沥青混凝土下面试验段施工方案917Word文件下载.docx
《沥青混凝土下面试验段施工方案917Word文件下载.docx》由会员分享,可在线阅读,更多相关《沥青混凝土下面试验段施工方案917Word文件下载.docx(12页珍藏版)》请在冰豆网上搜索。
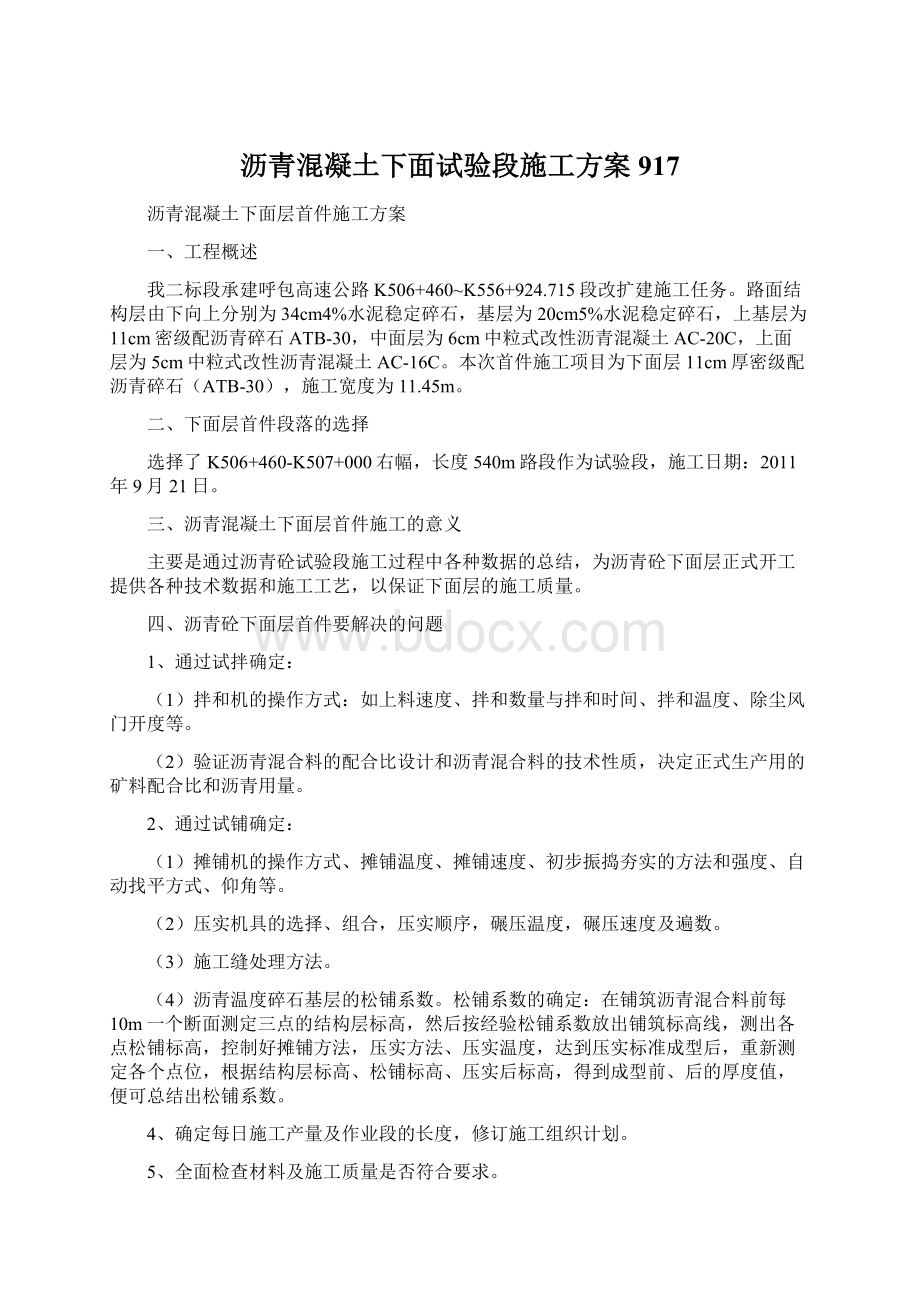
5、全面检查材料及施工质量是否符合要求。
6、确定沥青混凝土的压实标准密度。
采用取芯法及水中重法测定密实度,并用当天的马歇尔击实密度作为标准密度。
7、完成总结,上报审批。
五、组织机构:
1、项目经理:
罗云峰
2、项目副经理:
皮振涛
3、项目总工:
葛建国
4、工程办主任:
徐震
5、质检办主任:
胡永胜
6、试验室主任:
王玉杰
7、设备办主任:
郑晓伟
8、材料办主任:
高波
9、拌和站站长:
刘东
10、安全办主任:
鲁春海
施工组织机构图
项目经理
项目副经理
项目总工
质检办主任
试验室
设备办主任
材料办主任
工程办主任
质检员
试验员
机械组
材料员
测量员
工长
拌和站
六、下面层试验段施工工艺及方法
(一)、施工准备
(一)施工组织
人员准备:
1、施工总负责(经理):
2、现场技术负责人(总工):
葛建国
3、现场施工负责人(工程副经理):
皮振涛
4、机械负责人(机械经理):
郑晓伟
5、拌和站负责人(拌和站站长):
刘东
6、现场试验负责人:
王玉杰(试验室主任)、任玉强(试验员)
7、质检负责人:
8、质检员:
常兴
9、现场技术员:
邹德礼、李东航、郝成林
10、材料负责人:
高波
11、拌和站试验员:
王伟、苏家琛、任柏林
12、安全办:
鲁春海、周国忠、靳彦军
机械准备:
1、拌和站施工机械配备:
西筑4000沥青砼拌和站1座,用于上料的ZL50装载机4台。
2、施工现场机械配备:
陕西中大摊铺机1台,DD130双钢轮振动压路机3台,徐工30T胶轮振动压路机2台,20m3自卸汽车10台,洒水车2台,风力鼓风机2台。
3、配合拌和站及施工现场人工:
25人(拌和站10人,施工现场15人)。
材料准备:
1、沥青:
普通沥青A级90号道路石油沥青,试验结果详见试验检测报告。
2、矿粉:
呼和浩特市斯科耐特工贸有限公司矿粉,试验结果详见试验检测报告。
3、碎石:
采用自产碎石,分5挡料,1#(19-31.5mm)、2#(9.5-19mm)、3#(4.75-9.5mm)、4#(2.36-4.75mm)、机制砂,试验结果详见实验报告。
4、抗剥落剂:
采用镇江金阳道路材料科技有限公司生产的JY-K1型沥青抗剥落剂,其掺量为沥青用量的0.3‰。
(二)、施工工艺及方法
1、施工前准备工作
(1)当基层达到养生期并经试验满足设计强度要求时,经验收,各项指标合格。
