连铸技术总结.docx
《连铸技术总结.docx》由会员分享,可在线阅读,更多相关《连铸技术总结.docx(10页珍藏版)》请在冰豆网上搜索。
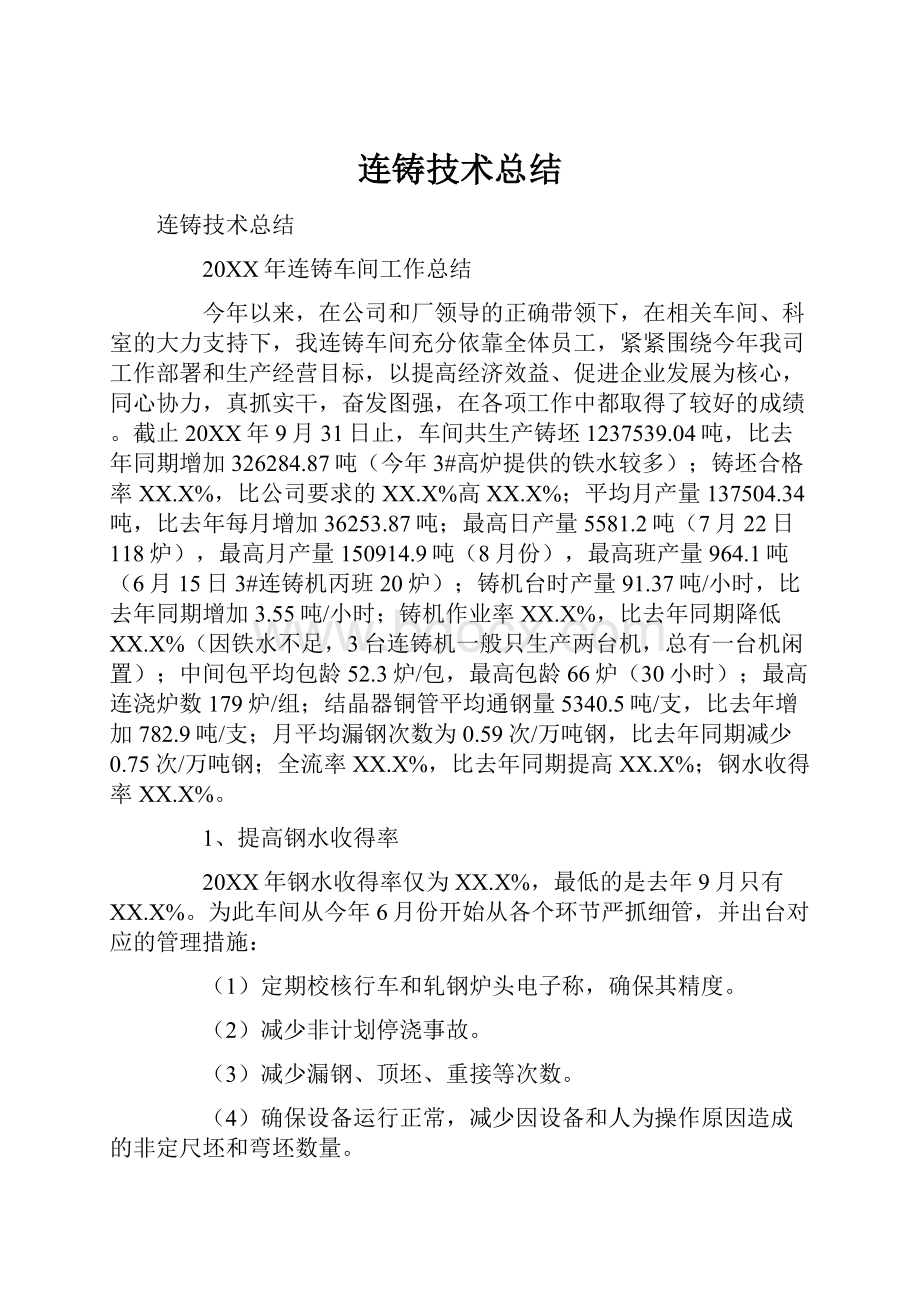
连铸技术总结
连铸技术总结
20XX年连铸车间工作总结
今年以来,在公司和厂领导的正确带领下,在相关车间、科室的大力支持下,我连铸车间充分依靠全体员工,紧紧围绕今年我司工作部署和生产经营目标,以提高经济效益、促进企业发展为核心,同心协力,真抓实干,奋发图强,在各项工作中都取得了较好的成绩。
截止20XX年9月31日止,车间共生产铸坯1237539.04吨,比去年同期增加326284.87吨(今年3#高炉提供的铁水较多);铸坯合格率XX.X%,比公司要求的XX.X%高XX.X%;平均月产量137504.34吨,比去年每月增加36253.87吨;最高日产量5581.2吨(7月22日118炉),最高月产量150914.9吨(8月份),最高班产量964.1吨(6月15日3#连铸机丙班20炉);铸机台时产量91.37吨/小时,比去年同期增加3.55吨/小时;铸机作业率XX.X%,比去年同期降低XX.X%(因铁水不足,3台连铸机一般只生产两台机,总有一台机闲置);中间包平均包龄52.3炉/包,最高包龄66炉(30小时);最高连浇炉数179炉/组;结晶器铜管平均通钢量5340.5吨/支,比去年增加782.9吨/支;月平均漏钢次数为0.59次/万吨钢,比去年同期减少0.75次/万吨钢;全流率XX.X%,比去年同期提高XX.X%;钢水收得率XX.X%。
