埋弧自动焊焊接工艺汇编Word格式文档下载.docx
《埋弧自动焊焊接工艺汇编Word格式文档下载.docx》由会员分享,可在线阅读,更多相关《埋弧自动焊焊接工艺汇编Word格式文档下载.docx(19页珍藏版)》请在冰豆网上搜索。
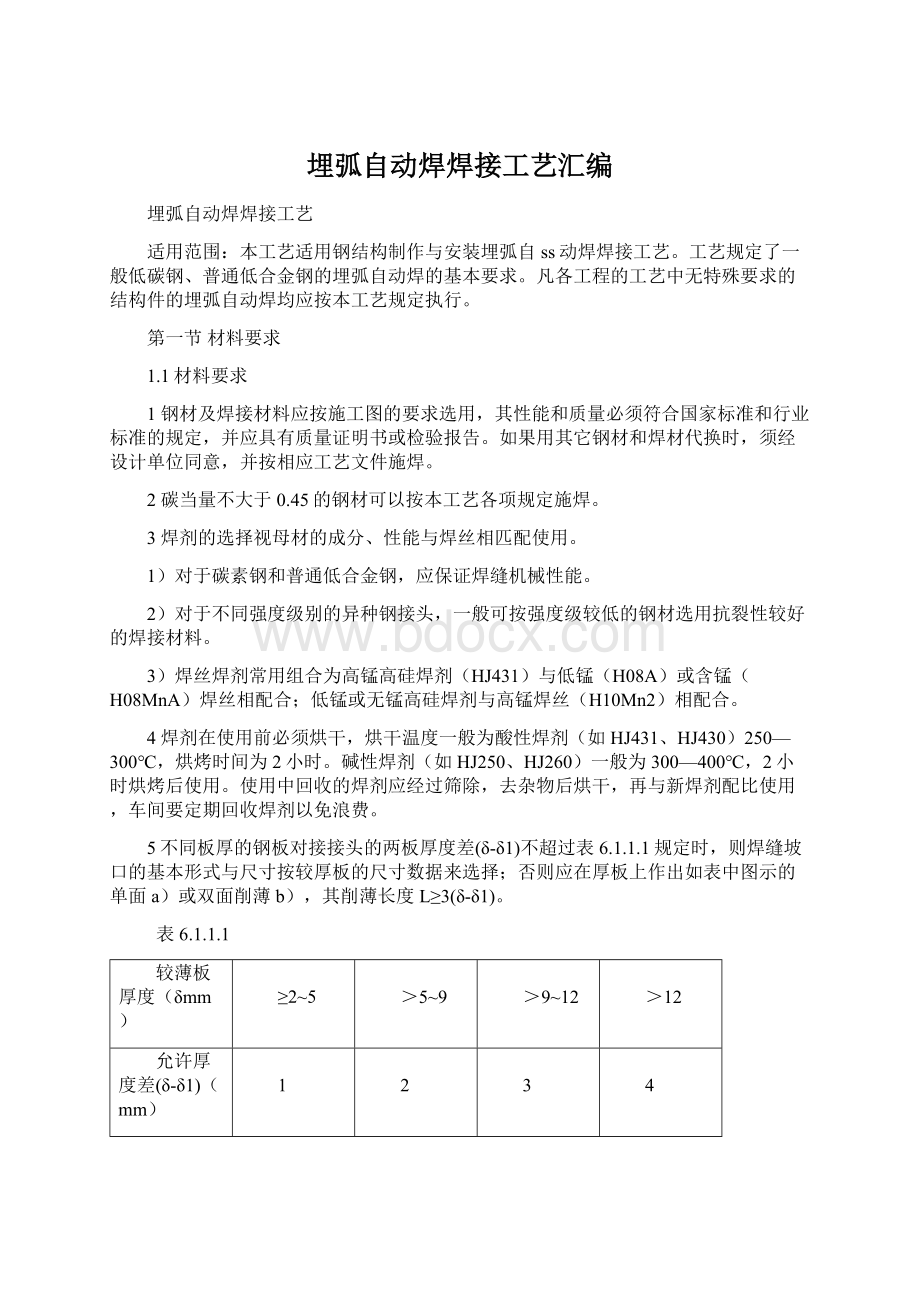
焊接滚轮架
翼缘矫正机
型钢校正
表6.2.1.2工厂加工检验设备、仪器、工具表
设备能力
超声波探伤仪
检查焊缝内部缺陷
数字温度仪
测量层间温度
数字钳形电流表
个
测量焊接电流
温湿度仪
测量空气湿度
焊缝检验尺
把
检验焊缝外观尺寸
磁粉探伤仪
检查焊缝外观尺寸
游标卡尺
钢卷尺
测量
第三节作业条件
3.1焊接区应保持干燥、不得有油、锈和其它污物。
3.2用于埋弧焊的焊剂应按照工艺确定的型号和牌号相匹配。
焊剂在使用前应按产品说明书规定的烘焙时间和烘焙温度进行烘焙,不得含灰尘、铁屑和其他杂物。
3.3焊前应对焊丝仔细清理,去除铁锈和油污等杂质。
3.4施焊前,焊工应复核焊接件的接头质量和焊接区域的坡口、间隙、钝边等的处理情况。
当发现有不符合要求时,应修整合格后方可施焊。
焊接连接组装允许偏差值见表6.3.4.1的规定。
表3.4.1焊接连接组装允许偏差值
第四节施工工艺
4.1工艺流程
拼装焊接校正二次下料制孔装焊其它零件校正打磨打砂油漆搬运贮存运输
4.2操作工艺
1.埋弧自动焊工艺参数选择
1)焊接电流的选择埋弧焊熔池深度决定于焊接电流。
有近似的经验公式可供估算:
h=kI
式中h——熔深,mm;
I——焊接电流,A;
k——系数,决定于电流种类、极性和焊丝直径等,一般取0.01(直流正接)或0.011(支流反接、交流)。
2)焊丝直径可根据焊接电流选择合适的焊丝直径,见表4.2.3。
3)电弧电压电弧电压要与焊接电流匹配,可参考表4.2.4。
2.埋弧自动焊工艺参数示例
1)不开坡口留间隙双面焊工艺参数,见表4.2.3。
2)对接接头埋弧自动焊宜按表4.2.4选定焊接参数。
3)厚板深坡口焊接工艺参数,见表4.2.5。
4)搭接接头的埋弧自动焊宜按表4.2.6选定焊接参数。
5)T型接头的单道埋弧自动焊焊接参数宜按表4.2.7选定。
6)船形T型接头的单道埋弧自动焊焊接参数宜按表4.2.8选定。
表.4.2.1不同直径焊丝适用的焊接电流范围
焊丝直径(mm)
5
6
电流密度(A/mm2)
63-125
50-85
40-63
35-50
28-42
焊接电流(A)
200-400
350-600
500-800
700-1000
820-1200
表4.2.2电弧电压与焊接电流的配合
600-700
700-850
850-1000
1000-1200
电弧电压(V)
36-38
38-40
40-42
42-44
注:
焊丝直径5mm,交流。
表4.2.3不开坡口留间隙双面埋弧自动焊工艺参数
焊件厚度
装配间隙
焊接电流
焊接电压(V)
焊接速度
(mm)
(A)
交流
直流反接
(m/h)
10-12
14-16
18-20
