大容量电站锅炉及辅机能耗诊断Word文件下载.docx
《大容量电站锅炉及辅机能耗诊断Word文件下载.docx》由会员分享,可在线阅读,更多相关《大容量电站锅炉及辅机能耗诊断Word文件下载.docx(15页珍藏版)》请在冰豆网上搜索。
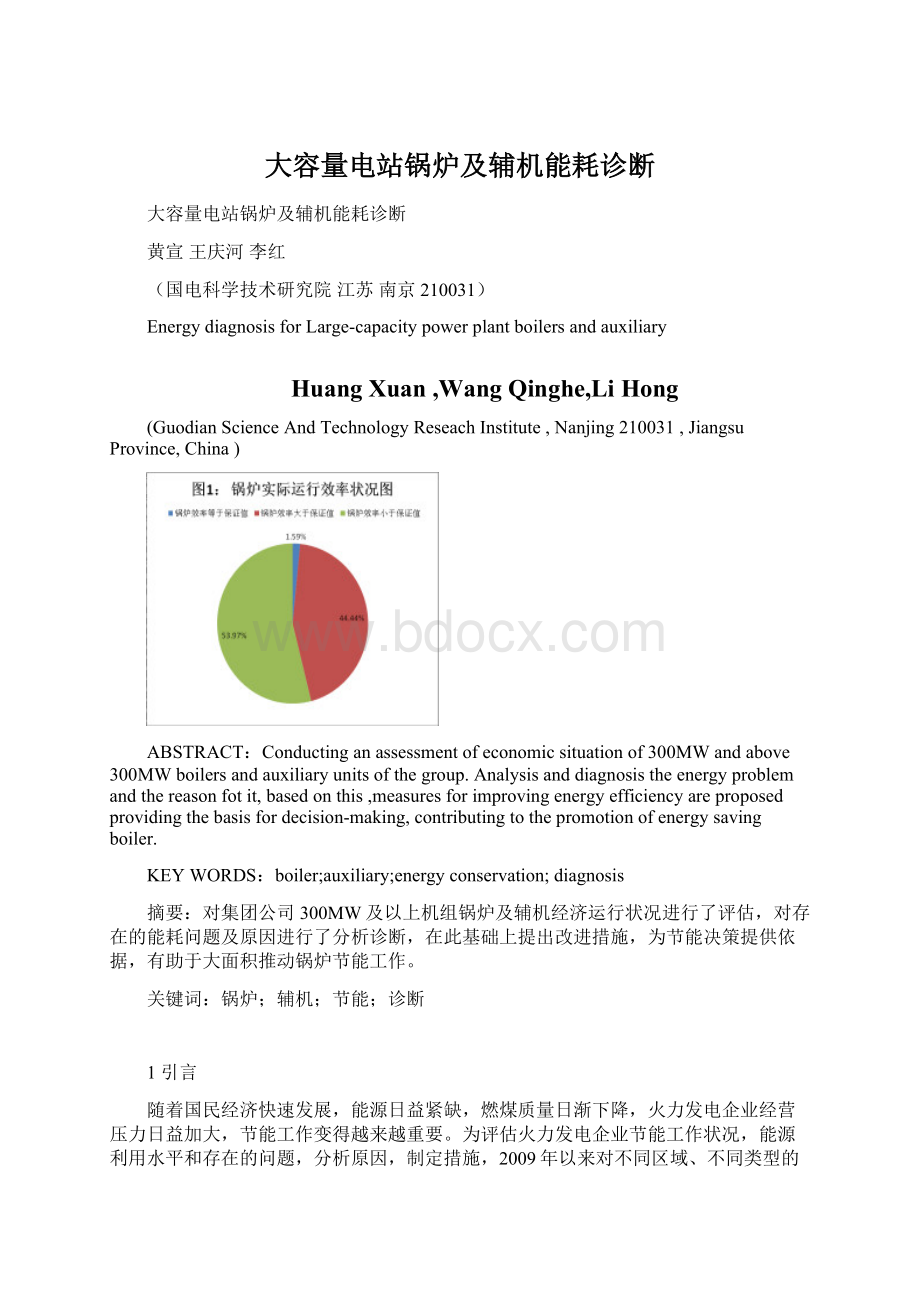
效率低于保证值的锅炉有34台,占检测锅炉总台数的53.97%,效率平均偏低1.28个百分点;
效率高于保证值的锅炉有28台,占检测锅炉总台数的44.44%,效率平均偏高0.88个百分点。
锅炉效率分布情况见图1。
1000MW超超临界机组锅炉效率平均为93.75%,比保证值偏高0.09个百分点,使供电标准煤耗降低0.29g/kW·
h;
600MW超临界机组锅炉效率平均为92.92%,比保证值偏低0.4个百分点,使供电标准煤耗升高1.52g/kW·
h,其中效率最差的比保证值偏低4.02个百分点;
600MW亚临界机组锅炉效率平均为92.05%,比保证值偏低0.77个百分点,使供电标准煤耗升高2.75g/kW·
300MW亚临界机组锅炉效率平均为91.7%,比保证值偏低0.19个百分点,使供电标准煤耗升高0.81g/kW·
锅炉效率呈现出从亚临界小容量到超临界大容量逐渐升高的趋势,体现出大容量、高参数锅炉设计的日趋完善,各类型锅炉平均效率见图2
2.1排烟温度检测诊断
排烟量一定情况下,排烟温度升高,排烟损失大致呈正比升高,排烟温度升高10℃,锅炉效率约降低0.5个百分点。
2.1.1排烟温度分析原则
排烟温度高现场简易分析方法遵循如下原则:
(1)预热器入口烟温不高于设计值,可排除蒸发和蒸汽吸热比例失衡、火焰中心升高、预热器前受热面吸热偏少等原因。
(2)同时存在一、二次风出口风温低、一、二次风温升和烟温降下降,可判断预热器换热存在不足。
(3)预热器烟气侧阻力不高于设计值,可排除预热器堵灰对换热影响。
(4)预热器不堵灰,其前烟温正常且烟温降降低幅度小于空气温升降低幅度,可以判断为预热器脏污或换热面积不足。
(5)预热器不堵灰,其前烟温正常且烟温降降低幅度大于空气温升降低幅度,可以判断预热器过风量减少(无组织风量或漏风大),但也可能同时存在预热器脏污或换热面积不足问题。
2.1.2排烟温度检测情况
按照上述原则,根据现场DCS测试条件,对62台锅炉排烟温度进行检测和修正计算,排烟温度偏高锅炉共44台,占锅炉总台数的68.75%,排烟温度平均偏高13.54℃,约使锅炉效率降低0.77%左右。
300MW亚临界锅炉,排烟温度平均偏高10.99℃;
600MW亚临界锅炉排烟温度平均偏高15.98℃;
600MW超临界锅炉排烟温度平均偏高15.83℃;
1000MW超临界锅炉排烟温度平均偏高6.69℃。
可见排烟温度偏高问题较普遍,对排烟损失影响也较大。
各类型锅炉排烟温度偏高情况见图3。
2.1.3排烟温度高原因诊断
各锅炉排烟温度偏高原因分析见表1。