1、提高钢水收得率
20XX年钢水收得率仅为XX.X%,最低的是去年9月只有XX.X%。
为此车间从今年6月份开始从各个环节严抓细管,并出台对应的管理措施:
(1)定期校核行车和轧钢炉头电子称,确保其精度。
(2)减少非计划停浇事故。
(3)减少漏钢、顶坯、重接等次数。
(4)确保设备运行正常,减少因设备和人为操作原因造成的非定尺坯和弯坯数量。
(5)提高大包工在浇注末期分清钢水和红渣的能力,把钢水浇完。
(6)控制好切头和尾坯的尺寸,并减少废品。
(7)制订对标挖潜奖励措施,奖好罚差,提高职工积极性。
实施后效果:
截止9月底,月平均收得率为XX.X%,其中6月、7月、8月、9月收得率分别为XX.X%、XX.X%、XX.X%、XX.X%,连续4个月都大于XX.X%以上。
2、提高拉速
(1)6月15日起,我车间在3#机开始做提高拉速试验,单流最大拉速3.0m/min,正常最大总拉速可维持在10.8m/min。
(2)6月25日起,我车间在1#机开始做提高拉速试验,单流最大拉速2.5m/min。
加高的好处是:
①随着钢液面高度增加,钢水中的夹杂物有更多的时间上浮,钢水更干净;②能储存更多的钢水;③可以提高拉速,在同样的时间内产量更高,节约耐材,降低吨钢成本!