(2)进行详细的技术交底,使每个施工人员了解设计意图,掌握规范及各项技术指标。
(3)合理配备人员、设备。
(4)恢复中线,复核水准点。
(5)清理下承层,清除杂物积水;
洒布透层油,透层油洒布后严禁非施工车辆通行,并做同步碎石封层。
(6)拌和站配备储备400T沥青的储存装置,并能够自动循环加热。
2、施工放样
恢复中线,加密(10m)中线桩;
校核水准点,每200m增设一个临时水准点;
在按松方系数1.15计算出的设计高程以上10-15cm处挂钢丝,钢丝绳的张力达到10KN以上,否则传感器在钢丝绳上移动时会出现挠度,要严格保护好摊铺机的传感器系统,不能磕碰传感器。
3、沥青混合料的拌和
(1)沥青采用AH-90石油沥青,油石比按3.3控制使用。
(2)沥青采用导热油加热,加热温度控制在155℃-165℃,利用控制柜的小火、大火开关、燃烧器电源开关,报警音响等来控制沥青温度,也可通过自动调节仪达到要求。
(3)矿料经滚筒烘干至165℃-185℃后,当各仓材料满足规定比例后,自动进入拌和仓,干拌5-10s后,加沥青后再拌和10-15s,加入矿粉后,继续拌和15s左右。
拌和仓温度设置为165-170℃,直至拌和均匀,无花白料,无结团块或严重的粗料分离现象,拌和时间控制在30-50s。
(4)沥青混和料的出料温度宜控制在155℃-165℃之间,混和料温度高于190℃混和料作废。
4、沥青混合料的运输
(1)运输车在装料前,每天对车辆进行检查和保养,发现故障立即修理,禁止车辆带病作业;
保证车辆状况良好;
沥青混合料运输车的运量应较拌合能力或摊铺速度有所富余,运输车辆数量按平均每公里往返1辆,摊铺现场卸料1辆,等候卸料2辆,拌和站下装料1辆,等候装料2辆,考虑车辆的完好率,本次试验段用50t运输车10辆。
(2)装料前把车厢清扫干净,在车厢板上涂一层隔离剂(油水比1:
3的混合液),但不得有余液积聚在车厢底部;
雨后开始施工时一定要检查车厢里是否有积水,如有积水必须清理干净
(3)车辆装料过程中要至少前后移动4-6次,将料分层铺满,以减少粗集料的离析(装车时要安排人员对混合料进行温度量测,料温低但还可以用时可以上路,但要通知前台要先卸,快速碾压;
料温过低,予以废除)。
(4)运输车辆必须覆盖苫布,并且要覆盖严密,以确保料温和防止污染、雨淋等。
(5)车辆到达摊铺现场,掉头过程中要多调几把舵避免车轮对下承层的损害。
(6)连续摊铺过程中,运料车在摊铺机前10-30cm处停住,不得撞击摊铺机,卸料过程中运输车应挂空档,靠摊铺机推动前进。
(7)混合料运输到现场温度控制不低于150℃。
5、沥青混合料的摊铺
稳车,根据摊铺厚度,测量人员用水准仪按断面5点测好,然后用木方及垫片垫够高,将摊铺机熨平板按照前沿对齐稳车,调整仰角(如摊铺起车作业面已是成型路面,则只垫垫片,垫片厚度略小于松铺厚度)。
