元月合成氨装置检修开车方案Word格式文档下载.docx
《元月合成氨装置检修开车方案Word格式文档下载.docx》由会员分享,可在线阅读,更多相关《元月合成氨装置检修开车方案Word格式文档下载.docx(11页珍藏版)》请在冰豆网上搜索。
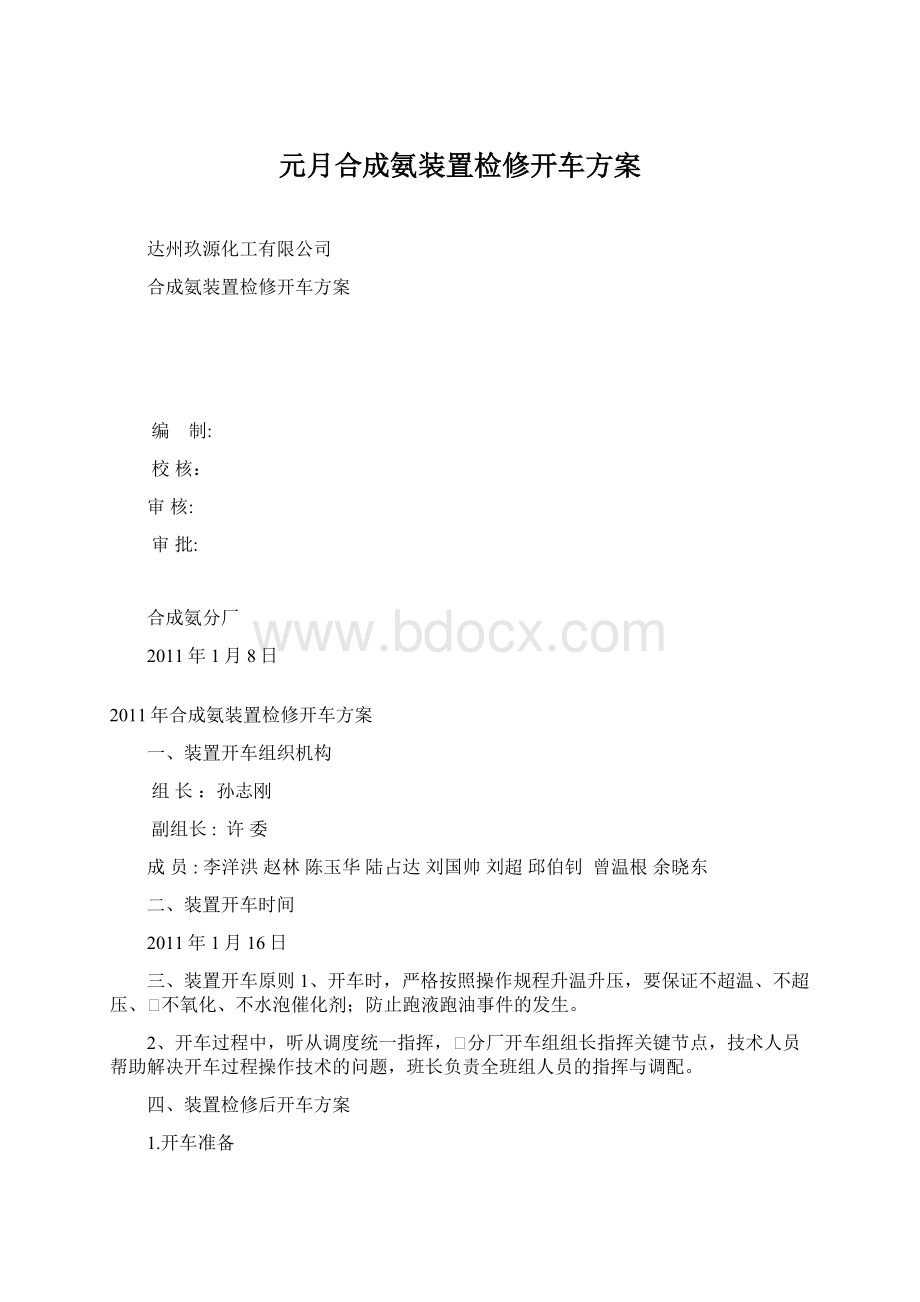
防止跑液跑油事件的发生。
2、开车过程中,听从调度统一指挥,分厂开车组组长指挥关键节点,技术人员帮助解决开车过程操作技术的问题,班长负责全班组人员的指挥与调配。
四、装置检修后开车方案
1.开车准备
(1)确认装置具备接受水、电、气的条件。
(2)200-FS液位28%以上,200-LS正常投运。
(3)仪表系统运行正常,供应合格的仪表空气,仪表空气管网压力在0.6~0.8MPa,露点在-40℃以下合格的仪表空气。
(4)装置用润滑油、润滑脂、水系统、联胺、磷酸盐、稀氨水、甲醇等全部备齐,加药槽溶液已按规定配置好。
(5)氮气纯度>99.9%,压力>0.5MPa,催化剂处于氮气保护状态之下,系统已氮气置换合格。
(6)检修项目逐项检查已完成,快锅、水系统具备开车条件,确认与开车有关的设备检修、更换施工完毕,设备清扫合格,仪表、阀门、安全阀、调试验收合格具备开车条件,临时盲板已拆除,“8”字盲板已倒换完成。
(7)DCS系统维护完成,操作系统画面、量程等已修改、发布更新。
(8)装置区内照明齐全,对讲机3对、电话机好用,消防器材,防毒、防护用具,事故急救箱已备齐就位。
(9)三大机组油循环过滤合格,联锁调试合格。
(10)静加油点加好油脂,油箱油杯已加油或换油至正常液位,机泵加好润滑油并处于良好备用状态。
(11)所有生产分析项目具备分析条件,记录报表齐全。
(12)现场已做到工完料净、场地清,道路畅通无阻。
2装置开车
2.1引天然气
(1)确认所有原料气、燃料气系统处于天然气正压状态或已氮气置换合格,所有阀门位置正确,安全阀已投用。
(2)将PIC0101设定4.0MPa投自动,缓慢开进界区天然气大阀,向管道充压,将PIC6002设定3.2MPa投自动,PCV1投自动,根据燃料气系统用量设定0.5~0.7MPa。
得到调度指令后,缓慢向快锅送天然气。
2.2引汽建立MS、LS管网
(1)引汽前,必须确认装置中压蒸汽、低压蒸汽管网已具备受汽条件,检查并关闭中压蒸汽、低压蒸汽管网所有与设备相连的截止阀。
(2)把中压蒸汽、低压蒸汽管网上各端点、低点导淋阀全开。
(3)缓慢开大中压蒸汽入界区阀,用PIC-25配合升压,升压速度0.1MPa/分,严防水击,压力达3.7MPa时,PIC-25投自动。
(4)中压蒸汽稳定后,及时投用疏水器;
稍开PCV-26进行低压蒸汽暖管,待排汽干燥后关闭导淋阀,升压至0.35MPa,PIC-26、PIC-27投自动。
(5)蒸汽管网建立后,立即安排对S蒸汽新配低压蒸汽管吹扫,每次吹扫10分钟,吹扫三次后,复位。
2.3建立循环水系统
(1)检查所有冷却器的封头、阀门、丝堵、压力表、温度计都安装好,循环水低点排水阀已关闭,水冷器进出口阀打开。
(2)联系调度送循环水,各水冷却器高点排气,排完气后及时关闭排气阀。
(3)检查有无泄漏点,如有泄漏及时联系处理。
2.4建立表冷器真空
