第四节热破坏加工全Word格式文档下载.docx
《第四节热破坏加工全Word格式文档下载.docx》由会员分享,可在线阅读,更多相关《第四节热破坏加工全Word格式文档下载.docx(70页珍藏版)》请在冰豆网上搜索。
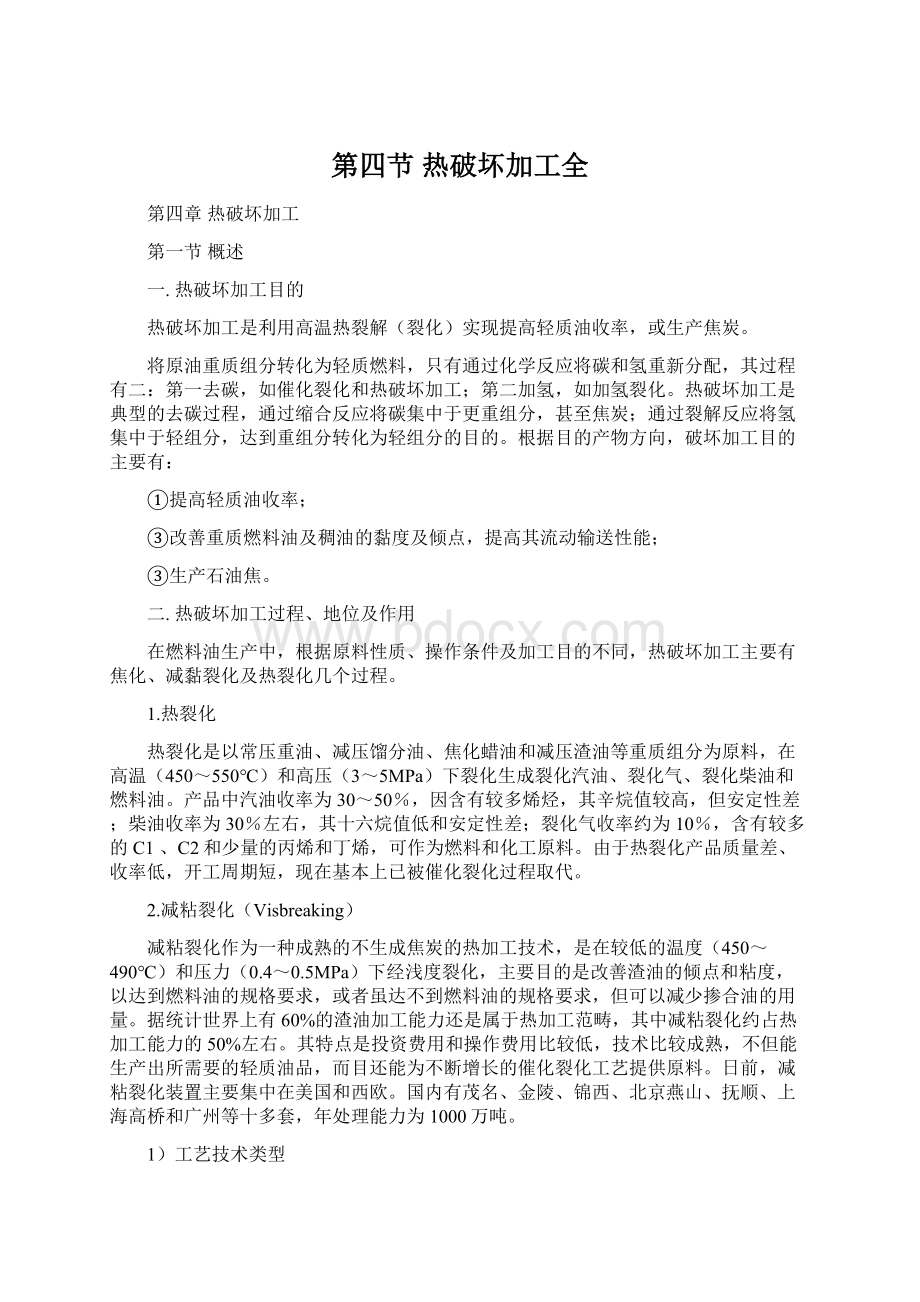
在渣油中加入一定量的具有供氢效果的化合物,也能起到氢气存在时同样的效果,并目还可以避免氢气带来的许多不利因素。
这些化合物能在热反应过程中提供活性氢自由基,有效地抑制自由基的缩合,从而提高裂化反应的苛刻度增加中间馏分油的产量。
供氢减粘裂化工艺就是在常规减粘裂化工艺基础上加入具有供氢效果的溶剂,使反应过程中液体供氢剂释放出的活性氢与渣油热裂化过程中产生的自由基结合而生成稳定的分子,从而抑制自由基的缩合。
可提高裂化反应的深度,防止结焦,增加轻馏分油和中间馏分油的收率。
④减黏组合工艺
如洛阳石化四联合装置的溶剂脱沥青一催化裂化一减粘裂化组合工艺;
加拿大的KastenEadieTechnogy公司的破乳脱水-减粘组合工艺,可以同时解决脱水和减粘两个问题。
2)发展及应用
①传统热减粘裂化工艺的改进
·
使用进料分布器,解决减粘裂化进料和裂解产物在减粘裂化塔内停留时间不一样导致了部分物料过度裂解而部分物料又裂解不足;
使用固体颗粒作为生焦载体,提供结焦场所,提高特重油转换率;
采用流化床裂化反应器,提高减粘裂化过程操作苛刻度并增加馏分油产量。
②开发催化减粘裂化工艺技术
催化加氢减粘裂化;
硒催化减粘裂化。
③在减粘裂化原料中加入添加剂
加入供氢剂;
加入降黏剂;
加入防焦剂。
3.焦碳化
简称焦化,是以减压渣油为原料,在常压液相下进行长时间深度热裂化反应。
其目的是生产焦化汽油、柴油、催化裂化原料(焦化蜡油)和工业用石油焦。
其中焦化汽油和柴油的安定性较差,需进一步精制加工。
焦化过程主要有延迟焦化、釜式焦化、平炉焦化、流化焦化及灵活焦化,其中延迟焦化占绝大多数(2004年占94%)。
因此,本书主要阐述延迟焦化过程。
延迟焦化自20世纪30年代开发以来,已成为渣油加工主要工艺。
2006年全世界焦化处理量为24140.2万t/a,占原油处理能力的5.7%;
其中美国焦化处理量为13046.7万t/a,占原油处理能力的15.1%;
我国焦化处理量为858.5万t/a,占原油处理能力的2.7%,具重油转化能力第一位,其余为催化裂化、溶剂脱沥青、渣油加氢、氧化沥青等。
第二节热破坏加工化学反应
一.热破坏加工化学反应类型
热裂化、焦炭化、减粘裂化等热加工过程所处理的原料,都是石油的重质馏分或重、残油等。
它们的组成复杂,是各类烃和非烃的高度复杂混合物。
在受热时,首先反应的是那些对热不稳定的烃类,随着反应的进一步加深,热稳性较高的烃类也会进行反应。
