数控插补软件设计文献综述格式1Word文档格式.docx
《数控插补软件设计文献综述格式1Word文档格式.docx》由会员分享,可在线阅读,更多相关《数控插补软件设计文献综述格式1Word文档格式.docx(11页珍藏版)》请在冰豆网上搜索。
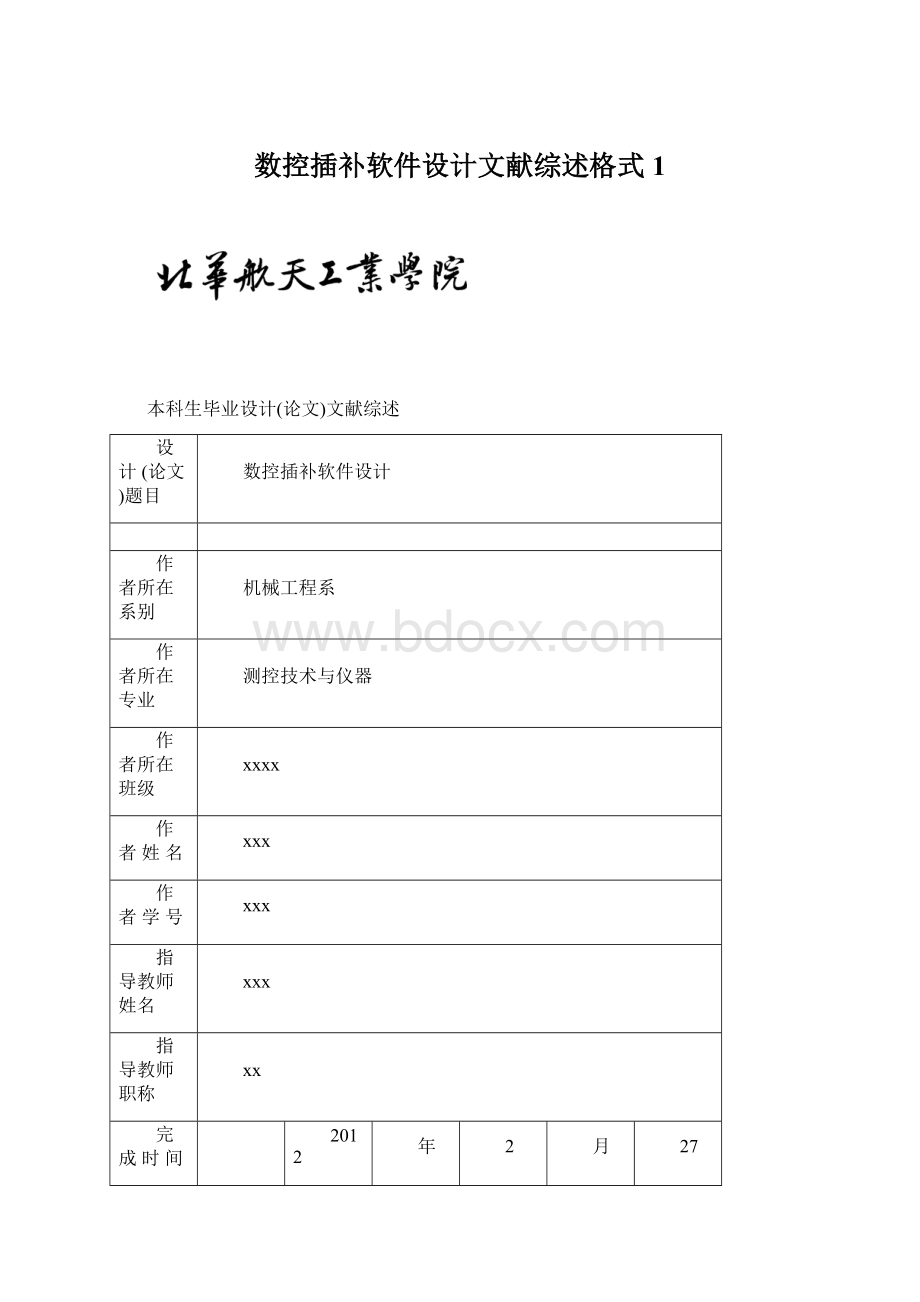
文献综述作为毕业设计(论文)答辩委员会对学生答辩资格审查的依据材料之一。
2.文献综述应在指导教师指导下,由学生在毕业设计(论文)工作前期内完成,由指导教师签署意见并经所在专业教研室审查。
3.文献综述各项内容要实事求是,文字表达要明确、严谨,语言通顺,外来语要同时用原文和中文表达。
第一次出现缩写词,须注出全称。
4.学生撰写文献综述,阅读的主要参考文献应在10篇以上(土建类专业文献篇数可酌减),其中外文资料应占一定比例。
本学科的基础和专业课教材一般不应列为参考资料。
5.文献综述的撰写格式按毕业设计(论文)撰写规范的要求,字数在2000字左右。
文献综述应与开题报告同时提交。
毕业设计(论文)文献综述
摘要
插补控制功能是数控制造系统的一个重要组成部分,是数控技术中的核心技术。
它的性能直接代表制造系统的先进程度,它的好坏直接影响着数控加工技术的优劣,
是目前数控技术急需提高和完善的环节之一。
本论文首先对数控技术的发展史进行了概述,介绍了数控装置的组成和工作过程
其次,在分析传统基准脉冲插补、数据采样插补算法的基础上,着重介绍了数控技术插补原理然后,在软件技术方面详细地分析了逐点比较法、数字积分法、最小偏差法等实用插补算法的组成和特点,最后对数控机床技术做了展望。
关键词:
数控机床,插补,数控装置
Abstract
Controlofinterpolationisanimportantcinstituentinthenumericalcontrolmanufacturesystem,itsperformancedirectlyrepresentsthelevelofadvancedmanufacturesystem.InterpolationmoduleisthecoretechniqueinNCtechnolgy.ItsqualitywillaffecttheabilityofNCsystemdirectly,anditisthemaintachethattobeimprovedandcompletedindireneed.
Atfirstthepapersimplyintroducesnumericalcontroltechnology'
sdevelopmenthistory.Secondly,afteranalyzingthetraditionpulseinterpolationandthedatasamplinginterpolation.Afterwards,asforsoftware,structureandfeaturesofutilityinterpolatingalgorithm,suchaspoint-to-pointcomparingmethod,DDAmethodandminimumdeviationmethod,areanalyzedindetails.Finally,bringforwardsomehopeaboutthissubject.
