基于PROE的注塑模具设计DOC.docx
《基于PROE的注塑模具设计DOC.docx》由会员分享,可在线阅读,更多相关《基于PROE的注塑模具设计DOC.docx(8页珍藏版)》请在冰豆网上搜索。
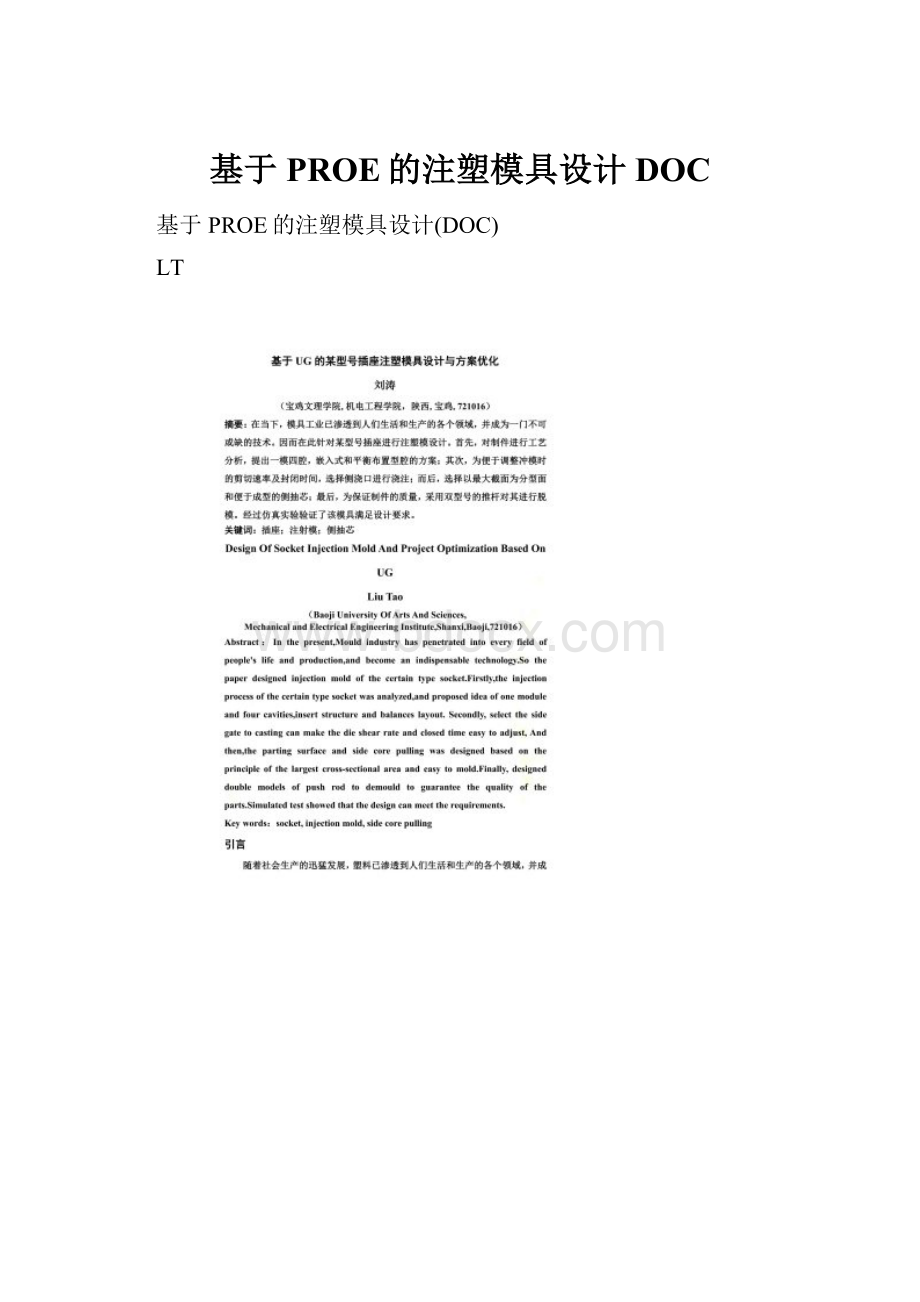
基于PROE的注塑模具设计DOC
基于PROE的注塑模具设计(DOC)
LT
图2插座底座三维模型
2模具结构设计
通过整体分析,该设计使用一模四腔的排列布置方式,排列方式为对称H形,通过对塑件的结构形状分析,采用推杆推出的推出形式。
浇注系统设计时,流道采用对称平衡式,浇口采用侧浇口,且开设在分型面上。
因此,定模部分不需要单独开设分型面取出凝料,动模部分需要添加型芯固定板、推板和推杆固定板,由上综合分析可确定选用由推杆推出的单分型面的注射模。
2.1分型面设计
分型面的设计是否合理直接影响模具结构的合理性、塑件的质量及加工的难以程度。
而分型面的选择首先要选在其最大截面处,其次要保证塑件留在动模一侧。
通过对塑件结构形式的分析以及分型面的选择原则,该制件的分型面位置如图3所示:
图3分型面的设计
2.2浇注系统设计
注射模具的浇注系统,是指从主流道的最前端一直到型腔之间的熔体流动的通道。
它的作用是为了使塑件的塑料熔体能够平稳的填充到模具的型腔之中,从而得到所需的塑件。
因此,合理的设计浇注系统对于整个注塑成型设计来说是至关重要的。
而浇注主要有主流道、分流道、浇口和冷料穴四部分。
1)主流道。
主流道是带有锥度的流动通道,大端与注射机喷嘴相连接,小端与分流道相连接。
本次设计主流道的大端直径为7mm,小端直径为4.5mm。
主流道部分设计成可拆卸的主流道衬套形式,可选用T8A单独加工和热处理。
2)浇口套。
浇口套一般为标准件可进行选购浇口套,和定位圈装配。
3)浇口的设计。
浇口是用于连接分流道和型腔的通道,其作用是使塑体熔体能够在较短的时间内充满型腔,并使浇口残余的熔体凝固从而封闭浇口,有效的抑制型腔内部发生熔体倒流现象。
而浇口又分为点浇口和侧浇口。
点浇口可使熔体具有较高的剪切速率和摩擦,有利于提高熔体的温度,对于熔体的流动有利。
但是采用点浇口时注射压力损失较大,大多采用三板模结构,且成型周期较长,废料较多。
而侧浇口的成型周期较短,易于去除浇注系统的凝料,可根据制件的结构灵活的调节浇口的位置。