表1:
排烟温度偏高原因分析表
排烟温度偏高原因
受影响锅炉台数
占排烟温度偏高锅炉的百分数(%)
预热器脏污或换热面积不足
23
52.27
预热器堵灰
17
38.64
送风出力不足,经过空预器空气量偏少,预热器空气流量偏差
14
31.82
煤质差、水分高、卫燃带布置偏多造成火焰中心高,蒸发与蒸汽吸热比例失衡、烟气量大
10
22.73
高排汽温偏高,烟气挡板调节不及时
2
4.55
因预热器脏污或换热面积不足造成排烟温度偏高锅炉有23台,占排烟温度偏高锅炉的52.27%。
预热器换热面积偏小分两种情况,一是本身设计偏小,二是实际填充偏少。
预热器堵灰造成排烟温度偏高锅炉有17台,占排烟温度偏高锅炉的38.64%,预热器堵灰一方面与煤质有关,另一方面与运行管理和设备维护水平有关;
因煤质差、水分高、卫燃带布置偏多造成火焰中心高,蒸发与蒸汽吸热比例失衡、烟气量大等因素,造成排烟温度高锅炉有10台,占排烟温度偏高锅炉的22.73%;
因送风出力不足,经空预器空气量偏少和预热器空气流量偏差等原因造成排烟温度高锅炉有14台,占排烟温度偏高锅炉的31.82%;
因高排汽温偏高,烟气挡板调节不及时造成排烟温度偏高锅炉有2台,占排烟温度偏高锅炉的4.55%。
可见预热器脏污或换热面积小、预热器堵灰、送风不足和无组织风量大、煤质差等原因,是造成排烟温度偏高的主要原因,既有设计问题,也涉及运行和煤种原因。
2.1.4降低排烟温度措施
降排烟温度应针对不同原因采取不同措施,火焰中心高就要考虑降火焰中心,如降低一次风速、提高一次风温、降低煤粉细度、减少上层燃烧器运行、热负荷采取正塔形分布、难燃煤种避免放在上层燃烧、喷燃器摆角尽量下摆等;
若为预热器堵灰脏污,运行中应加强的预热器吹灰,检修机会彻底清理预热器蓄热片,预热器冷端金属温度保持在烟气露点以上,避免省煤器泄漏等;
若预热器换热面积不足,并有预留空间,可增加部分换热面,或采用高效蓄热板,甚至采用前置预热器。
也可考虑将烟气余热利用于低温省煤器或供热加热器等;
若排烟温度高原因为送风量不足和掺入冷风量大,应进行送风机扩容,提高磨煤机出口风温,减少制粉系统掺入冷风量,检查消除炉膛、烟道漏风等;
若前部换热面换热不足,可适当增加吹灰,并根据具体情况调整受热面。
2.2预热器漏风率检测诊断
排烟温度一定情况下,排烟量增加,排烟损失成正比上升。
大多数锅炉预热器前氧量是基本合理的,只是个别锅炉未进行规范的氧量优化试验,因此影响排烟量的主要因素是预热器漏风率。
漏风率上升1个百分点,发电标准煤耗约上升0.15g/kw·
2.2.1预热器漏风率检测情况
预热器漏风率超标锅炉33台,占锅炉总数的47.14%,漏风率平均超标3.95个百分点。
可见预热器漏风问题较为普遍,对排烟损失影响较大。
2.2.2预热器漏风率偏大原因诊断
引起预热器漏风率偏大的主要原因一方面是动静密封间隙大,另一方面一次风压高。