KeyWords:
Numericalcontrolmachinetool,Interpolation,Numericalcontrolunit
1.1引言
机床工业是制造业的基础。
机床是生产各种技术装备的工作母机。
它性能的好坏,直接决定着其它技术装备的质量。
而技术装备的性能高低和水平优劣,则直接影响着国民经济各生产部门的产品质量、生产效率和经济效益。
所以说,在国民经济的发展之中,提高机床的各部分性能,占着基咄性的重要作用。
数控技术的问世,使机械加工进入了自动化的时代。
它解决了传统方式难以解决的复杂零件的制造问题,改变了以往机械加工中的周期长、效率低的局面,能充分适应多品种、小批量的现代生产方式,从而大大提高对现代化工业和军事装备需求的能力。
因此,数控技术使得机床性能产生了“质”的飞跃,极大地推动了制造业的发展,成为现代制造技术中的基石。
在世界著名企业中,数控机床在生产设备中的比例不断提高,如美国波音公司中的数控机床达到约90%,GE公司达到约80%,日本在1990年的时候,机床的数控化率已经为80%。
它的制造能力高度发达,无不在于其数控技术的高度发展而形成的强大的自动化制造手段。
我国是一个机床生产大国和应用大国,虽然目前研究和使用数控技术的研究机关和厂家不少,并且取得了长足的进步,但是与世界上发达国相比,差距仍然很大,数控技术的研究应用水平还很低。
这些都严重制约着我国制造水平的提高。
高性能的数控设备依赖进口,不仅代价昂贵而且受到技术限制,有时因为经验和认识上的不足,还会受到很大损失。
所以发展民族数控事业,是迫在眉睫的大事。
国家在近几个“五年规划”中,都把数控技术的研究列为重中之重。
1.2数控技术的发展历程
从1952年诞生世界上第一台数控铣床开始到现在,数控技术的发展大致经历了两个阶段和六个时代[1一4]。
1.2.1NC阶段
数控可以说是军备竞赛的产物。
1948年,美国密执安州拉弗斯城帕森公司的帕森(JohnC.Parson),为了精确地制作出直升飞机叶片的样板,首先设想出用电子信号来控制坐标锁定的想法。
限于当时的电子技术水平和计算机技术水平,为了实现这种想法,在MIT的协助下,经过约三年的努力,于1952年成功研制出采用电子管、继电器和模拟电路构成的三坐标连续轨迹控制铣床的试验样机,通常称之为第一代数控机床(NC)。
此机床的伺服机构采用一台控制用的小伺服马达改变液压马达斜盘角度以控制液动机速度。
其插补装置采用脉冲乘法器。
这台NC机床的研制成功标志着NC技术的开创和机械制造的一个新的、数字控制时代的开始。
随着电子器件的发展,NC阶段的数控系统经历了三个时代:
第一代数控:
1952一1959年采用电子管构成数控系统。
第二代数控:
从1959年开始采用晶体管构成数控系统。
第三代数控:
从1965年开始采用小、中规模的集成电路。
至此,数控技术在工业发达国家进入了应用阶段。
以上所述的三代数控系统,机床的各项功能控制,都是由硬件逻辑完成的,因此称它们为“硬线”数控(亦即NC)。
NC一经设计之后,就无法进行更改,而且电路复杂,难于编程,限制了其进一步的发展和应用。
1.2.2CNC阶段
