浅述鲁奇炉造气文档格式.docx
《浅述鲁奇炉造气文档格式.docx》由会员分享,可在线阅读,更多相关《浅述鲁奇炉造气文档格式.docx(15页珍藏版)》请在冰豆网上搜索。
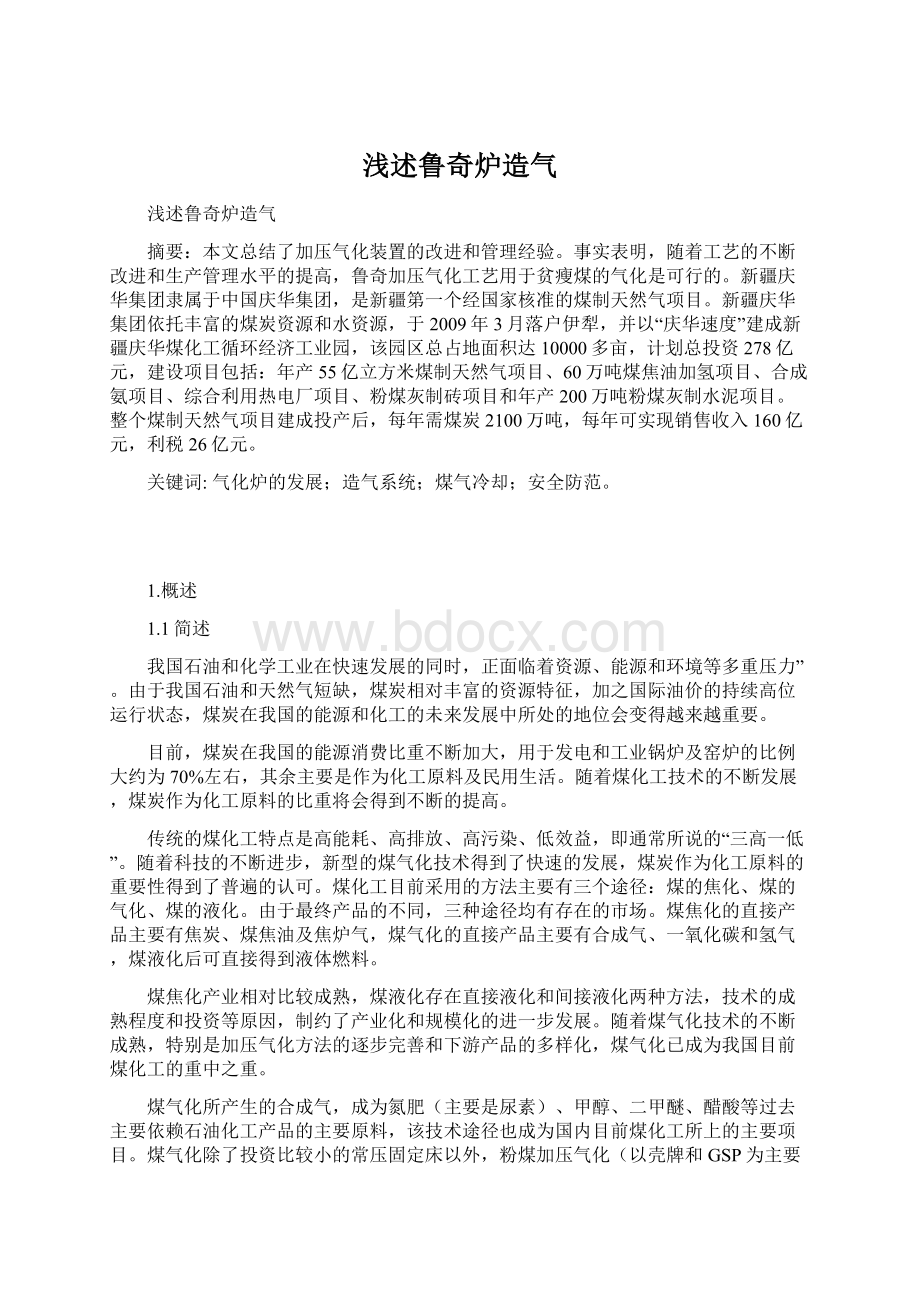
煤气化所产生的合成气,成为氮肥(主要是尿素)、甲醇、二甲醚、醋酸等过去主要依赖石油化工产品的主要原料,该技术途径也成为国内目前煤化工所上的主要项目。
煤气化除了投资比较小的常压固定床以外,粉煤加压气化(以壳牌和GSP为主要代表)、水煤浆加压气化(以德士古为主要代表)成为众多厂家引进国外节能环保的主要首选技术。
1.2鲁奇加压气化工艺发展前景展望
对于鲁奇加压气化工艺今后的发展,我们认为应在以下几方面予以重视:
①重视原料煤制备,确保气化用煤质量;
②进一步改进气化炉排灰系统,实现长周期运行;
③改进布煤器和搅拌器的结构和材质,延长使用寿命;
④适当扩大配套空分装置能力,气化炉氧耗高时不至于影响煤气产量;
⑤加强煤焦油等付产品的综合利用。
鲁奇加压气化技术在我国已得到了较好的发展,目前有两套煤制氨装置,三套城市煤气装置。
原料煤由褐煤扩大到贫瘦煤和长烟煤,对优质煤和高灰份的劣质煤都有很好的适应性。
我们相信鲁奇加压气化工艺将在我国的煤化工行业获得更广泛的应用。
2.煤加压气化技术简述
2.1煤加压气化的主要优势
气化效率高,碳转化率可高达98~99%,煤气中CO+H2(即有效气体成分)可达80%~90%。
气化压力高,水煤浆加压气化炉压力可达8.5MPa,粉煤加压气化炉压力可达4MPa,有利于实现装置的大型化,与其他先进技术联合使用,可以省去合成气的压缩机,降低能耗。
气化温度高,水煤浆加压气化炉温度可达1200~1500℃,粉煤加压气化炉温度可达1300~1700℃,GSP技术据说最高可达1900℃或以上。
气化温度高,煤中的有机物质分解气化彻底,降低污染,同时扩大了煤种的适应范围。
目前,我国普遍采用的煤加压气化技术是水煤浆加压气化和粉煤加压气化,二者各有特点,主要有:
1.气化压力:
由于原料进料方式的不同,一般情况下,粉煤加压气化的压力没有水煤浆加压气化的压力高。
2.气化温度:
由于炉内向火面的结构不同,水煤浆气化炉由于使用耐火砖形式,气化温度相对不能太高,这在一定程度上限制了煤种的适用范围。
3.水煤浆气化由于要将原料制成煤浆,因此要求原料煤具有稳定的成浆性能,当然,由于气化温度的限制,煤的灰熔点也不能太高。
4.粉煤气化由于是干粉供应,因此对原料煤的水分有一定的要求,而壳牌粉煤气化使用的废热锅炉冷却合成气,用于制氢和制合成氨时,在一氧化碳变换系统中,还要重新加入蒸汽,部分抵消了气化过程中的优势。
5.水煤浆由于需要将液体原料(含高浓度的固体煤粉)通过工艺烧嘴进行雾化,工作条件非常恶劣,因此,烧嘴的连续使用寿命制约了整个气化炉的连续运行周期。
6.为了追求较高的气化效率(有效气体成份),壳牌粉煤气化中需要用废热锅炉和过滤器,同时要用到循环气对气化炉出口合成气进行激冷,流程相对复杂,投资较大;
