挤压工艺课后答案Word文档格式.docx
《挤压工艺课后答案Word文档格式.docx》由会员分享,可在线阅读,更多相关《挤压工艺课后答案Word文档格式.docx(6页珍藏版)》请在冰豆网上搜索。
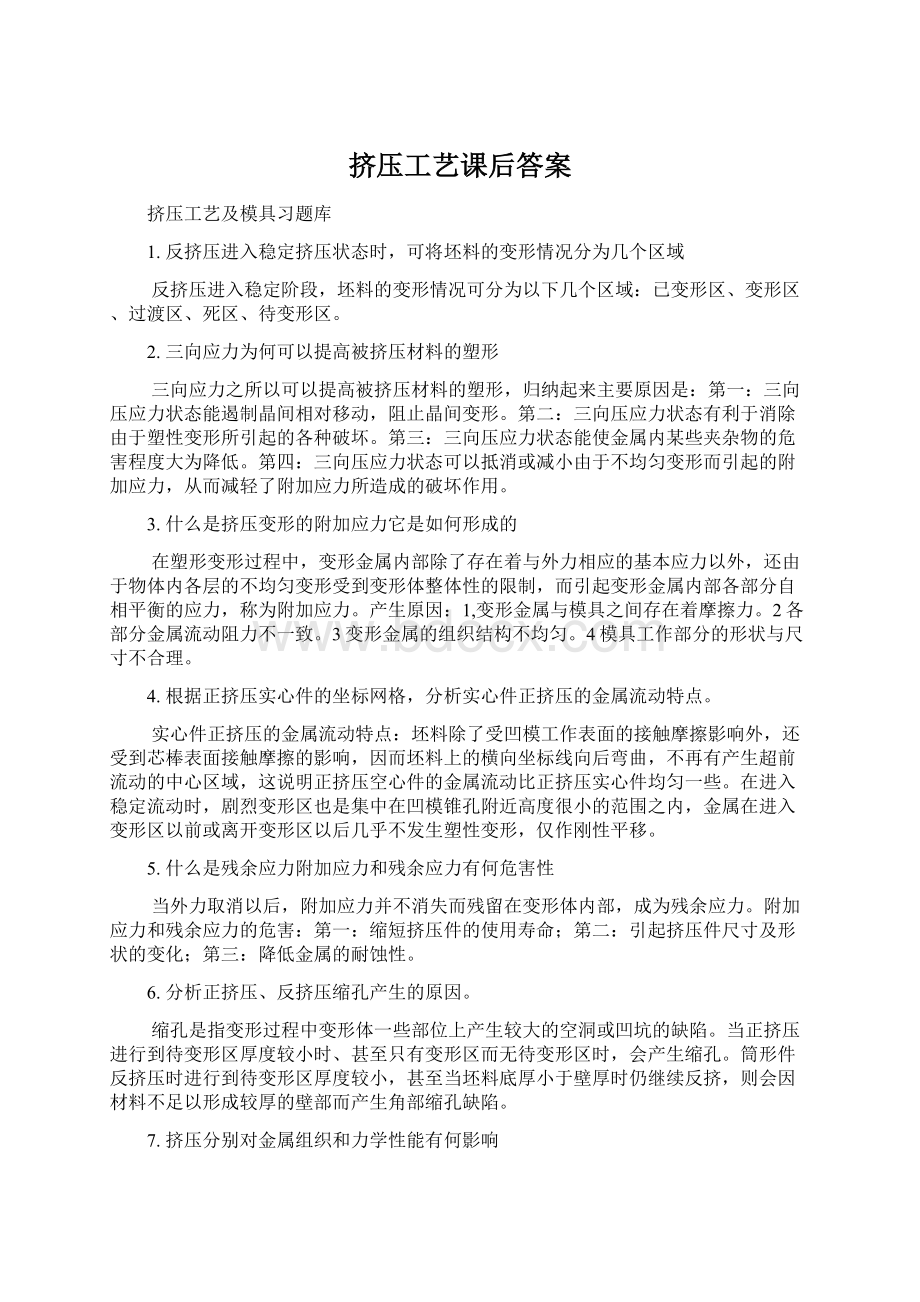
3变形金属的组织结构不均匀。
4模具工作部分的形状与尺寸不合理。
4.根据正挤压实心件的坐标网格,分析实心件正挤压的金属流动特点。
实心件正挤压的金属流动特点:
坯料除了受凹模工作表面的接触摩擦影响外,还受到芯棒表面接触摩擦的影响,因而坯料上的横向坐标线向后弯曲,不再有产生超前流动的中心区域,这说明正挤压空心件的金属流动比正挤压实心件均匀一些。
在进入稳定流动时,剧烈变形区也是集中在凹模锥孔附近高度很小的范围之内,金属在进入变形区以前或离开变形区以后几乎不发生塑性变形,仅作刚性平移。
5.什么是残余应力附加应力和残余应力有何危害性
当外力取消以后,附加应力并不消失而残留在变形体内部,成为残余应力。
附加应力和残余应力的危害:
缩短挤压件的使用寿命;
引起挤压件尺寸及形状的变化;
降低金属的耐蚀性。
6.分析正挤压、反挤压缩孔产生的原因。
缩孔是指变形过程中变形体一些部位上产生较大的空洞或凹坑的缺陷。
当正挤压进行到待变形区厚度较小时、甚至只有变形区而无待变形区时,会产生缩孔。
筒形件反挤压时进行到待变形区厚度较小,甚至当坯料底厚小于壁厚时仍继续反挤,则会因材料不足以形成较厚的壁部而产生角部缩孔缺陷。
7.挤压分别对金属组织和力学性能有何影响
挤压对金属组织和力学性能的影响有:
挤压时,在强烈的三向应力作用下金属晶粒被破碎,原来较大的晶粒挤压后变成为等轴细晶粒组织,因而提高了强度。
8.冷挤压常用原材料的形态有哪有种各使用在哪些场合
冷挤压时常用材料的形态有:
线材、棒材、管料、板料等。
线材主要用于镦挤螺栓之类标准件。
棒材一般用于单工序的挤压设置
管料为无缝钢管或热挤铝管,铜管等。
板料当坯料的长径比较小,或者在挤压有色金属零件外形为非圆形时。
9.冷挤压坯料为何要进行软化处理
冷挤压坯料进行软化处理的原因:
为了改善冷挤压坯料的挤压性能和提高模具的使用寿命,大部分材料在挤压前和多道挤压工序之间必须进行软化处理,以降低材料的硬度,提高材料的塑形,得到良好的显微组织,消除内应力。
10.碳钢和合金钢坯料冷挤压前采用何种表面处理这种表面处理为何能提高冷挤压零件的表面质量和模具使用寿命
碳钢和合金钢坯料冷挤压前要进行磷化处理。
磷化处理又叫磷酸盐处理,也就是把钢坯放在磷酸盐溶液中进行处理。
