锅炉房改造施工方案.docx
《锅炉房改造施工方案.docx》由会员分享,可在线阅读,更多相关《锅炉房改造施工方案.docx(18页珍藏版)》请在冰豆网上搜索。
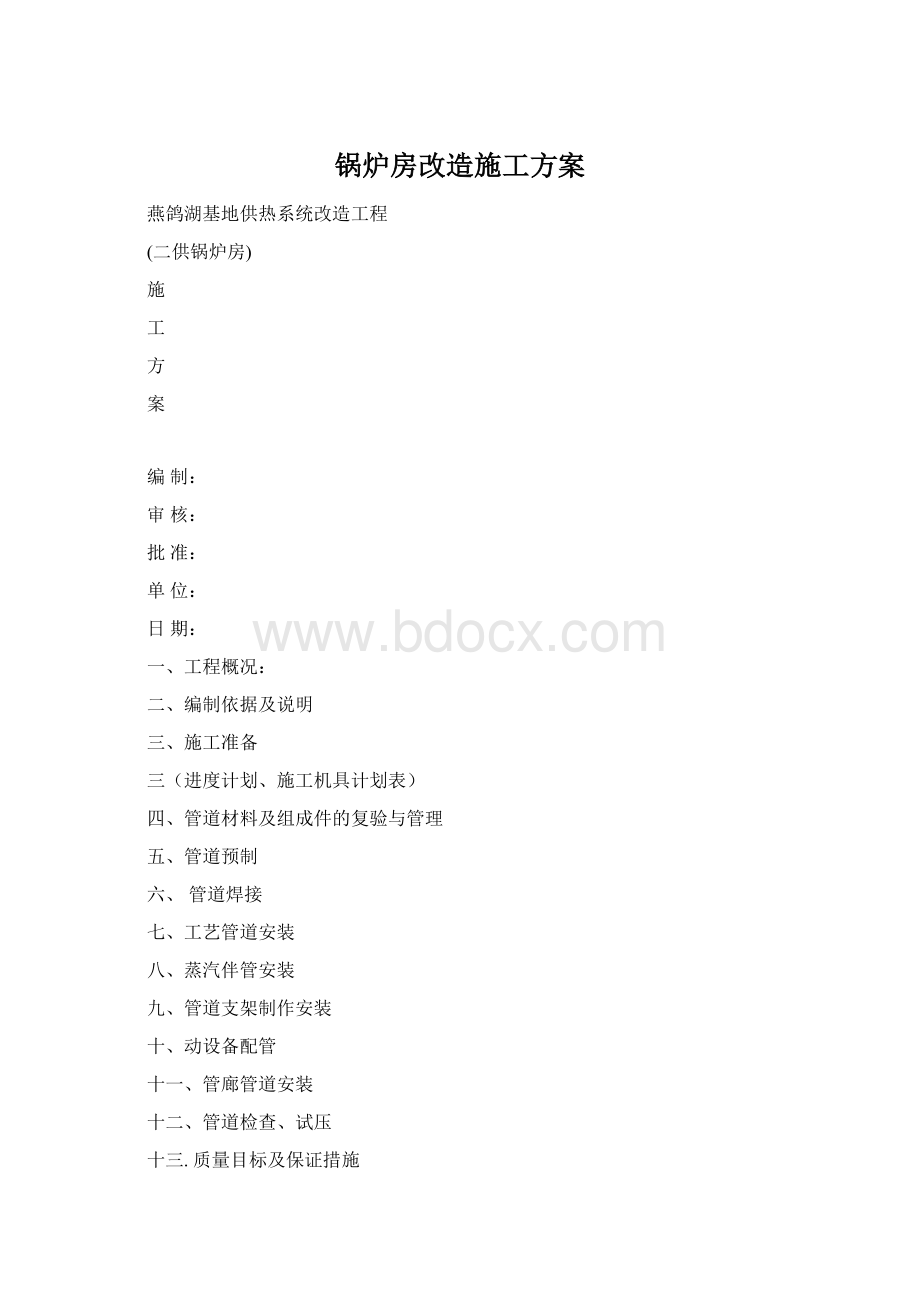
锅炉房改造施工方案
燕鸽湖基地供热系统改造工程
(二供锅炉房)
施
工
方
案
编制:
审核:
批准:
单位:
日期:
一、工程概况:
二、编制依据及说明
三、施工准备
三(进度计划、施工机具计划表)
四、管道材料及组成件的复验与管理
五、管道预制
六、管道焊接
七、工艺管道安装
八、蒸汽伴管安装
九、管道支架制作安装
十、动设备配管
十一、管廊管道安装
十二、管道检查、试压
十三.质量目标及保证措施
十四、安全、文明施工
一、工程概况:
本工程为燕鸽湖基地供热系统改造工程(二供锅炉房)工程,
工程位于银川市兴庆区石油城,主要对该锅炉房内工艺管道及设备和电气线路改造。
二、编制依据及说明
1. 锅炉房工艺管道施工设计图;
2.《石油化工有毒、可燃介质管道工程施工及验收规范》SH/T3501-2002
3.《工业金属管道工程施工及验收规范》GB50235-97;
4.《工业金属管道工程质量检验评定标准》GB50184-93;
5.《石油化工钢制管道工程施工工艺标准》SH/T3517-2001;
6.《现场设备、工业管道焊接工程施工及验收规范》GB50236-98;
7. 《压力管道安装安全质量监督检验规则》[国质检锅]200283
8. 劳动部《压力管道安全管理与监察规定》(1996版);
9.本公司企业标准《压力管道安装质量体系程序文件》。
10.《石油化工设备和管道涂料防腐蚀技术规范》SH3022-1999;
11.《石油化工设备管道钢结构表面色和标志规定》SH3043-2003。
三、施工准备
1、技术文件准备:
对设计施工单线图进行编制(应包括焊口编号、预制管段号、确定〈FW〉位置),无单线图管线需绘制管道空视图。
复核平面图与管道PID图是否存在区别,施工时流程以PID图为准,平面图为位置确定指导施工图,空视图为预制、安装尺寸图,所有图应以设计院PID图为基础对施工作业组进行技术交底(管道等级、材质、规格、技术要求、质量要求、安全、环境要求),编制施工计划。
2、施工材料准备:
按照施工合同与招标文件关于材料供货范围确定,由业主提供的材料,在业主方材料到货检查合格后,向业主申请领用,运至施工现场;由施工单位提供的材料(包括消耗材料),提出申请计划,采购到位。
甲供材料主要包括钢管、阀门、弯头、螺栓、垫片、法兰、管帽、三通等管件和管道设备;乙方主要供应给排水的铸铁管材料。