烃类在加热条件下的反应基本上可分为两个类型,即裂解与缩合(包括叠合)。
裂解产生较小的分子为气体,缩合则朝着分子变大的方向进行,高度缩合的结果便产生胶质、沥青质乃至最后生成碳氢比很高的焦炭。
1.裂解反应
1)烷烃
热裂解反应是指烃类分子发生C-C键和C-H键的断裂,但C-H键的断裂要比C-C键断裂困难,因此,在热裂解条件下主要发生C-C断裂,即大分子裂化为小分子反应。
各类烃中烷烃热稳定性最差,且分子量越大越不稳定。
如在425℃温度下裂化一小时,C10H22的转化率为27.5%,而C32H66的转化率则为84.5%。
异构烷烃在加热条件下也可以发生C-H键的断裂反应,结果生成烯烃和氢气。
这种C-H键断裂的反应在小分子烷烃中容易发生,随着分子量的增大,脱氢的倾向迅速降低。
烷烃裂解反应如:
C20H42→C10H22+C10H20
C20H42→C20H40+H2
烷烃各种键能数据见表4.2.1。
表4.2.1烷烃各种键能数据
键的位置
键能/(kJ/mol)
CH3-H
C2H5-H
C3H7-H
nC4H9-H
iC4H9-H
tC4H9-H
CH3-CH3
431
410
398
394
390
373
360
C2H5-C2H5
C3H7-CH3
nC3H7-nC3H7
nC4H9-nC4H9
iC4H9-iC4H9
335
339
318
310
364
由表4.2.1可知,烷烃热裂解反应规律:
①C—C键的键能大于C—H键,因此C—C键更易断裂;
②长链烷烃中,越靠近中间的C—C键能越小,易发生中间断裂;
③随烷烃分子增大,烷烃中的C—C键及C—H键的键能都呈减小趋势,即它们的热稳定性逐渐下降;
④异构烷烃中的C—C键和C—H键的键能都小于正构烷烃,即异构烷烃更易断链和脱氢。
因此产物中异构烷烃量远少于正构烷烃;
⑤烷烃分子中叔碳上的氢最容易脱除,其次是仲碳上的。
2)环烷烃
环烷烃的热稳性较高,在高温下(575~600℃)五员环烷烃可裂解成为两个烯烃分子。
除此之外,五员环的重要反应是脱氢反应,生成环戊烯。
六员环烷烃的反应与五员环烷相似,只是脱氢较为困难,需要更高的温度。
六员环烷的裂解产物有低分子的烷烃、烯烃、氢气及丁二烯。
带长侧链的环烷烃,在加热条件下,首先是断侧链,然后才是断环。
而且侧链越长,越易断裂。
断下来的侧链反应与烷烃相似。
多环环烷烃热分解,可生成烷烃、烯烃、环烯烃及环二烯烃,同时也可以逐步脱氢生芳烃。
3)芳香烃
芳烃,特别是低分子芳烃,如苯及甲苯对热极为稳定。
带侧链的芳烃主要是断侧链反应,即“去烷基化”,但反应温度较高。
直侧链较支侧链不易断裂,而叔碳基侧链则较仲碳基侧链更容易脱去。
侧链越长越易脱掉,而甲苯是不进行脱烷基反应的。
侧链的脱氢反应,也只有在很高的温度下才能发生。
4)烯烃