3、降低万吨钢漏钢次数。
攻关前状况:
去年同期车间万吨钢漏钢次数为1.34次,漏钢次数与三钢相比仍有差距,为此车间制订了攻关目标:
力争全年万吨钢漏钢次数≤1次。
为了攻关该项目,车间和其它科室共8人用了9个
月时间做了大量工作:
(1)制订合理的温度制度,钢水正点率控制在3~8分钟,并确保合适的中包钢水温度:
1515~1535℃(HRB系列);1530~1545℃(HPB235);杜绝高温钢上台。
(2)3台机全程跟踪设备安装精度,引锭杆对弧精确到0.5mm以下;流间距和外弧基准线偏差小于1mm以下。
(3)严格执行标准化操作规程,各岗位实行规范化操作。
(4)跟踪记录保护渣使用效果,根据现场生产实际情况选用性能良好的保护渣,保证足够的液渣层厚度和合适的融化温度,减少因保护渣润滑不良造成的漏钢事故。
攻关后状况:
截止到今年9月份共有8个月万吨钢漏钢次数少于1次,最少的为0.27次(1月份)。
每万吨钢1#机漏钢次数为0.43次,2#机为1次,3#机为0.34次,车间平均为0.59次,比去年同期减少0.75次。
由于漏钢次数的明显减少,连铸全流率达到XX.X%,设备损耗减少,钢坯质量上了一个台阶,同时可以加快生产节奏。
4、减少废品,提高钢坯合格率。
实施前:
去年分别对1#机和2#机进行了技术改造,把原来的6米弧改为7米弧、铸坯断面由150mm×150mm改为160mm×160mm,对于新的断面和新的铸机弧度本车间都是没有接触过的,属于新课题,为此不得不重新为其制订新的技术操作规程和合理的连铸工艺制度(温度制度、拉速制度、配水制度),在摸索过程中断断续续有零星废品出现,尤其是9月中、下旬2#机在生产HPB235钢种时出现批量废品,废品达到109.19吨。
针对这种情况我们今年主要采取了以下措施:
(1)调整二冷室各段喷嘴型号;调整二冷水比水量和各段比例,1#机、3#机零段增加一排角喷,效果比较好;2#机正试用新喷嘴(喷淋
角度由65°增大到70°),目前仍在跟踪当中。
(2)钢液面高度增加到400mm以上,钢水中的夹杂物有更多的时间上浮,钢水更干净。
(3)稳定中间包钢水过热度。
(4)利用购买的测振仪测量各流振动台数据,有异常的及时处理和调整(主要是更换偏心轮);振幅统一为±5mm,2#机振动频率为80V,1#机思想汇报专题、3#机均为75V。
(5)加大对二冷室的管理力度。
每次停浇后及时检查二冷设备并试水,杜绝掉喷嘴现象和确保喷淋管对中良好。
对相关人员奖勤罚懒。
跟踪各个结晶器(包含铜管)的使用情况。
(6)浇钢过程实行全程保护浇注,并延长大包长水口工作时间,减少钢水二次氧化。
(7)技术员对每一组HPB235钢各流取小块样观察铸坯内部质量情况,发现异常及时处理,并定期取样做低倍和金相实验。
(8)更换浸入式水口实行标准化操作;P4岗位对钢坯实行巡检制度,有异常的铸坯则挑出、割除。
实施后效果:
今年1~9月份连铸废品总量为592.1吨,比去年减少150吨。
2#机在生产HPB235钢种时出现大批量废品的情况已经很少,基本能满足轧钢生产的要求。
截止到今年9月底,铸坯合格率为XX.X%,比公司要求的XX.X%高出XX.X%,其中3、5、6、7、8、9月合格率均大于XX.X%,9月份更是达到了XX.X%。
5、提高钢包自开率。
去年10月中旬率先在2#机安装和试用马鞍山博威公司的钢包液压机构,并取得成功。
今年2月底推广应用到1#机和3#机,自开率达到XX.X%,比去年同期提高XX.X%。
6、新品种试生产
(1)2月20日起,2#机进行新钢种HPB300试生产,共计生产3053.7吨,全部符合公司标准。
(2)3月30日,进行新钢种HRB500E试生产10炉,共计生产449.2吨,全部符合公司标准
