5SWord下载.docx
《5SWord下载.docx》由会员分享,可在线阅读,更多相关《5SWord下载.docx(40页珍藏版)》请在冰豆网上搜索。
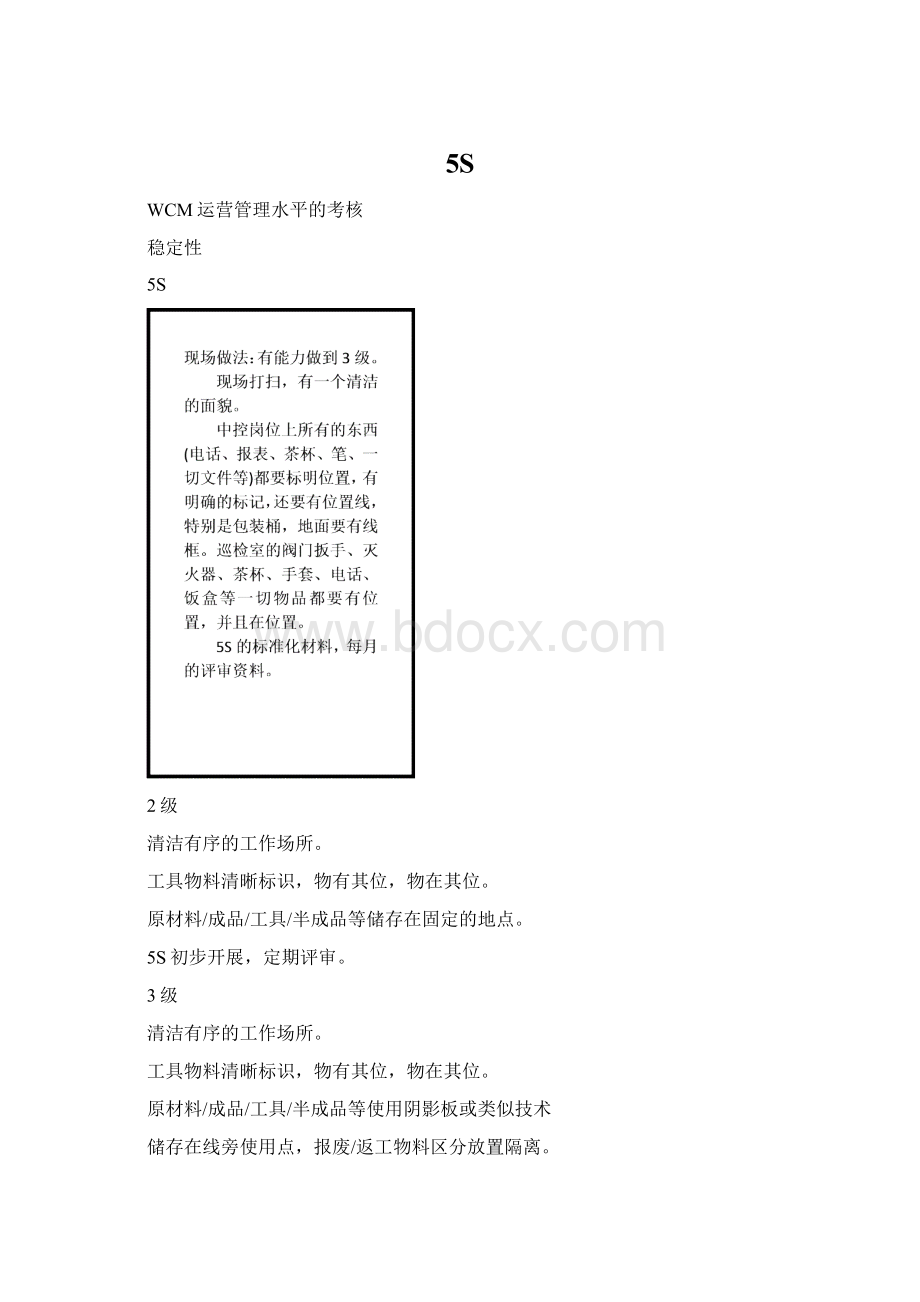
准化作业,作业员遵循程度超过75%。
标准化作业得以维持但生产单元/生产
线未每周审核,标准作业组合表未
加以利用实施过程改进。
在所有生产区域实现标准化并文件化。
标准化作业制定并张贴,并被生产单
元的工作人员理解和使用,作业员遵
循程度超过85%。
标准化作业目视易懂,及时更新,每
周审核,标准作业组合表由管理者及
现场同事加以利用实施过程改进。
一些最佳实践得以复制以持续改进流程。
5级
在所有生产区域实现标准化并文件
化,持续努力简化流程,减少变异。
作业指导书用来培训员工,包括新员
工。
标准化作业张贴在每个工作站/单元/
线,遵循程度超过>
95%。
标准化作业用于启动持续改进活动。
员工协助现场主管/团队领导制定标准
化作业并以此为基础进行改进。
一些最佳实践得以复制以持续改进流
程
TPM
1级
频繁的设备停机,没有停机
时间/OEE的指标数据。
设备脏污,没有PM计划或者查检清单。
设备仅在发生故障时由维修部门的人员进行检修。
有计划性保养。
但紧急维修很普遍。
对于关键设备有PM计划,但大多
数维修发生在非计划停机期间。
对于停机时间/OEE的数据很少.
只有维修技术人员进行设备维修,对设备负责。
所有设备的PM计划张贴出来。
绝大多数的PM计划是基于时间/频率而定。
有TPM程序。
一线作业员负责自主保全,包括基
本的设备保养活动,含清洁,每天
的检查,润滑等等。
这是其标准化
作业的一部分。
机器的开机时间使用图表进行追溯并与目标进行对比。
属于预防性维修(PM)。
自働化
异常探测
4~5级
所有摄像头完好。
操作员熟知每一监控点出现不正常情况由谁负责处理,如何处理。
所有连锁及报警必须及时作出判断及处理,不许有蜂鸣和红色报警出现而不作为。
现场操作员讲解出现异常情况,一键安全停车的按键及操作程序。
没有开发及使用防错装置,错误无法探测。
或者防错装置应用薄弱,使用无法持续。
一线员工通过自检及返工来识别及预防缺陷,
问题难以确定,异常事件在很大程度上被忽视。
实施探测性防错手段,通过抽样检验的方式检出不良品
使有限的不良品流到客户手中。
手工方式发现缺陷。
没有引入过程检验(后工序操作员查核)。
存在一些防错装置和过程监控手
段,但一线员工仍希望预防错误的发生。
只有少数人了解车间的状况,注意到问题的存在。
实施探测性防错手段,执行被动的根本原因分析。
过程检引入但未被遵循。
没有随后的纠正行动。
在工厂75%的工作区域内采用可视化
