模具设计与制造冲压模课程设计.docx
《模具设计与制造冲压模课程设计.docx》由会员分享,可在线阅读,更多相关《模具设计与制造冲压模课程设计.docx(14页珍藏版)》请在冰豆网上搜索。
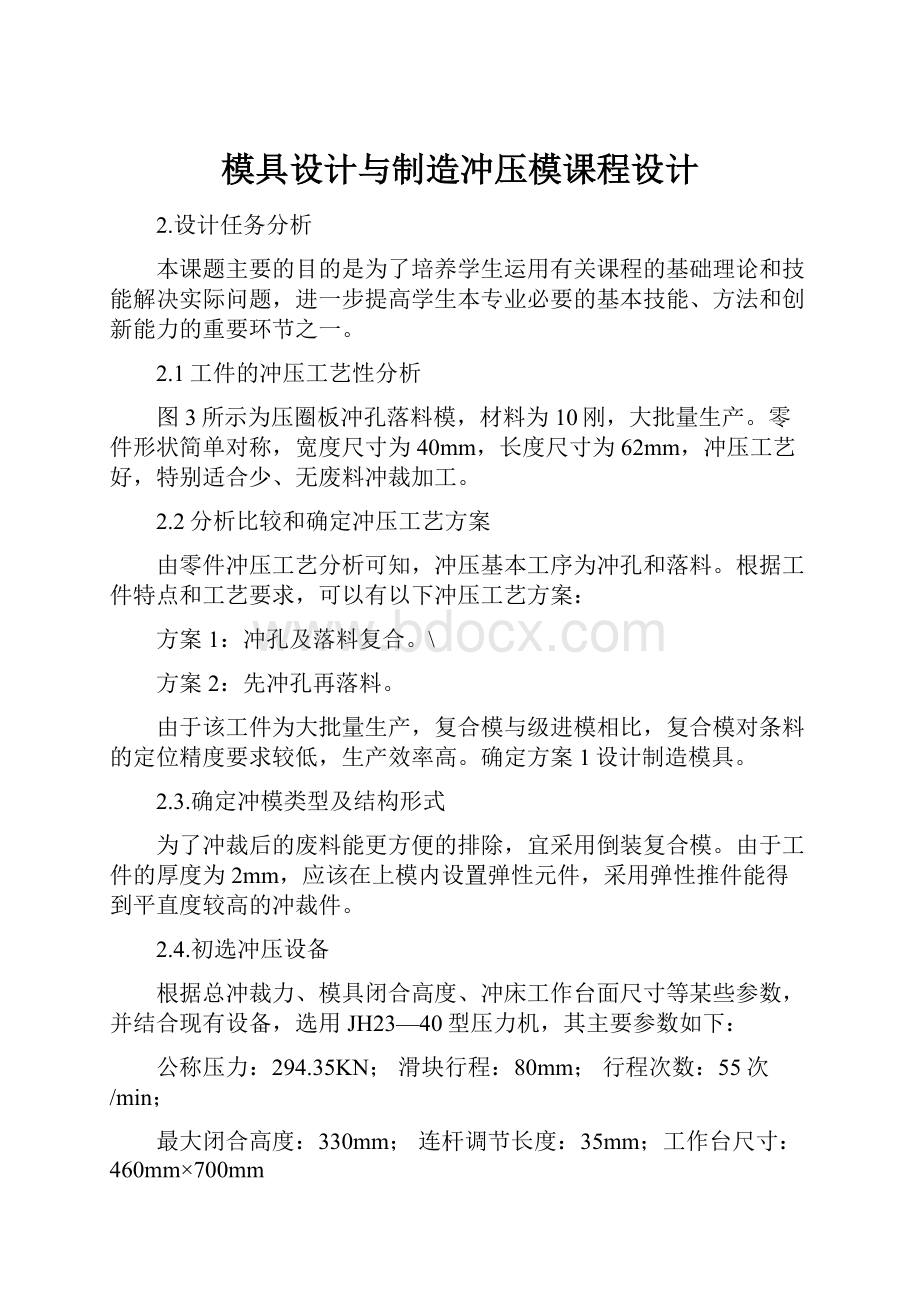
模具设计与制造冲压模课程设计
2.设计任务分析
本课题主要的目的是为了培养学生运用有关课程的基础理论和技能解决实际问题,进一步提高学生本专业必要的基本技能、方法和创新能力的重要环节之一。
2.1工件的冲压工艺性分析
图3所示为压圈板冲孔落料模,材料为10刚,大批量生产。
零件形状简单对称,宽度尺寸为40mm,长度尺寸为62mm,冲压工艺好,特别适合少、无废料冲裁加工。
2.2分析比较和确定冲压工艺方案
由零件冲压工艺分析可知,冲压基本工序为冲孔和落料。
根据工件特点和工艺要求,可以有以下冲压工艺方案:
方案1:
冲孔及落料复合。
\
方案2:
先冲孔再落料。
由于该工件为大批量生产,复合模与级进模相比,复合模对条料的定位精度要求较低,生产效率高。
确定方案1设计制造模具。
2.3.确定冲模类型及结构形式
为了冲裁后的废料能更方便的排除,宜采用倒装复合模。
由于工件的厚度为2mm,应该在上模内设置弹性元件,采用弹性推件能得到平直度较高的冲裁件。
2.4.初选冲压设备
根据总冲裁力、模具闭合高度、冲床工作台面尺寸等某些参数,并结合现有设备,选用JH23—40型压力机,其主要参数如下:
公称压力:
294.35KN;滑块行程:
80mm;行程次数:
55次/min;
最大闭合高度:
330mm;连杆调节长度:
35mm;工作台尺寸:
460mm×700mm
3.冲压工艺计算
3.1.排样、计算条料宽度和搭边值,画排样图
经表3-15得a=2.5mm,a1=2mm由表3-16得△=0.6mm
故条料宽度为B=(D+2a+△)0-△=(40+2×2.5+0.6)0-0.6=45.60-0.6mm
冲裁步距为S=40+2=42mm排样图见上图:
3.2.计算冲压力
根据公式,冲裁力
错误!
未找到引用源。
式中,L—冲裁长度(㎜);
错误!
