m3高炉炉型设计及物料平衡计算1Word文件下载.docx
《m3高炉炉型设计及物料平衡计算1Word文件下载.docx》由会员分享,可在线阅读,更多相关《m3高炉炉型设计及物料平衡计算1Word文件下载.docx(18页珍藏版)》请在冰豆网上搜索。
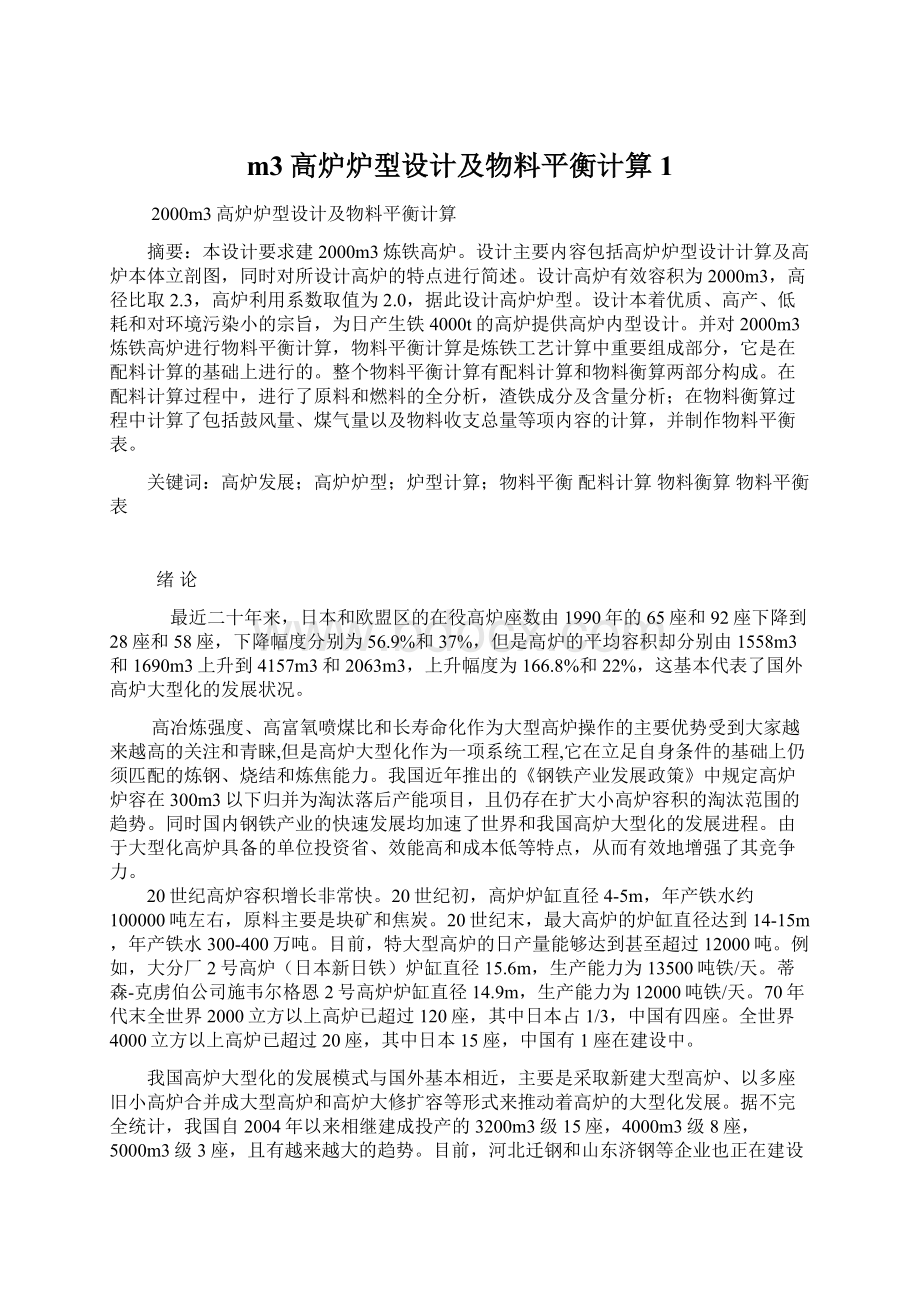
1.2五段式高炉
①高炉有效客积和有效高度高炉大钟下降位置的下沿到铁口中心线间的距离称为高炉有效高度,对于无钟炉顶为旋转溜槽最低位置的下缘到铁口中心线之间的趴离。
在有效高度范围内,炉型所包括的容积称为高炉有效容积。
高炉的有效高度,对高炉内煤气与炉料之间传热传质过程行很大影响。
在相同炉窖和冶炼强度条件下,增大有效高度,炉料与煤气流接触机会增多,有利于改善传热传质过程、降低燃料消耗;
仅过分增加有效高度,料校对煤气的阻力增大.容易形成料供,对炉科下降不利。
高炉有效高度应适应原燃料条件,如原燃料强度、粒度及均匀性等。
生产实践证明,高炉有效高度与有效容积有一定关系,但不是直线关系,当有效容积增加到—定值后,有效高度的增加则不显著。
②炉缸高炉炉型下部的圆筒部分为炉缸,炉缸的上、中、下部位分别没有风口、渣口与铁口,现代大型高炉多不设渣口。
炉缸下部容积盛装液态渣铁,上部空间为风口的燃烧带。
(1)炉缸直径炉缸直径过大和过小都直接影响高炉生产。
直径过大将导致炉腹角过大,边缘气流过分发展,中心气流不活跃而引起炉缸堆积,同时加速对炉衬的侵蚀;
炉缸直径过小限制焦炭的燃烧.影响产员的提高。
炉缸截面积应保证一定数量的焦炭和喷吹燃料的燃烧,炉缸截面燃烧强度是高炉冶炼的一个重要指标,它是指每1h每1m3炉缸截面积所烧侥的焦炭的数量,一般为1.00~1.25t/(m2·
h)。
炉缸截面燃烧强度的选择,应与风机能力和原燃料条件相适应,风机能力大、原料透气性好、燃料可燃性好的燃烧强度可选大些,否则选低值。
(2)炉缸高度炉缸高度的确定,包括渣口高度、风口高度以及风口安装尺寸的确定。
铁口位于炉缸下水平面,铁口数目根据高炉炉容或高炉产量而定,一般1000m3以下高炉设一个铁口,1500~3000m3高炉设2~3个铁口,3000m3以上高炉设3~4个铁口,或以每个铁口日出铁量1500—3000t设铁口数目。
原则上出铁口数目取上限,有利于强化高炉冶炼。
渣口中心线与铁口中心线间距离称为渣口高度,它取决于原料条件,即渣量的大小。
渣口过高,下渣量增加,对铁口的维护不利;
渣口过低,易出现渣中带铁事故,从而损坏渣口,大、中型高炉渣口高度多为1.5~1.7m。
(3)炉腹炉腹在炉缸上部,呈倒截圆锥形。
炉腹的形状适应了炉料熔化滴落后体积的收缩,稳定下料速度。
同时,可使高温煤气流离开炉墙,既不烧坏炉墙又有利于渣皮的稳定,对上部料柱而言,使燃烧带处于炉喉边缘的下方,有利于松动炉料,促进冶炼顺行。
燃烧带产生的煤气量为鼓风量的1.4倍左右,理论燃烧温度1800~2000℃,气体体积剧烈膨胀,炉腹的存在适应这一变化。
炉腹的结构尺寸是炉腹高度h2和炉腹角α。
炉腹过高,有可能炉料尚未熔融就进人收缩段,易造成难行和悬料;