直馏原料中几乎没有烯烃存在,但其它烃类在热分解过程中都能生成烯烃,烯烃在加热条件下,可以发生裂解反应,其碳链断裂的位置一般发生在双键的β位上,其断裂规律与烷烃相似。
在温度不高时,烯烃裂解成气体的反应远低于缩合成高分子叠合物的反应。
由于缩合作用所生成的高分子叠合物也会发生部分裂解,这样,缩合反应和裂解反应就交叉地进行,使烯烃的热反应产物的馏程范围变得很宽,而且在反应产物中存在有饱和烃、环烷烃和芳香烃。
烯烃的分解反应有两种形式:
大分子烯烃→小分子烯烃+小分子烯烃
大分子烯烃→小分子烷烃+小分子二烯烃
其中二烯烃非常不稳定,其叠合反应具有链锁反应的性质,生成分子量更大的叠合物,甚至缩合成焦炭。
当温度超过600℃时,烯烃缩合成芳香烃、环烷烃和环烯烃的反应变得更为明显。
5)含硫化合物
原油中含硫化台物主要有硫醇、硫醚、二硫化物和噻吩等,在重油中噻吩类硫含量约占总硫含量的三分之二。
硫醚类化合物中C—S键能小于C—C键,其热稳定性低于同碳数的烃类,在受热条件下C—S键很容易断裂,这是热破坏加工过程能部分脱硫的原因之一。
不同结构硫醚的热稳定性也不同,芳基硫醚比较稳定,环硫醚(硫杂环烷)次之,烷基硫醚最不稳定。
烷基硫醚和环硫醚受热转化的产物主要是不饱和烃类和H2S,如:
RCH2一S—CH2CH2R’→RCH=CH2+R’CH=CH2+H2S
和芳香环相类似,噻吩环的热稳定性相当高,一般情况下环不易破裂。
重质油中含有噻吩衍生物,而且多半是属于苯并噻吩系、二苯并噻吩系和萘并噻吩系,受热条件下它们会产生烷基或环烷取代基的断裂反应,而芳香环和噻吩环并合的稠环系则基本保留。
所以重质油热转化过程所生成的渣油中的硫大部分为噻吩硫。
延迟焦化所生成的高硫石油焦中硫的前身也应该是噻吩硫。
6)含氮化合物
渣油中的氮含量也是比较高的,所含的氮化物主要存在于五员的吡咯系或六员的吡啶系的杂环中,它们均具有芳香性,这种热稳定环不易破裂。
渣油中的氮杂环一般是与苯环或萘环相并合的。
在热转化条件下,它们往往会缩合为更大的芳香环系,从而富集于热反应后的残渣油中。
这些含氮环系分子上大多还带有烷基侧链。
在受热时,它们和一般烷基芳香烃一样会发生侧链断裂反应。
由于氮的存在,与氮杂环并合的芳香环上的烷基侧链与芳香环之间的C—C键会被活化,从而使侧链更容易断裂,导致重质油热转化反应速率的增大。
7)含氧化合物
原油中所含的氧主要存在于羧基和酚基中,羧酸主要是环烷酸。
此外,还有少量的脂肪酸和芳香酸。
羧酸对热不稳定,容易发生脱羧基反应生成烃类和CO2,如:
RCOOH→RH+CO2
8)胶质和沥青质
胶质、沥青质主要是多环、稠环化合物,分子中也多含有杂原子。
它们是相对分子质量
分布范围很宽、环数及其稠合程度差别很大的复杂混合物。
缩合程度不同的分子中也含有不
同长度的侧链及环间的链桥。