未找到引用源。
—冲件材料抗拉强度,取370MPa;
t—冲件材料厚度(㎜)。
F=(32.656+78.48+43.96+78.5+50.24)×2×370≈210KN
查表,得卸料力系数Kx=0.045;冲孔的推件力系数Kt=0.055
则总冲裁力F总=F+F×0.045+F×0.055≈294.35KN
由于是IT14,精度要求不高,所以选用开式压力机。
查表知:
选用开式压力机JH23-40。
3.3.确定压力中心
由于冲裁件的形状对称,其压力中心与模具几何中心重合,所以理论压力中心与实际压力中心重合取凸凹模几何中心为压力中心。
如图所示:
压力中心的坐标:
(21,0)
4.冲压模具工作零件设计计算
4.1.冲裁刃口尺寸及公差计算
零件形状比较简单,冲裁模的凸模及凹模的加工在拥有普通线切割机床、平面磨床等一般模具加工设备的前提下,可考虑在热处理后,按图纸分开加工制造。
(配作法)由于工件的公差为IT14,故X=0.5,由表得△=0.6mm
A类(尺寸增大):
R80-0.36
400-062620-0.74
A1凹=(amax—x△)+△/40=(8-0.5×0.36)+0.090=7.82+0.090mm
A2凹=(amax—x△)+△/40=(40-0.5×0.62)+0.1550=39.69+0.1550mm
A3凹=(amax—x△)+△/40=(62-0.5×0.74)+0.1850=61.63+0.1850
B类(尺寸减小)2-
8+0.360mm
25+0.520
B1凸=(bmin+x△)0-△/4=(8+0.5×0.36)0-0.09=8.180-0.09mm
B2凸=(bmin+x△)0-△/4=(25+0.5×0.52)0-0.13=25.260-0.13mm
C类(尺寸不变)45
0.3119.62
0.26
C1凹=(Cmin+△/2)+-△/8=(45-0.31+0.31)
0.0775=45
0.0775mm
C2凹=(Cmin+△/2)+-△/8=(19.62-0.26+0.26)
0.07=19.62
0.07
凸模尺寸按实际尺寸配置,保证正常边间隙Zmin/2.
