应氧气流量(实际值)Nm3/hr
0.24
0.71
1.18
1.66
2.36
3.27
氧气利用率70%
纯度45%的富氧实际需要量Nm3/hr
0.37
1.10
1.83
2.57
3.67
5.10
开工初期
0.29
0.86
1.43
2.00
2.85
3.96
氧气利用率78%
二硫化物排放量kg/hr
1.45
4.36
7.26
10.16
14.52
20.18
从表4可以看到,即使在原料液化气中硫含量达到1390mg/m3处理量达到15t/h的工况下,目前45%浓度5.1NM3的富氧空气也足以再生所需要的碱液。
在液化气硫含量较低时,可以将富氧空气减少到1NM3以下,或者视脱硫效果间歇启用。
本次液化气脱硫醇部分扩能改造与改造前相比,废碱液的排放量大大减少,从源头上减少了对大气和水体的污染,为我公司的节水减排工作作出了贡献。
7.碱液常温富氧氧化再生系统的安全措施
本次技术改造由于时间仓促,在设计和改造过程中遇到以下几方面的问题:
1.过量氧气在二硫化物分离罐中的累积。
2.氧化塔内碱液因压差波动倒灌到气体分布头和制氧机富氧缓冲罐和空气过滤器。
3.制氧机非防爆型。
针对以上情况在施工过程中,对其设计进行变更(变更后流程如图三所示),主要采取措施如下:
1.在二硫化物分离罐中通入常量的稀释和保护用氮气,并设置与产生富氧的非净化风进料量之间的联锁自保。
一旦氮气意外降量或中断,则自动切断富氧进料。
2.在富氧进氧化塔前的管线上设置单向阀,可防止碱液倒流进制氧机附属设施;
另外针对碱液因压差波动倒灌进气体分布头,在管线上增加冲洗水设施,可在适当的工况下对气体分布头进行反冲洗。
3.采用防爆型制氧机,尤其是制氧机中的电器部分如电磁阀、控制柜、空气干燥机等。
均达到ExdⅡBT4以上的防爆等级(为赶施工进度,从不影响开工考虑,对制氧机安装了非净化风跨线)。
图三碱液富氧再生部分局部示意图
8.存在问题和改进方向
LPG液膜脱硫醇部分扩能改造完成后,随着催化装置的开工而全面投用,在投用初期主要遇到以下几方面的问题:
1.循环碱液系统中由于残留杂质较多,易堵塞碱液精细过滤器。
2.常温下酞菁钴催化剂的溶解较慢,未溶解的催化剂也会堵塞碱液精细过滤器,导致操作工劳动强度增大。
3.由于二硫化物分离罐较大(40立方),目前产生的预计900公斤左右的二硫化物还未能通过集油槽排出罐外,有待进一步积累。
针对以上问题,车间拟采取以下改进措施:
1.对原碱液储罐尤其是罐底采用高压水进行冲洗,清除罐底的杂质,并尽快安装碱液预过滤器。
2.酞菁钴催化剂需要预先在50-70℃的热水中进行溶解,然后再配成催化剂碱液(在现场可根据具体情况安装一化药槽即可进行配制)。
9.主要结论
1)采用液膜脱硫醇技术进行技术改造后,液化气的脱硫效率显著提高,产品铜片腐蚀监测结果全部合格。
2)液膜脱硫设备操作简单,可控性、稳定性好。
3)碱液富氧常温氧化再生工艺从使用情况来看效率高于常规工艺,且碱液利用率提高,碱渣排放明显减少。
4)整个工艺流程短,设备体积小,效率高。
在提高处理量的情况下,占地面积大大减小,节约投资费用。