22-24
26-28
30-32
2-3
3-4
4-5
5-6
6-7
750-800
775-825
800-850
850-900
900-950
950-1000
34-36
36-40
38-42
40-44
32-34
32
30
25
23
20
16
焊剂431,焊丝直径5mm。
两面采用同一工艺参数,第一次在焊剂垫上施焊。
表4.2.4对接接头埋弧自动焊参数
板厚
焊丝直径
接头形式
焊接顺序
焊接参数
电弧电压
(V)
(m/min)
8
正
440-480
0.50
反
480-530
31
10
530-570
0.63
590-640
33
12
620-660
35
0.42
680-720
0.41
14
830-850
600-620
35-38
0.75
18
850
800
780-820
29-32
0.33
700-750
0.46
925
36
0.45
38
22
1000
0.40
37-39
0.62
续表4.2.4对接接头埋弧自动焊参数
24
700-720
34
0.3
900
0.27
28
820
0.30
0.25
表4.2.5厚壁多层埋弧焊工艺参数
交流
直流
600-7100
0.4-0.5
700-800
0.45-0.55
表4.2.6搭接接头埋弧自动焊工艺参数
焊脚
a
α
简图
(。
)
530
55-60
7
650
1.5-2.0
600
780
32-35
表4.2.7型接头单道埋弧自动焊焊接参数
送丝速度
b
600-650
0.7
0.67-0.77
2-2.5
≤1.0
60
650-770
0.67-0.83
2.0-3.0
表.4.2.8船形位置T型接头的单道埋弧自动焊焊接参数
0.77-0.83
675-700
1.83
0.83-0.92
725-750
33-35
2.0
0.9-1
3除按以上各条确定焊接参数外,焊接前尚应按工艺文件的要求调整焊接电流、电弧电压、焊接速度、送丝速度等参数后方可正式施焊。
4厚度12mm以下板材,可不开坡口,采用双面焊,正面焊电流稍大,熔深达65%—70%,反面达40%—55%。
厚度大于12mm-20mm的板材,单面焊后,背面清根,再进行焊接。
厚度较大板,开坡口焊,一般采用手工打底焊。
5多层焊时,一般每层焊高为4—5mm,多道焊时,焊丝离坡口面3mm-4mm处焊。
6填充层总厚度低于母材表面1—2mm,稍凹,不得熔化坡口边。
7盖面层使焊缝对坡口熔宽每边3±
1mm,调整焊速,使余高为0—3mm.
8焊道两端加引弧板和熄弧板,引弧和熄弧焊缝长度应大于或等于80mm。
引弧和熄弧板长度应大于或等于150mm。
引弧和熄弧板应采用气割的方法切除,并修磨平整,不得用锤击落。
9埋弧焊每道焊缝熔敷金属横截面的成型系数(宽度:
深度)应大于1。
10施焊前,焊工应复核焊接件的接头质量和焊接区域的坡口、间隙、钝边等的处理情况。
11不应在焊缝以外的母材上打火引弧。
12定位焊采用的焊材型号应与焊件材质相匹配。