因此,胶质及沥青质在热反应中,除了经缩合反应生成焦炭外,还会发生断侧链、断链桥等反应,生成较小的分子。
表4.2.2列出了胜利管输油减压渣油中的胶质、沥青质在460℃、45min热反应条件下的反应结果。
表4.2.2胜利管输油胶质、沥青质热反应数据
组分
转化率(w)/%
相对产率①(w)/%
馏分油
气体
焦炭
中、轻胶质
重胶质
沥青质
59.4
92.9
98.5
51.5
35.1
25.7
16.5
4.5
1.5
31.7
60.3
72.8
注:
①相对产率=产品收率/转化率
由表4.2.2中数据可见,轻、中、重胶质及沥青质的热反应行为有明显的差别,随着缩合程度的增大,馏分油的相对产率下降而焦炭的相对产率增大,对沥青质而言,在460℃、45min
的条件下,已转化的原料中约3/4都转化为焦炭。
沥青质分子的稠合程度很高,带有的烷基侧链很少,而且是很短的侧链,因此,反应生成的气休也很少。
2.缩合反应
石油烃在热的作用下除进行分解反应外,还同时进行着缩合反应,所以使产品中存在相当数量的沸点高于原料油的大分子缩合物,以至焦炭。
缩合反应主要是在芳烃及烯烃中进行。
芳烃缩合生成大分子芳烃及稠环芳烃。
烯烃之间缩合生成大分子烷烃或烯烃。
芳烃和烯烃缩合成大分子芳烃。
缩合反应总趋势为:
芳烃,烯烃(烷烃→烯烃)→缩合产物→胶质、沥青质→碳青质
二.热破坏加工化学反应机理
关于烃类热反应,目前一般都认为遵循自由基反应机理。
根据此机理,可以解释许多烃类热反应的现象。
例如,正构烷烃热分解时,裂化气中含C1、C2低分子烃类较多;
反应很难生成异构烷和异构烯等现象。
1.自由基定义
自由基(freeradical),化学上也称为“游离基”,是含有一个不成对电子的原子团,如H·
、CH3·
、C8H17·
、C6H5·
等。
由于原子形成分子时,化学键中电子必须成对出现,因此自由基就到处夺取其他物质的一个电子,使自己形成稳定的物质。
2.自由基反应原理
1)自由基形成
大烃分子中的某个C—C键或C—H键的电子对发生均裂,生成两个都含有一个不成对电子的原子团,即自由基,如:
C16H34→2C8H17·
C6H5—C10H21→C6H5—C2H4·
+C8H17·
C6H6→C6H5·
+H·
2)自由基转移
形成的自由基不稳定,容易继续进行反应,从而生成新分子和新自由基,如:
C8H17·
→C4H8+C4H9·
C2H5·
→C2H4+H·
+C8H18→C2H6+C8H17·
H·
+C8H18→H2+C8H17·
3)自由基还原
反应结束后,所有自由基两两结合,生成新分子,最终反应产物中不含自由基,如:
+H·
→H2
+C2H5·
→C2H6
+CH3·
→C9H20
2C6H5·
→(C6H5)2
三.反应热与反应速度
1.反应热
烃类的热反应包括分解、脱氢等吸热反应以及叠合、缩合等放热反应。