处理时金属表面发生溶解和腐蚀。
由于化学反应的结果,在金属表面上形成一层很薄的磷酸盐覆盖层。
可减少坯料与模具之间的接触摩擦,降低单位挤压力,提高冷挤压件的表面质量和模具使用寿命。
11.奥氏体不锈钢和硬铝坯料在冷挤压前要进行何种表面处理
奥氏体不锈钢因与磷酸盐基本上不发生化学反应,所以不能用磷化处理,故用草酸盐处理来代替。
硬铝坯料苏醒差,在挤压过程中,为了避免产生裂纹,应使硬铝坯料表面形成一层氧化膜。
可用氧化处理、磷化处理或氟硅化处理来获得。
12.计算冷挤压力有何意义与作用
冷挤压力即冷挤压变形前所需要的作用力。
它是设计模具、选择设备的依据,并可衡量冷挤压变形前的难易程度。
13.影响单位冷挤压力的主要因素有哪些影响情况如何
影响冷挤压力的因素主要有:
冷挤压用材料、变形程度、变形温度、变形速度、毛坯的几何形状、变形方式、润滑条件及模具结构等因素的影响。
14.冷挤压工艺对压力机的特殊要求有哪些选择冷挤压设备的原则是什么
冷挤压时单位挤压力很大,对挤压件的精度要求高,因此对冷挤压使用的压力机提出了一些特殊要求:
能量要大;
刚性要好;
导向精度要求高;
要具备顶出机构;
第五:
要有过载保护装置;
第六:
能提供合适的挤压速度;
第七:
要对模具进行润滑冷却的装置。
求出所需的挤压力后,仅此为依据去选择机械压力机的标称压力是不够的,还必须把冷挤压工艺示功图与压力机许用负荷图画在一起。
15.冷挤压模具有哪些特点
冷挤压模具应具有以下特点:
模具应有足够的强度和刚度,要在冷热交变应力下正常工作;
模具工作部分零件材料应具有高强度、高硬度、高耐磨性,并有一定的韧性;
凸、凹模几何形状应合理;
模具易损坏部分应更换方便;
为提高工作部分强度,凹模一般采用预应力组合形式,凸模有时也采用组合形式;
模具工作部分零件与上下模板之间要设置厚实的淬硬压力垫板;
上下模板采用中碳钢经锻造或直接用钢板制成,应有足够的厚度,以保证模板具有较高的强度和刚度。
16.为何要采用预应力组合凹模其有什么优点
为了提高冷挤压凹模的强度,确保凹模在较大的单位挤压力下有较长的使用寿命,一般采用预应力组合凹模结构形式。
17.组合凹模的压合工艺有哪几种
组合凹模的压合工艺主要有以下三种:
热压配合法;
冷压配合法;
常温强力压合法。
18.对冷挤压模工作零件有哪些要求工作零件常用的材料有哪些
对冷挤压工作零件材料的要求有:
必须具有高强度和高硬度;
应具有相当高的韧性,可以避免由于冲击、偏心载荷,疲劳应力集中而引起的折断和开裂破坏;
应具有较高的耐磨性;
具有足够的耐热性能;
材料必须有良好的加工性能。
常用的材料有:
碳素工具钢,高合金工具钢,高速工具钢,硬质合金,钢结硬质合金。
19.热挤压时钢的加热缺陷有哪些有什么危害应该怎样防止
热挤压时钢的加热缺陷有:
氧化、脱碳、过热、过烧、开裂等。
氧化皮大大降低了挤压件的表面质量,增加了模具的磨损;
当钢中含有钨、铝、钛、硼等合金元素时,特别容易引起脱碳;
对于过热不太严重的钢,通过大变形量的锻造可以得到改善;
坯料一旦过烧,锻造时一击便碎,工件只能报废;
高合金钢的导热性能差,开裂倾向也大,必须缓慢加热,严防开裂。
20.简述感应加热的基本原理。
为什么说加热不同直径的棒料要选用不同频率的感应加热炉
感应加热是交变电流通过感应线圈产生感应交变磁场,进而感应出交变电场。
将金属坯料置于电场中,因其导电而产生感应电动势,形成闭合回路,在棒料(坯料)内产生感应电流而达到加热的目的。
21.热挤压时为什么要制定冷挤压件图和热挤压件图有何区别各自的作用如何
冷挤压件图是在零件图基础上加上了机械加工余量、成形公差和工艺余料等而绘制的,主要勇于最终挤压件的检验、后续机械加工工艺的编制和工夹具的设计等。
热挤压件图则是在冷挤压件图的基础上加上收缩量,主要用于挤压模具的设计与制造、挤压过程的质量控制等
22.为什么说模具的冷却和润滑是温挤压成败的关键因素
温挤压模具在连续生产过程中温度迅速上升,当模具的温度达到其回火软化温度时,在很高的挤压应力的作用下会发生变形,表面硬度下降,使模具迅速失效。
因此,必须对模具进行充分的冷却,使其维持在200摄氏度左右,保证其性能的发挥;
在挤压温度在250摄氏度以上时,采用冷挤压时的润滑方法,会使磷化层和皂化剂烧损,使润滑条件恶化,因此,在温挤压时,润滑剂的选取很重要,是温挤压成败的关键因素
23.过共析钢的温挤压温度如何确定成形温度超过了相变温度对最终热处理有何影响
如果零件最终热处理前对组织状态有要求时,特别是要求过共析钢为球状珠光体时,则要求其温挤压温度在相变温度前。
当原球状珠光体经相变为奥氏体组织,再经挤压后冷却为片状珠光体组织的温挤压件,不仅不利于切削加工,而且经最终热处理淬火后的马氏体组织粗大,容易产生淬火变形,影响零件的力学性能。
因此,其挤压后的组织应为球状珠光体。
24.温挤压对润滑剂有什么要求常用润滑剂的种类、特点和使用方法如何
温挤压对润滑剂的要求:
对摩擦表面具有最大活性和足够的粘度,不易流失,较好地粘附摩擦表面;
润滑剂应具有一定的热稳定、耐热性和绝热性;
润滑剂的化学稳定性要高;
在温挤压温度下能均匀地粘附在坯料表面或模具表面上,形成均匀的润滑膜;
具有良好的悬浮分散和可喷涂性能。