间隙大的主要原因包括间隙自动跟踪不能正常跟踪、扇形板卡死不能调整、密封片磨损、吹损得不到及时维护和调整、预热器冷端腐蚀、预热器安装水平度不合格等。
一次风压高原因主要是煤质差,磨煤机出力不能满足负荷要求,为保证制粉出力,提高一次风压。
2.2.3降低预热器漏风率的措施
预热器漏风不但影响其有效换热量,使排烟损失增加,还会导致三大风机耗电率上升,甚至影响锅炉燃烧。
解决预热器漏风首先还是强化漏风治理,保证间隙跟踪,及时调整修复间隙。
为进一步提高密封水平,可采用一些较为成熟的密封新技术,如双密封、接触软密封等;
另外加强燃料管理,优化配煤掺烧试验,尽可能降低一次风压。
2.3固体不完全燃烧损失检测诊断
固体不完全燃烧损失决定于入炉煤热值、收到基灰分、飞灰炉渣可燃物及份额、石子煤热损失等,由固体不完全燃烧损失计算公式由公式可知,热值越低、收到基灰分和飞灰炉渣可燃物越高、石子煤热损失越大,则固体不完全燃烧损失越大。
入炉煤热值、收到基灰分决定于煤质,飞灰炉渣可燃物及石子煤热损失既决定于煤质,也决定于设备水平和运行方式。
2.3.1固体不完全燃烧损失检测情况
固体不完全燃烧损失偏高锅炉有26台,占锅炉总台数的41.27%,固体不完全燃烧损失平均偏大1.06个百分点,约使供电标准煤耗上升3.91g/kwh。
2.3.2固体不完全燃烧损失偏高原因诊断
各锅炉固体不完全燃烧损失偏高原因分析见表2
表2:
固体不完全燃烧损失偏高原因分析表
固体不完全燃烧损失偏高原因
受影响锅炉台数(台)
占固体不完全燃烧损失偏高锅炉的百分数(%)
热值低、灰分大引起的固体不完全燃烧直接损失
61
96.15
煤质差、灰分高使燃烧不充分;
煤质差,煤量大,磨煤和干燥出力紧张,磨煤机得不到及时维修,出力进一步降低,为保负荷一次风量高,一次风管、分离器及喷燃器通流面积相对不足,一次风速高,风温低和煤粉粗,使燃烧不充分。
21
80.77
煤质差,矸石多,制粉出力紧张,磨风环间隙大得不到及时恢复,为提出力保持高料位运行等原因,造成石子煤量大、热值高。
9
34.62
因局部缺氧燃烧
6
23.08
炉膛温度低
5
19.23
送、引风机出力不足
4
15.38
底部二次风口面积偏小,托粉能力不足,煤粉离析严重。
8.33
煤质差必然存在热值低和灰分大直接引起的固体不完全燃烧损失,这种情况占锅炉总数的96.15%。
因煤质差、灰分高,导致煤粉颗粒与氧接触面积减少,增加氧向灰颗粒内部的渗透困难,进而影响燃烧速度和强度,使燃烧不充分;
或因煤质差,煤量需求大,磨煤和干燥出力紧张,磨煤机得不到及时维修,出力进一步降低,为保证负荷而提高一次风量,一次风管、分离器及喷燃器通流面积相对不足,引起一次风速高,风温低和煤粉粗,使燃烧不充分的锅炉有21台,占固体不完全燃烧损失偏大锅炉的80.77%,是影响固体不完全燃烧损失的主导因素。
煤质差矸石多,制粉出力紧张,中速磨风环间隙偏大得不到及时恢复,为提高出力保持高料位运行等原因,造成石子煤量大,石子煤热值高,从而使固体不完全燃烧损失上升的锅炉有9台,占固体不完全燃烧损失偏大锅炉的34.62%。