显示手段监控流程,异常状况容易识别。
重点是通过引入防错装置来预防错误的发生。
过程不流出不良品。
实施预防性防错手段,防错活动着手被动解决根本原因。
很好的执行过程检,但没有随后的纠正行动。
在工厂85%的工作区域内采用可视化显示手段监控流程,
采用防错装置停止失控的过程。
异常状况容易为所有人识别并理解。
广泛使用防错法防止缺陷流出制程。
实施预防性防错手段,过程检持续优化,直到纠正措施实施。
稳健设计。
采用可视化显示手段监控流程,在工
厂范围内采用防错装置自动停止失控
的过程,使异常对工作区域所有的人而言显而易见。
识别防错机会并实施成为日常工作。
安灯系统
一线员工在问题发生时可以通知主管/领班,但不能停止生产。
没有有效的过程帮助员工对存在的问题发出信号。
对报警响应时间缓慢和/或没有纠正行动。
临时解决停线问题。
在所有生产线/单元记录一次通过率的问题,但没有纠正行动。
一线员工可以就质量或安全问题停线并等待主管/领班响应。
安灯信号得以利用清晰暴露问题发生的位置,停线并记录。
进行根本原因分析。
质量或安全问题导致超出生产节拍要求。
在所有生产线/单元记录一次通过率的问题,并有一些纠正行动。
一线员工按照既定程序当有异常发生时有权停线。
快速响应团队组建并要求需要在10分钟内到达问题发生的
准确位置,迅速执行纠正行动,但仍超过节拍时间。
在所有生产线/单元使用一次通过率指标,记录问题,解决问题。
停线程序明确,一线员工有权在出现异常时立即停线。
快速响应团队必须在5分钟内响应。
在线修复质量问题,满足节拍时间要求。
人机分离
一名员工可以操作多台设备(通常是同一类设备),但仍需要监
控过程以防止出现错误。
设备设计中加入质量内置装置以在源头就确保质量,允许一名员
工操作一种或多种类型的多台设备。
过程自动,作业员负责装卸。
在设备的设计中加入基于效率的控制手段(例如,一触式启动或
自动停机),自动卸载,多处理功能
设备的设计及单元布局使作业员仅负责装载产品,设备一个周期
完成,快速便捷的自动卸载产品。
也称为“一步接一步"
。
测量系统
应用MSA/GageR&
R技术非常有限(<
25%),对于关键的
质量特性未使用该技术。
25%),集中在关键的
质量特性上使用。
<
50%的量具测试及校验至少一次,没有定期的计划,集中
在关键的质量特性上使用。
>
50%的量具测试及校验至少一次,有定期的计划,集中在
关键的质量特性上使用。
所有的量具按照定期计划进行测试及校验,所有的测量系统是
可重复的及可再现的,直接集中在关键的质量特性上使用。
控制图
关键的过程指标使用控制图,过程改进专家负责更新。
小于50%过程指标应用控制图,通过过程改进专家保持更新。
