无凸缘筒形件模具设计Word下载.docx
《无凸缘筒形件模具设计Word下载.docx》由会员分享,可在线阅读,更多相关《无凸缘筒形件模具设计Word下载.docx(36页珍藏版)》请在冰豆网上搜索。
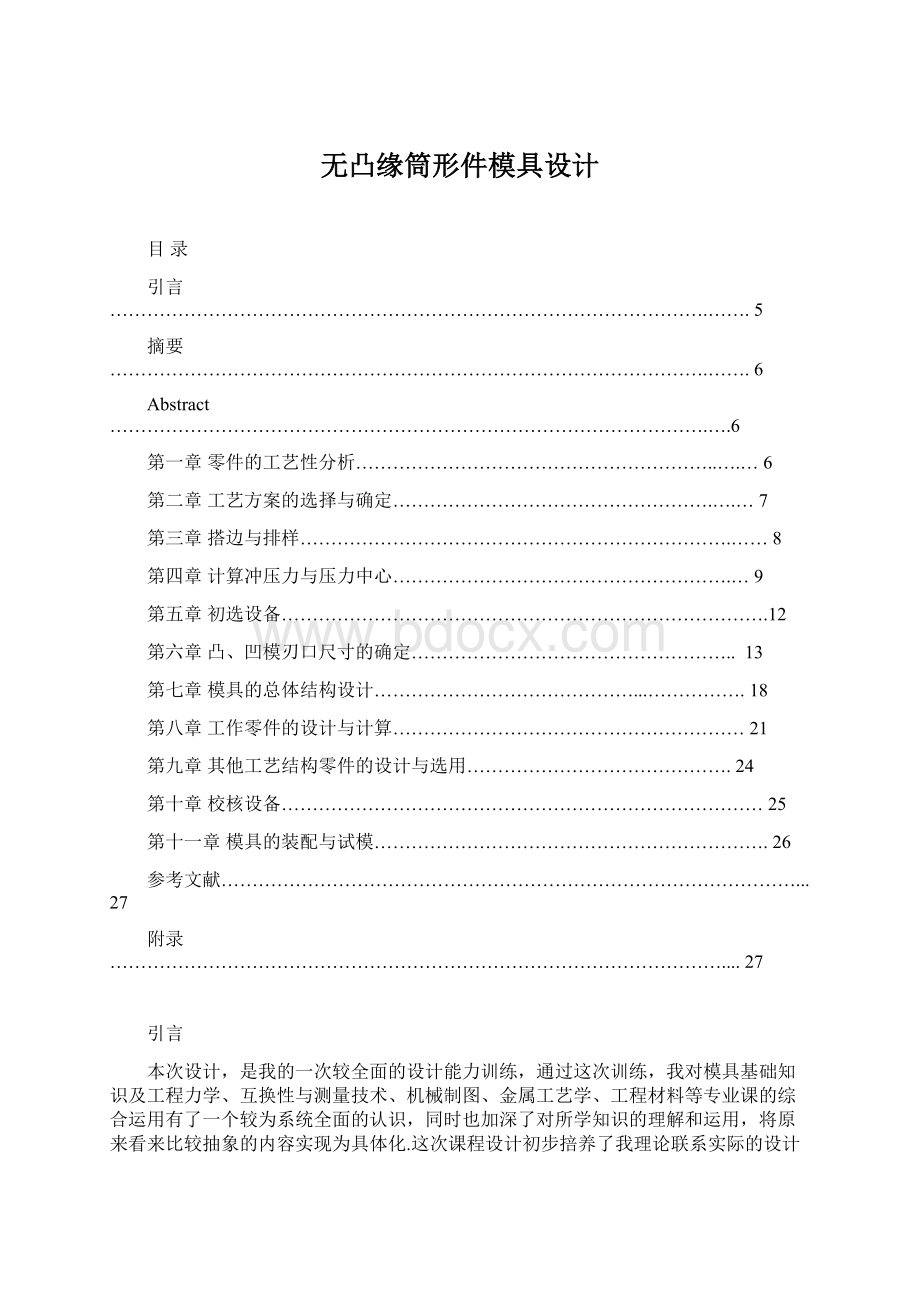
铜黄铜
d≥1.5t
d≥1.3t
d≥t
d≥0.9t
d≥1.2t
d≥0.8t
d≥0.7t
d≥1.35t
d≥1.1t
d≥0.6t
零件冲裁孔与边缘的间距d=21-(29\2)=6.5mm,d>
t满足设计要求。
(2)冲裁精度
2.6.7冲裁断面的表面粗糙度表 2.6.8冲裁件允许毛刺的高度
通过查上表2.6.7的冲裁断面的表面粗糙度表Ra=12.5;
查表2.6.8冲裁件允许毛刺的高度:
新建试模时≤0.05mm,生产时≤0.15mm。
d为孔直径
t为材料厚度
第2章工艺方案的选择与确定
(1)根据冲裁件的形状,分为冲孔和落料两道工序,且为大批量生产,故选择复合模。
(2)提出可能方案
冲裁该零件,所需工序有:
(a)落料
(b)冲直径29mm的孔
根据以上工序,可以有如下方案
方案一:
先落料
再冲直径29mm的孔;
方案二:
在同一模具上同时完成冲直径29mm的孔和落料
比较以上两种方案,第二种方案易实现自动化生产,且生产率高操作安全,适合大批量生产,所以选方案二。
(3)冲模的生产过程简图如图1-2
图1-2
第三章搭边与排样
(1)确定合理的排样形式
根据材料的经济应用原则,材料利用率η=F/F0×
100%=F/AB×
100%,利用率越过越经济,同时还要考虑冲裁件的精度要求,精度要求高的要留搭边。
搭边a和a1的数值查表1-4
表1-4搭边a和a1数值(低碳钢)
注:
对于其他材料,应将表中数值乘以下系数:
中等硬度钢0.9,硬钢0.8硬黄铜1~1.1,硬铝1~1.2
故有:
a=2.5(mm)a1=2.2(mm)
(2)确定条料宽度和步距
每次只冲一个零件的步距A的计算式为:
A=D1+2a1=(51+21)+2*2.2=74.2(mm)
条料宽度:
B=(D+2a)=(18+55)+2*2.5=78(mm)
(3)计算利用率
选择的排样方式如图1-3所示:
η——材料利用率;
F——工件的实际面积;
F0——所用材料面积,包括工件面积与废料面积;
A——送料进距(相邻两个制件对应点的距离);
B——条料宽度。
D1—平行于送料方向的宽带
D—垂直于平行于送料方向的宽带
图1-3
工件的实际面积:
F=52×
55+3.14*9*9-2*(4*30)-3.14*4*4/2+0.5*3.14*21*21-3.14*(29×
29)/4=3361.40
F0=A*B=74.2×
78=5787.6
材料利用率:
η=F/F0×
100%=58.08%
第四章计算冲压力与压力中心
(1)冲裁力的计算
普通平刃冲裁模,其冲裁力P一般可按下式计算:
FP=tLτ
材料抗剪强度:
τ=(1.2×
t/d+0.6)*σb
≈150(MPa)
冲孔边缘:
L1=29×
3.14=91.06(mm)