4.2.工作零件结构设计尺寸计算
(1)、垫板:
首先以承压面较小的凸模进行承压应力计算,以判断是否采用垫板。
其承压应力为:
σ=冲裁力/凸模承压面面积=210000/1071=196MPa
垫板的长宽高L×B×H=120mm×62mm×40mm。
(2)、卸料板:
本模具采用弹性卸料,考虑到卸料力较大,卸料板外形尺寸亦较大,故厚度取15mm,材料为10钢,硬度为38~42HRC。
(3)、卸料橡皮的安装高度:
经计算(计算过程略),冲裁2mm厚的零件,橡皮的安装高度为20mm。
(4)、凸模固定板:
凸模固定板厚度H固,H固=0.7H=0.7x20=14mm,确定取20mm。
凸模固定板上型孔尺寸均按凸模实际尺寸配作(M7/h6),孔距尺寸与凹模保持一致。
4.3.1.凹模外形结构、尺寸计算
(1)、凹模的外形结构与固定方法
凹模的结构形式也较多,按外形可分为标准圆凹模和板状凹模;按结构分为整体式和镶拼式;按刃口形式也有平刃和斜刃。
下图为冲裁圆凹模及固定方法:
由于工件的冲孔,其上冲裁圆凹模主要用于冲裁(孔径d=1~28mm,料后<2mm),可根据使用要求及凹模的刃口尺寸从相应的标准中选取。
(2)、凹模外形尺寸:
凹模厚度H=K×b(≥15mm)
式中,b——凹模刃口尺寸(mm),考虑冲件外形,取封闭孔口的最大尺寸,b=40mm;
K——考虑板厚影响所取的系数,查得K=0.42
计算得,H=0.42×40=16.8mm,确定取H=20mm;
凹模壁厚C=(1.5~2)×H=(>30mm)
取系数2计算,得C=2×16.8=33.6mm,确定取C=40mm;
根据排样图即可得到凹模外形尺寸
L×B×H(长×宽×高)=(40+2×40)×(62+2×40)×40=120×142×40
取整数,确定凹模外形尺寸为L×B×H=120mm×62mm×40mm。
4.3.2.凸模外形结构、尺寸计算
(1)、凸模外形结构
按照B型圆凸模的结构形式来设计凸模,因为B型圆凸模直径范围d=3.0~30.2mm,然而工件需要冲裁的孔d=25mm和8mm。
其结构如下图:
(2)、凸模尺寸计算
(3)凸模的尺寸:
长、宽与凹模一样、高为30mm。
5.选择标准模架型号和标准紧固件、定位件、导向件、弹性件的
5.1.选择标准模架的型号
模架由上下模座、模柄以及导向装置组成。
模架产品标准有GB/T2851.1、GB/T2851.3~7、GB/T2852.1~4,共十个。
在这里我选用四导柱模架,4个导柱分布在矩形凹模的两对角上,其导向精度与刚度好。
其结构如下图:
(L×B≤200×160)
5.2.选择标准紧固件的规格与尺寸
(1)、模柄
凸缘模柄在于凸缘以下部分可加工出容纳推板的形孔,此外拆装比较方便,该模柄
结构形式和尺寸规格如上页:
(2)、螺钉及圆柱销
内六角螺钉的尺寸规格见下左图;圆柱销的尺寸规格见下右图:
5.3.选择定位件、导向件的规格与尺寸
(1)、冲模定位零部件的规格与尺寸
活动挡料销:
它多在倒装模的弹性挡料装置中使用,结构形式和尺寸规格见下表:
2)、导向件的规格与尺寸
A、导柱如下图
3)B、导套如上图
5.4.选择弹性件的结构、规格与尺寸
圆柱螺旋压缩弹簧的结构、规格与尺寸见下图:
6.校核冲压设备的基本参数
6.1.模具闭合高度校核
冲模的闭合高度是指滑块在下死点即模具在最低工作位置时,上模座上平面与下平面之间的距离H。
冲模的闭合高度必须与压力机的装模高度相适应。
冲模的闭合高度应介于压力机的最大装模高度Hmax与最小装模高度Hmin之间。
Hmax-5mm≥H≥Hmin+10mm
6.2.冲裁总压力
校核其总压力为F冲=294.35<400KN 符合要求