所有材料必须有质保资料,并按规定的检验标准进行检验,在报验后方可进入现场,保证合格使用。
3、施工人员准备:
根据现场施工条件,管道安装计划需用人员详见附表一(人力计划表)。
4、施工机具准备:
根据现场施工条件,管道安装计划需用设备计划详见附表二
三(进度计划、施工机具计划表)。
四、管道材料及组成件的复验与管理
1、材料进出库及检验:
⑴、所有材料出库前业主方库房应必须对其外观、数量、规格、尺寸、型号等进行检查、核对钢号、标准号及炉批号(与产品合格证明书对照),应符合设计要求的规范检验规定,如果有问题,不能发放、领用。
领用后的材料必须按规定自检如不合格应通知业主供货单位进行退换。
生产压力管道材料的厂家应持有《压力管道元件制造单位安全注册证书》;
⑵、只有经过复验合格的管材管件才能进入我公司材料堆场和库房,并按业主管道材料规定标识内容作好标识:
⑶、按要求将材料向监理工程师报验,经其同意后才能用于施工。
⑷、所有管子及管道组成件出库经检验合格后,按照规格摆放整齐。
⑸、对小管件,按管件的标准、材质及规格型号分类摆放在货架上,并挂牌。
⑹、管道材料的领用和发放执行业主及我公司项目设备材料部有关规定;
⑺、对各施工班组实行限额领料,供应严格按照单线图(结合管线号)发料。
2、管道使用替代材料应符合业主要求的《施工现场中的设备材料代用导则》(SHSG-035-89)的规定;
3、焊条或焊丝的使用应遵守本工程现场焊接材料管理规定;
4、阀门要求外观、尺寸、型号符合规范和设计要求,工作压力及性能必须符合设计要求,壳体外表应平滑、洁净、无砂眼、裂纹等缺陷;阀门开关灵活,指示正确,并具有合格证(包括阀门试验合格证)阀门铭牌上应有设计文件上所规定的材料编码。
按本标段业主招标时及合同中规定,所有阀门均由独石化公司供应处试压检验合格后,才发放给施工单位,并出具试验合格记录。
因此,阀门在现场就不必进行压力试验。
阀门检验合格后进入现场按规格、型号分类堆放,领用时按阀门铭牌上的材料编码按单线图进行核对。
5、合金钢管道组成件经光谱分析或其他方法对材质进行复查,并做标识。
合金钢阀门的内件材质应进行抽查,每批抽查数量不得少于1个。
6、现场管道材料控制组织体系
五、管道预制
管道预制必须严格按照SH/T3517-2001的要求进行,预制管道前必须认真核对管道平面布置图、详图、管段图,以避免造成不必要的返工。
1、管子下料
⑴、下料应严格按设计单线图进行,切割前材料尺寸应仔细核对。
⑵、下料时应根据管子长短合理排料,减少浪费。
对数量少,管径大,管壁厚及其它特殊材质管道,应先整体排料再下料,严格控制管子的用量,对100mm以上的切割余量不能作为废料处理,应按材质登记保管以便备用。