炉腹过低则减弱炉腹的作用。
(4)炉身炉身呈正截圆锥形,其形状炉料受热后体积的膨胀和煤气流冷却后的收缩,有利于减少炉料下降的摩擦阻力,避免形成料拱。
炉身角对高炉煤气流的合理分布和炉料顺行影响较大。
炉身角小,有利于炉料下降,但易于发展边缘煤气流,过小时但只边缘煤气流过分发展。
炉身角大,有利于抑制边缘煤气流发展,但不利于炉料下行,对高炉顺行不利。
设计炉身角时要考虑原料条件,原料条件好时,可取大些,相反,则取小些。
高炉冶炼强度大,喷煤量大,炉身角取小值。
同时要适应高炉容积,一般大高炉由于径向尺寸大,径向膨胀量也大,就要求小些,中小型高炉大些。
(5)炉腰炉腹上部的圆柱形空间为炉腰,是高炉炉型中直径最大的部位。
炉腰处恰是冶炼的软熔带、透气性变差,炉腰的存在扩大了该部位的横向空间,改善了透气条件。
在炉型结构上,炉腰起着承上启下的作用,使炉腹向炉身的过渡变得平缓,减小死角。
炉腰直径与炉缸直径和炉腹角和炉腹高度几何相关,并决定了炉型的下部结构特点。
一般炉腰直径与炉缸直径有一定比例关系,大型高炉D/d取值1.09~1.15,中型高炉1.15~1.25,小型高炉1.25~1.5。
(6)炉喉炉喉吴圆柱形,它的作用是承接炉料,稳定料面,保证炉料合理分布。
炉喉直径与炉腰直径、炉身角、炉身高度几何相关,并决定了高炉炉型的上部结构特点。
第二章高炉炉型设计计算
根据任务要求,可得出以下条件:
Hu/D=2.5~3.1Vu=1500~3000m3设置2个铁口炉腹3.0~3.6m
炉腰直径D/炉缸直径d=1.09-1.15炉腹角取78o-83o
炉渣口高度1.5~1.7m炉腰直径高度1-3m
炉喉直径d1/炉腰直径D=0.64~0.73
本设计任务:
设计2000m3高炉一座
2.1定容积
选定高炉座数为1座,高炉利用系数为ηv=2.0t/(m3·
d),高炉容积Vu=2000m3
2.2确定年工作日和日产量
年工作日为355天,日产量P总=Vu·
ηv=4000t
2.3炉缸尺寸
1炉缸直径
它是决定焦炭燃烧量和出铁能力的重要参数,大型高炉一般采用经验公式:
炉缸直径
2)炉缸高度
要求能储存一次铁水量和下渣量,加上出铁量波动系数。
一般应使炉缸的容积占高炉有效容积的一个比例范围,现代大型高炉一般在17%~18%左右。
A.炉缸高度
B.风口高度
取
C.风口数量
2.4炉腰尺寸
(1)炉腰直径
决定于炉缸直径,炉腰高度和角度,炉腰直径稍大些好,它有利改善初成渣的透气性可D/d来确定,可经验公式
炉腰直径
(2)炉腰高度
在炉腹部位炉料下降缓慢,未还原的矿石在此经过充分还原后进入炉缸。
因此,炉腹的高度应与炉容相适应。
炉腹过高,可能是炉料还未熔化就过早的进入炉腹,容易导致悬料:
炉腹过低就无法发挥作用
炉腰高度
(3).炉喉尺寸
1)炉喉直径
2)炉喉高度
炉喉起到控制炉料和煤气流分布的作用。
炉喉过高时炉料挤紧,影响下降速度,过低不便使改变装料制度调节煤气流分布。
一般在1~3m
炉喉高度
(4).炉腹高度
在炉腹部位炉料下降缓慢,未还原的矿石在此经过充分还原后进入炉缸,所以在冶炼铸造生铁和使用难还原的矿石的时候,炉腰要高一些好。