因此,在选择工艺路线时,要考虑投资、煤种、效益等多方面因素,任何一种工艺技术,都不是十全十美的,均存在需要改进的地方。
北京达立科科技有限公司、清华大学、山西丰喜肥业集团共同开发的水煤浆分级气化技术(也称之为“非熔渣-熔渣”煤气化技术),就是对传统水煤浆加压气化技术的一次有效改进,取得了很好的效果(详细论述见下文),该技术于2007年12月6日通过了中石化协会组织的专家鉴定。
本文作者全程参与了该项目的开发过程,从方案选取、专利申请、气化炉型结构确定、工艺烧嘴的设计及配置、二次补氧烧嘴的设计、配置等方面均提供了建议,并得到了有效实施。
同时为该工艺技术配套提供了专用的工艺烧嘴和二次补氧烧嘴,为该工艺技术的工业实施做出了重要的贡献。
2.2气化炉的优化操作
气化炉的运行有以下主要控制指标:
①灰锁温度;
②气化炉出口温度;
③煤气成份;
④H2O/O2的调整。
灰锁温度间接反映火层的高度,温度升高说明火层偏低,灰层薄容易烧坏篦子;
该温度偏低说明火层高,气化反应时间缩短,煤气质量和产气量都会下降,应加快排灰速度。
气化炉出口温度同样为火层高度的间接反映,该温度升高证明火层偏上,容易烧坏搅拌器,必须降负荷生产。
通过上下两个温度的控制,可以有效地控制火层,建立良好的工况。
如果两个温度发生异常,出现“双高”,且灰中有残碳存在,说明火层偏烧,局部反应状况不好。
此时,观察夹套耗水量,判断是否漏水,另一方面如果较长时间处于低负荷运行,应将气化炉负荷提到60%以上,低负荷下容易引起炉篦布气不均匀。
提高气化炉负荷的另一原因是高负荷下可以减弱漏水产生的影响。
气化炉出口组份反映气化反应的状况,在气化炉上下温度和H2O/O2一定时,煤气组份是相对稳定的。
如果CO2升高,反映气化反应不好,可能由以下原因造成:
①火层高,②干馏层结焦的干扰,③炉内漏水,④火层偏烧等。
H2O/O2的调整是重要的操作之一,主要依照灰的结渣情况和煤气成分进行调节。
固态排渣要求有适度的结渣,灰细灰粗都会造成炉篦子不下灰,H2O/O2的调整首先要满足排灰的要求。
煤气中的CO2含量反映了反应状况好坏,正常情况下CO2升高,说明H2O/O2偏高,CO2偏低说明H2O/O2低,反应温度高,容易发生结渣。
如果炉内有漏水现象存在,要防止发生H2O/O2调整偏低的现象。
因为漏水干扰气化反应,引起煤气中CO2升高,按正常情况调整H2O/O2势必会发生偏低的现象,严重时造成炉内大量结渣。
2.3气化炉的事故处理
气化炉操作不正常时,应首先考虑气化炉的安全。
煤气中的CO2和氧含量是重要的安全指标,CO2≥40%、O2>
0.4%,应作气化炉停炉处理。
气化炉发生以下故障,应考虑停车:
①加煤系统故障,炉内严重缺煤;
此时极容易烧透,氧气一旦穿入煤气中就会发生过氧爆炸。
②长时间不能排灰,火层严重上移,气化炉出口温度超标;
③炉内严重漏水,夹套耗水明显增大,煤气中CO2明显偏高;
④搅拌器长时间停转,干馏层对气化反应产生明显的影响。
3.造气系统
3.1加压气化原理
3.1.1物理化学基础
温度冷却