因局部缺氧燃烧使固体不完全燃烧损失上升的锅炉有6台,占固体不完全燃烧损失偏大锅炉的23.08%,主要体现在“W”火焰锅炉高负荷工况加风燃烧不稳,缺氧燃烧和沿炉膛宽度方向氧量分布严重不均(中部缺氧)。
因炉膛温度低使固体不完全燃烧损失上升的锅炉有5台,占固体不完全燃烧损失偏大锅炉的19.23%。
炉膛温度低与燃煤灰分、水分大,热值低和炉膛设计容积热负荷偏低有关。
因送、引风机出力不足使固体不完全燃烧损失上升的锅炉有4台,占固体不完全燃烧损失偏大锅炉的15.38%。
送、引风机出力不足导致高负荷工况缺氧燃烧,飞灰可燃物升高。
有2台600MW超临界锅炉为四角切圆燃烧方式,由于底部二次风口面积相对偏小,托粉能力不足,造成煤粉离析严重,炉渣可燃物偏高,占固体不完全燃烧损失偏大锅炉的8.33%。
2.3.3降低固体不完全燃烧损失的措施
热值低、灰分大直接造成的固体不完全燃烧损失只能通过改变煤种解决;
飞灰、炉渣可燃物造成的固体不完全燃烧损失要根据引起的原因区别对待。
如煤粉粗、一次风速高引起的损失,可调整合理的煤粉细度,如无调整余地,可对中速磨进行增速改造,对钢球磨增加装球量或改善钢球配比,通过增加磨煤出力降低一次风速,改善煤粉细度,也可增加喷燃器喷口面积,降低一次风速;
针对石子煤量大问题,可减小风环间隙,加强磨煤机维护,及时修复磨损碾磨件,保持合理的一次风率和风温,保持合理的磨煤机料位等;
炉膛温度低锅炉可适当调整卫燃带或在适当位置喷涂隔热涂料,提高炉温;
局部缺氧可改善动力场分布,保持氧量分布均匀性,送、引风机出力不足首先要对预热器和烟风道漏风和阻力大问题进行治理,仍然不足时可考虑风机增容改造,如增速、增加叶片数等;
四角切圆燃烧超临界600MW机组锅炉底部风口面积小,托粉能力不足,可考虑增加底部二次风喷口面积。
3减温水量与蒸汽参数检测诊断
减温水量和蒸汽参数对锅炉计算效率没有直接影响,但对热力循环效率影响较大,也是锅炉经济性重要评判指标。
过热减温水若在给水泵出口引出,每10t/h约使发电标准煤耗升高0.1g/kw·
h,若在省煤器前或省煤器后引出,则对经济性影响不大。
再热减温水影响更大,每10t/h约使发电标准煤耗升高0.3g/kw·
主汽温和再热汽温每变化10℃约影响发电煤耗0.7-0.9g/kw·
h,主汽压力每变化1MPa约影响发电煤耗1.1g/kw·
3.1减温水和蒸汽参数检测情况
过热减温水偏大锅炉25台,占锅炉总数的39.68%,减温水量平均偏大57.86t/h;
再热减温水偏大锅炉33台,占锅炉总数的52.38%,减温水量平均偏大27.28t/h;
主汽温偏低锅炉18台,占锅炉总数的28.57%,主汽温平均偏低4.43℃;
再热汽温偏低锅炉30台,占锅炉总数的47.62%,汽温平均偏低7.36℃;
主汽压力明显偏低锅炉2台,占锅炉总数的3.17%。
减温水量及蒸汽参数偏差情况见图4。