炉腹高度
(5).炉身高度
主要炉料粒度和焦炭强度等对煤气流分布的影响,也要考虑和其他比为的相互关系
炉身高度
(6)有效高度
高炉有效高度直接影响到高炉的还原能力和热交换能力,并对料柱的透气性带来影响
有效高度
(7)死铁层高度
(8)日产量
(9)炉腹角、炉身角
A.炉腹角
B.炉身角
(10)校核炉容
炉缸体积
炉腹体积
炉腰体积
炉身体积
炉喉体积
高炉容积
相对误差
所以,设计合理。
具体设计参数见表2.1。
表2.1高炉内型参数
项目
参数
炉缸直径
10
炉缸高度
4.7
炉腰直径
11.3
1.8
炉喉直径
7.6
2.3
死铁层高度
1.874
炉腰角
83.0°
15
炉腹角
78.5°
3.2
风口数目
26
27
铁口数目
2
高径比
2.38
有效容积
2000
第三章物料平衡计算
整个物料平衡计算有配料计算和物料衡算两部分构成
3.1配料计算
由于物料平衡计算是在配料计算的基础上进行的,故欲进行物料平衡的计算,就得先进行配料计算。
而配料计算的基本原则是要满足质量守恒定律,即加入炉内的炉料中的各种元素和化合物的总和应等于高炉产品中各元素和化合物的总和。
为进行配料计算,需收集和整理一些资料。
包括:
1、需要原料和燃料的全分析数据,并折算成100%;
2、生铁品种及其成分;
3、确定矿石配比;
4、确定焦比;
5、各种元素在生铁、炉渣和煤气间的分配率;
6、炉渣成分,即选定合适的炉渣碱度。
3.1.1确定原始条件
原始条件包括
(1)原料的主要成分见表1。
表1原料主要成分(%)
成分
原料
TFe
FeO
CaO
SiO2
MgO
Al2O3
MnO
S
P
Fe2O3
烧损
烧结矿
53.46
9.69
11.86
8.61
2.02
1.70
0.62
0.023
0.041
球团矿
62.52
0.50
0.49
3.54
0.12
0.43
2.39
0.010
0.035
天然矿
59.40
7.13
1.91
7.12
0.52
1.18
1.05
0.210
混合矿
55.87
7.60
8.59
7.45
1.49
1.39
1.02
0.039
0.038
66.20
1.15
石灰石
0.63
0.814
54.02
1.38
0.37
0.27
0.01
0.004
45.43
(2)焦炭成分及焦炭灰分、挥发分和有机物见表2至表4
表2焦炭成分(%)
灰分
水分
挥发分
有机物
固定碳
13.50
4.00
0.9
0.7
84.0
(3)焦炭中的水分是在打水熄焦时渗入得,通常为2%~6%.
表3焦炭灰分(%)
P2O5
9.30
54.00
4.34
1.10
25.64
0.39
3.68
表4焦炭挥发分和有机物含量(%)
成分
CO2
CO
CH4
H2
N2
挥发物
0.34
0.02
0.05
0.15
0.3
0.1
(4)煤粉成分见表5
表5煤粉成分(%)
C
O2
H2O
灰分16.23
AL2O3
74.47
4.21
0.42
3.37
0.8
0.5
8.76
4.06
0.35
2.44
(5)炼钢生铁成分见表6
表6炼钢生铁成分(%)
Si
Mn