原料煤气
压力净化
3.1.2煤气化化学反应
压力下煤的气化在高温下受氧、水蒸汽、二氧化碳的作用,各种反应如下:
碳与氧的反应:
1C+O2=CO2+408.8MJ
22C+O2=2CO+246.4MJ
3CO2+C=2CO-162.4MJ
42CO+O2=2CO2+570.24MJ
碳与水蒸汽的反应:
⑸C+H2O=CO+H2-118.8MJ
⑹C+2H2O=CO2+2H2-75.2MJ
⑺CO+H2O=CO2+H2+42.9MJ
甲烷生成反应:
⑻C+2H2=CH4+87.38MJ
⑼CO+3H2=CH4+H2O+206.2MJ
(10)2CO+2H2=CH4+CO2+274.4MJ
3.2加压气化工艺流程
工艺流程图如下
(1)
(2)
工艺流程简述:
碎煤加压气化装置由气化炉及加煤煤锁和排灰灰锁组成,煤锁和灰锁均直接与气化炉相联接。
装置运行时,煤经由自动操作的煤锁加入气化炉,入炉煤从煤斗通过溜槽由液压系统控制充入煤锁中。
煤斗的容量可供四小时用,它装有料位测量装置。
装满煤之后,对煤锁进行充压,从常压充至气化炉的操作压力。
在向气化炉加完煤之后,煤锁再卸压至常压,以便开始下一个加煤循环过程。
这一过程实施既可用自动控制,也可使用手动操作。
用来自煤气冷却装置的粗煤气和来自气化炉粗煤气使煤锁分两步充压;
煤锁卸压的煤气收集于煤锁气气柜,并由煤锁气鼓风机送往燃料气管网。
减压后,留在煤锁中的少部分煤气,用气化剂—蒸汽、氧气混合物,经安装在气化炉下部的旋转炉蓖喷入,在燃烧区燃烧一部分煤,为吸热的气化反应提供所需的热。
在气化炉的上段,刚加进来的煤向下移动,与向上流动的气流逆流接触。
在此过程中,煤经过干燥、干馏和气化后,只有灰残留下来,灰由气化炉中经旋转炉蓖排入灰锁,再经灰斗排至水力排渣系统。
灰锁也进行充压、卸压的循环。
灰锁拥有可编程控电子程序器,也可手动操作。
充压用过热蒸汽来完成。
喷射器抽出。
经煤尘旋风分离器除去煤尘后排入大气。
为了进行泄压,灰锁接有一个灰锁膨胀冷凝器,其中充有来自循环冷却水系统的水。
逸出的蒸汽在水中冷凝并排至排灰系统。
气化所需蒸汽的一部分在气化炉的夹套内产生,从而减少了中压蒸汽的需求。
为此向气化炉夹套中加入中压锅炉给水,气化炉中产生的蒸汽经汽/液分离器送往气化剂系统,蒸汽/氧气在此按比例混合好喷射入气化炉。
离开气化炉的粗煤气以CO、H2、CH4、H2O和CO2为主要组分。
还有CnHm、N2、硫化物(H2S)、焦油、油、石脑油、酚和氨等众多气体杂质。
气化炉为带夹套的Φ4000型,每台气化炉有一台煤锁、一台灰锁、一台洗涤器和一台废热锅炉与之配套。
煤锁和灰锁装卸料的频率取决于产气量。
离开气化炉的煤气首先进入洗涤冷却器,在此,煤气用循环煤气水加以洗涤并使其饱和。
洗涤冷却器的用途首先是将煤气温度降至200℃左右,其次是除去可能夹带的大部分颗粒物。
饱和并冷却后的煤气进入废热锅炉,通过生产0.5Mpa(表压)低压蒸汽来回收一部分煤气中蒸汽的冷凝热。
在废热锅炉下部收集到的冷凝液的一部分,用洗涤冷却器循环泵送出。