3.2减温水超标原因诊断
过热减温水偏大锅炉中,有20台锅炉因喷燃器摆角或烟气挡板不能自动调整或卡死,而使过热减温水受到影响,占过热减温水偏大锅炉的80%,成为过热减温水量大的主导因素。
喷燃器摆角或烟气挡板不能自动原因主要是变形、积灰、调节迟滞性大或执行机构问题;
有16台锅炉因煤质差、一次风速高、煤粉粗,导致火焰中心升高,使蒸发吸热和蒸汽吸热比例失衡,使过热减温水偏大,占过热减温水偏大锅炉的64%,是影响过热减温水量的又一主导因素;
有7台锅炉因设计和改造不当导致蒸发吸热与蒸汽吸热比例失衡,使过热减温水偏大,占过热减温水偏大锅炉的28%;
有11台锅炉过热器面积偏大,使过热减温水偏大,占过热减温水偏大锅炉的44%;
有4台锅炉结焦,降低了蒸发吸热比例,使过热减温水偏大,占过热减温水偏大锅炉的16%;
有5台锅炉存在汽温偏差或自动调节品质差,使过热减温水偏大,占过热减温水偏大锅炉的20%。
具体原因分析见表3。
再热减温水偏大锅炉中,有27台锅炉因喷燃器摆角或烟气挡板不能自动或卡死,使再热减温水受到影响,占再热减温水偏大锅炉的81.82%;
有17台锅炉因煤质差、一次风速高、煤粉粗,导致火焰中心升高,使蒸发吸热和蒸汽吸热比例失衡,使再热减温水偏大,占再热减温水偏大锅炉的51.52%;
有16台锅炉因炉膛设计不合理或再热器面积偏大使再热减温水偏大,占再热减温水偏大锅炉的48.48%;
有11台锅炉高排温度偏高较多,使再热减温水偏大,占再热减温水偏大锅炉的33.33%;
有4台锅炉结焦,降低了蒸发吸热比例,使再热减温水偏大,占再热减温水偏大锅炉的12.12%;
有9台锅炉存在汽温偏差或自动调节品质差问题,使再热减温水偏大,占再热减温水偏大锅炉的27.27%。
个别锅炉存在再热减温水门内漏和运行方式不当问题。
表3:
减温水及蒸汽参数偏差原因分析表
指标偏差
偏差原因
受影响锅
炉台数(台)
占偏差锅炉百分数(%)
过热减温水量大
喷燃器摆角或烟气挡板不能自动调整或卡死
20
80
煤质差、一次风速高、煤粉粗,导致火焰中心升高,使蒸发吸热和蒸汽吸热比例失衡
16
64
过热器面积偏大
11
44
锅炉因设计和改造不当导致蒸发吸热与蒸汽吸热比例失衡
7
28
汽温偏差或自动调节品质差
锅炉结焦,降低了蒸发吸热比例
再热热减温水量大
喷燃器摆角或烟气挡板不能自动或卡死
27
81.82
煤质差、一次风速高、煤粉细度粗,导致火焰中心升高,使蒸发吸热和蒸汽吸热比例失衡
51.52
因炉膛设计不合理或再热器面积偏大
48.48
高排温度偏高
33.33
汽温偏差或自动调节品质差问题
27.27
12.12
主汽温低
受热面超温、爆管或为控制氧化皮生成速度而降低主汽温控制定值
55.56
炉膛偏高偏大或卫燃带布置偏少
8
44.44
喷燃器摆角不能正常调整
汽温偏差大、自动调节品质不佳或煤质差而不稳引起的汽温波动大
再热汽温低
喷燃器摆角或烟气挡板不能正常调整或调整不当