⑶、切割后的管材标识若被破坏,应在剩余管材上复制原有标识。
材料标识要求见附表四。
⑷、不锈钢管材必须用机械或等离子切割,其余管材可用火焰切割下料和制备坡口,切口表面应平整,无裂纹、重皮、毛刺凹凸、缩口,熔渣、氧化物、铁屑等应及时去掉。
⑸、切口端面的倾斜偏差△不大于管外径的1%,且不超过2mm。
2、坡口制备要求见下图
管道连接主要是焊接方式,坡口是焊接的首要条件,必须按规范规定进行,中、低压管道坡口型式采用V型,见下图一;高压管道采用YV(双V)型坡口,见图二。
坡口加工应平整,不得有裂纹、重皮、毛刺和氧化铁等,用角向磨光机将坡口和附近10mm范围内打磨出金属光泽。
具体坡口形式按焊接工艺卡执行。
C=2mm.P=1mm∽2mm.а=65°-75°
3、焊口组对
管道组对前,将接口内外表面25mm范围内的泥垢,油污、铁锈等清除干净,用钢丝刷或拖布将管内杂物清除。
对预制和安装时未封闭的管段,应采取措施封堵管口,避免杂物进入管道内。
4、预制允许偏差:
⑴、法兰面与管中心垂直度:
DN<100时0.5mm,100≤DN≤300时1.0mm,DN>300时2.0mm;
⑵、尺寸偏差:
自由管段±10mm,封闭管段±1.5mm
管子对口时应在距接口中心200mm处测量平直度,测量方法如图所示:
(a为偏差)
当DN<100mm时,a<1mm;DN≥100mm时,a<2mm;但全长允许偏差小于10mm。
当管子公称直径小于100mm时,允许偏差值α为1mm;当管子公称直径大于或等于100mm时,允许偏差值α为2mm;但全长的偏差值不得超过10mm。
5、管道预制件应按规定要求编号(管线号、焊口编号和焊工号)以便于质量控制和安装时查找。
6、预制完毕的管段,应将内部清理干净,并及时封闭管口,保证管内清洁。
特别指出,本工程所有管口在安装前必须全部封闭,确保预制管道进入现场100%封堵。
7、等厚管道对接焊口的组对应做到内壁齐平,内壁错边量不宜超过壁厚的10%,且不大于2毫米。
8、不等厚管道组成件组对时,当内壁错边量超过1.5mm或外壁错边量超过3mm时应照下图休整处理
9、支管与主管连接可采用跨接或插入连接,连接要求见下面图a,图b,图c,管座连接按图b执行
备注:
对(a)图(b)图g=2~3mmm≤3.2mm或0.5Tb;对(c)图g=1~3mmm≤3.2m
或0.5Tb。
10、相邻焊口间距要求
环焊缝中心面间距:
DN≥150mm不小于150mm,DN<150mm不小于管外径;
纵焊缝最近点间距应大于等于5倍管子壁厚;
支管开孔距主管环焊缝或纵焊缝的最近点间距不小于3倍主管壁厚。
11、当耳柱、支架焊接在管子上时,支架或耳柱焊口不应穿越管子或管件焊口。
.