且侧浇口尺寸调整方便,利于达到各型腔的浇口平衡,适用于一模多腔的模具,提高注射效率[1]。
本文针对该插座采用一模四腔,为便于调整冲模时的剪切速率及封闭时间,所以采用侧浇口浇注。
其长为2mm,宽度为3mm。
2.3侧抽心机构设计
侧抽芯机构是成型侧孔或侧凹的零件,一般做成可活动的结构。
在塑件脱模前,一般都需要侧向分型和抽芯才能取出塑件。
根据制件的结构分析,其侧壁只有一个半径为5mm半圆形小孔,且厚度为3mm,因而其抽芯力较小。
设计时采用斜滑块抽芯机构,结构简单,运动平稳、可靠。
其结构如下图4所示:
8—斜滑块,9—圆柱头内六角螺钉M6,10—滑块抽芯,11—圆柱头销钉M6,12—弹簧M6,13—滑槽,14—限位销M4,15—圆柱头内六角螺钉M10,16—肋板。
图4斜滑块抽芯机构
2.5脱模推出机构的设计
在注射完成后,为了使塑件能够顺利的从模具的型芯上分离,所以就必须设计推出塑件的机构,这种机构称为脱模机构(或称推出机构、顶出机构)。
脱模机构的作用包括塑件等的脱出、取出两个动作,即首先将塑件和浇注系统凝料等与模具松动分离,称为脱出,然后把其脱出物从模具内取出[1]。
根据对塑件的整体结构分析,由于该零件内部细小部件繁杂,所以为在脱模是保证塑件的表面质量,因此推杆应如下述设计。
1)针对单个塑件整体,采用直径为5mm的推杆,共计14根,呈对称形式均匀的布置在制件上。
2)针对单个塑件内的细小部件,采用直径为2.5的推杆,共计18根,呈对称形式均匀的布置在制件内部的加强筋处。
2.6冷却系统的设计
为减少在注射成型时,模具温度对塑件生产效率和成型质量的影响,所以分别在型腔和型芯上开设一条单回路冷却水道。
冷却介质为常温水,冷却时常为21s。
3模具总装图设计
该模具主要由浇注系统、成型零件(型腔、型芯)、脱模系统(推出和侧抽芯机构)、导向系统、冷却系统、固定和安装部分等,其装配图如图6所示。
a)
b)
c)
1—浇口套,2—定位圈,3、9—圆柱头内六角螺钉M6,4—定模座板,5—型腔固定板,6—圆柱头内六角螺钉M10,7—型腔,8—斜滑块,10—滑块抽芯,11—圆柱头销钉M6,12—弹簧M6,13—滑槽,14—限位销M4,15、19、25—圆柱头内六角螺钉M10,16—肋板,17—型芯,18—型芯固定板,20—推杆M2.5,21—拉料杆M6,22—推杆固定板,23—推板,24—动模座板,26—水嘴,27—密封圈,28、29—圆柱头内六角螺钉M16,30—圆柱头内六角螺钉M4,31—推杆M5,32—导柱,33—导套。