66.67
再热器面积偏小、炉膛偏高偏大或卫燃带布置偏少
46.67
12
40
受热面超温爆管或为控制氧化皮生成速度而降低再热汽温控制定额
3.3主汽温偏低原因诊断
主汽温偏低锅炉中,有10台锅炉因受热面超温、爆管或为控制氧化皮生成速度而降低主汽温控制定值,从而影响了主汽温平均水平,占主汽温偏低锅炉的55.56%;
8台锅炉因炉膛偏高偏大或卫燃带布置偏少,导致主汽温偏低,占主汽温偏低锅炉的44.44%;
8台锅炉因喷燃器摆角不能正常调整,导致主汽温偏低,占主汽温偏低锅炉的44.44%;
8台锅炉因汽温偏差大、自动调节品质差或煤质差而不稳引起的汽温波动大,导致主汽温降低,占主汽温偏低锅炉的44.44%。
具体原因分析见表3
3.4再热汽温偏低原因诊断
再热汽温偏低锅炉中,20台锅炉因喷燃器摆角或烟气挡板不能正常调整或调整不当,导致再热汽温降低,占再热汽温偏低锅炉的66.67%;
12台锅炉因受热面超温爆管或为控制氧化皮生成速度而降低再热汽温控制定额,从而影响了再热汽温平均水平,占再热汽温偏低锅炉的40%;
12台锅炉因汽温偏差大、自动调节品质差或煤质差而不稳引起的汽温波动大,导致再热汽温降低,占再热汽温偏低锅炉的40%;
14台锅炉因再热器面积偏小、炉膛偏高偏大或卫燃带布置偏少,导致再热汽温降低,占再热汽温偏低锅炉的46.67%。
3.5主汽压偏低原因诊断
主汽压力偏低主要发生在动态过程,由于煤质差,制粉出力紧张,高负荷工况增负荷过快时燃料暂时难于跟上,导致主汽压力降低,这种情况会很快恢复;
P厂2台锅炉因再热减温水波动大,使中低压缸出力增加,为保证电负荷不变,高调门关小,主汽压力上升,有时导致高旁频繁动作,为避免这种情况发生,人为降低主汽压控制值,由于降低幅度很大,对经济性影响也较大。
3.6降低减温水量、提高蒸汽参数的措施
影响过、再热减温水量的因素有许多相似之处,需要采取的措施也基本相同。
针对喷燃器摆角和烟气挡板不能自动或无法调整问题,重要的是加强维护,并坚持使用;
因煤质差导致火焰中心升高,进而改变蒸发与蒸汽吸热比例问题,除控制煤质外,就是控制火焰中心高度;
设计问题导致减温水量大,应根据具体问题进行改造,如减少受热面,减少卫燃带布置等;
炉膛结焦应解决结焦问题,如采用防结焦喷燃器、合理的空气动力场、贴壁风、运行增加炉膛风量、合理吹灰等;
烟、汽温偏差容易导致减温水量增加,对于切圆燃烧锅炉,消除烟、汽温偏差可考虑反切风,是较为有效的措施。
一般来说对冲燃烧锅炉烟、汽温偏差不大,但查评中发现部分600MW超临界锅炉烟、汽温偏差相对较大,目前原因不十分明确,需要进一步研究。
给水泵出口给水做过热减温水的锅炉,若存在一定减温水量,并不太大,经过一定核算后,可改造为高加出口给水做减温水,这样可减少减温水对经济性的影响。
汽温偏低原因中,喷燃器摆角和烟气挡板问题是首要影响因素,其摆角影响正好与减温水的调节方向相反;