大于50%过程指标应用控制图,大部分过程受控,员工对
控制图方法理解有限。
过程能力分析
过程负责人对关键的质量特性进行过程能力评估,过程有能力。
对大多数流程进行过程能力评估,过程负责人对指标及差距负责,员
工有能力意识。
对所有流程进行能力评估,大多数受控,员工懂得如何缩小差距。
准时化
库存管理
库存管理没有遵循FIFO.库存的放置区域远离使用点.
确定库存(原料、WIP、成品)的放置区域和水平困难。
标准WIP数量未度量与确定
在一些孤立的区域有实践FIFO.确定的库存放置区域可能存在,
但是由于没有可视化标识而不清晰,而且没有纪律实行。
建立了标准WIP数量并可以测量。
有正式的系统来支持FIFO实行。
库存放置区域明确而清晰的标识出来。
但是由于缺乏纪律和差的过程
设计经常会背离标准。
实际WIP数量<
150%的标准WIP数量
其他运营支持系统
供应商管理
超过70%的供应商按时交货。
随机的进料检验。
没有团队与供应商协同工作。
没有供应商评估及认证。
超过80%的供应商按时交货。
基于供应商的表现设立
具体的进料检验要求。
供应商评估系统建立。
超过90%的供应商按时交货选择认证合格的供应商。
关键供应商质量需求已识别并评估,有团队协同
供应商解决问题。
超过95%的供应商按时交货。
80%的供应商被认证。
关键供应商KPI建立并持续评估,一些流程程改进团队
协同解决供应商的问题,支持供应商持续改进。
JIT物料
供应开始应用。
在产品研发阶段开始考虑关键供应商
的早期参与。
人力资源管理
每个员工每年培训时数小于10小时,无培训计划,
技能水平低。
没有岗位轮换。
或者每个员工每年培
训时数大于10小时,已制定培训计划。
员工没有交叉培训,大多数一线员工只能操作一种
作业。
没有正式的程序使作业员具备上岗资格,所
有的培训都是靠人带人。
一人一岗(一个作业员只
懂得一项技能,能够在节拍时间内执行标准化作业)。
岗位轮换每月一次。
每个员工每年培训时数大于20小时,培训计划与工
作需要相关联。
大多数作业员掌握了一种以上的技能,但没有正式
的交叉培训程序。
多数培训仅限于最基本的工作技
能。
一线员工在其他的工序交叉训练,实现1岗2
人,1人2岗(2名员工掌握两种不同的工作技能,
能够在节拍时间内执行标准化作业)。
岗位轮换一周一次。
每个员工每年培训时数大于40小时,培训计划与交
叉培训需求及单元指标相联系。
正式的交叉培训程序,关键技能已确定。
大多数培训
受持续改进需求驱动,但培训往往在非计划停机时
间发起进行.追溯技能水平并在大部分区域清楚地张贴。
实现1岗3人,1人3岗(3名员工掌握3种不同的工作
技能,能够在节拍时间内执行标准化作业)。
培训指标板
张贴并保持。
岗位轮换一天一次.
