气体悬浮焙烧炉教材Word文档格式.docx
《气体悬浮焙烧炉教材Word文档格式.docx》由会员分享,可在线阅读,更多相关《气体悬浮焙烧炉教材Word文档格式.docx(11页珍藏版)》请在冰豆网上搜索。
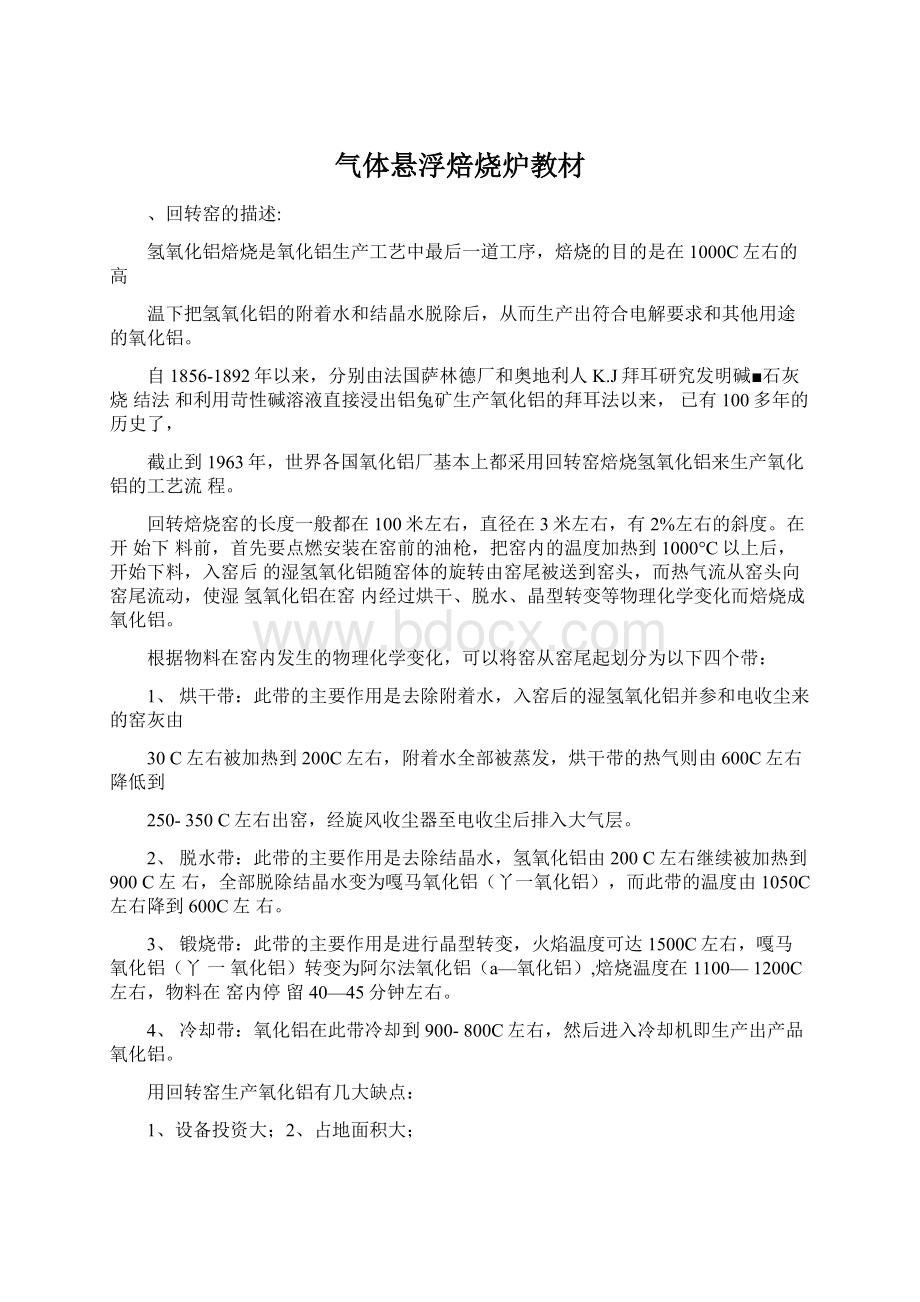
SiO2
Fe2O3
Na2O
灼减
一级
98.60
0.02
0,02
0.50
1.0
二级
98.40
0.04
0.03
0.60
三级
98.30
0.06
0.65
、新型氧化铝焙烧窑炉的发展和应用:
当今世界各国氧化铝厂采用的新型焙烧炉主要有三种类型:
1、美国铝业公司的流态化闪速焙烧炉:
美国铝业公司从1946年开始进行流态化焙烧的实验和半工业化试验,到1963年第一座300t/d氧化铝的流态闪速焙烧炉诞生,用了
17年的时间,至今美国铝业公司的F・F.C装置已发展为五种规格型号,产能最大可达到2400吨以上。
2、德国鲁奇公司和联合铝业公司的循环流态焙烧炉,鲁奇公司从1958年开始研究氢氧化铝沸腾焙烧,1963年第一座25t/d的试验装置成功。
1970年在利泊厂建成一台500t/d循环沸腾焙烧炉,从研究到产业化共用了12年时间,最大设计产能3000t/do
3、丹麦史密斯公司的气体悬浮焙烧炉:
丹麦史密斯公司的气体悬浮焙烧是从水泥窑的气体悬浮窑处分解装置移植而来,史密斯公司从1975年立项开始进行氢氧化铝气体悬浮焙烧试验,到1979年进入半工业化试验,进行了三个月的试验比较成功。
1984年在印度的享达尔阔厂设计安装了一台850t/d的气态悬浮焙烧炉(G.・S・C),1986年投产,从研究到产业化共用10年时间。
4、法国F.C・B公司的气体悬浮焙烧炉:
在法国,流态化焙烧炉原先由尤仁辛尔曼公司和西德的K.H.D公司所属的加丹氧化铝厂内建成一台30t/d氧化铝的闪速焙烧炉,进行T6个月的焙烧一铝电解系统的联合试验,试验结果非常好,于是F.C・B公司和希腊铝业公司在1981年6月决定在圣.尼古拉斯厂建设一套日产900吨氧化铝的气体悬浮焙烧炉,1984年建成投产。
三、流态化焙烧技术及装置的优缺点:
目前,世界上四个国家研制开发的三种类型的焙烧炉虽各有特点和略有优劣之别,但均具有共同的技术经济的先进性,与回转焙烧窑相比,流态化焙烧具有以下显着优点:
1.焙烧氧化铝理论热耗约为2.42GJ/T—AL2O3,其余热量主要是出窑废气和焙烧后的