多余的煤气水送往煤气水分离装置。
离开气化工段的粗煤气在压力2910kpa(g)、温度180℃饱和状况下,通过粗煤气总管进入煤气变换冷却工段。
3.3造气车间的主要装置
备煤系统、碎煤加压气化、煤气冷却、煤气水分离、酚胺回收等。
备煤系统主要任务及设备:
备煤系统的任务是为14台气化炉提供合格的原料煤以及5台锅炉合格的燃料煤;
其范围是从汽车卸车槽卸煤开始至造气厂房气化炉顶储煤仓及锅炉系统的煤仓上部为止。
主要包括原料煤、燃料煤的卸车、上煤、储存、粉碎、筛分及运输任务。
备煤系统主要设备有:
带式输送机54台,带式称重给料机48台,叶轮给煤机4台,驰张筛2台,圆振筛2台,环锤破碎机2台等,其中B60101AB两台驰张筛由德国进口,其余全部为国内配套。
3.4主要工艺控制参数
(1)供煤粒度要求
a.进煤粒度≤50mm,允许最大粒度≤100mm,含量≤5%。
b.锅炉供煤≤30mm。
c.造气供煤≥6mm,≤50mm。
d.造气供煤粒度小于6mm含量≤5%。
(2)供煤内在控制指标
a.煤中水份含量≤12%。
b.煤中不能含有其它杂物(如木棒、铁器、扫帚、皮带等)。
c.块煤中矸石<4%
(3)锅炉每小时耗煤429吨,日耗煤9438吨。
锅炉煤仓总储煤6400吨,可供锅炉运行15个小时。
(4)造气炉每小时耗煤420吨,日耗煤10080吨。
气化炉煤仓总储煤2240吨,可供造气炉运行5个小时。
(5)1#~8#圆筒仓储原煤76000吨,1#、2#地槽储原煤3000吨,总储原煤79000吨,可供全厂运行4天。
(6)原煤单系列输煤能力1200吨/小时。
(7)造气单系列输煤能力750吨/小时。
(8)锅炉单系列输煤能力600吨/小时。
3.5主要任务及设备
造气系统的主要任务是向煤气冷却工号提供合格的粗煤气,经冷却工段冷却后提供给后序工段,以生产甲醇和二甲醚。
造气选用碎煤加压气化炉,其炉型为Mark-Ⅲ,是目前世界上使用最广泛的一种炉型。
其内径为¢3·
8M,外径4·
128M,炉体高12·
5M,炉内燃料堆放高度4000毫米,炉体容积119M3,炉体总重量169.5(其中包括内件重量40吨),操作重量250吨,夹套宽度为46毫米,总容积为13M3,气化炉操作压力为3·
05Mpa。
该炉生产能力高,炉内设有搅伴装置,可气化除强黏结性烟煤外的大部分煤种。
下图为气化炉图
煤锁是用于向气化炉内间歇加煤的压力容器,其上下为圆锥形封头,中间为圆筒形。
煤锁的容积为12.1m3,有效容积为11.2m3。
煤锁加煤操作时的各阀门的动作靠液压装置来驱动。
它是通过泄压,充压循环将存在常压煤仓的原料煤加入高压的气化炉内,以保证气化炉的连续生产。
煤锁包括两部分:
(1)连接煤仓与煤锁的煤溜槽。
(2)煤锁及煤锁下阀,它将煤锁中的煤加入气化炉中。
下图为煤锁
气化炉体:
加压气化炉的炉体不论何种炉型均是一个双层筒体结构的反应器。
其外筒体承高压,一般设计压力3·
6MPa,温度260℃,内筒体承受低压,及气化炉与煤气通过炉内料层的阻力,一般设计压力为0·