7、增加结晶器铜管的通钢量。
今年车间继续使用首钢长白和齐齐哈尔厂家的结晶器铜管。
在使用过程中跟踪铜管的磨损、刮伤情况,上、下线时测量锥度、水缝。
我们还依据工艺数据科学制订了《各厂家铜管下线炉数规定》,使得铜管的平均通钢量为5340.5吨/支,比去年增加782.9吨/支,节约铜管36支,节省XX.X万元。
8、员工培训工作。
我车间一贯重视对员工的培训工作。
今年投入使用钢包液压新设备,为此我车间邀请厂家技术员和设备科、技术科等对车间XXX名工人进行理论培训和现场实际操作,并指定师傅带徒弟,通过传、帮、带的方式让新工人尽早熟悉本岗位的操作。
9、强化安全管理,把安全工作落到实处。
安全工作重于泰山,安全工作一向是我车间工作的重中之重。
今年向各班组提供了看火镜500副、平光眼镜40副、手电筒60把和防护透明面罩若干,维护好中间包烘烤器旁边和操作室共XXX个煤气报警器。
这些物品、设备的投入使用不仅提高了员工的个人防护能力,也为减少安全事故起到了积极的作用。
与此同时,我车间完善了《各岗位安全操作规程》,出台了《安全生产考核规定》、《劳保用品穿戴标准》和《各种突发事件应急预案》,并且成立安全联合检查小组,每个月不定期进行不少于3次的安全检查,发现安全隐患马上整改。
由于我们制度到位,责任落实到位,检查工作到位,从而保证了我车间的各项工作都能安全的开展。
截止到今年9月底我车间未发生过重
篇二:
连铸工段20XX年工作总结
炼钢厂连铸工段20XX年工作总结
20XX年连铸工段在厂部领导的大力支持下,本着“抓安全,促生产,强管理”的基本原则,群策群力,从严从细努力完成了全年的各项工作。
现将工作情况做如下总结:
一.抓好安全生产严防工伤事故
全年来,我工段坚持:
“安全第一,预防为主”的管理理念,始终把安全工作放在各项工作的首位,积极开展“安全生产”活动,层层落实责任,全方位开展隐患排查与整改。
各班组坚持进行经常性安全教育,并加大违章违纪的安全事故考核力度,杜绝重大伤亡事故发生。
八九月工段根据厂部安排,利用停产时间,对新老员工进行安全作业培训。
制定安全,工艺操作规程,让员工切忌,熟背并进行相关岗位考试,以增强员工对实践知识的掌握和突发事故的应急处理能力。
工段全年开展安全教育会议48次,安全培训4次,培训人员XXX个,重大安全事故零起。
二.加大生产力度提高产品质量
一年来,各项生产治理制度的细化,推进了生产强度,在“时间就是效益”的理念影响下,设备作业率不断提高,促进了产能的快速发挥,连铸机的作业率大幅度提高。
最高日产钢坯2100吨,钢坯收得率XX.X%,钢坯全年产量达到37533.23吨。
通过对中包的改造并投入使用,连铸拉炉数不断提高,最高达到48炉/次,连拉时间达到
XXX个小时/次。
经改造中包生产出的钢坯,其夹杂物明显比板包减少了很多。
在质量上,加强技术控制,每天点评,每周汇总,每月攻关,对
比目标,推进标准化作业,把岗薪与质量指标挂钩,形成有效的质量治理体系。
针对钢坯表面横裂纹和内部质量缺陷,积极采取措施。
上半年在各班组生产中钢坯脱方较多,针对这质量缺陷,工段调整操作要求,各班拉钢要做到:
温度合理,拉速均衡,稳定液面,减少波动。
严抓这一环节后,下半年钢坯脱方问题得以改善,质量得以大幅度提高。
三.加强管理严格考核
连铸工段的管理主要是人和设备的管理。
在人管理上提高班组长
的带班管理水平和提高岗位工的技术水平。
对于班组长,工段基本做到用人得当,奖罚分明,关心爱护,大胆使用。
注意引导他们就产量,质量上杜绝溢钢,漏钢事故。
和去年相比,工段全年漏钢84次,比
去年减少了了XX%。
而水口班责任心不强,导致大包机构渗钢2次。