如果冲模的闭合高度大于压力机最大装模高度,冲模不能在该压力机上使用。
反之,小于压力机最小装模高度时,可加经过磨平的垫板。
冲模的外形结构尺寸也必须和压力机相适应,如模具外形轮廓平面尺寸与压力机垫
板、滑块底面尺寸,模柄与模柄孔尺寸,下模缓冲器平面尺寸与压力机垫板孔尺寸等都必须适应,以便模具正确安装和正常使用。
6.3.模具最大安装尺寸校核
模座的底面尺寸是200×160mm,压力机的工作台尺寸是460×700mm,模座的尺寸小于压力机的尺寸,并且其闭合高度也合格,所以最大安装尺寸是合理的。
7.凸凹模加工工艺过程卡
落料凹模加工工艺过程
落料凹模加工工艺过程
材料:
T10A硬度:
56~60HRC
序号
工序名称
工序内容
1
备料
锻件(退火状态):
175×130×50mm
2
粗洗
洗六面到尺寸167×128×42mm,注意两大平面与相邻侧面用标准角尺测量达到基本垂直
3
平面磨
磨光两大平面厚度达到41mm,并两相邻侧面达到四面垂直,垂直度0.02mm
4
钳
划线画出各孔径中心线并画出凹模洞口轮廓尺寸
钻孔钻螺纹底孔、销钉底孔和凹模洞口穿线孔
绞孔绞销孔到要求
攻丝攻螺纹到要求
5
热处理
淬火使硬度达到56~60HRC
6
磨平面
磨光两大平面,使厚度达到40mm
7
线切割
割凹模洞口,并留有0.01~0.02的研磨量
8
钳
研磨洞口内壁侧面达到0.08um
9
钳
用垫片层保证凹模与凸凹模间隙均匀后,凹模与上模座配做销钉孔
10
平磨
研磨凹模板上面达到厚度尺寸要求
冲孔凸模加工工艺过程
冲孔凸模加工工艺过程
材料:
T10A硬度:
56~60HRC:
序号
工序名称
工序内容
1
备料
锻件(退火状态)
2
热处理
退火硬度达到180~220HB
3
车
车一端面,打顶尖孔,掉头车另一端,长度至尺寸86mm;打顶尖孔
双顶尖顶,车外圆尺寸到要求
4
检验
检验
5
热处理
淬火硬度至HRC56~60
6
磨削
磨削外圆尺寸达到要求
7
线切割
切除工件端面顶尖,长度尺寸至84mm
8
磨削
磨削端面尺寸到表面粗糙的要求
9
检验
检验
10
钳
装配(钳修并装配、检修)
8.冲压模具装配工序卡
冲压模具装配工序卡
工号
工序
工艺说明
1
凸、凹模的预配
1、装配前仔细检查各凸模、凹模的形状及尺寸,是否符合图纸要求和尺寸精度,形状;
2、将凸模分别于相应的凹模孔配合,检查间隙是否加工均匀,不合适者应重新修磨或更换。
2
凸模装配
以凹模孔定位,将各凸模分别压入凸模固定板的孔中,并挤紧牢固。
3
装配下模
1、在下模座1上画中心线,按中心线装配下垫板凸凹模和卸料板;
2、在下模座、卸料板上,用机加工好的凹模分别确定其螺孔位置,并分别钻孔,攻丝;
3、将下模、卸料板、下垫板、凸凹模、活动当料销,弹簧装在一起,打入销钉,用螺钉钉紧。
4
装配上模
1、在已装好的下模上放等高垫铁,并在凹模中放入0.12的纸片,装上落料凹模,空心垫板,然后将凸模与固定板组合并转入凹模中;
2、预装上模,画出与凸模固定板相应的螺孔、销孔位置并钻绞螺孔销孔;
3、用螺钉将固定板组合、垫板、上模座连接在一起,但不要拧紧;
4、复查凸、凹模间隙并调整合适,紧固螺钉;
5、切纸检查,合适打入销钉,宁静螺钉。
5
试冲与调整
装机试冲并根据试冲结果作相应调整。
装配图
凹模
凸模
11.参考资料
11.1.《实用五金手册》;
11.2.《冲压手册》——机械工业出版社2004年4月版
11.3.《模具课程设计指导》——机械工业出版社2007年2月版
11.4.《冲模结构图册》——机械工业出版社2006年8月版
11.5.《最新冲压新工艺新技术及模具设计实用手册》——2004年11月版