25MPa(外压),温度310℃.内外筒体的间距一般为40-100㎜其中充满锅炉水,以吸收气化反应传给内筒的热量产生蒸汽,经汽液分离后并入气化剂中。
这种内外筒结构的目得在于尽管炉内各层温度高低不一,但内筒体由于有锅炉水的冷却,基本保持在锅炉水在该操作压力下的蒸发温度,不会因过热而损坏。
由于内外筒受热后的膨胀量不尽相同,一般在内筒设有补偿装置。
夹套蒸汽的分离也分为内分离或外置汽包分离,如图所示
炉蓖:
如图炉篦设在气化炉的底部,它的主要作用:
是支承炉内燃料层,均匀地将气化剂分布到气化炉横截面上,维持炉内各层的移动,将气化后的灰渣破碎并排出,所以炉篦是保证气化炉正常连续生产的重要装置。
现在运行的装置在设计上,大多采用了宝塔形炉篦。
宝塔形炉篦一般由四层依次重叠成梯形锥状的炉篦块及顶部风帽组成,共五层炉篦,它们依次用螺栓固定在布气块上。
灰锁:
用来将炉箅刮下的炉灰间歇排出炉外的锁灰容器,其上部为凸形封头,下部为锥形封头。
灰锁容积为10.1m3,有效容积6.4m3。
灰锁各阀操作同样是靠液压装置来驱动。
灰锁由于是储存气化后的温灰渣,工作环境较为恶劣,所以一般灰锁设计温度为470℃,并且为了减少灰渣对灰锁内壁的磨损和腐蚀,一般在灰锁筒体内部都衬有一层钢板,以保护灰锁内壁,延长使用寿命。
灰锁结构如图所示:
灰锁膨胀冷却器:
灰锁膨胀冷却器是第三代鲁奇炉所专用的附属设备。
它的作用是在灰锁泄压时将含有灰尘的灰锁蒸汽大部分冷凝,洗涤下来。
一方面使泄压气量大幅度减少,另一方面保护了泄压阀门不被含有灰尘的灰锁蒸汽冲刷磨损,从而延长阀门的使用寿命,提高气化炉的运转率。
如图
喷淋洗涤冷却器:
喷淋洗涤冷却器(简称喷冷器)与气化炉粗煤气出口管垂直相连,其作用是对气化炉出来的高温粗煤气进行洗涤冷却,使粗煤气温度由400~500℃降至204℃,并且除去焦油和煤尘。
结构如图所示:
4.煤气冷却工段
4.1工艺原理
煤气冷却工号的目的是把来自加压气化工号的粗煤气中的废热回收、利用并冷却至37℃,送往低温甲醇洗工号进一步净化。
来自气化的181℃粗煤气经过预热锅炉给水、脱盐水,最终用循环冷却水冷却至37℃,送后系统低温甲醇洗工号。
本装置的煤气水洗涤流程为逆流流程,利用煤气水分离装置的高压煤气水及粗煤气自身的冷凝液作为本工号洗涤用水。
本装置洗涤煤气后的煤气水返回煤气水分离装置,这样就减轻了煤气水分离工号的处理负荷。
4.2工艺流程简述
来自200#气化的粗煤气大约181℃,首先进入粗煤气洗涤器(B609A01),在洗涤器内粗煤气用来自粗煤气洗涤水泵(J609A01)的煤气水洗涤,洗涤水不足时,由来自煤气水分离装置的高压喷射煤气水补充。
在此过程中,粗煤气中的大量灰被洗涤下来,粗煤气温度大约下降2℃,这样粗煤气中少量焦油被冷凝洗涤下来。
下游的粗煤气分离器(F609)把夹带在煤气中的少量液滴分离下来,与洗涤水一起收集起来。
离开分离器底部的含有焦油的煤气水,送往煤气水分离装置。
离开分离器顶部的粗煤气接近无尘,进入预冷器(C609AB)进行第一步冷却,在此粗煤气从179℃冷却至130℃,粗煤气中部分焦油和水蒸气将被冷凝下来。