(1)摊铺前要对熨平板进行加热,加热时最好用喷灯配合摊铺机的预热系统加热,这样可以提高加热速度。
加热温度达110度左右,熨平板底部要清洁,夯锤接缝要严密。
(2)摊铺速度要和拌合站生产能力相匹配(刚起车时一定要慢,便于摊铺机摊铺厚度及拱度调整),正常摊铺要匀速,不间断摊铺,不得任意快速摊铺和停机等料,停人不停机。
要求摊铺机前要有两台运输车等候,并且当前一台运输车摊铺一半时在将下一辆车的苫布打开这样可以保持混合料的温度。
(3)摊铺过程中前后台要保持经常联系以及防止设备坏和天气影响造成摊铺不连续影响整体质量。
(4)沥青砼的厚度是保证质量的一个硬指标,所以厚度设专人检测,每十米检测左中右3点,并记录。
(5)摊铺温度是保证质量的前提,沥青砼不低于145度,现场有人做好温度记录。
(6)正常摊铺过程中不应该用人反复休整,当出现下列情况时可用人工做局部找补。
a、构造物接头部分缺料。
b、摊铺带边缘局部缺料。
c、表面明显不平整和混合料明显离析。
d、摊铺机后有明显拖痕。
(7)摊铺机不得随意收料斗,除特殊情况,尽量减少收斗次数。
(8)摊铺质量的好坏对路面平整度影响非常大,所以要求有专人控制摊铺机的传感器,除了工长其他人轻易不得调整,包括钢丝线和平衡梁,工长随时检查基准线。
(9)每天摊铺结束后,摊铺机应开到彩条布上进行清理和保养,不得在下承层上进行上述工作,应将夯锤及熨平板上粘的残料清理干净。
(10)摊铺机应经常检查主要部位以确保完好率。
(11)施工过程中摊铺机如需调迁,最好使用拖板车进行,这样可以提高速度和减少机器损耗。
(12)施工中一定注意沾工具用的柴油,一定要放至在摊铺机前施工作业面外,防止污染损毁路面。
6、碾压
碾压是一个非常重要的程序,直接影响路面的实体质量,所以对路面的压实度要有专人负责。
沥青混合料压实采用胶轮压路机和振动压路机组合方式,总体原则“高频,低幅,紧跟,慢压”,由低向高碾压,碾压分为初压,复压,和终压三个阶段。
(1)初压:
摊铺之后立即进行,应尽可能在高的温度下紧跟摊铺机碾压,用2台DD130双钢轮振动压路机前静后振碾压各1遍,压实时应将驱动轮面向摊铺机,初压后立即检查平整度和路拱,必要时予以修正。
(2)复压:
初压后紧接着进行复压,用30T轮胎压路机碾压4-6遍,光轮压路机振压3-4遍使其达到要求的压实度。
(3)终压:
复压之后紧接进行终压,采用DD130双钢轮压路机振压1遍,静压2遍,消除轮迹。
(4)沥青混合料按初压、复压、终压三个阶段进行,压路机的碾压速度应符合以下规定:
初压振动压路机静压速度为1.5-2km/h
复压轮胎压路机碾压速度为3-4km/h
振动压路机振压速度为2-4km/h