25.与冷、热挤压相比,温挤压模具结构有什么特点
与冷热挤压相比,温挤压模具的结构特点:
具有抗室温及中温破坏的足够的硬度、强度与韧性;
在反复变形力与热的作用下,必须具有高的抗磨损、耐疲劳性能;
模具工作部分易损零件应装拆方便,固定可靠;
在模具上应设计循环冷却系统,使凸膜、凹模等模具工作零件充分冷却;
所选用的模具材料应具有良好的加工性能。
26.铝合金型材按断面可分为实心型材和空心型材,所采用的挤压方法分别有哪些
挤压实心型材采用两种基本方法,即金属正向流动的挤压、金属反向流动的挤压;
空心型材的挤压可采用两种基本的方法,即挤压针管材挤压法、组合模焊合挤压。
27.如何确定铝型材挤压工艺的工艺参数
定工艺参数时,应综合考察金属与合金加工时的可挤压性和对制品质量的要求(尺寸与形状的允许偏差,表面质量,组织与性能等),以满足提高成品率与生产率的需要。
28.铝型材挤压工艺毛坯尺寸如何确定
选择铸坯直径时,应在满足制品断面力学性能要求和均匀性要求的前提下尽可能采用较小的挤压比。
但是,在挤压外接圆大的复杂形状断面型材时,要考虑模孔轮廓不能太靠近挤压筒壁,以免制品出现分层缺陷。
挤压管、棒、型、线材的锭坯一般为实心圆锭坯,但在生产有些特殊要求的管材时最好使用空心铸坯,包括锭坯直径计算和锭坯长度计算。
29.挤压模按模孔的断面形状分成哪些按模具结构又分成哪些
流线形模和双锥模等。
按模具结构可分为整体模、分瓣模、可卸模、活动模、舌型组合模、平面分流组合模、嵌合模、叉架模、前置模、保护模等。
30.在实心型材模的设计中减少金属流动不均匀的措施有哪些
在实心型材模的设计中减少金属流动不均匀的措施有第一:
采用不等长的工作带;
采用阻碍角或促流角;
采用平衡模孔;
考虑模孔的配置、模孔制造尺寸的确定和选择,保证型材断面各个部分的流动速度均匀,并且要选择有足够强度的模具结构。
31.在热挤压多孔实心型材模的设计中,模孔的排列应注意什么
在布置多孔模的模孔时,不仅需要考虑型材断面各部分流动的均匀性,有时还需要考虑模子的强度问题。
为了保证模具的强度,多孔模各个模孔之间的距离应当合适,不能过小。
在实际生产中模孔之间的间距大体在15-50mm范围内,对于以下的挤压机取20-30mm;
49MN左右的挤压机取35-50mm;
对于以上的大型挤压机,可取60mm以上。
同时,模孔间距应系列化,以便模垫可互相交换使用。
32.实心型材挤压模如何设计(即模孔位置、模孔尺寸、工作带、空刀应如何确定)
实心型材挤压模具设计时要考虑模孔的合理布置、模孔几何尺寸的确定、减少金属流动不均匀性的措施、型材模子的强度校核等。