工段开展了班与班之间的相互竞争,形成了积极良好的局面。
尤其是公司每年举办的岗位能手评比,我工段又有两名员工符合评比条件。
一是拉钢老员工黄旭义,工作积极主动.认真勤恳,20XX年突破个人全年拉钢1550炉,全年无漏钢,技术比武名列前茅的好成绩。
二是丙班机长韦健,在他带领下,丙班全年完成了产量第一,质量第二的好成绩。
设备是连铸生产和质量的保障。
在生产组织和日常管理中,除了
完成各班的产量外,也加强了设备的维护和保养。
工段明确员工检修和维护职责,要求设备“台台有人管,人人有职责”,并推行操作人员对简单问题的自主维修。
四.全力做好环保工作。
在抓好安全生产的同时,我工段积极落实厂部指令,全力做好环保工作,连铸是高温,高危,粉尘作业,工段狠抓作业岗位卫生,并定期对绿化带进行分班护理。
五.存在问题与改进措施
1.在实践工作中,安全形势依然严峻,今年工段发生5起轻伤事故,说明我们的安全管理还存在漏洞,部分员工还有麻痹松懈思想,这就要求我们必须采取更有利的措施,千方百计保证生产。
2.生产上由于设备老化,给生产带来一定障碍。
上半年的钢坯脱方问题也反映了连铸机辊道设备上没有定期测量校正,引锭没定时调正对中。
因而设备点检定修方面还要不断完善,班组生产组织上需要进一步加强。
3.20XX年工段人员浮动变化大,新员工较多,,只懂得简单的岗位操作,没具备工作质量意识,影响工作效率。
工段要加强在岗员工的技术培训,进一步提高员工的业务素质和操作水平。
20XX年1月4日
连铸工段
篇三:
连铸车间技术总结09.10
连铸车间20XX.10月份技术总结
一、指标及重点技术数据情况
铸坯表面一次合格率:
一号机为XX.X%;ASP:
XX.X%;四号机为XX.X%;
大纵裂:
大纵裂有272.035吨,裂纹总量为1865.326吨,占裂纹数量的XX.X%,中厚板线共生产167666吨,大纵裂裂纹率为XX.X%;保护渣单耗:
亚泰J2渣,0.46kg/吨;武钢中碳渣,0.42kg/吨;日本大中渣,0.41kg/吨;亚泰X70-N4,0.43kg/吨;西峡中碳渣,0.43kg/吨;亚泰666M-4H,0.44kg/吨;亚泰666M-2SH,0.45kg/吨;亚泰616D60,0.41kg/吨;
漏钢率:
一号机为0,二号机为XX.X%,三号机为0,四号机为0;浸入式水口寿命:
一号机为8.8炉,二号机为5.9炉,三号机为5.6炉,四号机为7.2炉;
各班组分铸机呕钢次数统计:
切割定尺合格率,长短尺比例统计
长尺率:
XX.X%,短尺率:
XX.X%,定尺合格率:
XX.X%
二、对指标完成情况做技术分析
1.本月2#机漏钢分析:
10月12日丁班夜班,2号机拉CAS直上Q235B-R2。
中包第8炉炉号9505709,氩前1620,氩后1585,处理26分钟后吊至3号精炼补成分,1:
44上机。
本炉计划换水口。
1:
49分大包开浇,2:
05分中包温度1552,拉速降至0.8换水口。
换水口后,热电偶波动异常,频繁报警。
2:
10-2:
11,外弧偶头报警两次,自动爬行。
2:
14,内弧偶头报警,自动爬行。
2:
18,内弧大部分偶头波动异常,手动爬行。
2:
22分,拉速1.6m/min,内弧偶头再度异常,试坯壳有粘结迹象,收流观察坯壳。
2:
23漏钢。
2:
25通知电工、钳工、调度。
2:
45吊出结晶器、弯曲段。
3:
48坐入新弯曲段。
4点32坐入新结晶器。
5:
20具备拉钢条件。
确认无计划后,6点模拟。
事故原因:
处理粘结漏钢报警报警过程中,塞棒收流过快,导致结晶器液面下降到水口侧孔以下,接头粘结不牢强度不足,导致接头
漏钢。
2.大纵裂分析