(1)通知调度向合成装置送脱盐水,大、小表冷建立90%高液位。
(2)开启一台透平冷凝液泵,开冷凝液出口LCV-2阀,通过LCV-2A阀进行循环,维持1/3~1/2的液位。
(3)将大小表冷器开工喷射器投用,建立真空,并依次将后冷凝器的喷射器投用,PI-657≤-380mmHg,并检查疏水阀。
(4)在开车初期,打开112-J出口去循环水池阀门,待冷凝液合格后关闭,将冷凝液送入2005-U,此时将2005-U处压力提至0.35~0.40MPa,及时向引、送风机、104-J等大气式安全阀送密封水,提高表冷器真空度。
2.5水夹套建立液位
向各水夹套充水,充水后边充水边排污,排污水无杂质和颜色为合格,合格后关闭排污阀将液位控制阀LCV25、28、29分别投自动,检查溢流情况并微调整。
2.6105-JT透平试车、104-C壳侧热水清洗
中低压管网建立正常压力,即可对检修后的105-JT透平试车,具体时间由生产部与机动部安排。
合成装置建立蒸汽管网后,可向104-C壳侧加入一次水,开104-C壳侧顶部放空阀,当放空阀出水后,停止加水,在壳侧导淋接低压蒸汽胶管用蒸汽加热,去除101-E带来的溶液、杂质等,当壳侧温度加热至约100℃后,停止加热,放水。
重复一次。
排尽积水后用氮气将104-C壳侧置换合格。
3转化系统开车
3.2将脱氧槽(101-U)投入运行
(1)检查给水系统及104-J/JA、各计量泵完好备用。
(2)向脱氧槽上脱盐水,投用LCV-23并保持正常液位,开大底部排污阀对101-U进行冲洗,待排出水清澈后关闭排污阀。
(3)打开101-U顶部放空,缓慢打开PIC-16,按50℃/h速度将101-U水温升至115℃,PIC-16控制0.085MPa投自动,含氧≤7PPb合格。
(4)开联胺计量泵向101-U加入联胺,开104-J时开稀氨水计量泵调整给水PH值、视分析数据调整各计量泵冲程,联胺控制在200~300mg/L,PH≥10.5以利钝化。
3.3汽包(101-F)上水建立液位
(1)104-J暖泵合格,控制101-U给水温度与泵体水温差<30℃。
泵出口最小流量线、平衡管线全开。
(2)开启104-J使其在调速器的最低点,检查104-J123-C101-F给水线路是否畅通,拆掉101-F顶部氮气胶管,开101-F顶部2″阀,开104-J出口阀向101-F充水,控制50%液位。
适当开114-C,123-C各低点排污及管道低点排污,所有排污点轮流排污。
(3)将Na3PO4加入系统控制PH≥10.5,当PI-82压力大于0.4MPa,改V-1007放空后,加药改至正常。
(4)101-F建立液位后,101-CA/CB、103-C、123-C、114-C工艺侧导淋排水检查,严防水泡催化剂。
3.4启动一段炉引风机
(1)一段炉、辅锅检修完毕,炉膛、风道清扫干净,人孔封闭。
(2)检查引、送风机是否具备开车条件,全开一段炉窥火孔,对流段风筒,事故风门,联系仪表切除引、送风机低转速联锁。
(3)按程序启动引、送风机运行,进行炉膛置换,控制PIC-19在-5mmH2O左右。
(4)引送风机升至正常转速后,投用引送风机联锁。
关事故风门,关窥火孔,对流段风筒。
3.5一段炉、辅锅(101-BU)点火产汽