落料边缘:
L2=21×
3.14+2*(30+2*3.14+9*3.14+55)=3.5.02(mm)
冲孔力:
F1=L1τt=91.06×
150×
3=40977N
落料力:
F2=L2τt=305.02×
3=137259N
冲裁力:
F0=F1+F2=178236N
考虑到模具刃口的磨损和凸凹模间隙的波动,材料的机械性能的变化,材料厚度偏差的,实际所需的冲裁力还要增加30%,即:
F=1.3×
F0=231706.8N
τ——材料抗剪强度,见附表(MPa);
L——冲裁周边总长(mm);
t——材料厚度(mm)
σb—抗拉强度为235(MPa)
d---材料最大宽度
当上模完成一次冲裁后,冲入凹模内的制件或废料因弹性扩张而梗塞在凹模内,模面上的材料因弹性收缩而紧箍在凸模上。
为了使冲裁工作继续进行,必须将箍在凸模上的材料料刮下,将梗塞在凹模内的制件或废料向下推出或向上顶出。
从凸模上刮下材料所需的力,称为卸料力;
从凹模内向下推出制件或废料所需的力,称为推料力;
从凹模内向上顶出制件需的力,称为顶件力(图1-5)。
影响卸料力、推料力和顶件力的因素很多,要精确地计算是困难的。
在实际生产中常采用经验公式计算:
卸料力FQ=KFP=
推料力FQ1=nK1FP
顶件力FQ2=K2FP
图1-4工艺力示意图
由下表1-5查的K=0.045K1=0.05K2=0.04
厚度/(mm)
K
K1
K2
钢
≤0.1
0.1~0.5
0.5~2.5
2.5~6.5
6.5
0.1
0.063
0.055
0.045
0.025
0.14
0.08
0.06
0.05
0.03
0.065~0.075
0.045~0.055
0.04~0.05
0.03~0.04
0.02~0.03
解得:
FQ=0.045×
178436.7=8029.65N
FQ1=0.05×
178436.7=8921.84N
FQ2=0.04×
178436.7=7137.47N
(2)冲裁中心
冲模的压力中心,可按下述原则来确定:
(a)对称形状的单个冲裁件,冲模的压力中心就是冲裁件的几何中心。
(b)工件形状相同且分布位置对称时,冲模的压力中心与零件的对称中心相重合。
(c)形状复杂的零件、多凸模的压力中心可用解析计算法求出冲模压力中心。
解析法的计算依据是:
各分力对某坐标轴的力矩之代数和等于诸力的合力对该坐标轴力矩。
求出合力作用点的座标位置O0(x0,y0),即为所求模具的压力中心如图1-5
图1-5
其中:
X0=(X1+X2+X3+X4+X5)/5=66.2
Y0=(Y1+Y2+Y3+Y4+Y5)/5=51.4
P——冲裁力(N);
K——卸料力系数,其值为0.02~0.06(薄料取大值,厚料取小值);
K1——推料力系数,其值为0.03~0.07(薄料取大值,厚料取小值);
K2——顶件力系数,其值为0.04~0.08(薄料取大值,厚料取小值);
n——梗塞在凹模内的制件或废料数量(n=h/t);
h——直刃口部分的高(mm);
t——材料厚度(mm)。
第五章初选设备
(1)计算压力机的表承压力