从裂纹台帐统计共产生铸坯表面纵裂64支,分析裂纹情况,中包第一炉,出现18支,说明在开浇时,流场不稳定,保护渣熔化不好等情况下,产生裂纹的几率很大。
由于目前1#机开浇大都不使用开浇渣,而是开浇后直接加入保护渣,开浇后极易造成液面结壳,中包工必须不断搅动液面,造成保护渣下渣不良,传热、润滑都不好,促成裂纹的产生。
在中包第一炉等炉次,各个班出现裂纹的几率都比较大,说明我们并没有真正找到解决问题的办法,中包第一炉、换水口等炉次,虽然流场,保护渣,夹杂物等因素都容易产生裂纹,但是在操作中精益求精、不断改进,降低裂纹率还是能做到的。
本月还有7支裂纹发生在等钢水期间,可以归咎到工艺衔接问题,大家都知道恒速拉钢对提高铸坯质量,尤其是内部质量有好处,我们连铸工艺上也比较平稳,操作更规范,要做到恒速拉钢,个人认为重点并不在连铸,破坏衡速的往往是炼钢出现问题,钢水跟不上,硫高到精练脱硫等。
这就要求我们及时联系,出现情况及时通知,即使不能衡速,给我们一定时间平稳的把拉速降下来影响也会小些。
协议板和废品板方面,共有1865吨,总量还是比较多的。
一方面,切割要加大裂纹检查力度,提高精整质量;另一方面,要严格执行送坯制度,杜绝由于我们的失误导致大规模质量问题的出现。
另外,月初曾因铸坯角部裂纹出现大量协议板,更换结晶器后改善。
3.呕钢情况分析
根据现场观察情况分析,呕钢钢种多为合金含量比较高的钢种,切并不是发生在开浇时,而是发生在开浇注流稳定后,钢水自下水口与套管间隙慢慢溢出。
这种情况,说明钢包下水口与套管间隙过大。
在9月份开展呕钢劳动竞赛的基础上,本月推广1#机丁班的经验,使用两个整体密封圈,呕钢得到有效控制。
但是因密封圈供应问题和部分钢包下水口重复使用抹泥两个因素影响,造成呕钢现象。
本月征求多方意见已联系厂家定制新石棉垫,进行试验。
4.定尺情况分析
分别抽查了四班122支铸坯,定尺合格率仅为XX%,其中乙班不足XX%,切割多次反应二切割定尺不准,另外少数是由于非稳态等原因造成非计划下线,热送改为冷送,造成短尺。
抽查的铸坯中,长尺最多80mm,短尺90mm,与定尺差距较大,与操作工责任心不强有关,,车间已经严肃整顿,要求每班必量,把好定尺关。
三、本月重点工作总结
1、呕钢问题,得到比较有效的控制,采用新石棉垫圈后,效果明显比分体式垫圈效果好。
2、长短尺问题依然严重,二切割定尺改造的同时,要求加强责任心,把好定尺关。
3、结晶器整备质量差,更换原因有渗水、驱动报警,且近几个月因为此种问题更换频率明显增加,造成一定隐患,严重时造成班计划完不成。
四、存在的问题
1、目前出现窄尺问题,主要是由于非稳态下线,红送改冷送所导致,对于不同工艺路线钢种,下口问题需要继续探讨完善。
2、呕钢问题已基本解决,但部分钢种呕钢几率明显比其他钢种严重,且呕钢多集中在一些重点钢种上,一旦呕钢必须换托圈,敞浇,O、N要求很难达到。
3、抽调人员后,各岗位人员紧张,且新晋级人员较多,需加强教育,尤其是对预案的学习与掌握。
五、措施或下一步工作
1.1#长寿命浸入式水口进行扩大实验,目前试验来看,水口寿命可以达到700分钟,满足一个浇次使用,每个渣线可以使用350分钟。
使用时可配合免烘烤水口使用,出现质量问题及时更换。
2、改进型保护套管密封圈需要扩大试验,取O、N样分析保护浇注情况。
3、进行预案知识竞赛,加强各个岗位人员对预案的掌握。
4、2、3#机DD13钢种絮流情况有所改观,但须进一步研究操作要点,做到多炉连浇。
六、需分厂协调解决的问题
1.一号机摄像定尺项目尽快调试投用。
2.铸坯宽度对应结晶器峡口尺寸需要进一步优化完善,以满足下到工序要求。
3.改进型保护套管密封圈需要扩大试验定型,以解决保护套管呕钢问题。