(1)检查各烧嘴考克阀是否关闭,启动辅锅、一段炉点火程序,打开V28、V29、V30,开燃料气管道各旋塞阀,将燃料气送至烧嘴考克阀前。
(2)如一段炉提前检修完成,而蒸汽系统还未建立时,可先将一段炉烟道9个中心烧嘴点燃,保持最小火。
对一段炉烟道烘炉升温,当引送风机正常运行后,根据筑炉厂家要求,按升温曲线逐渐增大燃料气量。
(3)按操作程序点燃辅锅2#主烧嘴,根据烧嘴负荷和火焰颜色调整风门挡板开度,要保证足够的燃烧空气。
(4)缓慢增加燃烧气量,控制TI1-65以40℃/h的速度,将101-F升压至0.2MPa。
当101-F产汽压力达0.2MPa时,全开101-F顶部2″放空阀。
(5)通过增加燃烧气量并适时增点101-BU烧嘴,按“汽包101-F升压曲线”规定的速度,升压时汽包壁升温速度≤50℃/h。
将汽包升压到6.3MPa。
汽包升压速度:
1小时升至0.2MPa,3小时升至0.5MPa,4小时升至1MPa,5小时升至3MPa,6小时升至6.3MPa。
(6)当101-F的PI-82达到0.4MPa时,开汽包顶部出口大阀,开V-1007放空阀,同时关101-F顶部2″放空阀,维持101-F压力不变直至101-F顶部2″放空阀全关,将101-F蒸汽倒至V-1007放空,开蒸汽过热盘管导淋、PCV13减压站、103-JAT大阀处导淋,对高蒸管网暖管。
升压过程中逐渐关小各点导淋阀。
(7)当101-F产汽压力>0.35MPa后,开连续排污阀1/4圈左右,进行排污,汽包压力0.50MPa<
PI-82<
1.0MPa时,开156-F顶部与LS管网连通阀,投用LIC-21液位控制在30~50%。
根据炉水分析数据,控制2002-LJ的加药量及炉水排污量大小。
汽包升压期间,锅炉系统各间断排污,每两小时进行一次,每个排污阀开2分钟左右。
(8)根据高蒸过热度逐步增点一段炉烟道烧嘴,过热烧嘴;
炉顶烧嘴每排点一个,按梅花形分布,控制小火焰,防止火焰舔到炉管。
3.6并汽
(1)当汽包升压到6.3MPa,TI85A>TI1-41为50~80℃时可将高压蒸汽并入中压蒸汽管网。
现场缓慢关闭V-1007-4″放空阀,关小导淋阀的开度,总控根据汽包压力逐步缓慢打开PIC-13/B阀,保持101-F压力PI-82不变,向MS蒸汽管网并汽,多余蒸汽在PIC-25放空。
并汽后关闭高蒸导淋阀。
(2)开TIC-90的现场手动阀,及时投用TIC-90,调整温度在330~350℃。
(3)详细检查锅炉给水、锅炉水,以及蒸汽系统等各项工艺指标并调整至规定范围内。
3.7一段炉干烧
(1)增点一段炉顶部烧嘴至20~30个,升温速度按50~60℃/h进行,以过渡段烟气温度TI1-68~71的平均值为准。
增点炉顶烧嘴原则是小火焰、多烧嘴,基本要求是保持火焰和热分布尽可能地均匀。
TI1-68~71平均值升至350~400℃时结束干烧,进行蒸汽升温。
(2)干烧时一段炉顶烧嘴尽量控制较小的火焰、多点烧嘴、并分布均匀、严防局部超温,在干烧时不点烟道烧嘴、过热烧嘴,TI1-68~71不允许超过430℃。
3.8高变蒸汽升温、一段炉蒸汽升温、脱硫升温
(1)并汽结束后,全开高变进口V-35放空阀,拆除氮气胶管,开高变底部中压蒸汽升温阀,控制FI54在4~5t/h,尽可能降低高变床层背压,以减少冷凝水的产生量,103-C、104-C管程导淋全开排水,待完全干燥后关闭。