到二十世纪七十年代,通用小型计算机开始成批生产,其性能特别是运算速度比原来有了大幅度的提高。
因此用它来做数控系统的核心部件成为了可能。
从此数控技术也进入了计算机数控(CNC)阶段。
1970年,在美国芝加哥机床的博览会上,展出了由小型计算机为核心的计算机数控系统(CNC),标志着数控系统进入了以计算机为主体的第四代。
至此,机床功能由原来硬件逻辑实现改为现在由软件来实现,称之为“软连接”系统。
软件的灵活性,极大地推动了CNC的发展。
1974年,出现了以微处理器为基础的CNC,象征着数控系统进入第五代。
微处理器的应用,进一步缩小了工作母机的体积,降低了成本,并且由于CRT的应用,简化了编程操作。
由此,CNC达到了一般企业可以接受和普及的程度。
1977年,美国麦道飞机公司推出了多处理器的分布式CNC系统,使CNC进入第六代。
其特征是大规模集成电路,大容量高可靠的磁泡存储器的应用,可编程接口和为附S用的遥控接口,控制功能更为完备,基本上完成了标准型单机系统的开发。
自1981年以来,CNC进入第七代,达到了全功能的技术特征。
其体系结构朝着柔性模块化方向发展,辅助软件发展很快,具有交互式对话编程,三维图形校验,实时多任务操作和向机床制造厂提供二次开发手段,以便使其纳入机床制造厂的丰富工艺经验。
在产品上,实现了标准化、系列化,可以按用户需求来分别扩充、裁剪,以满足各种不同层次上的需求。
目前最新型的CNC处于第八代,它的技术特征是面向高速度、高精度,成为实现柔性制造系统((FMS)、计算机集成制造系统(CIMS)、工厂自动化(FA)的基础。
当前先进的数控系统主要有日本FANUC公司的161,181系列,‘德国西门子公司的SINUMERIK850/880系列,西班牙FAGOR公司的8030,8050系列,NUM公司的NUM150,海德汉公司的TNC426,Mi1lplus系列等等。
这些公司的产品代表了当前数控技术的最高水平,所有这些系统大都具有五轴联动功能,能够控制较高的主轴转速和进给速度,并且具有丰富的图形功能和自动程序设计功能。
某些产品还具有网络功能。
1.2.3我国数控伎术的发展
我国的数控技术已有四十多年的发展历史,其间经历起步、停滞、引进和消化、开发和创新等几个阶段〔5,6〕。
从1958年起,一些科研院所、高等学校和少数机床厂开始进行数控系统的研制和开发。
由于受到当时国产电子元器件、加工工艺技术落后、部门经济等因素的制约,未能取得较大的发展,科研和生产基本处于停滞状态。
1980年开始,我国先后从日本和德国引进数控制造技术合作生产数控机床,打破了国产数控技术徘徊不前的局面。
此后,经过“六五”(1981一1985)的技术引进、散件组装,“七五”(1986一1990)期间的消化吸收、国产化,“八五”(1991一1995)国家组织的科技攻关和“九五”(1996一2000)国家组织的产业攻关,使我国的数控系统技术获得了质的飞跃,开发出一批具有自主版权的中高档数控系统。
中国珠峰数控公司的中华I型(型号CME988)采用工业PC机作为主控板(IPC486DX/33),CPU为32bit486微处理器,实现了多功能控制系统。
北京航天数控集团自行开发的航天I型(型号以SNUCgH砒)采用与通用PC机体系结构兼容的总线式、模块化、开放型嵌入式结构,构成了典型的前后结构数控系统,较好地解决了实时多过程控制。