冲裁时,压力机的公称压力必须大于或等于冲裁各工艺力的总和。
采用弹压卸料装置和上出件的模具时:
FP总=FP+FQ+FQ2
=178436.7+8029.65+7137.47
=246873.92N≈247KN
根据标称压力等参数查表1-7,可初选压力机为:
JH23-25
压力机型号
J23-3.15
J23-6.3
J23-10
J23-16F
JH23-40
标称压力/KN
31.5
63
100
160
250
400
滑块行程/mm
25
35
45
70
75
80
滑块行程
200
170
145
120
55
最大封闭高度
150
180
205
260
330
封闭高度调节量
65
立柱间距/mm
220
270
340
喉深/mm
90
110
130
工作台前后尺寸/mm
240
300
370
460
工作台左右尺寸/mm
310
450
560
700
垫板厚度/mm
30
40
50
垫板孔径/mm
140
210
320
模柄孔直径/mm
模柄孔深度/mm
60
最大倾斜角
电动机功率/kw
0.55
0.75
1.1
1.5
2.2
5.5
表1-7
第六章凸、凹模刃口尺寸的确定
已知冲裁件材料为Q235A钢厚度t=3mm,冲裁件精度IT12,查公差表1-8
公差表1-8
查的各尺寸如下图1-6所示:
FP总-冲裁各工艺力的总和
dd—冲孔凹模基本尺寸(mm);
dp—冲孔凸模基本尺寸(mm);
dmin—冲孔件孔的最小极限尺寸(mm);
△—制件公差(mm);
x—系数
冲裁模刃口尺寸计算的基本原则:
落料件尺寸由凹模尺寸决定,冲孔时孔的尺寸由凸模尺寸决定。
故设计落料模时,以凹模为基准,间隙取在凸模上;
设计冲孔模时,以凸模为基准,间隙取在凹模上。
冲裁件内圆孔由冲孔制成,外形为非圆形落料而成,
(a)冲孔
凸模制造偏差取负偏差,凹模取正偏差。
其计算公式如下:
dp=(dmin+x△)-δp
dd=(dp+Zmin)+δp
通过查下冲裁件处始双面间隙表1-9,
表1-9冲裁件处始双面间隙
材料厚度mm
软铝
含碳(0.08~0.2)%的钢
Zmin
Zmax
1
0.04
0.07
1.2
0.084
0.072
0.096
0.108
0.075
0.105
0.09
0.12
0.135
1.8
0.126
0.144
0.162
2
0.1
0.16
0.18
0.13
0.176
0.154
0.198
0.22
2.5
0.15
0.2
0.175
0.225
0.25
2.8
0.168
0.224
0.196
0.252
0.28
3
0.24
0.21
0.27
0.3
3.5
0.245
0.315
0.35
0.385
4
0.36
0.32
0.4
0.44
4.5
0.405
0.45
0.49
δp—凸模下偏差,
δd—凹模上偏差
得到:
Zmax=0.27mmZmin=0.21mm
Zmax-Zmin=0.06mm
冲孔部分冲裁凸模,凹模的制作公差,可查表1-10
表1—10
基本尺寸、mm
凸模偏差δp/mm