由于分解反应占据主导地位,因此,烃类的热反应通常表现为吸热反应。
反应热的大小随原料油的性质、反应深度等因素的变化而变化,其范围在500~2000kJ/[kg(汽油+气体)]之间。
重质原料油比轻质原料油有较大的反应热,而在反应深度增大时则吸热效应降低。
2.反应速度
研究表明,在反应深度不太大时(例如小于20%),烃类热反应的反应速率服从一级反应的规律,其反应速率可用以下方程表示:
dx/dt=k(a-x)
式中a—单位反应容积内原始反应物的摩尔数;
x—在t秒种内反应了的摩尔数;
k—反应速率常数,s-1。
当裂化深度增大时,在温度一定的条件下k不再保持为常数,一般是k值随裂化深度的增大而下降。
这种现象的出现可能有两个原因,即未反应的原料与新鲜原料相比有较高的稳定性,其次是反应产物可能对反应有一定的阻滞作用。
因此热裂化反应不再服从一级反应的规律。
四.重油热反应特点
重油是由多种烃类和非烃类化合物构成的极为复杂的混合物,反应过程又涉及裂解和缩合等不同的反应类型,其组分的热反应行为自然遵循各类的热反应规律。
重油的热反应具有以下特点:
1.平行-顺序反应
重油热反应比单体烃更明显地表现出平行一顺序反应的特征。
图4.2.1和图4.2.2示出了这个特征。
由图4.2.1和图4.2.2可见,随着反应深度的增大,反应产物的分布也在变化;
作为中间产物的汽油和中间馏分油的产率,在反应进行到某个深度时会出现最大值;
而作为最终产物的气体和焦炭则在某个反应深度时开始产生,并随着反应深度的增大而单调地增大。
图4.2.1重油热反应平行-顺序反应特征
图4.2.2重油热反应产物发布与反应时间变化关系平
1-原料;
2-中间馏分;
3-汽油;
4-裂化气;
5-残油;
6-焦炭
2.易缩合生焦
重油,尤其渣油进行热反应时容易生焦,除了由于渣油自身含有较多的胶质和沥青质外,还因为不同族的烃类之间的相互作用促进了生焦反应。
芳香烃的热稳定性高,在单独进行反应时,不仅裂解反应速度低,而且生焦速度也低。
例如在450℃下进行热反应,欲生成1%的焦炭,烷烃(C25H52)要144min,十氢萘要1650min,而萘则需要670000min,但是如果将萘与烷烃或烯烃混合后进行热反应,则生焦速度显著提高。
含胶质甚多的原料油,如将它用不含胶质且对热很稳定的油品稀释,可以使生焦量减少。
五.延迟焦化反应原理
1.延迟焦化反应步骤
延迟焦化过程的反应机理复杂,无法定量地确定其所有的化学反应。
可以认为在延迟焦化过程中,重油热转化反应是分两步进行的:
1)原料加热
原料油在加热炉中很短时间内被加热至450~510℃,少部分原料油发生轻度的缓和热反应;
有部分原料气化和反应产生的油气。
2)焦化反应
从加热炉出来,已经部分反应和汽化的原料油进入焦炭塔。
根据焦炭塔内的工艺条件,塔内物流为气一液相混合物。