华中理工大学开发的华中I型(NHCI)以32位工控机为硬件主体,配置了具有曲面造型与自动编程的CAD功能软件,能进行复杂曲面的造型、数控加工规划、NC程序生成、干涉检验和加工仿真,并实现了曲面直接插补功能。
此外,中科院沈阳计算所研制的蓝天I型、北京航空航天大学的CH2010也都是基于PC平台的数控系统,各具特色。
这些拥有自主版权的高档数控系统的开发成功,表明我国已经具备开发、生产中、高档数控系统的能力,打破了过去巴统禁运的限制,为我国高档数控机床的发展提供了技术支撑,在技术上和战略上都具有重要意义。
数控系统中的插补技术
2.1引言
插补模块是整个数控系统中极其重要的功能模块之一。
在数控加工中,首先根据工件设计图和加工工艺要求编写出零件加工程序,然后将其输入到数控系统中。
经过数控系统软件的译码和预处理后,根据设定参数开始进行插补运算处理,得到刀位点位置等数据。
伺服系统根据获得的数据协调控制各坐标轴的运动,从而获得所要求的刀具位置姿态和运动轨迹,加工出所要求的工件外形(1,11)。
具体而言,插补就是根据零件轮廓尺寸,结合精度和工艺等方面的要求,按照一定的数学方法在理想的轨迹或轮廓上的已知点之间确定一些中间点,从而逼近理想工件外形轮廓。
换句话说,插补过程就是对给定曲线进行“数据点的密化”过程。
插补算法的选择将直接影响到系统的精度、速度和加工能力。
在早期的数控系统中,插补过程由专门的数字逻辑电路完成。
这种用硬件实现的插补的运算速度很快,但是灵活性较差。
目前,随着计算机水平的提高,在CNC系统中,插补功能大多采用软件的方法来实现。
对插补算法的一般要求有:
插补所需的原始数据较少;
算法简单,运算速度快;
插补精度高,没有累积误差;
能控制进给速度。
2.2数控系统常用的插补控制方案
插补技术是CNC系统实现轨迹控制的基础,插补运算是CNC系统软件实现运动控制的核心模块。
它依据零件加工NC程序给定的基本数据,通过实时计算密化加工轨迹,输出各轴的进给分量,控制机床按NC程序给定的速度沿给定的加工轨迹运动。
作为数控机床实现高速、高精加工的控制核心,数控系统所具有的插补功能的多少,插补算法的优劣,一直是评价数控控制系统性能的重要指标,也直接影响着数控机床的加工质量和加工效率。
高速高精度数控系统对插补模块的性能要求更高,因为高速加工的进给速度很快,数控系统的插补周期很短(T<
lms),因而要求插补模块在很短的时间内对各轴位置进给控制做出反应〔16)。
数控系统中完成插补运算工作的装置或程序称为插补器。
根据插补器的不同结构,可分为硬件插补器、软件插补器、硬件结合插补器三种类型。
早期的NC数控系统使用硬件插补器,它由逻辑电路组成,特点是运算速度快,但灵活性差,结构复杂,成本高。
CNC数控系统多采用软插补器,它主要由微处理器组成,通过计算机程序来完成各种插补功能,特点是结果简单,灵活易变,但速度慢。
随着微处理器运算速度和存储容量的不断提高,为了满足日益增长的插补速度和精度要求,现代CNC速度系统大多数采用软件插补或硬件相结合的方法,由软件完成粗插补,硬件完成精插补。
粗插补采用软件方法先加工轨迹分割为线段,精插补采用硬件插补,将粗插补分割的线段进一步密化数据点。