(2)当TI1-68~71达到350~400℃时,全开一段炉八排导淋,101-CA/CB工艺侧导淋,全开TCV10,SP39开度5~10%,开FCV2向一段炉投蒸汽11t/h,控制TIC501以60℃/h的速度上升,并同步逐渐增加蒸汽量,在TI1-85、90达400℃前,将FIC-2加到47t/h以上。
101-B、101-CA/CB工艺气导淋排汽干燥后,管排温度在400℃以上时关闭导淋,上好管排导淋堵头。
(3)当TI1-85、90温度达350℃左右时,控制10~15℃升温速度匀速升温至480℃,保持TI1-65温度控制稳定,汽包液位控制40%并稳定,FIC-2稳定在47t/h,PI-826.3~6.5MPa左右,保持以上条件稳定,密切注意PDI4001,PDI4002的值变化情况。
辅锅负荷不要太高,汽包液位要稳定,以防废锅发生逆循环。
(4)若TI1-85、90达530℃废锅仍没循环,降温度至300℃(TI1-85/90),重新升温。
(5)循环建立后,再以50-60℃/h的速度将TIC-501提至760℃。
准备投料还原。
同时通知分析取样分析高蒸,从分析数据判断是否是正循环,若产生逆循环,同样按没有建立循环情况处理。
(6)当101-CA/CB工艺侧导淋排汽完全干燥后,高变床层上部温度大于170℃时停高变升温蒸汽,倒V35放空至PCV4放空。
在蒸汽升温过程中要严防对流段盘管超温,根据温度情况,适当灭烟烧或过热烧嘴。
倒至PCV4放空后,通知机修人员对103-C、104-C封头螺栓热紧。
(7)当蒸汽升温开始后,即开始脱硫升温,FIC1量逐步加至8000Nm3/h,升温速度按30~40℃/h,最终将109-DA/DB床层温度升至350~360℃,通知分析脱硫出口气取样,脱硫出口硫含量合格后,安排对低变天然气升温。
(8)为防止蒸汽升温时催化剂局部过热,要求尽量多点火嘴,均匀升温,一段炉16点管排温度在升温末期控制在740~770℃之间,蒸汽升温后期逐渐101-B火嘴逐渐全点。
3.9一段炉化工投料
当达到以下条件时,一段炉可以进行化工投料:
(1)TIC501温度达到760℃
(2)FIC2≥47t/h
(3)109-DA/DB脱硫床层达350℃以上,且原料气总硫含量<0.2mg/L,FIC18000Nm3/h
(4)脱硫出口压力大于FCV2阀后压力0.1~0.2MPa
当达到以上条件时,主控联系一段炉顶部现场人员将剩余烧嘴全点,联系脱硫现场逐步开脱硫至一段炉切断阀(此时若低变正在天然气升温,以FI1003为参考值),逐步关脱硫放空阀,101-B投料后,主控及时调整101-B燃烧气量,TIC501温度要尽量保持平稳,控制在760~780℃。
用FIC-1控制,进一步加量,当FI1003加至8000~10000Nm3/h,水碳比控制在3.5~3.8,PIC4提至2.0MPa。
投料后,一段炉炉管温差和烧嘴专人负责调节。
投料后将SP39开度开至30~50%,以免造成压差过大,同时尽量提高高变进口温度。
一段炉投料后加强对103-C、104-C处的检查,如有明显泄漏,及时汇报。
3.10二段炉加空气