图5插座底座装配图
4工作过程
该模具的工作过程大体上可分为合模、注射、保压、冷却、开模、顶出6个循环过程,具体工作过程如下:
1)动、定模沿分型面合并构成型腔和浇注系统,而后熔融塑料进入模具型腔内经过保压、排气和冷却后动定模沿分型面分开;2)随着动模向下移动,斜滑块对塑件进行抽芯,同时弹簧受压收缩。
待达到最大开模行程后,侧抽芯从型腔内抽出;3)与此同时推板推动推杆,将塑件从型芯内推出;4)待塑件取出后,动模向上移动、两侧抽芯受弹簧压力向型腔内部移动,再次构成型腔和浇注系统从而进行下一次循环。
4结语
1)塑件工艺分析是模具设计的基础,也是整体设计的前提。
本文针对某型号插座进行工艺分析,提出一模四腔、嵌入式和平衡式布置的设计理念。
2)分型面选择的合理性决定塑件是否能够完美成型,综合分型面的选择各项原则,选择单分型面,并以其最大截面为分型面。
3)侧抽芯的合理选择关乎整个模具设计的合理性,由于本文所选制件侧凹较浅,所需抽芯距不大,综合考虑选用斜滑块侧向抽芯机构。
4)浇口设计是本次设计的重点,其合理性对于整个浇注过程影响较大。
本文对于浇口设计初选两套方案,综合考虑后选用侧浇口对其浇注成型。
5)推出机构对于整个模具的设计也是一大重点,其合理性决定塑件能否完好取出,因该塑件内部结构复杂,为保证其表面质量,采用双型号推杆的推出机构,经仿真实验,基本满足设计要求。
参考文献
[1].叶久新,王群.塑料成型工艺及模具设计[M].北京:
机械工业出版社,2007.
[2].刘朝福.塑料模具设计[M].北京:
清华大学出版社,2010.
[3].张国强.注塑模设计与生产应用[M].北京:
化学工业出版社,2010.
[4].许鹤峰,陈言秋.注塑模具设计要点与图例[M].北京:
化学工业出版社,1999.
[5].贾润礼,程志远.实用注塑模设计手册[M].北京:
中国轻工业出版社,2000.
[6].蒋继宏,王效岳.注塑模具典型结构100例[M].北京:
中国轻工业出版社,2000.
[7].陈万林.实用塑料注射模设计与制造[M].北京:
机械工业出版社,2000.