粗、精插补结合的方法,对数控系统运算速度要求不高,并可节省存储空间,且响应和分辩率都比较高〔7,8)。
由于直线和圆弧是构成零件轮廓的基本线型,因此,CNC系统一般都具有直线插补和圆弧插补两种基本工种。
在三坐标以上联动的,CNC中,一般还具有螺旋线插补功能。
在一些高档CNC系统中,机警地出现了抛物线插补、渐开线插补、正弦线插补、三样条曲线插补和球面螺旋线插补等功能。
插补的方法和原理很多,根据数控系统输出到伺服驱动装置的信号不同,插补方
法可归纳为基准脉冲插补和数据采样插补两种类型。
(l)基准脉冲插补
基准脉冲插补又称脉冲增量插补或行程标量插补,其特点是数控装置在插补结束时向各个运动坐标轴输出一个基准脉冲序列,驱动各坐标轴进给电机的运动。
每个脉冲使各坐标轴仅产生一个脉冲当量的增量,代表了刀具或工件的最小位移;
脉冲的数量代表了刀具或工件移动的位移量;
脉冲序列频率代表了刀具工件运动的速度〔191。
基准脉冲插补的插补运算很简单,容易用硬件电路实现,运算速度很快。
早期的NC系统都是采用这类插补,在目前的CNC系统中,也可用软件来实现,但仅适用于与一些由步进电机驱动的中等精度或中等速度要求的开环数控系统,有的数控系统将其用于数控采样插补中的精插补。
基准脉冲插补方法很多,如逐点比较方法、数字积分法、比较积分法、数字脉冲乘法器法、最小偏差法、矢量判断法、单步追踪法、直接函数法等,其中使用较多的是逐点比较法和数字积分法。
(2)数据采样插补
随着数控系统中计算机的引入,插补运算时间和计算复杂性之间的矛盾得到了大大缓解,特别是高性能直流伺服系统和交流伺服系统的研制成功,为提高现代数控系统的综合性能创造了充分条件〔20]。
相应地,这些现代数控系统中采用的插补方法,就不再是最初硬件数控系统中所使用的脉冲增量法,而是结合了计算机采样技术的数据采样法。
数据采样法实质上就是使用一系列首尾相连的微小直线段来逼近给定曲线。
由于这些线段是按加工时间来进行分割的,因此数据采样插补又称为时间分割法插补。
一般来讲,分割后得到的这些小线段相对于系统精度来说仍然是比较大的,不能满足系统精度。
为此,必须进一步进行数据点的密化工作。
通常也称微小直线段的分割过程是粗插补过程,而后续进一步的密化过程是精插补过程。
通过二者的紧密配合即可实现高性能轮廓插补。
具体而言,数据采样插补法是将加工一段轮廓曲线的时间划分为若干相等的插补周期。
每个插补周期进行一次插补计算,算出各坐标轴的进给量,作为下个插补周期内,各坐标轴计算机位置闭环控制系统的增量进给指令。
也就是根据数控加工程序设定的速度将零件轮廓曲线按插补周期将其分割为一系列微小直线段,然后将这些微小直线段对应的位置增量数据进行输出以控制伺服系统实现坐标轴的进给。
这样边计算,边加工,一直加工到轮廓的终点。
显然,这类插补算法插补的结果就不再是单个脉冲,而是一个数字量。
所以,这类插补算法是适用于以直流或交流伺服电机为驱动
元件的闭环或半闭环数控系统的。
直线插补算法原理:
第一步插补准备,完成一些在插补计算过程中固定不变的常量的计算,例如各轴长度、直线的长度等等。
插补一段直线只计算一次。
第二步插补计算,每一插补周期计算一次,算出一个插补点的坐标并送出。
具体的算法有进给率数法、方向余弦法、直接函数法、一次计算法等等。