终压振动压路机静压速度为4-5km/h
(a)沥青混合料的初压符合以下要求:
初压应在混合料摊铺后较高温度下进行,一般宜控制在不低于135℃,不得产生移动、开裂等现象。
压路机应丛外侧向中心碾压,相邻碾压带应重叠1/2轮宽,最后碾压中心部分,压完全幅为一遍。
当边缘有路缘石等支挡时,应靠支挡碾压。
当边缘无支挡时,可把耙子将边缘的混合料稍稍耙高,然后将压路机外侧轮伸出边缘10cm以上碾压。
(b)驱动轮面向摊铺机,碾压路线及方向不许突然改变,压路机起动或停止必须减速缓慢进行。
(c)沥青混合料的复压应紧接在初压之后。
复压采用重型双光轮压路机。
碾压遍数应经验确定,一般不宜小于4-6遍,达到要求的密实度无显著轮迹,其混合料温度控制在125℃-135℃为宜。
(d)终压紧跟在复压后进行,选用胶轮压路机碾压,一般终压不得小于2遍,碾压终了沥青混合料的温度不低于90℃。
7、特殊部位处理
(1)在预定摊铺段的末段先铺上一薄层纱带再摊铺混合料,待混合料冷却后用3米直尺找平,将纱带部分和不合格的部分(1m以上)用彩粉笔划一条垂直路中心的横线。
(2)接缝时沿划好的横线将不合格(2-4m)切割齐后取走,扫净砂子,用干拖布将纱带部分处的水分吸走,待干燥后在断部洒粘层沥青,然后进行摊铺。
(3)对摊铺机的熨平板应放在已铺完的路段上,并在下面按松方系数垫两块木板条,用熨平板和热料对横缝熨平45分钟。
然后调整好初始工作仰角,并依1.5-2m/min的速度摊铺。
(4)对于熨烫好的横缝附近用扫帚清扫大颗粒和浮料,用压路机从低向高处错20cm先碾压横缝约20cm长,再向前碾压。
(5)初压后再用3m直尺检查,若有麻面可用热料中的细颗料填平找平,然后用振动压路机横向从旧路面向新路面以15-20cm宽碾压,待压路机全部压在新路面上,然后纵向碾压。
8、中途停机段处理
(1)①要尽量靠近摊铺机碾压;
②适当缩短碾压段;
③防止人员在未碾压段上行走。
(2)当要停机时应降低振动力,同时要放慢摊铺速度(一般放慢到1m/min),如停机时间过长,混合料温度降低较大,不能继续摊铺,必须提机按横缝处理。
9、在坡度路面碾压时,应首先自低处向高处进行,无论上坡或下坡驱动轮始终在后方。
10、弯道碾压时,压路机应走切线(直线)方向,用多切线形成弯道内外边沿,每次从内边沿开始,依次向外边沿扩展碾压。
11、养护及开放交通
(1)热拌沥青混合料待摊铺后完全自然的冷却,沥青路面表面温度低于50℃后,方可开放交通。
(2)对已成型的面层,每公里应放1-2名民工,负责路面清扫并派人监督防止往路面上洒汽油、柴油等破坏性材料。
12、质量检查
(a)每天拌和机开机时,要进行混合干料的筛分,保证混合料的级配合理。
(b)对混合料进行抽提实验,使混合料油石比和级配均满足规范的规定。