气液两相分别在塔内的温度、时间条件继续发生裂化、缩合反应,即:
①焦炭塔内油气在塔内主要进行继续裂化反应;
②焦炭塔内的液相重质烃在塔内持续发生裂化、缩合反应,直至生成烃类蒸气和焦炭为止。
2.焦炭的生成机理
焦化过程中,重油中的沥青质、胶质和芳烃分别按照以下两种反应机理生成焦炭:
①沥青质和胶质的胶体悬浮物,发生“歧变”形成交联结构的无定形焦炭。
这些化合物还发生一次反应的烷基断裂,这可以从原料的胶质-沥青质化合物与生成的焦炭在氢含量上有很大差别得到证实(胶质-沥青质的炭氢比为8~10,而焦炭的炭氢比为20~24)。
胶质-沥青质生成的焦炭具有无定形性质和杂质含量高,所以这种焦炭不适合制造高质量的电极焦。
②芳烃叠合和缩合,由芳烃叠合反应和缩合反应所生成的焦炭具有结晶的外观,交联很少,与由胶质-沥青质生成的焦炭不同。
使用高芳烃、低杂质的原料,例如热裂化焦油、催化裂化澄清油和含胶质-沥青质较少的直馏渣油所生成的焦炭,再经过焙烧、石墨化后就可得到优质电极焦。
第三节减粘裂化
减粘裂化是以常压重油或减压渣油为原料进行浅度热裂化反应的一种热加工过程。
主要目的是为了减小高粘度燃料油的粘度和倾点,改善其输送和燃烧性能。
在减粘的同时也生产一些其它产品,主要有气体、石脑油、瓦斯油和减粘渣油。
现代减粘裂化也有一些其它目的,如生产裂化原料油,把渣油转化为馏分油用作催化裂化装置的原料。
一.原料和产品
1.原料油
常用的减粘裂化原料油有常压重油、减压渣油和脱沥青油。
原料油的组成和性质对减粘裂化过程操作和产品分布与质量都有影响,主要影响指标有原料的沥青质含量、残炭值、特性因数、粘度、硫含量、氮含量及金属含量等。
2.产品
表4.3.1列出普通减粘裂化过程的产品收率。
表4.3.1普通减粘裂化过程的产品收率
原料油
胜利管输减渣
胜利-辽河混合油减渣
大庆减渣
反应温度/℃
反应时间/min
380
180
430
27
420
57
产物收率/%
裂化气
C5~200℃
200~350℃
〉350℃
1.0
98
1.4
3.5
4.1
91.0
1.3
2.0
2.5
93.6
原料渣油粘度(100℃)/(mm2/s)
减粘渣油粘度(100℃)/(mm2/s)
103
38.7
578
70.7
121
55.4
由表4.3.1数据可见,减粘裂化轻质油转化率低,对于我国减压渣油经普通减粘过程后,其低于350℃生成油及裂化气的产率不到10%,350℃的产率在90%以上。
但减粘渣油的粘度
较原料渣油相比明显降低。
减粘裂化气体产率较低,约为2%左右,一般不再分出液化气(LPG),经过脱除H2S后
送至燃料气系统。
表4.3.2列出胜利减压渣油裂化气体产品组成。
表4.3.2胜利减压渣油裂化气体产品组成
H2S
H2
CH4
C2H4
C2H6
C3H6