(1)在一段炉蒸汽升温时,安排101-J联锁调试、暖机暖管,切除101-J低转速联锁,101-J具备开车条件后按升速曲线升至5800rpm,主控与现场配合关闭V22、V23,气体在FIC-4放空。
继续101-J升转至6500rpm,101-J正常运行后投用101-J联锁。
(2)当一段炉投料稳定后,TIC501760℃,二段炉TI118温度大于700℃,101-J出口压力高于PIC40.3MPa,开SP3副线阀1~2圈,向二段炉加空气,待TI-118有明显温升后,逐渐将SP3副线阀全开,再逐渐开SP-3,关闭SP-3副线阀。
(3)103-D床层温升速度控制60~80℃/h,加空气时注意,如103-D加入空气后无明显温升,立即切除空气,将TIC-501温度稍提一点重新加入空气。
空气加量不能过大,防止烧坏催化剂,TI-85/90≤1003℃。
加空气过程中,根据TIC10温度,逐步将SP39全开。
4、低变及低变保护床升温
(1)当脱硫升温合格后,先对低变保护床升温,拆除低变氮气胶管,关闭MOV31,全开MOV3,MOV30,开脱硫出口至172-C天然气阀门,开FI58处升温阀,缓慢向104-DG充压,至0.2~0.3MPa,开104-DG出口放空阀,调整FI58流量至6000~8000Nm3/h,若此时一段炉已经投料,调节要缓慢,要保持FI1003的流量稳定。
升温速度控制在30~40℃/h,当床层温度升至200℃时结束升温,在升温期间可逐步开升温天然气去一段炉燃料气阀门,将低变升温天然气回收一部分,降低消耗,在回收操作时调整要缓慢,防止造成一段炉温度及一段炉燃料气压力大幅波动,保持PIC2开度在10~20%之间。
(2)低变保护床层升温结束后,按相同方法将低变床层升至200℃,升温结束。
逐步将低变升温气倒为放空,再切除,防止引起一段炉波动。
切除过程中逐步降低FIC1的量,保持FI1003的流量稳定。
5、脱碳系统建立循环
(1)开172-C至101-E充压管线,将101-E压力充至2.0MPa。
(2)按程序开接力泵,开107-JT,开101-E出口大阀,开常压泵建立脱碳系统正常循环,FI5流量控制在760~780m3/h,通过LCV4/4A,FCV101A/B调节各塔液位。
(3)开MOV6提高102-EA/B底部温度,关小108-C循环水阀门,控制101-E贫液进口温度在50℃左右。
若各塔液位偏低及溶液总胺浓度过高,可适当向系统补充脱盐水。
(4)当高变床层温度达到400℃以上,即可将工艺气导入脱碳系统。
开SP5副线阀、MOV9副线阀,开137-C进口大阀均压,待系统压力平衡后,全开SP5、MOV9,关闭SP5副线阀、MOV9副线阀,当PIC4至PIC5之间压力平衡后,将PIC5设定值低于PIC40.2MPa后投自动,逐步将PIC4的放空气倒至PIC5放空。
(5)当脱碳系统导入工艺气后,用锅炉给水淬冷水控制TIC19温度在175~180℃,关闭MOV6。
此时安排专人密切注意102-F液位,当102-F建立正常液位后就地排放清澈后,改送158-F并送至103-E,按开车程序开低压汽提系统。
(6)开106-J淬冷水泵,将TIC19淬冷水倒为工艺冷凝液淬冷水。
6、高变气串低变
当高变出口气CO<1.5%,高变床层温度在400℃,工艺气已串脱碳并在PIC5放空,低变床层温度在140℃以上,即可将低变串入系统。