氧化铝带走或通过窑体散失,而流态化或气态化焙烧的热耗约为3.18-
3.27MJ/kg—
AL2O3,可节煤气约为300m3o
2.产品质量好:
⑴产品中有害杂质SiO2基本不受焙烧过程的影响,只取决于它在氢氧化铝中的含量;
⑵流态化焙烧产品中不同粒级氧化铝的焙烧程度均匀,相同比表面积的氧化铝中阿尔法氧化铝(a—氧化铝)含量低,在铝电解中溶解速度较快,可提高铝电解的电流效率;
⑶流态化焙烧的破碎指数不高;
⑷三种类型的流化焙烧炉均能满足生产砂状氧化铝要求。
3.投资少:
流态化焙烧的投资比回转窑焙烧的投资少,国外各公司发表的数据为:
(1)
美国F.F.C少50%左右;
(2)西德G.・S・C少20%左右;
(3)法国G.・S・C少1510%左右,国内于是1983年,以日产800吨氧化铝的焙烧装置为例,根据实物工作量按当时的国内价格计算,流态化焙烧装置的投资比回转窑少40—60%左右。
4.占地面积小:
流态化焙烧装置的占地面积小,以日产800吨氧化铝的焙烧设备为例,仅是回转窑焙烧装置的五分之一,而建筑面积约为三分之一至三分之二。
5.设备简单,使用寿命长,维修难度低,费用低流态化焙烧系统除了引风机、给料设备之
夕卜,没有大型的转动设备。
炉衬使用寿
命可长达10年左右,因而维修费用低,据有关厂家提供的数据:
流态化焙烧炉的维修费用只是回转窑的35%左右。
6・对环境的污染轻由于流态化焙烧炉燃烧完全,过剩空气系数低,废气中氧的含量低(
1-2%),废气中的SO3的生成量均要比回转窑低;
排入大气的烟含尘量均小于50mg/nm3,因此对环境的污染轻。
四、流态化和气态化焙烧技术和设备在我国应用的状况:
流态化焙烧炉和气态悬浮焙烧是二十世纪八十年代以来,我国开始引进的具有世界先进水平的氢氧化铝焙烧技术和设备,该炉型装置具有热耗低、投资少、设备简单、使用寿命长、维修费用低、自动化程度高、有利于环境保护等特点,截止到2005年,我国已投入使用和正在建设中
的流态化和气态悬浮焙烧炉大约有27台之多,如:
山西正在使用的6台,山东正在使用的2台,郑铝正在使用的3台,中州铝正在使用的4台,平果铝正在使用的2台,桂西正在建的2台,贵铝正在使用的2台,重庆正在建的1台,义马正在使用的1台,山东茨平正在建的2台,东方希望正在使用的一台,开曼即将建成的一台。
五、三种炉型的优劣分析:
流态化焙烧炉虽具有共同的优点,但认真分析比较,无论从技术经济指标,还是炉型的设计成熟性与生产稳定性,不同炉型具有各自的特点与不足,比较分析如下:
1、美铝流态闪速焙烧炉(F.F.C)
美铝流态闪速焙烧炉属正在作业,采用稀相换热和浓相保温相结合的技术,相对另两种炉型有其特点:
其一:
由于采用了调节焙烧温度和停留保温槽料位(控制反应时间)这一双重控制方式,产品质量能得到可靠的保障,同时可根据用户的要求获得不同灼减、比表面积及a—氧化铝含量的焙烧产品。
其二:
由于整套装置设计了预热炉、流化干燥器、停留保温槽、流化冷却器这四个缓冲器,若焙烧炉的干燥段、焙烧段和冷却段中任何一段出现短时故障(或因进出料外部系统影响),另外三段仍能维持运行,整个系统不会产生热工制度的大波动,对焙烧炉的使用寿命及生产的恢复有利,因此整个焙烧炉运行稳定可靠,并且承受各种事故的能力强,其三:
炉内衬及养护(烘炉)过程设计合理,因此运转率可达95%左右。
美铝流态闪速焙烧炉也有其本身的不足:
一、此套装置适应低水分的氢氧化铝物料(6-
8%),若氢氧化铝附着水较高时,必需通过增加过剩空气,使热量从焙烧段带入干燥段,以增强干燥能力,相对来说,使焙烧的热耗和电耗增加;
二、整套装置流化板多,大小床板等多达7块,这样维修时工作量相对增加;
三、控制回路多,控制软件设计复杂,相应对操作人员和计控人员提出了较高的要求;
四、由于系统是正压作业,整个焙烧炉体的密封检测点的密封及容器回料封系统要求严格。
2、鲁奇循环流态焙烧炉(C・F.C)
鲁奇循环流态焙烧炉是采用正压作业浓相流态化技术,其炉型有独特之处。
其一,流态化循环炉依靠大量的物料循环(为产量的12—30倍),焙烧停留时间6分钟左右,这样可降低焙烧温度,有利于降低焙烧氧化铝的热耗,同时确保焙烧氧化铝产品质量,此外,大量循环物料的热仿量、热冲击,维持系统的热稳定性,对提高炉内衬的使用寿命极为有利,炉子运转率可达90-94%;
其二,整个装置无高电压、大型设备,设备简单,投资省,生产控制灵活,事故率低;
其三,控制回路简单,流态悬浮焙烧自动控制回路仅有6条。
循环流态化也有焙烧炉对颗粒破损率大,究其原因如下:
一、气体在喷射口、旋风筒入口及弯头处的流速大;
二、颗粒在循环炉内发生颗粒之间、颗粒与器壁的撞击与摩擦,尽管鲁奇公司对该装置不断地进行改造与完善,使破损率大幅度降低,但目前,焙烧产品45卩m粒极的破损率仍高达3-6%,其二,循环焙烧炉有4个流化床,不仅在冷却系统设计有流化床,而且在高温段也设有流化床,增加了维修工作量;