凹模偏差δd/mm
≤18
0.02
>
180~260
>18~30
260~360
0.035
30~80
360~500
80~120
500
120~180
查的:
δp=0.02mmδd=0.025mm
有:
δp+δd=0.045mm<Zmax-Zmin
x—系数,是为了使冲裁件的实际尺寸尽量接近冲裁件公差带的中间尺寸,与工件制造精度有关,按下列关系取值,也可查表1-11:
当制件公差为IT10以上,取x=1
当制件公差为IT11~IT13,取x=0.75
当制件公差为IT14以下时,取x=0.5。
表1-11系数x
材料厚度t(㎜)
非圆形
圆形
0.5
工件公差Δ
<
1
1~2
2~4
4
≤0.16
≤0.20
≤0.24
≤0.30
0.17~0.35
0.21~0.41
0.25~0.44
0.31~0.59
≥0.36
≥0.42
≥0.50
≥0.60
0.20
0.30
≥0.16
≥0.20
≥0.24
≥0.30
查的x=0.75,Δ=0.24
故得:
dp=(dmin+x△)+δp=((29+0.75×
0.21)+0.02
=29.16+0.02
dd=(dp+Zmin)-δp=*(29.16+0.27)-0.025
=29.43-0.025
(b)落料
落料时以落料凹模设计为基准的刃口尺寸计算如下表
表1-11以落料凹模设计为基准的刃口尺寸计算
工序性质
凹模刃口尺寸磨损情况
基准件凹模的尺寸图2.3.3(b)
配制凸模的尺寸
落料
磨损后增大的尺寸
Aj=(Amax-x△)+0.25△
按凹模实际尺寸配制,保证双面合理间隙2cmin~2cmax
磨损后减小的尺寸
Bj=(Bmin+x△)-0.25△
磨损后不变的尺寸
Cj=(Cmin+0.5△)±
0.125△
Aj、Bj、Cj为基准件凹模刃口尺寸;
Amax、Bmin、Cmin为落料件的极限尺寸。
计算凹模各尺寸:
查上表1-11的,尺寸42,52,55对应的x=0.75,尺寸18对应x=1
磨损后增大的尺寸的:
Aj=(Amax-x△)+0.25△
42mm的:
A1=(42-0.75×
0.25)+0.25/4=41.81+0.06
52mm的:
A2=(52-0.75×
0.30)+0.30/4=51.81+0.06
18mm的:
A3=(18-1×
0.18)+0.18/4=17.82+0.05
圆弧R9,R21的尺寸为了保证分别与18mm,42mm相切,不用计算直接取其
A3,A1值的一半。
磨损后不变的尺寸:
0.125△
44mm的C1=(55+0.75×
0.3)±
0.125×
0.3=54.78±
凸模的尺寸按上述凹模相关尺寸配制,保证双面间隙Zmin~Zmax=0.21~0.27mm(前面以由表1-11查的)
(C)模具间隙
模具间隙即模具凸模与凹模之间的间隙,其对冲裁件的质量,冲裁力,模具寿命都有较大的影响。
因此选择合理的间隙,非常重要,确定合理间隙的方法如下:
1.理论确定法
如图1-7,中的三角形ABC可确定合理的间隙,
图1-7
C=(t-h0)×
t×
tgβ=t(1-h0/t)×