1)定位焊焊脚尺寸不宜超过设计焊缝厚度的2/3,且不应大于6mm。
长焊缝焊接时,定位焊缝长度不宜小于50mm,焊缝间距500~600mm,并应填满弧坑。
2)定位焊的位置应布置在焊道以内。
如遇有焊缝交叉时,定位焊缝应离交叉处50mm以上。
3)定位焊缝的余高不应过高,定位焊缝的两端应与母材平缓过渡,以防止正式焊接时产生未焊透等缺陷。
4)如定位焊缝开裂,必须将裂纹处的焊缝铲除后重新定位焊。
在定位焊之后,如出现接口不平齐,应进行校正,然后才能正式焊接。
5)定位焊缝不得有裂纹、夹渣、焊瘤等缺陷。
焊前必须清除焊接区的有害物。
13对于非密闭的隐蔽部位,应按施工图的要求进行涂层处理后,方可进行组装;
对刨平顶紧的部位,必须经质量部门检验合格后才能施焊。
14在组装好的构件上施焊,应严格按焊接工艺规定的参数以及焊接顺序进行,以控制焊后构件变形。
1)控制焊接变形,可采取反变形措施,其反变形参考值见表2.4.9。
焊接收缩量参见表4.2.10。
2)在约束焊道上施焊,应连续进行;
如因故中断,再焊时应对已焊的焊缝局部做预热处理。
3)采用多层焊时,应将前一道焊缝表面清理干净后再继续施焊。
表.4.2.9焊接反变形参考数值
板厚t(mm)
f
(α+2)/2
反变形角度
(平均值)
B(mm)
150
200
250
300
350
400
450
500
550
700
1。
30’40”
2.5
4.5
22’40”
3.5
5.5
4’
1.5
55’
34’20”
27’20”
0.5
17’20”
40
11’20”
15因焊接而变形的构件,可用机械(冷矫)或在严格控制温度的条件下加热(热矫)的方法进行矫正。
1)普通低合金结构钢冷矫时,工作地点温度不得低于-16。
C;
热矫时,其温度值应控制在750~900。
C之间。
2)普通碳素结构钢冷矫时,工作地点温度不得低于-20。
热矫时,其温度值不得超过900。
C。
3)同一部位加热矫正不得超过2次,并应缓慢冷却,不得用水骤冷。
表4.2.10焊接收缩量
结构类型
焊件特征和板厚
焊缝收缩量(mm)
钢板对接
各种板厚
长度方向每米焊缝0.7;
宽度方向每个接口1.0
实腹结构及焊接H型钢
断面高小于等于1000mm且板厚小于25mm
四条纵焊缝每米共缩0.6,焊透梁高收缩1.0,每对加劲焊缝,梁的长度收缩0.3
断面高小于等于1000mm且板厚大于25mm
四条纵焊缝每米共缩1.4,焊透梁高收缩1.0,每对加劲焊缝,梁的长度收缩0.7
断面高大于1000mm的各种板厚
四条纵焊缝每米共缩0.2,焊透梁高收缩1.0,每对加劲焊缝,梁的长度收缩0.5
格构式结构
屋架、托架、支架等轻型桁架
接头焊缝每个接口为1.0;
搭接贴角焊缝每米0.5
实腹柱及重型桁架
搭接贴角焊缝每米0.25
圆筒型结构
板厚小于等于16mm
直焊缝每个接口周长收缩1.0;
环焊缝每个接口周长收缩1.0
板厚大于16mm
直焊缝每个接口周长收缩2.0;
环焊缝每个接口周长收缩2.0
第五节质量标准
详见《钢结构工程质量验收规范》GB50205-2001