其三,循环流态焙烧炉与流态闪速焙烧炉一样,亦不适应氢氧化铝附着水高的物料。
3、丹麦气体悬浮焙烧炉(G.・S.C)
丹麦气体悬浮焙烧炉是流态化焙烧的后起之秀,整个装置采用负压作业、稀相流态化技术,相对比,上述两种炉型具有明显的优势。
其一,此炉型采用了在干燥段设计安装了热发生器这一新颖措施,当供料氢氧化铝附水含量增加时,不需象其他炉型那样,采取增加过剩空气的方式来增加干燥能力,而只需启动干燥热发生器来增加干燥段的热量,从而避免了废气量大增而大量热能损失。
因此,与前两种炉型相比,气体悬浮焙烧炉热耗和电耗略低一些;
其二,整套装置设计简单,一是物料自上而下流动,可避免事故停炉时的炉内积料和计划停炉时的排料;
二是设备简单,除流化冷却器外无任何流化床,没有物料控制阀,方便了设备维修;
三是负压作业对焙烧炉的问题诊断和事故处理有利。
这些都是有
利于发生故障后快速恢复生产,给生产带来方便。
其三,控制回路简单,气体悬浮焙烧炉虽有
12条自动控制回路,但在生产中起主要作用的仅有2条,一条是主燃烧系统的主炉温度回路,另一条是氧气含量控制回路。
气态悬浮焙烧炉是20世纪80年代发展起来的的气态悬浮焙烧装置,90年代,我国开始引进这一技术,通过近10年来国内各氧化铝厂的消化吸收、改进完善,基本上已经定型,目前,它已是国内大部分氧化铝厂焙烧氧化铝设备的首选。
其主要缺点是:
一、烘炉设计不太完美,二、由于各悬浮焙烧炉容器部下料管改用了翻板阀,生产中不能低产运行,即便是刚开始下料,也必须迅速提高产量,其目的是避免气流反窜(走短路)或焙烧炉系统内料流形成回流现象,因此,G・.S.C产能的可调范围
窄,一般要求在设计能力的50%以上调节。
三、气体悬浮焙烧炉设计的检修、清理、观察孔较多,易造成系统漏风隐患,四、电收尘’粉料输送系统和文丘里烟道降温系统的设计尚未定型,各氧化铝厂各有千秋。
五、各旋风器下料腿结构简单,料封性能差,料腿高,因此气态悬浮焙烧炉的炉体高,造成投资增大。
国外各公司的主要技术经济指标
项目名称
美国铝业公司流态闪速焙烧
(F.F.C)
西德鲁奇■联合铝业公司循环流态焙烧(C.F.C)
丹麦史密斯公司气态悬浮焙烧
(G..S.C)
法国费凯贝克公司闪素速焙烧炉
(F.C.