圆弧插补算法原理:
其基木思想是,在满足精度要求的前提下,用弦进给代替弧进给,即用直线逼近圆弧。
第一步将圆弧转化成弦段,弦段的最小长度应该满足误差要求。
第二步将弦段进行插补,计算出相应的点的坐标送出。
圆弧的数据采样插补算法主要有直线函数法、数字增量DDA法、扩展DDA法、角度逼近圆弧插补算法等等。
2.3几种常用的插补方法原理介绍
2.3.1逐点比较法
逐点比较法又称为区域判别法,代数运算法或醉步法,是早期数控机床开环系统中广泛采用的一种插补方法。
可实现直线插补、圆弧插补,也可用于其他非圆二次曲线(如椭圆、抛物线和双曲线)插补,其特点是运算直观,最大插补误差不大于一个脉冲当量,脉冲输出均匀,调节方便。
逐点比较法的基本原理是每次仅向一个坐标轴输出一个进给脉冲,每走一步都要将加工点的瞬时坐标与理论的加工轨迹相比较,判断实际加工点与理论加工轨迹的偏移位置,通过偏差函数计算二者之间的偏差,从而决定下一步的进给方向。
每进给一步都要完成偏差判断、坐标进给、新偏差计算和终点判别四个工作节拍。
(l)偏差判别判别刀具当前位置相当于给定轮廓的偏差情况,即通过偏差值符号确定加工处在理想轮廓的那一侧,并以此决定刀具进给的方向。
(2)坐标进给根据偏差判别结果,控制相应的坐标进给一步,使加工点向理想轮廓靠拢,从而减小其间的偏差。
(3)偏差计算刀具进给一步后,针对新的加工点计算出能反映其偏离理想轮廓的新偏差,为下一步偏差判别提供依据。
(4)终点判别每进给一步后都要判别刀具是否达到被加工零件轮廓的终点,若达到了则结束插补,否则继续重复上述四个节拍的工作,直到终点为止。
逐点比较法的特点[3]:
l)算法简单,便于软件实现。
2)多轴联动时,扩展困难,计算量剧增。
3)进给速度易于控制。
2.3.2最小偏差法
可以说最小偏差法是对逐点比较法的一种重大改进。
在逐点比较法中每一步只能有一个轴进给,效率较低、驱动脉冲小平稳且平均偏差较大,而最小偏差法采用了一种更加合理的脉冲输出方式。
它先定义以固定方向上插补步数较多的轴为长轴,对应的另一轴为短轴,以长轴为基准连续输出脉冲,而短轴则根据相应的判别式间或发出脉冲。
这样插补相同的一条线段,最小偏差法的插补周期数等于长轴脉冲数,而逐点比较法的插补周期数为长轴脉冲数十短轴脉冲数。
尽管最小偏差法的算法相对复杂,但多数情况下效率仍然较高。
另外在脉冲输出平稳性以及轨迹平均偏差方面,最小偏差法显示出明显的优越性。
最小偏差法的特点(14):
(l)插补速度高。
(2)算法复杂,便于实现复杂曲线插补。
(3)实时性差。
(4)进给速度不便控制
2.3.3数字积分法
数字积分法是利用数字积分原理建立起来的一种插补方法。
其插补装置叫做数字积分器,又叫做数字微分分析器,简称nnA(DigitalDifferentialAnalyzer),是一种应用广泛的插补算法。
数字积分法的基本原理可以形象的比喻为“零存整取”。
它将曲线在各轴的进给量分段收集起来,当某个轴凑够一个指定的进给量时就进给一步。