第六节成品保护
6.1构件焊接后的变形,应进行成品矫正,成品矫正一般采用热矫正,加热温度不宜大于650℃,构件矫正应符合下列要求:
项目
允许偏差
柱底板平面度
5.0
桁架、腹杆弯曲
1/1500且不大于5mm,梁不准下挠
桁架、腹杆扭曲
H/250且不大于5.0mm
牛腿翘曲
当牛腿长度≤1000时为2
当牛腿长度>1000时为3
6.2凡构件上的焊瘤、飞溅、毛刺、焊疤等均应清除干净。
要求平的焊缝应将焊缝余高磨平。
6.3根据装配工序对构件标识的构件代号,用钢印打入构件翼缘上,距端500MM范围内。
构件编号必须按图纸要求编号,编号要清晰、位置要明显。
6.4应在构件打钢印代号的附近,在构件上挂铁牌,铁牌上用钢印打号来表明构件编号。
6.5用红色油漆标注中心线标记并打钢印。
6.6钢构件制作完成后,应按照施工图的规定及《钢结构工程施工及验收规范》进行验收,构件外形尺寸的允许偏差应符合上述规定中的要求。
第七节应注意的问题
7.1材料和质量要求
1材料的关键要求
(1)焊接材料的品种、规格、性能等应符合现行国家产品标准和设计要求。
(2)重要钢结构采用的焊接材料应进行抽样复验,复验结果应符合现行国家产品标准和设计要求。
(3)焊剂不应受潮结块。
(4)所用钢材及焊接材料的规格、型号、材质以及外观检查,均应符合设计图纸和规程的要求。
2技术关键要求
焊工应严格按照焊接工艺及技术操作规程施焊。
3质量关键要求
建筑钢结构焊接质量检查应由专业技术人员担任,并须经岗位培训取得质量检查员岗位合格证书。
4职业健康安全关键要求
焊工须有合格证及施焊资格,禁止无证上岗。
5环境关键要求
雪雨天气时,禁止露天焊接。
构件焊区表面潮湿或有冰雪时,必须清除干净方可施焊。
在四级以上风力焊接时,应采取防风措施。
7.2安全环保措施
1.认真贯彻执行国家有关安全生产法规,认真贯彻执行有关施工安全规程。
同时结合公司实际,制定安全生产制度和奖罚条例,并认真执行。
2.牢固树立“安全第一”的思想,坚持预防为主的方针,对职工经常进行安全生产教育,定期开展安全活动,充分认识安全生产的重要性,掌握一定的安全生产知识,对职工进行安全生产培训。
在安全生产上,一定要克服麻痹思想。
3.坚持所有进入车间的人员必须戴安全帽,每天上班前检查车间用气体的安全措施。
4.搞好安全用电。
所有电缆、用电设备的拆除、车间照明等均由专业电工担任,要使用的电动工具,必须安装漏电保护器,值班电工要经常检查、维护用电线路及机具,认真执行JGJ46-88标准,保持良好状态,保证用电安全。
5.各种施工机械编制操作规程和操作人员岗位责任制,专机专人使用保管,特殊工种必须持证上岗。
6.切实搞好防火。
氧气、乙炔气、CO2气要放在规定的安全处,并按规定正确使用,车间、工具房、操作平台等处设置足够数量的灭火器材。
电焊、气割时,先注意周围环境有无易燃物后再进行工作。
7.文明施工具体措施
(1)对施工人员进行文明施工教育,加强职工的文明施工意识。
(2)实行区域管理,划分责任范围,定期进行文明施工检查。