预冷器是立式管壳式换热器,粗煤气从预冷器顶部进入(管程),由底部排出。
预冷器底部贮槽收集冷凝液。
壳程的冷却介质锅炉给水从105℃加热到150℃。
根据需要来自煤气水分离装置的高压喷射煤气水喷入预冷器的管程。
第二步冷却,在中间冷却器(C609A02)中粗煤气由130℃降至70℃,煤气中部分油和水蒸气将冷凝。
中间冷却器为立式,粗煤气由其顶部进入管程,从底部排出。
来自煤气水分离装置的煤气水喷入中间冷却器管程,冲洗NH3,以防止管程表面形成碳酸氢铵结晶。
喷射的高压煤气水和冷凝液收集在中间冷却器底部贮槽,并由此排出。
中间冷却器壳程冷却介质为脱盐水,在此脱盐水由40℃加热到85℃。
第三步冷却,粗煤气在最终冷却器(C609A03)中由70℃降至37℃。
最终冷却器也是立式管壳换热器,煤气从顶部进入管程,底部排出。
来自煤气水分离装置喷入最终冷却器管程,喷射高压煤气水的目的与第二步的冷却目的相同。
高压喷射煤气水与冷凝液收集在最终冷却器的下部贮槽内,并由此排出。
最终冷却器壳程冷却介质为循环冷却水,其温度由32℃加热到42℃。
最终分离器(F609A02)将从最终冷却器进入的煤气中含有的少量氨、油及煤气中夹带的少量液滴进一步分离,最终离开最终分离器的无氨、无尘、无油、无焦油和酚的粗煤气进入低温甲醇洗工号。
煤气冷却工号有两条煤气水管线分别进入煤气水分离工号。
——含焦油煤气水
——含油煤气水
含焦油煤气水是一种混合物,主要成份水、尘和焦油。
从预冷器C609A01A/B里冷凝下来的含焦油煤气水和粗煤气分离器F609A01底部排出的含焦油煤气水一并送往煤气水分离初焦油分离器装置。
含油煤气水也是一种混合物,主要成份为水、油、氨和酚。
此部分煤气水包括来自中间冷却器C609A02和最终冷却器C609A03的喷射煤气水及煤气冷凝液。
含油煤气水最终送往煤气水分离工号含
煤气水分离工段
4.3主要任务与设备
主要任务是将加压气化和煤气冷却工段以及低温甲醇洗等工段来的煤气水膨胀分离出其中的溶解气、固体颗粒及焦油/油,并向气化(606#),煤气冷却(609#)分别提供低压喷射煤气水和高压喷射煤气水。
多余的煤气水经过双介质过滤器处理后送往酚胺回收工段在处理。
设备有:
膨胀冷却器、初焦油分离器、油分离器、第一、二缓冲槽、煤气水储槽、泥浆液槽、纯焦油槽、油槽、焦油污水槽、膨胀气鼓风机气液分离器、膨胀气气液分离器、安全水封汽液分离器、最终油分离器、双介质过滤器、含尘煤气水膨胀器安全水封、含油煤气水膨胀器安全水封、焦油污水槽安全水封、含尘煤气水冷却器、余热回收器、膨胀气冷却器、煤气水换热器、煤气水冷却器、煤气水泵等。
工作原理
根据无压重力沉降原理,利用不同组分的密度差,把煤气水中的油、含尘焦油分离出来。
利用压力降低气体在液体中溶解度减小的原理,经闪减压,分离出煤气水中溶解的CO、NH3、CO2等气体。
流程简述
从601#来的含尘煤气水进入废热锅炉回收热量,煤气水从199℃降到155℃,产生143℃的饱和蒸汽送除氧站,出来的含尘煤气水进入串联的含尘煤气水冷却器,均用循环冷却水最终冷却到70℃,冷却后的煤气水进入两个并联的含尘煤气水膨胀器。