(1)检查低变系统电动阀阀门位置是否正确,放空阀及导淋阀是否关闭。
(2)开SP4副线阀向低变充压,当低变系统压力与系统压力平衡后,全开SP4电动阀,关闭SP4副线阀,全开低变出口大阀及MOV1电动阀。
(3)关闭SP5,此时投TIC281、TIC111淬冷水,控制低变及低变保护床进口温度,待温度稳定后投自动。
(4)调节119-F、160-F的液位在指标范围内。
(5)在低变串入系统时,开104-DA/DG导淋排水,确认无积水后关闭。
7、串甲烷化
当101-E出口CO≤1.0%,CO2<0.2%,可以串甲烷化。
串甲烷化前拆除氮气胶管。
(1)全开MOV12,全开V3阀,开甲烷化进口阀副线阀,对甲烷化炉充压,充压速度0.2MPa/min,待PIC5与PIC6压力相等后,全开甲烷化进口大阀,关闭其副线阀。
(2)将MCV12手动开5~8%,打通114-C锅炉给水流程,对114-C预热。
(3)缓慢开PIC-6,逐渐关PIC-5,将系统工艺气导至104-F顶部放空,用TIC-12控制106-D升温速度,在200℃以前按80~100℃/h,200℃以后按60℃/h,一直升至280~290℃。
(4)在导气的过程中,逐步开大MCV12,控制114-C锅炉给水出口温度在220~240℃。
当甲烷化床层温度达290℃以上,并有10~20℃的温升,通知甲烷化出口气取样分析。
(5)104-F有液位后,用LCV8投自动控制。
(6)甲烷化正常后,前工段逐渐加负荷,FIC1加至23000Nm3/h,逐渐将高蒸流量提到190t/h,为103-J开车做准备。
8、冷冻系统开车
(1)105-J检修完毕,开200-J,通过FCV1502副线及开工引氨管线向109-F引氨,109-F液位达85%停止引氨。
冷冻系统充压至0.05MPa,105-J建立密封油。
检查冷冻系统有无泄漏。
(2)继续向冷冻系统充压至0.35MPa,在冷冻系统开车过程中,如109-F液氨不足可再次引氨以满足系统开车需要。
(3)全开FCV9、10、11,切除105-J低转速联锁,切除密封油差压低联锁。
在二段炉加空气时105-JT可预先安排暖管,节约开车时间。
如105-JT拆开检修则按程序做超速脱扣实验,合格后将联轴节连上。
(4)105-J按程序冲转,按升速曲线逐步升至5600rpm,期间注意控制110/111/112-F闪蒸槽压力与温度,105-J升至5800rpm后逐渐关小FCV9、10、11防喘振阀。
(5)105-J稳定后,向160-CA加氨,降低104-F进口温度。
投用105-J联锁。
(6)开LCV15,建立110-F液位,为129-C加氨做准备。
9、合成系统开车
9.1103-J开车
(1)拆掉合成系统氮气胶带,检查相关阀门阀位是否正确。
当甲烷化出口微量小于10ppm,即可向103-J段间充压。
(2)启动201-D分子筛顺控程序,选择分子筛在停车前所处步骤并投半自动,打开201-D进出口阀,201-F进出口阀,与103-J一起充压。
(3)当103-J段间压力充至0.3~0.5MPa时,建立103-J密封油系统。
全开FCV7、FCV8、MCV22。
切除103-J低转速联锁。