(3)切实加强火源管理。
车间禁止吸烟,电、气焊及焊接作业时应清理周围的易燃物,消防工具要齐全,动火区域要安放灭火器,并定期检查。
(4)废料要及时清理,并在指定地点堆放,保证施工场地的清洁和施工道路的畅通。
(5)做好成品的外观及形体保护,减少污染。
7.3当设计对厚板有Z向性能要求时的焊接工艺措施
在高层及超高层钢结构中,大量采用厚板焊接。
由于钢板存在微裂纹等缺陷、Z向力学性能差,因此厚板焊接、特别是大于40mm钢板焊接时,易导致层状撕裂。
1.选择合理的焊接接点连接形式:
由于规范往往只考虑节点连接的强度及施工的可行性,而对厚板焊接时的层状撕裂未做明确规定,因此在按规范要求进行焊接设计时并不能保证避免层状撕裂的现象发生。
为此,在进行大于40mm厚钢板焊接时,应选择合理的节点连接形式,图6.7.3.1以减小局部区域由于焊缝收缩引起应力集中或尽量避免钢板Z向受拉。
图7.3.1
附图1
(1)在满足要求焊透深度的前提下,采用较小的焊接坡口角度及间隙,图7.3.1.a。
(2)在角接接头中,采用对称坡口或偏向册板的坡口,减小板厚方向承受的收缩应力,图6.7.3.1.b
(3)采用对称坡口,减小焊接收缩应力,图7.3.1.c
(4)在T型或角接接头中,不应在厚板方向受焊接拉应力的板材端部设置焊缝,而应使该板厚度方向受拉的板材端部伸出接头焊缝区,附图图7.3.1.d
(5)在T型、十字型接头中采用过渡段,以对接接头取代T型、十字型接头,图7.3.1.e、f。
(6)对大型连接节点,建议采用图的构造设计来避免或减小厚度方向的应变,图7.3.1.g。
2.焊材及母材的选择
(1)对有特殊要求的部位,可选用Z向延性性能好的钢材
(2)在满足受力要求的前提下,尽可能选择屈服强度低的焊条。
3.使用涂层和垫层
采用软金属丝(一般为低强度的焊条)做垫层,使收缩变形发生在焊缝中,而避免在母材中产生应力集中。
或在节点焊缝处涂焊一层低强度延性焊接金属,让焊缝收缩变形发生在涂焊金属中。
图6.7.3.2
图7.3.2
4.防止层状撕裂的工艺措施
(1)T型焊接时,在母材板面用低强度焊材先堆焊塑性过渡层,图6.7.3.3。
图7.3.3
(2)厚板焊接时,可采用低氢型、超低氢型焊条或气体保护焊施焊,并适当的提高预热温度。
(3)当板厚≥80mm时,对Ⅰ类或Ⅱ类以上钢材箱形柱角焊缝,板边火焰切割面宜用机械方法去处淬硬层,图7.3.4。
图7.3.4
(4)对大尺寸熔透焊,可采用窄焊道焊接技术,并选择合理的焊道次序,以控制收缩变形,焊接过程中,应用锤击法来消除焊缝残余应力。
(5)采用合理的焊接顺序和方向
先焊收缩量较大的焊缝,使焊缝能较自由地收缩;
先焊错开的短焊缝,后焊直通长焊缝;
先焊工作时受力较大的焊缝,使内应力合理分布。
(6)采取反变形降低局部刚性
(7)当焊缝金属冷却时,锤击焊缝区
锤击时温度应维持在100。
C~150。
C之间或在400。
C以上,避免在200。
C~300。
C之间进行;
多层焊时,除第一层和最后一层焊缝外,每层都要锤击。
(8)焊前预热
(9)加热减应区