Fe
0.30
0.67
0.03
0.16
4.07
94.77
(6)配矿比:
烧结矿70%,球团矿20%,天然矿10%。
(7)元素分配率见表.7
表7各种元素的分配率(%)
生铁
99.5
50
100
3
炉渣
82
煤气
(8)炉渣碱度R=CaO/SiO2=1.04。
(9)焦比为450㎏/t,煤比为90㎏/t。
3.1.2计算
以1000Kg生铁作为计算单位,进行计算:
(1)根据铁平衡求矿石需求量:
焦炭带入的铁量:
450×
0.009=4.05㎏
煤粉带入的铁量:
90×
0.0244×
(56÷
72)=1.708㎏
进入炉渣的铁量:
947.7×
(0.005÷
0.995)=4.76Kg
需要混合矿量:
(947.7-4.05-1.708+4.76)÷
0.5587=1694.47Kg
(2)根据碱度平衡求石灰石用量:
混合矿带入的CaO量:
1694.47×
0.0859=145.55㎏
焦炭带入的CaO量:
0.1350×
0.0434=2.64㎏
煤粉带入的CaO量:
0.0062=0.57㎏
共带入的CaO量:
145.55+2.64+0.57=148.76㎏
混合矿带入的SiO2量:
0.0745=126.24㎏
焦炭带入的SiO2量:
0.5400=32.81㎏
煤粉带入的SiO2量:
90×
0.0876=7.88㎏
共带入的SiO2量:
126.24+32.81+7.88=166.93㎏
还原Si消耗的SiO2量:
3×
(60÷
28)=6.43㎏
石灰石用量:
[(166.93-6.43)×
1.04-148.76]/(0.5402-0.0138×
1.04)=34.53㎏
考虑到机械损失及水分,则每吨生铁的原料实际用量列于表8
表8每吨生铁的实际用量
名称
干料用量/㎏
机械损失/%
水分/%
实际用量/㎏
混合料
1694.47
1745.30
34.53
1
34.88
焦炭
450
4
477.00
合计
2179.36
2257.18
(3)终渣成分:
1)终渣S量:
炉料全部含S量:
0.00039+450×
0.005+90×
0.005+34.53×
0.0001=3.36Kg
进入生铁S量:
0.3Kg
进入煤气S量:
3.36×
0.15=0.504Kg
进入炉渣S量:
3.36-0.3-0.504=2.556Kg
由于分析得到的二价钙离子都折算成CaO,而其中一部分钙离子以CaS形
式存在,CaS与CaO之重量差为S/2,为了重量平衡钙离子仍以CaO存在计算,而S则只算S/2。
2)终渣FeO量:
4.76×
(72/56)=6.12Kg
3)终渣MnO量:
0.0102×
0.5=8.64Kg
4)终渣SiO2量:
166.93-6.43=160.50Kg
5)终渣CaO量:
148.76+34.53×
0.5402=167.41Kg
6)终渣Al2O3量:
0.0139+450×
0.135×
0.2564+90×
0.0406+34.53×
0.0027=44.88Kg
7)终渣MgO量:
0.0149+450×
0.0111+90×
0.0035+34.53×