(4)按程序103-J冲转,按升速曲线逐步升至8800rpm,期间逐步关小PCV13/13B,关小TIC90减温水。
103-J升至8800rpm后将103-JBT的手阀全开一个,注意转速的变化,逐步将103-J转速升至9500rpm。
(5)向129-C加氨,PIC10控制压力0.35MPa。
(6)103-J运行正常后,投用103-J联锁,投用水碳比联锁。
9.2合成塔床层升温
(1)合成塔充压前检查各点塔壁温度是否均大于5℃,否则按合成装置原始开车程序进行暖塔。
(2)开SP13″副线向合成系统充压,充压速度0.6~0.7MPa/10min,当合成塔出口PI253B压力与PI80压力值小于0.3MPa,可全开SP1,关闭SP13″副线阀。
(3)关闭105-DA/DB进口大阀,关闭105-DA/DB升温阀,开105-D升温阀3~5圈,开V-17-2″放空阀,开PIC541,MV25开度10%,建立FI62流量43000~45000Nm3/h。
(4)按操作规程,102-B点火升温,控制105-D床层升温速度,按30~50℃/h进行升温,当第一床层上层温度达到290~300℃时,催化剂开始合成反应,逐步开SP33前球阀,逐步关V-17-2″放空阀,关PIC541,增大循环量。
(5)在合成塔升温的同时,冷冻系统逐渐建立111-F、112-F的液位,关闭致冷阀。
当106-F液位逐渐上涨,及时开LCV13A/B前后球阀,投用LIC13,投用LIC12,PIC33,逐步将各指标调整至正常范围内。
(6)当112-F液位正常后,开109-J向氨罐送氨。
(7)当105-D能够维持自身热平衡后,逐步将升温气导至105-DA/DB,按同样方式升温。
当105-DA/DB能维持自身热平衡后,逐步减火,最后停102-B,关闭102-B进口大阀,关闭合成塔升温阀。
(8)当合成塔105-D升温阀关死后,用测温枪侧升温阀阀后温度,微开MIC131%,每隔3~5分钟,开大1%,最后按控制床层进口温度正常调节。
(9)在合成塔升温过程中,逐渐关小FCV7、FCV8、MCV22,直至MCV22全关,FCV7、8投自动。
当SP33前球阀全开后,关闭V-17-2″放空阀,将PIC541放空倒至MCV18。
10、当脱碳系统正常运行后,根据调度指令开121-J向尿素装置送二氧化碳;
当合成装置稳定出氨后,根据调度指令,开161-J向尿素供氨。
11、驰放气回收装置开车
驰放气回收装置经检查具备开车条件后,关闭氮气阀门,按操作规程正常开车。
11.1氨回收系统建立正常循环。
(1)按操作规程向V803送脱盐水,开P-801向K-801送水建立40%液位,暂停送水。
开FCV2000,开PV801副线阀将K-801充压至4.8~5.0MPa。
继续向K-801送水,开LV802将K-801溶液压至K-802。
(2)当E-804建立50%以上液位,TCV803阀前导淋排汽干燥后,逐步开大TCV803,加热E-804,投用E-810,注意E-804冷凝液出口阀逐步开大,不要全开,防止中蒸串汽至E-810引起E-810安全阀起跳。
(3)将PIC822设定2.45MPa投自动,开LV805将E-804溶液返回V-803,氨回收系统建立循环,FI803流量控制在1.6