另外,从气化来的低压含尘煤气水、开车期间由废锅来的煤气水以及从低温甲醇洗一系列来的部分冷凝液和从煤气冷却来的部分含油煤气水也进入。
上述混合煤气水在膨胀至接近大气压,煤气水靠重力进入四个并联的初焦油分离器,煤气水进入分离器的中心,在此,煤气水通过一中心管进入第一沉降区,在这个区域物流沿径向方向流入分离器壁,粘稠的含尘焦油和大部分重焦油沉降到分离器的锥形底部,分离器内有两个搅拌器,以防止焦油和尘沉积在分离器壁上。
含尘焦油从分离器的底部分离出来,就地装车。
在分离器中,纯焦油从煤气水中分离出来,并靠一外部可调溢流堰从分离器间断排出,靠重力流入纯焦油槽,由纯焦油泵将焦油送往罐区。
在第二沉降区,煤气水沿径向返回到分离器中心流到安装在分离器中心管四周的固定溢流管到环状槽,靠重力流到最终油分离器,煤气水也可溢流到缓冲槽。
从609#煤气冷却来的部分含油煤气水与低温甲醇洗一系列来的部分冷凝液进入两个并联的含油煤气水膨胀槽,膨胀至接近大气压,煤气水靠重力流入两个并联的油分离器,通过一中心管沿内壁进入第一沉降区形成一均匀的径向流,在第一沉降区焦油沉降在分离器的锥形底部,底部外壁装有蒸汽伴热管。
在这个沉降区,油靠浮力从煤气水中分离出来,物流通过油提升器到第二沉降区的煤气水表面,凝结的油滴从煤气水中分离出来,并升到液面上,分离的油沿径向返到分离器中心,经一内部固定的溢流管到环状槽,在这儿,油通过一外部可调溢流堰排到油槽,然后用油泵打往罐区。
分离后的煤气水靠重力流入最终油分离器或到缓冲槽。
经过初焦油分离器和油分离器分离出焦油和油的煤气水,混合后由最终油分离器的底部进入,首先进入焦炭过滤框向上流,在上升过程中,使小的油滴相互碰撞形成大的油滴,以增进油、水、焦油的分离,在油的分离过程中,一些油滴离开焦炭过滤框直接上升到液面,收集在最终油分离器的集油室,油靠重力通过一外部可调溢流堰流入油槽。
分离后的煤气水从TPI板件底部离开,然后向上流到其集水室并经一溢流堰靠重力流到缓冲槽,由泵经冷却器完成冷却后送往双介质过滤器进行过滤。
经过初焦油分离器和油分离器分离出焦油和油的煤气水也可送到缓冲槽,然后经泵送到煤气水冷却器完成冷却,冷却后的煤气水再进入进行分离,分离后的煤气水再到由泵经冷却器的旁路送往双介质过滤器进行过滤。
另外,通过调节冷却水的量来调节出口的温度。
这样使得可在70℃(不冷却)和40℃(冷却)间操作。
还向提供低压冲洗煤气水。
喷射煤气水泵从缓冲槽和向提供高压喷射煤气水。
经过最终油分离器分离后的煤气水中还有悬浮固体、油和焦油,所以由分离后的煤气水经泵从双介质过滤器顶部进入,经床层过滤后从底部排出,过滤后的煤气水进入煤气水贮槽。
双介质过滤器运行一段时间后,床层压差增大,易于损坏床层,因此必须进行返洗。
返洗水由反洗泵从煤气水贮槽送到双介质过滤器的底部,每隔24小时对双介质过滤器进行返洗一次,反洗回水即泥浆液收集在泥浆液槽中,然后用泵送到初焦油分离器进行再