安全环保
执行EH&
S的评估,没有锁定/挂牌上锁程序。
EH&S的差距确定并建立计划改善,优选EH&
S活动,进行LO/TO保养培训。
EH&S部分遵循,关键岗位员工培训,在保养工作中执行
LO/TO程序
EH&S完全遵循,所有的员工接受EH&S细节培训,
遵循LO/TO,但不是100%。
EH&S完全遵循,所有员工理解并对
EH&S的行为负责,完全遵循LO/TO。
新产品开发
新产品/技术/服务开发质量及开发周期变异大,没有标
准的开发程序
存在非正式的新产品/技术/服务开发流程与设计评审。
与主要的竞争对手产品对标定量评估
初步建立了新产品/技术/服务开发程序,但没有得到严格遵循。
初步引入设计评审,有初步的项目控制计划、测量指标及批准程序。
开发及制造阶段,数据管理过程确保新产品/技术/服务其持续的功能
再现性。
建立了标准的新产品/技术/服务开发程序,并得到严格遵循。
严格引入设计评审,有清晰的项目控制计划、测量指标及批准程序。
开发及制造阶段,数据管理过程确保新产品/技术/服务其持续的功能再现
性。
设计团队有适宜的技能使用统计工具开发强健的产品和服务,使用计算机
模拟及设计工具大大缩短开发周期。
过程验证显示新产品/技术/服务满足
客户需求的能力高,首次通过率超过50%
模拟及设计工具大大缩短开发周期,与竞争对手相比有明显优势。
过程验证显示新产品/技术/服务满足客户需求的能力非常高,
首次通过率超过65%
建立了基于客户需求持续开发世界级新产品/技术/服务的业务计划及开发
路径
客户服务质量
没有客户满意度调查及记录。
关键客户未识别,没有正式的方法来确定顾客
的关键需求。
当前的流程只是对顾客问题予以响应。
存在非正式的客户满意度调查,调查结果有记录,
但没有随后的改进计划。
识别出关键客户,建立了有效的过程与客户直接接触,
所采集到的信息可传递到职能部门。
建立了正式的客户满意度调查程序,调查结果有记录,
与客户及时沟通满意度调查结果,有随后的改
进计划及改进结果记录。
对关键客户,建立了关键需求有关的指标,定期评审,
产生改进计划,并与客户沟通改进结果
管理层定期评审所有的运营系统,确定并消除影响客
户满意的薄弱之处。
对关键客户,建立了计分卡程序,
与客户一些建立关键需求有关的指标、实施评审过程,
过程改进计划及结果沟通程序。
在整个产品生命周期,采用系统化的方式与客户及时沟
通满意度调查结果,程序上的变化及改进计划和结果。
在整个组织内部沟通并部署清晰的客户满意目标。
引入第三方客户满意调查,分析及报告系统,为管理层
提供重要信息,以分析客户满意度数据,及时执行改进
计划,客户满意度结果显示持续改进。
组织关注于预测客户问题,预防其发生。
通过客户早期介入项目,客户需求预测及追溯模型等手段
预测客户长短期需求
营销及运营计划S&
OP
无营销及运营计划
针对关键客户关键市场尝试引入营销及运营计划,
但不是必须要求,销售、市场、工程、订单管
理及运营部门开始尝试协同工作
针对关键客户关键市场导入营销及运营计划,
每月一次S&
OP会议,销售、市场、工程、订
单管理及运营部门协同工作,以改进客户服务,
提高库存周转
至少每月一次S&
OP会议,销售、市场、工程、
订单管理及运营部门协同工作,以改进客户服务,
全面导入营销及运营计划,销售、市场、工程、
订单管理及运营部门协同工作,生产计划、销售
计划可实现并与长期业务计划连为一体,客户服
务,库存周转、生产效率持续改进
CI执行及部署能力(持续化)