C3H8
C4H8
C4H10
%
8.46
0.35
18.0
1.07
11.95
5.20
14.32
6.35
10.48
由4.3.2可见,减粘裂化气体中烯烃含量较高。
减粘石脑油组分的烯烃含量较高,安定性差,辛烷值约为80,经过脱硫后可直接用作汽油调合组分;
重石脑油组分经过加氢处理脱除硫及烯烃后,可作催化重整原料;
也可将全部减粘石脑油送至催化裂化装置,经过再加工后可以改善稳定性,然后再脱硫醇。
减粘柴油含有烯烃和双烯烃,故颜色安定性差,需加氢处理才能用作柴油调和组分。
减粘重瓦斯油性质主要与原料油性质有关。
介于直馏VGO和焦化重瓦斯油的性质之间,
其芳烃含量一般比直馏VGO高。
减粘渣油可直接作为重燃料油组分,也可通过减压闪蒸拔出重瓦斯油作为催化裂化原料。
二.工艺流程
根据工艺目的和对产品要求的不同,减粘裂化有不同的工艺过程。
以生产燃料油为目的的常规减粘裂化工艺原理流程见图4.3.1。
图4.3.1减粘裂化工艺原理流程
减粘原料油为常压重油或减压渣油,在减粘加热炉管中加热至反应温度。
然后在反应段炉管中裂化,达到需要的转化深度。
为了避免炉管内结焦,向内注入约1%的水。
加热炉出口温度为400~450℃。
在炉出口处可注入急冷油使温度降低而中止反应,以避免后路结焦。
加热炉出料进入减粘分馏塔的闪蒸段,分离出裂化气、汽油和柴油,柴油的一部分可作急冷油用。
从塔底抽出减粘渣油。
此种过程也称为管式炉减粘。
以生产裂化装置的原料为生产目的时,采用带减压闪蒸塔的减粘裂化流程。
此流程基本与常规流程相同,只不过在粘减分馏塔后增加一个减压塔,减粘分馏塔底的重油进入减压塔,在减压塔内分离出减粘瓦斯油和减粘燃料油。
减粘瓦斯油直接进入其他转化装置作原料。
以生产轻馏分油或需要降低燃料油的倾点为生产目的时,采用减粘裂化一热裂化联合流程。
此流程在带减压闪蒸塔的减粘裂化流程基础上,增加一个热裂化加热炉,将减压瓦斯油直接进入热裂化加热炉,使其裂化为轻质产品。
热裂化加热炉的出料与减粘裂化产品一起进入分馏塔进行分馏。
在工业上,根据减粘裂化采用设备的不同,还有炉式减粘裂化和塔式减粘裂化之分。
炉式减粘裂化是指转化过程在加热炉的反应炉管中进行的。
炉式减粘裂化的特点是温度高、停留时间短;
塔式减粘裂化是在流程中设有反应塔。
虽然在加热炉管内有一定的裂化反应,但大部分裂化反应是在反应塔内进行。
反应塔是上流式塔式设备,内没几块筛板。
为了减少轴向返混,筛板的开孔率自下而中逐渐增加。
与炉式减粘裂化相比,塔式减粘反应温度低、停留时间长。
其流程见图4.3.2。
图4.3.2反应塔减粘裂化工艺流程图
三.影响减粘裂化因素
石油重质组分的热破坏反应过程,是一个复杂的平行-顺序反应过程。
原料组成、反应深度、反应条件对最终产品分布影响较大。
影响减粘裂化产品分布与质量