流程及设备
闪速流化床干燥脱水,载流预热,闪速焙烧,流化床保温,三级载流冷却加二级流化床冷去
卩。
一级载流干燥脱水,一级文丘里预热,循环流化床焙烧,一级载流冷却加六级流化床冷却
一级载流干燥脱水,一级载流预热,气态悬浮焙烧,四级载流冷却加流化床冷却
一级载流干燥脱水,一级载流预热,气态悬浮焙烧,三级载流冷却加流化床冷却
焙烧过程的流动状态
稀相载流焙烧加浓相流化床保温
快速流态化焙烧
稀相载流焙烧
稀相载流焙烧
焙烧温度
950-1050C
1100C
1150-1300°
C
1050-1250
焙烧时间
15-30分钟
20-30分钟
1.5秒钟
6秒钟
系统阻力损失
17651-20593
帕
29419帕
7845-8825帕
7845-8825
燃料热耗
3.25公斤/氧化铝
3.20-3.27公斤/氧
化铝
3.18公斤/氧化铝
3.27公斤/
氧化铝
焙烧系统电耗
25(包括氢氧化铝过滤及洗涤)
-22KW.h/吨■氧化铝
12KW.h/吨■氧化
铝
20.8
年运转率%
89-93
92-94
90以上
85-90
产品规格
砂状
各种类型
:
各种类型「
从国外各公司的主要技术经济指标和近年来国内各氧化铝厂的使用情况来看,一致认为,丹麦的气体悬浮焙烧炉(G、S、C)有以下明显的优势:
①运转率高;
②热耗低;
③电耗低;
④维修方便;
⑤生产环境卫生条件好;
⑥提产幅度大等优势已被国内外氧化铝厂
认可。
气体悬浮焙烧炉的炉型,是其它二种炉型的佼佼者。
六、气态悬浮焙烧炉工艺过程描述
1、目前国内使用的气态悬浮焙烧炉的规格有:
1850T/D.1400T/D.1300T/D、1200T/D.
850T/D几种规格,但都有相当大的提产幅度,焙烧炉的热能所需燃料有:
一是重油,二是煤气,三是天然气;
氢氧化铝的焙烧过程是一种固体颗粒与热气流直接混合接触并均匀分布于其中,强化了传质、传热的过程,其热效利用率可达80%,回转窑热利用率
在40%左右,气态悬浮焙烧炉热效利用率比回转焙烧窑提高了35%以上,它采用的是一级载流干燥脱水,一级载流预热,气态悬浮焙烧,四级载流冷却以及流态化床冷却等技术,属于稀相载流焙烧工艺。
其固体氢氧化铝颗粒在炉内始终处于悬浮运动状态,在悬浮运动过程中与载流热气进行传质、传热,完成干燥脱水和晶型转变等一系列物理化学演变过程,它具有结构紧凑、产能大、热耗低、焙烧时间短(约1.5秒左右)、系统阻
力小和运转率高等优点。
2、一级载流干燥脱水是在AO2文丘里干燥器内完成的,由螺旋给料机把湿氢氧化铝(含水率10%以下)送至AO2文丘里干燥器内,和来自预热旋风筒PO2的热气流(约320—400C左右)进行载流传质、传热,脱除氢氧化铝的附着水。
3、一级载流预热是在PO2预热旋风筒内完成的,来自分离旋风筒的氢氧化铝和来自PO3分
离旋风筒的热气流(约1000—1150C左右)在PO2旋风筒内进行载流预热,将氢氧化铝加热到300r左右,脱除氢氧化铝中的大部分结晶水。
4、气态悬浮焙烧是在PO4主炉内完成的,来自PO2的物料和来自V19主燃烧器所产生的1100C左右的高温气流相混合,最终在PCU、PO3筒体内脱除结晶水和完成晶型转变的全过程,生产出一种由a—氧化铝和丫一氧化铝混合物料构成的且物理化学性质符合电解要求的氧化铝产品。