0.0037=26.38Kg
终渣成分见表9。
表9终渣成分
成分
S/2
∑
R
㎏
160.50
44.88
167.41
26.38
8.64
6.12
1.278
415.21
%
38.66
10.81
40.32
6.35
2.08
1.47
0.31
1.04
(4)生铁成分校核:
1)生铁含量:
0.00038+450×
0.0368×
62/142+34.53×
0.00004=1.62Kg
1.62/1000=0.16%
2)生铁含S量:
0.03%
3)生铁含Si量:
0.3%
4)生铁含Mn量:
8.64×
0.5/0.5×
55/71×
100/1000=0.67%
5)生铁含Fe量:
94.77%
6)生铁含C量:
100%-0.03%-0.3%-94.77%-0.67%-0.16%=4.07%
最终生铁成分列于表10
表10最终生铁成分(%)
100.00
校验结果与原设生铁成分相符合。
3.2.物料平衡
高炉物料衡算分两种情况,一是生产高炉的,另一种是设计高炉的,它们计算的内容、方法和程序有所不同。
但计算原理是一样的。
本课题做的是炼铁设计时的物料衡算方法。
是在前面配料计算的基础上进行的。
3.2.1原始条件的确定
原始条件为:
[7]
(1)选择确定直接还原度:
可根据煤气成分来计算,但较复杂,故这里直接选定直接还原度rd=0.45。
(2)鼓风湿度f:
这里取大自然湿度为0.012Kg/
f=1.5%。
(3)假定入炉碳量0.5%的碳与H2反应生成CH4(纯焦冶炼可取0.5%~1.0%,喷吹燃料时可取1.2%)。
3.2.2物料衡算
物料平衡计算步骤为:
(1)风口前燃烧的碳量:
焦炭带入固定碳量:
0.84=378.00Kg
煤粉带入固定碳量:
0.7447=67.02Kg
共计燃烧碳量:
378.00+67.02=445.02Kg
生成CH4的碳量:
445.02×
0.012=5.34Kg
熔于生铁的碳量:
0.0407×
1000=40.70Kg
还原Mn消耗的碳量:
0.0067×
1000×
12/55=1.46Kg
还原Si消耗的碳量:
0.003×
24/28=2.57Kg
还原P消耗的碳量:
0.0016×
60/62=1.55Kg
还原Fe消耗的碳量:
0.9477×
0.45×
12/56=91.39Kg
直接还原消耗的碳量:
1.46+2.57+1.55+91.39=96.97Kg
风口前燃烧碳量:
C风=445.02–5.34-40.07–96.97=302.64Kg
C风占入炉总碳量的百分数:
302.64/445.02×
100%=68.01%
(2)根据碳平衡计算风量:
鼓风中氧的浓度:
0.21×
0.985+0.5×
0.015=0.2144
/
风口前燃烧碳素需要氧量:
(302.64×
22.4)/(2×
12)=282.46
煤粉可供给:
(0.0337/32+0.008/36)×
22.4=2.57
则每吨生铁鼓风量:
V风=(282.46-2.57)/0.2144=1305.46
(3)计算煤气各组分的体积和成分:
1)CH4的