33.舌形模的特点、结构类型及用途分别是什么
舌形模又称桥式模,在空心铝合金型材的挤压生产中,舌形模是应用最早的一种,与其他组合模相比,舌形模具有最小的挤压力,型材各个部分金属流动均匀,可以采用较高的挤压速度等一系列优点,因此舌形模在硬铝合金空心型材的挤压生产中应用得比较普遍。
舌形模的主要缺点是挤压压余大,强度较差,且制造加工困难。
舌形模的结构类型有四种结构形式:
突出桥式,半突出桥式,埋入桥式,平面桥式。
34.舌形模的结构要素设计包括哪些内容
舌形模的设计结构要素比较复杂,常对其主要结构要素进行分析。
主要包括:
模桥、焊合室、模芯(舌头)、模孔工作带。
35.平面分流模的工作原理及特点是什么
平面分流模一般由上模和下模组合而成。
平面分流模挤压型材的特点:
可适于用舌形模很难生产,甚至无法生产的双孔、多孔或内腔复杂的空心型材;
可以生产悬臂梁较大、用平模很难生产的半空心型材的挤压;
可以生产断面形状复杂、壁厚相差大或多齿的实心型材;
平面分流模较舌形模容易加工,挤压残料较舌形模的短且分离残料容易。
36.如何设计平面分流模的分流孔、模桥、模芯、焊合室、模孔尺寸、空刀
分流孔个数的选择要根据制品外形尺寸、断面形状和模孔排列位置来确定,一般有二孔、三孔、四孔和多孔。
分流孔的形状要根据制品的外形来确定,一般有圆形、扁椭形、腰子形、扇形和异形;
模芯又称舌头,根据模芯工作带部分的结构不同,模芯可以分为凸台式、锥台式、锥式三种基本结构形式;
焊合室常见的有圆形和蝶形两种;
平面分流模的孔空刀结构一般说来,当型材壁厚t>
2mm时,可采用加工容易的真空刀和斜空刀结构;
当t<
2或带有悬臂处可用组合空刀结构;
对于危险断面处(如带有小燕尾槽的型材等)可用两种空刀结构。
37.试制定建筑铝合金型材的平模、平面分流模的机械加工工艺规程。
型材挤压工艺,包括确定挤压工艺参数、选择合适的润滑条件、挤压比的确定及合理锭坯尺寸的计算,它们与合金种类、制品规格和设备能力有关。
38.型材热挤压模为何要进行热处理
挤压是铝合金型材成形加工中的主要工序,其它工序及其连续性取决于型材的供应状态,而供应状态又首先取决于用户所提出的要求。
不同的热处理所得到的型材状态不同
39.型材挤压模为什么要进行渗氮处理
型材挤压模进行渗氮处理,主要目的是通过渗氮使模具表面改变性能,提高模具的硬度和防腐蚀性。
40.热挤压型材模具应具备哪些性能条件
热挤压型材模具应具备的性能条件有:
高的强度和硬度;
高导热性和稳定性;
第三:
搞的耐蚀性;
良好的淬透性;
抗激冷、激热的适应能力;
良好的工艺性能。