5、四级载流冷却是在四个串联的旋风筒(COi、CO2、CO3、CO4)组成的载流冷却装置内完成的。
来自PO3的1050r左右的物料和来自冷风进口和流化床冷却器的空气进行载流热交换,物料被空气冷却达到250r左右,而空气被预热到700r左右后,进入PCU主炉下部,供V19主燃烧器煤气所需的助燃气体之用。
冷却旋风筒的作用:
在冷却物料的同时回收物料的热量,借此提高助燃空气的温度,从而提高整个气态悬浮焙烧炉的热效率。
6流化床冷却器KOkKO2是氧化铝物料的最终冷却器,来自CO4锥体下部分料阀的物料,在流化床内被来自罗茨鼓风机的空气流态化,流化床内装有管道冷却器,管内是流动的冷却水,流态化的物料通过管壁进行热交换,物料从250r左右被冷却到80r以下,从流态化冷却器出来的氧化铝经输送设施被送到氧化铝大仓。
7、气态悬浮焙烧炉内的气体流动的动力來自炉子尾部的排风机,整个炉子处于负压下状态
下工作,排风机前面还装有控制风量的可调的电动风门和净化焙烧炉尾气的电收尘,POi
预热旋风筒出来的含尘烟气在电收尘器内进行除尘,除尘后的气体含尘量要求在50mg/NM3以下,除尘后的气体通过烟囱排入大气。
整个气态悬浮焙烧炉错落布置,结构紧凑,形成一个完整的统一体。
气体悬浮焙烧炉的主要工作参数:
1主炉温度PO4T11020—1060r
2CO%v0.6%
302控制在1.0%—2.0%
4文丘里出口温度:
140r
5电收尘入口温度P11T1:
140r
6流化床出水温度:
W55r
7冷却水进口温度:
W35r
8流化床出料温度:
W80C
9入炉水份:
v10%三、主要设备及构造
1、主要设备及构造:
⑴喂料螺旋:
©
630x3200mm
减速电机:
YTC・280
(2)文丘里闪速干燥器A02
3750mmH=9047mm材质:
S=6mm低碳钢⑶旋风筒POi:
©
3950x9625mm材
质:
S=6mm低碳钢
⑷旋风筒PO2:
4800x11161mm
材质:
⑸旋风筒POa:
5700x14223mm材质:
⑹旋风筒PO4:
5750x17020mm材质:
⑺旋风冷却器COi:
4200x9666mm材质:
⑻旋风冷却器CO2:
3450x8307mm材质:
⑼旋风筒CO3:
3000x7094mm材质:
(10)旋风筒CO4:
2250x5523mm材质:
S=6mm低碳钢
(11)流化床冷却器:
1900x1900x10300mm
(12)ID风机2150S1BB50
流量:
Q=240000M3/h电机:
YPTQ500-4P=900KWIP44690V
(13)启动燃烧器T12:
SO-1000-GO
正常燃油:
400kg/h进口压力:
8—25x105Pa附风机:
MT50S电机:
P=15KW
⑭)燃烧器V19:
流量25000Nmh
(15)点火燃烧器:
PG-100作用:
内衬养护和焙烧炉主燃烧器点火
1000Nm3/h进口压力:
250mba电机:
KQF-40/44-N风量:
15—42M3/min压差:
350mba
电机:
SCLB-4.0KW-2-50n=2980rpm
(16)T*燥器加热器:
HG-G-63
作用:
控制干燥器出口温度流量:
0—5000Nm3/h
风机:
MT-50SQ=130M3/minP=15KW
3、气体悬浮焙烧炉的工艺流程介绍
工艺流程图(见附图)。
1氢氧化铝给料系统
