聚氨酯湿法合成革Word格式文档下载.docx
《聚氨酯湿法合成革Word格式文档下载.docx》由会员分享,可在线阅读,更多相关《聚氨酯湿法合成革Word格式文档下载.docx(6页珍藏版)》请在冰豆网上搜索。
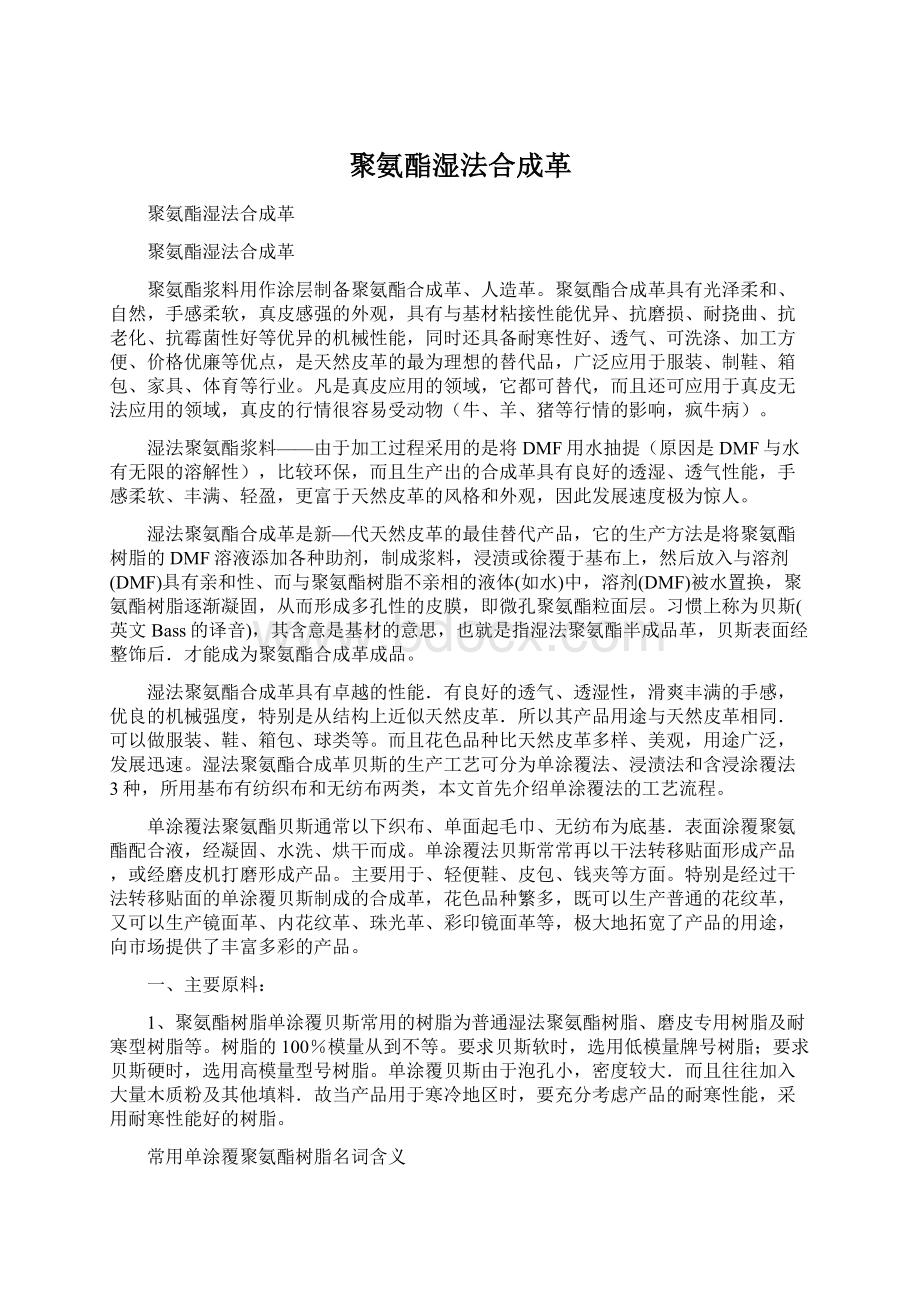
1、聚氨酯树脂单涂覆贝斯常用的树脂为普通湿法聚氨酯树脂、磨皮专用树脂及耐寒型树脂等。
树脂的100%模量从到不等。
要求贝斯软时,选用低模量牌号树脂;
要求贝斯硬时,选用高模量型号树脂。
单涂覆贝斯由于泡孔小,密度较大.而且往往加入大量木质粉及其他填料.故当产品用于寒冷地区时,要充分考虑产品的耐寒性能,采用耐寒性能好的树脂。
常用单涂覆聚氨酯树脂名词含义
品名NameofProduct;
固体份Solid(%);
粘度Viscosity(pa.s/25);
溶剂ViscositySolvent;
100%模量Modulus(Mpa);
抗拉强度T/S(Mpa);
伸长率E/L(%);
特性及用途Characteristics&
Application
2.木质粉在单涂覆贝斯配方中使用一定量的木质粉,既能降低产品成本.又能在凝固过程中起到骨架的作用。
木质粉的细度一般在400目以上。
3.阴离子表面活性剂OT—70阴离子表面活性剂主要起加快DMF与水的交换速度.提高凝固速度的作用,同时,使泡孔细密化。
阴离子表面活性剂可生成球形泡孔结构。
4.非离了表面活性剂S—80非离子表面活性剂由于其具有疏水性,可推迟表面的凝固速度,因面可使内部的DMF与水更快更充分地交换,非离子表面活性剂可生成针状的泡孔结构。
面活性剂的用量可以适当加大,以便贝斯产生针状泡孔,手感柔软,磨皮后增加绒感。
4、DMF除了起到溶解及稀释聚氨酯树脂的作用外,还对贝斯的泡孔大小有较大影响。
DMF用量大时,贝斯的泡孔则大,DMF用量小时、贝斯的泡孔则小,而且,适当加大DMF的用量,还可以降低成本。
为了满足不同用户的使用要求,DMF的用量要合理,一般在单涂覆贝斯的配方中用量为65份左右,做服装革时也可增到100份以上。
5、着色剂着色剂的用量因色泽不同差异很大,在普通贝斯中一般用量为5—10份左右,但在磨皮革配方中.着色剂用量较大,高达25—30份。
着色剂用量小时.色泽不鲜艳.所以通常选用稳定性高、着色力强的着色剂,如有机颜料、高色素炭黑等。
由于湿法贝斯的生产工艺是在水中凝固,故着色剂在水中的溶解性是一项重要技术指标。
在水中溶解性大的着色剂不能用于湿法贝斯的生产,否则会影响贝斯的色泽及废水的回收处理。
粘度是配方设计时应考虑的一个重要指标。
贝斯所配制的浆料的粘度为7000—9000Pa&
#8226;