爆管、管壁超温和控制氧化皮生成速度成为限制汽温提高的另一主要因素,爆管原因并不一定是超温引起,管壁超温往往是燃烧偏差和调节品质差或运行不当造成的,可以采取措施避免,超临界和超超临界锅炉氧化皮生成是必然的,只是快慢问题,重要的是防止脱落和脱落后及时带走,制造厂设计的汽、壁温应该认为是合理的,没有必要再刻意降低汽温控制值;
过、再热器面积偏小、炉膛偏高偏大或卫燃带布置偏少问题可通过受热面调整、在炉膛增加卫燃带或隔热涂料,运行方式上可采取提高火焰中心措施来解决(飞灰可燃物不能明显上升)。
4辅机耗电检测诊断
锅炉辅机主要包括磨煤机、送风机、引风机、一次风机、排粉机等。
在完成自身生产任务的同时,尽可能降低能量消耗是锅炉辅机节能研究的重点。
4.1辅机耗电率检测情况
送风机平均耗电率为0.25%,最低耗电率为0.12%,平均耗电率是最低耗电率的2.08倍;
引风机平均耗电率为0.68%,最低耗电率为0.30%,平均耗电率是最低耗电率的2.27倍;
一次风机平均耗电率为0.66%,最低耗电率为0.31%,平均耗电率是最低耗电率的1.96倍;
排粉机平均耗电率为0.64%,最低耗电率为0.40%,平均耗电率是最低耗电率的1.6倍;
磨煤机平均耗电率为0.71%,最低耗电率为0.22%,平均耗电率是最低耗电率的3.23倍。
辅机耗电率及偏差情况见图5,由此可见锅炉主要辅机耗电率仍有较大的节能空间,仍有节能潜力可挖。
4.2耗电率影响原因诊断及改进措施
4.2.1制粉系统及运行方式
制粉系统受煤质影响很大,煤质差,同负荷需要煤量大,备用磨失去备用,磨煤机磨损得不到及时维护,进一步降低磨煤出力,形成恶性循环,从而造成磨煤和一次风机电耗高,一次风率大,煤粉粗,磨煤机出口风温低和石子煤量大等问题。
这种情况的锅炉有38台,占锅炉总数的54.29%,严重影响了制粉系统、一次风机(排粉机)的经济运行,甚至影响锅炉安全经济燃烧。
制粉系统运行方式缺乏优化,致使耗电率偏高锅炉有21台,占锅炉总数的30%。
目前煤种偏离设计煤种较多,煤种变化,制粉系统应重新进行运行优化。
制粉系统运行优化对其经济运行起到重要作用,如J厂优化磨煤机钢球装载量和配比,磨煤机电流下降约45A,且出力有所增加。
排粉机、密封风机设计余量大或密封风机取气方式设计不合理(从大气去气)锅炉有21台,占锅炉总数的30%。
对制粉耗电率有一定影响。
由于排粉机和密封风机为离心风机,可进行叶轮切割。
磨煤机冷热风门内漏和卡涩在制粉系统中普遍存在,风门内漏增加了备用磨煤机的通风量和冷风参入量,甚至影响磨煤机正常维护。
风门卡涩可能影响到磨煤机出口风温或风量。
有15台锅炉磨煤机存在风门卡涩或内漏问题,占锅炉总数的21.43%。
解决风门卡、漏问题在合理选型基础上,更重要的是日常维护。
由于运行习惯,有11台锅炉磨煤机入口风门开度小,占锅炉总数的15.71%,造成一次风机耗电率升高。
可将磨煤机入口风门开到70%左右,将风门调节变为一次风机调节,由于风机调节为入口导叶、动叶或变频调节,调节效率