由平盘过滤机生产的氢氧化铝滤饼经皮带运至皮带称FO1上的氢氧化铝小仓中,从
皮带秤下来的物料经AH小皮带F03送至螺旋给料机A01螺旋给料机把物料送入文丘里闪速干燥器。
2文丘里闪速干燥器A02
含自由水分W10%的湿氢氧化铝通过螺旋输送机AO1,以50C温度进入闪速干燥器。
在干燥器中干燥了的物料由烟气及水蒸气的气流带入上部预热旋风筒。
闪速干燥器出口的温度大约为135Co给料螺旋的出口设计确保滤饼很容易分散到热气流中去。
3干燥热发生器T11
干燥器AO2出口的温度维持在135C左右,以防止电收尘受到酸腐蚀。
为控制因氢氧化铝水分波动而引起干燥器出口温度变化所需要的热量由干燥热发生器T11提供。
4预热旋风系统
烟气和干氢氧化铝的混合物在干燥器之后的预热旋风筒P01中得以分离。
干燥的氢氧化铝卸入第二级预热旋风筒PO2的上升管,在此与热旋风筒来的1050C左右的热气体混合。
氢氧化铝在上升管中同时得以预热和分解。
物料与气体之间的温度实际上已达到完全平衡。
预焙烧的氧化铝在第二级预热旋风筒PO2中与废气分离后大约以320E进入
焙烧炉。
由于经过焙烧的物料具有良好的流动性和较高的温度,通常焙烧辅炉PO3向第一级
冷却旋风筒的下料管上都不设翻板锁气阀和阀门。
然而,第一、二级预热旋风筒和冷却旋风筒的下料管都设有翻板锁气阀,以消除反向气流并改善热效率和旋风筒的分离效率。
5焙烧炉P04气态悬浮焙烧炉和热旋风筒组成为一个反应器一分离器联合系统。
焙烧炉是一个有
内衬耐火材料且带有锥形底部的圆柱形容器。
助燃空气在氧化铝冷却器中被预热到600-700C,并从焙烧炉底部引入。
预焙烧后的氧化铝平行地加入到炉子的锥形底部,在这里,物料同预热的空气、燃料充分混合。
焙烧炉入口处空气/烟气的速度选定以保证正常及部分产能下,在整个反应器断面上颗粒物料都能良好悬浮。
反应器合理的空气/烟气入口管尺寸可以是任何形式的分布板或高压喷嘴得以取消。
(这一点是气态悬浮焙烧炉与其他炉型不同的关键之处,也是悬浮炉得以命名的依据)。
在热旋风筒PO3中,焙烧好的氧化铝从热气流中分离并卸入上部的冷却旋风筒CO1
的上升管。
6CO1、CO2、CO3和C04初级冷去卩器
初级冷却在四级旋风筒冷却器组中进行,旋风筒组以紧凑的设计垂直布置。
氧化铝冷却用空气主要取自大气及第二流态冷却机。
空气和热氧化铝之间的热交换是在每一个冷却器旋风筒的上升管中顺流进行,空气和氧化铝在进入旋风筒中分离之前,其温度已经在上升管中达到了完全平衡。
由于旋风多级配置,氧化铝与焙烧炉所需的助燃空气之间可以达到完全的逆流热交换。
离开初级旋风筒冷却器的氧化铝约为240°
C,再进入第二级流态化冷却机进一步冷却。
7第二级冷却机KO1和KO2
第二级流化床冷却机将旋风筒冷却器来约240C的氧化铝降至80C以下。
流化床中氧化铝通过一组管束换热器用水流反向间接冷却,这种形式的冷却机要求的空气量受氧化铝流态所限制。
流态化所用的空气由罗茨鼓风机提供,并通过一块分布板分配到整个流态化床断面上。
流态化空气通过一套排风管连接到初级冷却器的空气入口管上。
8除尘系统
从顶部预热旋风筒PO1出来的含尘废气在电收尘P11中得以净化,两条空气斜槽把收下的粉尘卸入返灰系统。
除尘后的废气通过装有控制风量的百叶风门的排风机送入大气当中。
收下的粉尘在一个密闭循环系统中完全回收。