s,用于单涂覆粘度过高,则流动性差,过滤困难;
粘度过低,容易透底,造成革面不平整等缺陷,而且还浪费浆料。
另外.应注意在设计磨皮革配方时,由于没有填料,且要控制上述要求的粘度,就必须选用本身具有较高粘度的树脂,才能达到工艺要求。
三、生产工艺技术单涂覆聚氨酯贝斯主要使用起毛布为底基,也可使用平织布和无纺布。
但用无纺布作底基时.首先必须用橡胶胶乳或其他高分子材料进行预处理.必要时,用磨皮机将表面打磨平整。
现在国内行场上,可以采购到经过橡胶胶乳浸渍处理的无纺布,其表面平整,弹性好,可以直接用于湿法聚氨酯单涂覆使用。
无论使用起毛布,还是平织布或无纺布为基布流程是一样的,所用配方也基本相同。
1、生产工艺流程简述:
基布开卷经储布架进入浸水槽浸湿,再通过挤压辊将水挤出大部分,通过烫平轮一方面除去部分水分,同时将基布烫平(如果使用橡胶胶乳预处理过的无纺布基材,则可不必浸水),然后在涂料台上涂覆聚氨酯配合浆料,再进入凝固槽,使聚氨酯凝固成皮膜,而后再水洗、烘干、冷却卷成大卷贝斯。
2、生产工艺操作要点单涂覆贝斯所要求的浆料粘度较高,一般控制在,因此,配科时的加科顺序更为重要,以免影响产品质量。
一般在容器内先加入DMF而后加入木质粉,并用搅拌机充分搅拌,约10min左右,确保木质粉充分分散到DMF里。
若先把DMF和聚氨酯混合在一起搅拌,而后加入木质粉,则会使木质粉结团,不能充分地分散到树脂溶液中.即使过滤.结团的木质粉也极易堵塞过滤网,严重时造成浆料无法使用。
助剂添加的顺序对普通贝斯来说,影响要小一些。
一般在木质粉加入到DMF中分散均匀后加入即可,搅拌数分钟后停止搅拌.按配方要求加入聚氨酯树脂,用高速搅拌机搅拌20min后,测量浆料的粘度,使其在工艺要求范围内。
配制磨皮贝斯浆料时,助剂的加入顺序非常重要。
先在配料罐内加入阴离子表面活性剂(比如OT—70)与DMF搅拌至少5min后,再加入非离子表面活性剂(比如S—80),搅拌均匀后再加入聚氨酯树脂和色料,并搅拌至均匀一致为止。
如将OT—70与S—80同时加入,则无论浆料搅拌多长时间,生产的贝斯在磨皮时极易出现亮斑。
磨皮贝斯配方一般不使用木质粉,以免出现空壳等疵点。
生产磨皮贝斯时着色剂用量较大,着色剂的细度要求很高,若用色粉,则应事先将其用DMF溶解过滤后.再加入到浆中。
若使用色浆也应过滤后使用。
粘度是配料工序的一个重要工艺参数,一般单涂覆贝斯所用配合聚氨酯浆料的粘度为.为了保证产品的稳定,浆料的粘度必须控制在一定的范围内。
而配制的浆料的粘度既与树脂的生产日期、批号、品种有关,又与木质粉等填料的性质有关。
为了使粘度稳定,有时DMF的用量就不能严格按配方执行。