13、外观鉴定
(a)表面应平整密实,不应有泛油、松散、裂缝粗细明显离析等现象;
(b)无明显轮迹;
(c)缝紧密、平顺、烫缝不应枯焦;
面层与路缘石及其他构造物衔接平顺,无积水现象。
14、泛油、松散、裂缝常见病害的预防措施
(1)泛油、松散是沥青混凝土路面常见病害。
泛油大多是由于混合料中沥青用量偏多,沥青稠度太低等原因引起;
松散大多是由于混合料中沥青用量偏少,混合料级配不好等原因引起。
沥青进场时每车沥青到要进行试验,必须保证进场沥青材料质量合格;
施工时每天上下午进行两次抽提、筛分试验,严格按照施工配合比控制沥青混合料中的沥青含量、混合料的级配。
(2)裂缝是沥青路面最主要的破坏形式之一,按其成因不同可分为横向裂缝、纵向裂缝和网状裂缝三种类型。
沥青路面生开裂的原因,一种是因填土未压实,路基产生不均匀沉陷或冻胀作用所造成;
另一种是沥青路面施工时沥青混合料级配不好,沥青路面压实不够。
为避免裂缝产生,首先在路基施工时应严格控制每层填土厚度,并保证压实达到设计压实度要求,其次在沥青路面施工时应严格按照施工配合比控制沥青混合料的级配,再次沥青路面施工时应严格控制碾压的机械吨位、碾压的温度、碾压的遍数符合规范要求。
七、进度保证措施
1、配备足够的机械设备和施工人员。
2、主要施工负责人和有关管理人员要跟班作业,必要时组织力量进行重点难点突破。
3、制定好切实可行的雨季施工及夜间施工技术措施。
4、加大试验检测人员投入,确保检测频率,保证施工质量,杜绝返工现象发生。
八、文明施工
1、保证便道畅通无阻,能及时排水。
2、施工现场机械摆放有序,施工前后顺序分明。
3、施工现场整洁,组织有序。
4、施工现场各种标识牌齐全、醒目。
5、重要道口必须设专人指挥交通。
6、必须保证水平运输车辆箱体密封完好,防止关闭不严运输料洒落污染和破坏路面。
7、必须配有足够数量运输车辆并与摊铺能力、运距相适应,不能出现拥堵和断档现象,保证摊铺或平料的连续性,在摊铺作业现场形成一个不间断而有序的供料车流。
8、严禁压实设备及水平运输车辆在沥青混凝土路面上调头。
九、安全生产保证措施
1、施工现场配备专职安全员。
2、拌和站和施工现场有专人指挥车辆。
3、拌和站和施工现场设立醒目的安全标志。
4、对施工人员进行安全教育,签定安全责任状。
5、严格按照施工规范和安全操作规程施工,在作业地点挂警告牌,严禁违章操作野蛮施工。
6、经理部内要有严密的安全监督体系,并经常对参施人员进行安全教育,提高安全意识。
7、施工操作人员佩带安全防护工具,现场操作人员戴安全帽。
8、施工作业段落行车速度不大于20公里/小时。
9、施工路段尘土多处必须及时洒水降尘,保证形成视线清晰进而保证行车的安全。
沥青砼路面施工工艺流程图
不合格