六、管道焊接
1、奥氏体不锈钢管道焊接接头焊后应进行酸洗与钝化处理,用不锈钢专用酸洗钝化液(膏)处理不锈钢接头表面,清除焊接时产生的氧化物。
2、管道、高压切焦水管道、酸性水酸性气管道在焊后需进行热处理,处理方法见《延迟焦化装置安装工程工艺管道热处理方案》。
3、工艺管道焊接,在施焊前由焊接工程师进行技术交底,施焊时各焊接方法及焊材严格按照焊接作业指导书和技术要求实施,具体方法见焊接施工方案及焊接技术交底。
4、焊接现场应有防风、防雨雪和防寒等设施。
5、焊接前应将坡口表面及坡口边缘内外侧不小于10mm范围的油漆垢锈毛刺或镀锌层等清理干净,不得有裂纹或夹层出现,若有裂纹夹层应用砂轮机打磨后作液体渗透检验合格后再焊。
6、用于焊缝清扫的不锈钢和碳钢钢丝刷应分开。
7、焊接和焊后热处理焊接阀门时,阀门应保持半开状态。
8、不得在焊件表面引弧或试验电流,若有电弧擦伤等缺陷按规定进行处理。
9、焊接时,每条焊缝应连续一次焊完,相邻两焊道起点位置应错开。
10、承插焊焊口至少焊接2层,每层焊接起点应不同。
11、焊接组对时的点固焊及固定卡具焊缝的焊接,要求同正式焊接。
12、拆除固定卡具时,禁止用榔头直接敲掉,应用砂轮机或气焊火焰去掉,火焰切割仅限于焊缝外层。
与母材接触部分用砂轮机打磨去除,若有缺陷应作渗透检验合格后修复。
13、管道焊接的详细规定另见《延迟焦化装置安装工程工艺管道焊接施工方案》。
14、焊接预制完的管段应标注单线图号,管线号,焊口号,将DIN日报表交焊接工程师审核,管段内清理干净后封闭所有管口,放到指定地点。
焊接完成后应及时清除焊缝表面的渣皮、飞溅,并对管道焊缝表面质量进行自检。
15、管道焊缝表面质量应符合下列要求:
⑴、焊缝表面不得有裂纹、焊缝不得有未熔合、根部未焊透等缺陷;
⑵、咬边深度不大于0.5mm,在任何一段连续为300mm长焊缝中不大于50mm;C、焊缝表面不得有局部密集气孔、单个气孔和夹渣;
⑶、管子焊接具体要求见《焊接施工方案》
16、安装切割或修改时,要保证管内清洁,及时将管内焊渣清除。
七、工艺管道安装
1.工艺管道施工,一般安装程序见下图:
2.管道安装前仔细核对管线号、图号及尺寸,检查材料标记是否正确。
检查土建基础、结构、设备管口的尺寸是否与图纸相符,检查预制管段管内是否清洁。
与管道连接的机械设备已找正合格,固定完毕,并办理交接手续;
3.动设备接口配管时,不允许任何外力加于动设备口,不得用强力组对,加偏垫或加多层垫等方法来消除接口端面的空隙、偏斜、错口或不同心等缺陷。
动设备(如泵、压缩机等)的法兰口,一定要采取保护措施(如安装石棉盲板),防止异物进入。
与泵、压缩机等动设备进出口相连部分,应设置有标记的薄铁盲板或其它硬质盲板隔离,其固定焊口应远离机器,安装工序见第十动设备安装程序。
4.管道安装与电气仪表工作靠近或交叉作业时,要采取措施保护线缆、盘柜等,以免加热或焊接等热工作进行时遭到损坏。
5.保持阀门清洁,除非是焊接阀门和对焊接阀门焊口进行热处理,阀门不允许打开。
阀兰或螺纹连接式阀门,安装时应在关闭状态下进行,焊接式阀门在开启状态下安装。
管道上仪表取源部件的开孔和焊接在管道系统组对前进行。
6.安装时注意阀门流向。
在安装前反复核对,如遇有些设计要求流向要与介质流向方向相反的阀门,必须作特殊标志,试压前进行最终检查。
7.管道支架特别是热力管线的支架和设备配管的支架,必须严格按设计要求安装。
8.管道安装时,应检查法兰密封面及密封垫片不得有划痕、斑点等缺陷。
9.法兰连接应与管道同心,并应保证螺栓自由穿入。
法兰螺栓孔应跨中安装。
法兰间应保持平行。
不得