战略目标制定与部署
仅仅使用传统的销售,损益,未使用平衡计分
卡、方针计划HOSHINPLAN或者类似工具来
运营业务。
建立起平衡计分卡或者类似工具,但计分卡未
能与运营管理系统很好地结合,领导者很少关
注计分卡上的指标及目标。
孤立的进行各指标
的评估,未能确定彼此如何相互影响。
领导者
仅仅把计分卡作为一种响应方式;
建立起平衡计分卡或者类似工具,而且计分卡能与
运营管理系统很好地结合,各指标的评估考虑到
彼此如何相互影响。
由反应式向预防式转变。
建立起平衡计分卡或者类似工具,并用以驱动
业务的运行。
计分卡能与运营管理系统很好地
结合,领导者依据平衡计分卡评估绩效,进行
差距分析,制定行动方案。
关键流程的识别
支持战略及年度目标实现的核心流程及关键的
业务支持流程未识别,过程负责人未明确;
业务支持流程已识别确定,过程负责人明确,
但未对该流程进行评估;
支持战略及年度目标实现的核心流程及关键的业务
支持流程已识别确定,过程负责人明确,评估指标
明确,对其中绝大多数的流程进行了评估;
支持战略及年度目标实现的核心流程及关键的业务支持
流程已识别确定,评估指标明确,应用数据对流程进行
了评估并驱动持续改进;
过程负责人明确并有望对过程
实施改进;
支持流程已识别确定,评估指标明确,应用数据对
过程能力进行了测量和评估并驱动持续改进;
过程
负责人明确并有清晰的目标对过程实施改进。
过程绩效评估指标的建立
没有统一的过程绩效评估指标,也没有建立相
关数据的采集;
核心流程及关键业务支持流程导入统一的过程
绩效评估指标对产品和服务质量进行评估,并
建立了相关数据采集;
75%以上的流程使用统一的过程绩效评估指标,并
90%以上的流程使用统一的过程绩效评估指标,
并建立了所有相关数据的采集;
100%的流程使用统一的过程绩效评估指标,并
建立了所有相关数据的采集;
持续改进的沟通
有正式的持续改进沟通计划(孤立的或者综合
的),但部署零散。
在企业内部偶尔可见如
下行为:
-高层对员工的持续改进定期宣讲
-实现定期项目分享
-建立持续改进文化宣传走廊
-建立明星走廊
-引入“我建议“体系
-引入BBS互动平台
-引入CI标识体系
-引入“总裁月信”制度
有正式的持续改进沟通计划和部署,有关六西格玛
持续改进的信息坚持不懈得通过统一的业务渠道
(如公司文化专刊)进行沟通。
但计划未能与组织
的整体战略及规划的沟通相融合。
在企业内部经常可见如下行为:
有全面的持续改进沟通计划及部署,该计划与
组织的整体战略及规划沟通完全融合,持续得
对业务指标和目标,行动计划,重要CI项目进
行评审。
在企业内部总是可见如下行为:
-落实最佳实践分享机制,并通过PS系统建立
持续改进绩效评估
员工并不清楚业务目标,更不了解她们的工
作如何影响到业务目标。
与员工之间的基本沟通得以建立。
但绩效评估
指标及目标没有清晰得与过程相联系。
与员工之间的基本沟通得以建立,许多员工了解他
们的工作如何影响到业务指标和目标。
绝大多数的
员工绩效目标由他们的主管依据他们的工作内容设
立,持续改进方面的内容考虑纳入员工的绩效评估
中;
绝大多数员工了解他们的工作如何影响到业务
指标和目标。
所有员工绩效目标由他们的主管
依据他们的工作内容设立,初步建立起对管理
者和基层员工的持续改进绩效评估体系;
所有员工了解他们的工作如何影响到业务指标
和目标。
所有员工绩效目标由他们的主管依据
他们的工作内容设立。
过程改进是员工工作内容的一部分。