tgβ
查下表1-12的:
h0/t=0.2,β=4°
表1-12h0/t与β的值
h0/t
β
退火
硬化
软钢紫铜软黄铜
6°
5°
中硬钢硬黄铜
4°
硬钢硬青铜
C=3×
(1-0.2)×
tg4°
=3×
0.8×
=0.168mm
Z=2c=0.336mm
2.经验法
材料为硬材料:
t<3mmZ=(8%~10%)t
t=1~3mmZ=(11%~17%)t
t=3~5mmZ=(17%~25%)t
已知材料厚度为:
t=3mm
Z=0.33~0.51mm
式中,h0——凸模切入深度;
β——最大剪应力方向与垂线方向的夹角
第7章模具的总体结构设计
(1)模具的类型选择
根据冲裁件的结构特点,需冲孔和落料两道工序方能完成零件成型,而且要进大批量的生产,综合上述,课选择正装式复合模进行生产,其结构图如
图1-7.。
在压力机的一次工作行程中,在模具同一部位同时完成数道冲压工序的模具,称为复合模。
模具各部分名称和代号等参数如下表1-12
表1-12
(2)模架的选择
模架由上下模座,模柄及导向装置(导柱,导套)组成。
(a)模架的形式
模架的形式选择后侧导柱模架,可纵横送料,送料方便。
其模架的形式结构如下图1-8
图1-8
(b)导柱和导套
导柱和导套的结构与尺寸都可以直接从标准中选取,选滑动导向的导柱导套,安装尺寸示意图如图1-9.
图1-9
(c)模柄的选择
所作设计为大型,模具都通过模柄固定在压力机滑块上的,可使用螺钉固定。
第八章工作零件的设计与计算
(1)凸模
(a)凸凹模和凸模的结构形式
由于冲裁件的落料件为非圆形的,可选择直通式凸凹模,直通式凸模的工作部分和固定部分的形状与尺寸做成一样,这类凸模一般采用线切割方法进行加工。
1-10整体式凸模
而冲孔凸模则选择用台阶式凸模,如下图1-11
图1-11标准圆形凸模
(b)长度计算
凸模长度应根据模具结构的需要来确定。
采用固定卸料板和导料板结构时,图1-12所示,凸模的长度应该为:
L=h1+h2+h3+(15~20)mm
图1-12
(c)材料和其他要求
冲裁件的形状复杂,可选择Cr12,热处理为淬火;
工作部份的粗糙度为:
Ra0.8~0.4um固定部分粗糙度为:
Ra1.6~0.8um
(2)凹模
(一)凹模洞口的类型
1.凹模洞口的类型
常用凹模洞口类型如图1-14所示,其中a)、b)、c)型为直筒式刃口凹模。
其特点是制造方便,刃口强度高,刃磨后工作部分尺寸不变。
广泛用于冲裁公差要求较小,形状复杂的精密制件。
但因废料或制件在洞壁内的聚集而增大了推件力和凹模的涨裂力,给凸、凹模的强度都带来了不利的影响。
一般复合模和上出件的冲裁模用a)、c)型,下出件的用b)或a)型。
d)、e)型是锥筒式刃口,在凹模内不聚集材料,侧壁磨损小。
但刃口强度差,刃磨后刃口径向尺寸略有增大(如α=30`时,刃磨0.1mm,其尺寸增大0.0017mm)。
图1-14凹模洞口的类型
h1、h2、h3、t分别为凸模固定板、卸料板、导料板、材料的厚度。
15~20mm为附加长度,包括凸模的修磨量,凸模进入凹模的深度及凸模固定板