相比较而言,维持粘度的稳定比维持配方中DMF用量的准确性更为重要。
配制的浆料粘度符合要求后,将之移至真空脱泡机内脱泡。
脱泡时,先进行低真空度脱泡,以避免脱泡初期涌起的大量气泡把浆料带入真主管道或真空泵中造成事故。
随着脱泡时间的加长,逐渐加大真空度,同时,用手电观察料面的气泡情况。
气泡脱除干净后,停止真空泵运转,完全卸压后出料。
脱泡时间一般为40min左右。
若浆料粘度偏高时,可适当延长脱泡时间。
脱泡后的浆料用60—100目的滤网过滤,装在不锈钢桶内备用。
配制好的浆料要及时加盖密封,尤其是在潮湿的夏季更要注意浆料的吸湿问题,否则料桶内上部分的料因吸水会在使用中引起涂层不均、产生坑点等缺陷。
3、基布浸水处理基布开巷,经过储布架入浸水槽、然后用挤压辊把基布中的水分挤干,经烫平辊将基布烫至半干。
浸水处理的作用有两个:
一是提高织物湿度,防止浆料过分渗入基布组织内,产生透底现象,浪费原材料。
二是对脱脂性较差的基布,水槽中除清水外,还应加入1%的阴离子表面活性剂,如渗透剂等,以改善基布的亲水性,提高贝斯的外观质量。
如果基布较密实,浆料粘度较高,也可以不经浸水处理而直接涂料。
基布浸水烫干程度是一个重要的工艺参数.但生产现场不好定量测量,多凭经验掌握,一般以上述粘度的配合浆料涂覆后不透底为原则。
基布处理过湿,易造成浆料与甚布粘结不牢;
若过干,则易产生透底现象,使浆料消耗增大,且造成革面不平整。
4、涂覆——凝固经处理的基布,通过涂料台,采用辊衬涂覆法,把聚氨酯浆料均匀地涂覆在基布上。
在使用起毛布为底基时,要注意起毛布表面起毛的方向。
顺毛涂覆,贝斯表面光洁;
逆毛涂覆,贝斯表而粗糙,尤其是在起毛布的起毛较长时,这种现象更为明显。
涂层的厚度不仅对产品的厚度有影响,而且对产品的风格及质量也有影响。
涂层太薄,不能遮盖布毛,使贝斯表面粗糙,手感发板无弹性;
涂层太厚,易造成泡孔不匀、面层与基材分离等缺陷。
因此,当用户对产品厚度要求有变化时,不能仅仅依靠涂层厚度来改变产品的厚度,而主要依据恰当地选用基布的厚度来改变产品的厚度。
经涂覆聚氨酯浆料的基布进入凝固槽。
凝固槽中的凝固液是由水与DMF组成的,DMF的含量一般为20%—25%。
生产磨皮贝斯时,DMF的含量控制在10%一15%之间。
过高的含量会影响凝固速度.而且造成水今固形份含量增加;
浓度过低不仅增加DMF的回收成本.还使贝斯表面收缩率增大,导致卷边,降低产品质量。
在凝固槽内,浆料中的DMF与水发生置换,DMF迅速往水中迁移,而水渗入到料层中的速度则较慢。
当涂料层中DMF的浓度下降到一定程度时.溶解的聚氨酯发生凝固,形成有多孔的皮膜。
在浆料凝固过程中产生一定的收缩,使涂层变薄,且有一定程度的卷边。