全面建立
起对管理者和基层员工的持续改进绩效评估体
系,持续改进方面的内容已经全面纳入员工的
绩效评估中并得以贯彻实施;
项目识别与优选
没有正式的项目诊断流程。
项目根据管理层的
指令确定。
没有对项目实施的难易程度以其影
响作出评估。
项目聚焦于个别功能区域。
建立了正式的通过持续改进办公室评审并核准
项目的诊断流程。
项目的选择没有与关键的业
务指标、核心流程及职能活动相联系。
没有对
项目实施的难易程度以其影响作出评估。
没有
财务指导方针用于指导项目选择,项目聚焦于
个别功能区域。
项目机会诊断通常每年一次。
建立了系统化的通过持续改进办公室来操作的项目
诊断流程。
项目的选择考量了项目实施的难易程度
以其其影响。
项目与关键的业务指标、支持关键业
务指标的核心流程、职能活动相联系。
有非正式的
财务指导方针用于指导项目选择。
项目既涉及个别
功能区域又涉及工厂层面的整个价值流。
项目机会诊断通常半年一次,项目偏重于流程质量
改进
项目诊断流程持续运行,并与项目管理及追
溯流程结合以评估资源的部署。
项目与关键的
业务指标、支持关键业务指标的核心流程、职
能活动相联系,支持企业目标部署的实现。
有
正式的财务指导方针用于指导项目选择。
诊断
及优选的项目涉及从供应商到客户的整个价值
流。
项目机会诊断通常半年一次,同时结合核心管
理指标的定期评审,持续产生重要的CI改进项
目。
增加以精益价值流改进为主的持续改进项
项目管理
没有正式的流程来追溯项目进度及结果。
项目的财务收益没有要求。
建立起初步的追溯项目结果的流程,但是项目
结果与业务指标的结果很难连接。
60%的项目可以计算财务收益或有财务指
向,并得到验证。
-实施卓有成效的规
划,将技术革新项目,精益六西格玛带级认证
及已认证带级人员的持续改进项目及其他快速
改进项目都纳入持续改进项目管理的范畴
项目追溯及管理的流程建立起来并采用项目管理软
件系统进行管理,项目结果可以与业务指标联系起
来。
只有50%的项目按照该流程进行评审和管理。
项目的关键里程碑活动未如期严格实施并经过关口
评审。
60-79%的项目可以计算财务收益或有财务指
项目追溯及管理的系统化流程建立起来并采用
项目管理软件系统进行管理,项目结果可以与
业务指标联系起来并经过财务确认。
所有项目
按照该流程进行评审和管理。
项目关键阶段
的里程碑活动有定义并交付,通过关口评审。
项目实施过程中的障碍得以识别并及时解决。
有些项目的解决方案成果得以复制,但整体而
言没有统一部署。
80-95%的项目可以计算财务收益或有财务指
项目的各阶段
关键里程碑活动有定义并交付,通过关口评审
项目实施过程中的障碍得以识别并及时解决
项目解决方案成果复制与推广有专门进行评
估,效益最大化始终得以贯彻落实。
96-100%的项目可以计算财务收益或有财务
指向,并得到验证。
持续改进推行组织
持续改进办公室初步建立,持续改进组织中的
职能角色和关键责任明确,但没有充足的持续
改进组织资源配置,没有专门的人担当这些角
色,履行这些责任;
组织中的各角色被动得实
施持续改进工作;
持续改进办公室已经建立,工作程序和工作任务
实现标准化,持续改进组织资源配置充足,各角色
能够按照既定的程序执行工作任务;
25%以上的工
作任务得到落实
持续改进办公室已经建立,工作程序和工作任
务实现标准化,持续改进组织资源配置充足,
各角色能够主动执行工作任务,不断优化工作
质量,75%以上的工作任务得到落实
各角色能够主