以平面曲线为例,首先规定插补步长,比如定为0.oollnln,并定义两个以插补步长为容量的存储器,然后将曲线按时间均匀分段,分段的原则是使每个时间片中曲线的增量在X、Y两轴上的投影均不大于插补步长,插补输出时的工作就是将两轴上述每个分段中的分量分别填入对应的存储器,当某个轴的存储器出现溢出时便让对应的轴输出一个脉冲,这样就把曲线离散为一系列指定步长对应的位置点,当所累加的分段增量够一个步长时就暂存在存储器里,直到累积到溢出形成一个步长,同时溢出后的余数继续用于后面的累加,只要每个分段在各轴的投影计算足够精确,那么可以认为数字积分法不存在累积误差。
上述将数据分成小段求解再累加求和的方法就是数字积分法,它与代表指定步长的存储器配合就可方便地实现任何曲线的插补点位计算。
尽管任何曲线的分段位置增量都可以通过解参数方程等形式求得,但是考虑到插补运算的实时性以及运算效率,直接通过求解曲线方程得到分段位置增量的数字积分插补方式并不常见。
常用的求分段增量的方式为速度分解法,即用当前点的速度在各轴的投影分量与时间片△t的乘积作为下段的位置增量。
在实际应用中分段时间片的选择是很重要的,它既要使最大的分段位置增量小大于一个步长,又不能设置过小而加重运算负担。
数字积分法特点:
(1)算法简单,便于软、硬件实现。
(2)多轴联动,扩展简便。
(3)进给速度便于控制。
展望
数控机床是一门综合技术,需要多项先进技术的支持。
随着先进制造技术和制造观念的更新,计算机技术、网络技术和电子技术的不断发展,数控系统将不断吸收新技术的成果,能掌握技术、操作设备的技能型人才的需求量更将日益增长,怎样将过剩的劳动力转化为先进的生产力,变成高素质的技能性人才,把丰富的人力资源转化为人才资本,为各支柱产业的技能操作人员快速成长创造条件,不仅是各级政府需要解决的当务之急,也是教育需要面临的重大职责。
数控综合实训台的研发与使用对提高技能操作者的操作水平,加快技能操作人员的培训速度有极大的帮助,也为教育的发展增添了新的动力。
)C4E#r*c6s0?
6?
(q
参考文献
[1]叶伯生等.计算机数控系统原理、编程与操作.武汉:
华中理工大学出版社,1999
[2]周云飞.SDI插补系统的开发与研究.华中理工大学,1996
[3]毕承恩.现代数控机床.机械工业出版社,1991
[4]周延佑.国产数控系统的特点和机床数控改造的迫切性制造技术与右昧,1996:
6一9
[5]洪钟洲.创建开放式数控系统是我国制造业发展的需要.机电一体化,2000
(2):
9一12
[6]陆启建,刘明灯.数控技术的新进展.制造技术与机床,2002(5):
5一7
[7]INC技术发展的历史回顾与展望.
[8]李诚人.机床计算机数控.西安:
西北工业大学出版社,1988
[9]张吉堂,赵学良.数控原理与数控装置.太原:
华北工学院
[10]叶伯生.适应CNC系统并行处理的数据结构.机械与电子
[11]康飞,周玉杰等.数控加工过程仿真系统的研究.机电产品开发与创新增刊(虚拟制造技术研讨与
演示会),1998
[12]冯勇.现代计算机数控系统.北京:
机械工业出版社,1996,6
[13]王润孝,秦现生.机床数控原理与系统.西安:
西北工业大学出版社,1995,7
[14]薛彦成.数控原理与编程.北京:
机械工业出版社,·
1996
[15]汪木兰.数控原理与系统.北京:
机械工业出版社,2004
[16]林奕鸿等.机床数控技术及其应用.北京:
机械工业出版社,1994
毕业设计(论文)文献综