为防止卷边,一方面要保证凝固槽今的DMF浓度,另一方面在配料时可多加入些S—80,以延迟表而的凝固,增大泡孔。
还可以用铁夹子夹住布边和增加张力辊的方法来防止卷边。
凝固槽的温度一般为常温。
在冬季,可适当加温、但一般不超过40℃,通常控制在25—30℃。
过高的温度会使涂层凝固质量下降。
涂料层从入水凝固到出凝固槽凝固完全,大约需要5—10min,这与配方树脂牌号、水中的DMF浓度及温度等有密切关系。
料层在完全凝固前,不能与导辊接触,否则会损伤面层。
5、水洗—烘干—卷取聚氨酯涂料层在完全凝固以后,其泡孔层内仍然残留一定数量的DMF,这些DMF必须在水洗槽内强行脱出,如脱除不干净时.烘干后台造成贝斯表面有麻点等缺陷。
在工艺控制上要确保最后一个水洗槽内DMF的含量在1%以下,这样就可以保证贝斯中的DMF脱洗干净。
为了使DMF的洗出速度加快和减少残留于贝斯中的DMF,水洗槽一般都需要加温操作。
实践证明,水洗槽的温度对DMF的洗出速度及贝斯中的DMF残留量影响很大。
在水洗过程中,尤其是在水洗槽的后半部分,由于残留在贝斯中的DMF已经很少,因此,贝斯在水洗水中停留的时间对DMF洗净程度的影响远不如挤压次数对其的影响大。
因此,在水洗操作中,应十分重视贝斯的挤压次数。
贝斯水洗干净后,为除去水分,需烘干处理。
烘箱温度不宜过高,一般不超过150℃。
在进口处,因贝斯含有大量的水分,温度可高些,随着水分的蒸发.在烘箱后部温度可低些,一般120℃即可。
烘干的贝斯经冷却后卷成大卷,以备后加工使用。
四、产品质量缺陷及解决方法单涂覆聚氨酯贝斯在生产中易出现的质量问题,下面列出了一些常出现的质量缺陷,以及它的具体处理方案,但是由于实际过程中的事故原因多种多样,所以工程师在操作的时候要结合自身生产线、原料、工艺、和订单要求等情况,做相对应的调整。
序号质量缺陷产生原因处理办法
1:
剥离强度低:
起毛布起毛太短:
基布浸水后熨干程度不够,较湿:
配方中填料量大:
更换起毛布:
提高熨平温度;
减少填料用量。
2:
贝斯卷边:
凝固槽中DMF浓度太低:
配方中S—80量少:
凝固槽中张力辊设置不当:
提高凝固槽中DMF浓度:
增加S-80用量:
增设张力辊。
3表面不平整:
起毛布起毛不匀或起毛太长:
涂层太薄:
浆料透底:
增加涂层厚度:
降低熨平温度,提高基布湿度。
4表面有针孔:
浆料脱泡不净,延长脱泡时间。
5表面有坑点:
基布脱脂差:
配方不当:
更换基布,或在浸水槽内多加些渗透剂:
调整配方。
6表面有条纹:
凝固不完全:
凝固槽内有硬物接触贝斯表面:
降低车速,提高凝固槽湿度:
排水除掉硬物。
7耐寒性差:
树脂选型不当:
填料用量太大:
选用耐寒树脂如JF-8066AH: