铸造缺陷的特征鉴别成因及防治措施Word文档格式.docx
《铸造缺陷的特征鉴别成因及防治措施Word文档格式.docx》由会员分享,可在线阅读,更多相关《铸造缺陷的特征鉴别成因及防治措施Word文档格式.docx(27页珍藏版)》请在冰豆网上搜索。
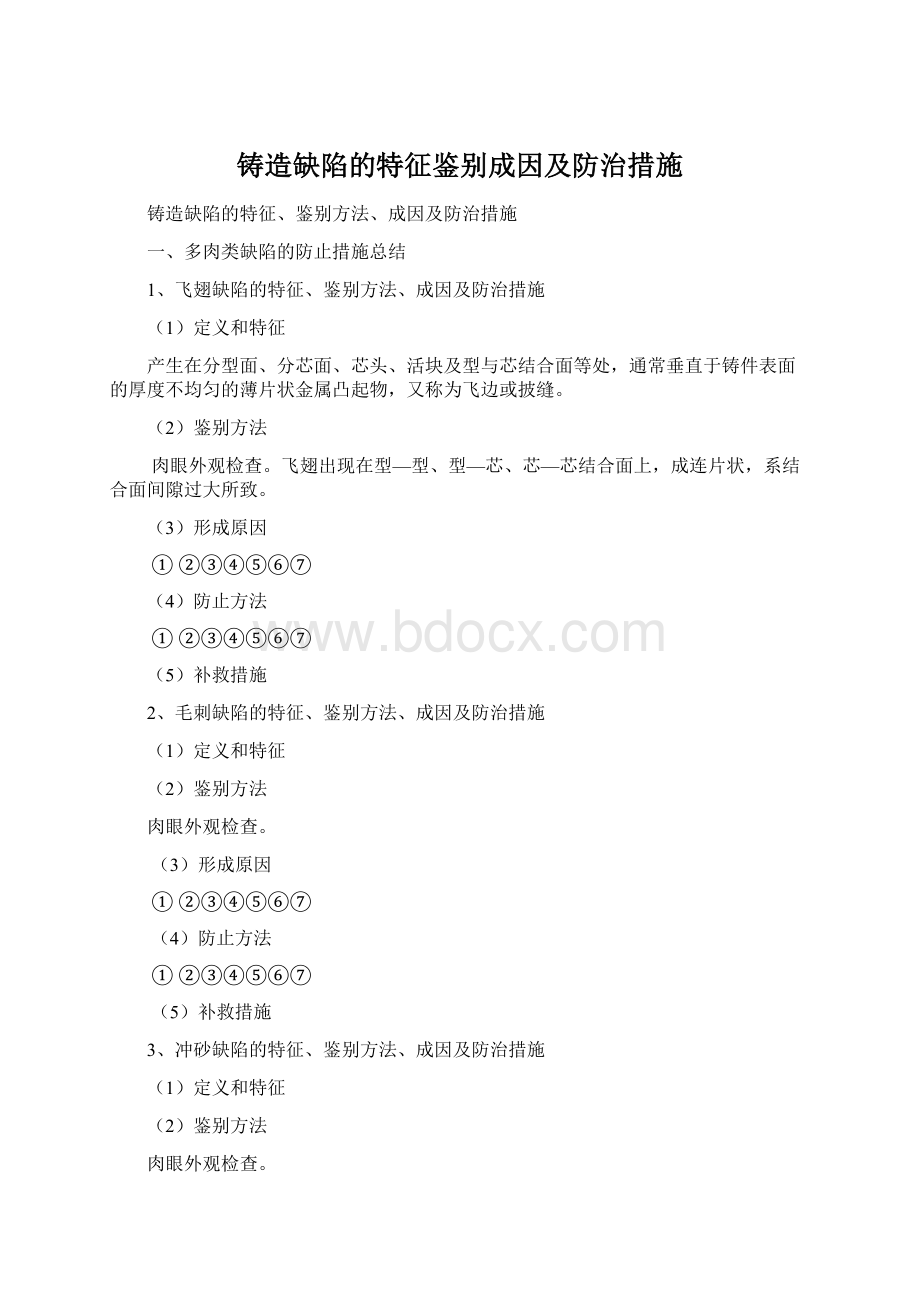
(5)补救措施
2、毛刺缺陷的特征、鉴别方法、成因及防治措施
肉眼外观检查。
(3)形成原因
(4)防止方法
(5)补救措施
3、冲砂缺陷的特征、鉴别方法、成因及防治措施
4、胀砂缺陷的特征、鉴别方法、成因及防治措施
(2)鉴别方法
5、抬型/抬箱缺陷的特征、鉴别方法、成因及防治措施
①②③④⑤
①②
6、外渗物/外渗豆缺陷的特征、鉴别方法、成因及防治措施
①②③
①②③④⑤⑥
7、掉砂缺陷的特征、鉴别方法、成因及防治措施
2、孔洞类
1、反应气孔缺陷的特征、鉴别方法、成因及防治措施
2、卷入气孔缺陷的特征、鉴别方法、成因及防治措施
①②③④
3、侵入气孔缺陷的特征、鉴别方法、成因及防治措施
4、析出气孔缺陷的特征、鉴别方法、成因及防治措施
①②③
5、疏松(显微缩松)缺陷的特征、鉴别方法、成因及防治措施
①②③④⑤⑥⑦⑧⑨⑩
①②③④
6、缩孔缺陷的特征、鉴别方法、成因及防治措施
①②③④⑤⑥⑦
①②③④⑤⑥⑦⑧
7、缩松缺陷的特征、鉴别方法、成因及防治措施
3、裂纹、冷隔类
1、白点(发裂)缺陷的特征、鉴别方法、成因及防治措施
①②
2、冷隔缺陷的特征、鉴别方法、成因及防治措施
3、冷裂缺陷的特征、鉴别方法、成因及防治措施
①②③④⑤
4、热处理裂纹缺陷的特征、鉴别方法、成因及防治措施
5、热裂缺陷的特征、鉴别方法、成因及防治措施
①②③④⑤⑥
4、表面类
1、表面粗糙缺陷的特征、鉴别方法、成因及防治措施
2、沟槽缺陷的特征、鉴别方法、成因及防治措施
3、化学粘砂缺陷的特征、鉴别方法、成因及防治措施
4、机械粘砂缺陷的特征、鉴别方法、成因及防治措施
5、夹砂结疤缺陷的特征、鉴别方法、成因及防治措施
夹砂结疤是砂型型腔表面在充型金属液强烈热作用下,因热应力、水分迁移、膨胀和强度降低等因素的综合作用,导致砂型表层拱起开裂,尚未凝固的金属液钻入裂缝而形成的夹砂类缺陷。
特征:
铸件表面产生的疤片状金属凸起物。
其表面粗糙,边缘锐利,有一小部分金属与铸件本体相连,疤片与铸件之间夹有砂层。
通常发生在铸件的上表面和下表面上。
发生在铸件内角和外角的夹砂结疤称为内角夹砂结疤和外角夹砂结疤,应与铸件的角部毛刺相区别。
结疤夹有型砂,铲除后铸件表面凹陷,毛刺无此特征。
根据这两点及其边缘锐利的特征,可将夹砂结疤与胀砂、冲砂、掉砂、粘砂和涂料结疤(由涂料剥落引起的疤状缺陷)相区别。
夹砂的金属边缘尖锐,一般不与铸件本体相连。
①铸件上表面的夹砂结疤称为上型面夹砂结疤,由上型面沟槽发展而成。
②铸件下表面的夹砂结疤称为下型面夹砂结疤,其形式有二:
一种类似鼠尾,但砂层翘曲程度和铸件表面凹陷程度比鼠尾严重,由鼠尾发展而成,称为夹砂结疤;
另一种类似上型面夹砂结疤,由两平行金属流股间的下型面表层拱起开裂而成。
③出现在铸件内角和外角的夹砂结疤称为角部夹砂结疤,由位于角部的上、下型面表层膨胀翘曲,脱离水分凝聚层伸入型腔所致。
④湿型铸造的铸件上表面或下表面为大平面,型砂膨胀率大,湿强度低,水分过多,透气性差,铸型排气不良,浇注温度过高,浇注时间过长时,易产生夹砂缺陷。
大型铸钢、铸铁和铜合金铸件易产生夹砂类缺陷。
①降低砂型的膨胀应力:
在型砂中加入煤粉、沥青、重油、木粉、纤维材料等易燃易软化材料,补偿砂粒膨胀,降低膨胀应力;
砂型表层全部或部分用高耐火度、低膨胀率砂型(例如锆砂)代替硅砂。
②提高型砂湿强度:
用钠基膨润土或活化膨润土配制湿型砂,增加湿型砂中膨润土或黏土含量;
采用粒度分散的原砂(例如四筛砂),适当加粗原砂粒度;
控制湿型砂水分不宜过高;
均匀紧实型砂,避免砂型局部紧实度过高。
③提高型砂透气性,上型要多扎出气孔,改善砂型的通气。
④用干型、自硬砂型代替湿型。
⑤适当降低浇注温度,缩短浇注时间,使金属液快速均匀地充满型腔。
对于大平面铸件,不能只根据铸件重量来确定浇注时间,应同时考虑铸件表面积大小;
一型多铸时,应根据单个铸件的重量和尺寸,而不是根据型内铸件的总重量来确定浇注时间。
⑥浇注过程中对砂型吹气冷却。
⑦铸造工艺设计时,将铸件大平面置于侧面。
必要时,可立浇卧冷或倾斜浇注。
⑧在容易产生夹砂结疤的下型面上,镶置预制的耐火材料板。
在上型表面插钉加固。
夹砂结疤严重时,会使铸件壁厚过分减薄甚至穿透而导致报废。
如允许焊补,可在铲除疤片后将凹陷区焊平并打磨到与周围平面平齐。
结疤不严重,且技术要求允许时,对于不加工表面,可在铲去多余金属后磨平表面或用腻子填平表面;
对于加工表面,铲去多余金属后可把凹陷区加工掉。
6、热粘砂缺陷的特征、鉴别方法、成因及防治措施
铸件表面粘附着一薄层玻璃状型砂烧结物,常发生在砂型表面受热严重的部位。
粘砂层无金属渗入,易清除。
热粘砂中不含金属,常呈玻璃体状,比较薄,多发生在黏土砂型中,清理比较容易。
①型砂和芯砂粒度太粗。
②砂型和砂芯的紧实度低或不均匀。
③型、芯的涂料质量差,涂层厚度不均匀,涂料剥落。
④浇注温度和浇注高度太高,金属液动压力大。
⑤上箱或浇口杯高度太高,金属液静压力大。
⑥型砂或芯砂中含黏土、黏结剂或易熔性附加物过多,耐火度低,导热性差。
⑦型、芯砂中含回用砂太多,回用砂中细碎砂粒、粉尘、死烧结土、铁包砂太多,型砂烧结温度低。
⑧铸件开箱落砂太晚,形成固态热粘砂,尤其是厚大铸件和高熔点合金铸件。
⑨金属液流动性好、表面张力低。
例如,铜合金中磷、铅含量过高,铸钢中磷、硅、锰含量过高。
⑩树脂砂型、芯表面未刷涂料或涂料质量差,涂层厚薄不均,浇注时砂粒间树脂膜汽化,形成毛细通道,在金属液静压力、蒸汽压和表面张力作用下,金属液或金属蒸汽渗入毛细通道,形成机械粘砂。
金属液中的氧化物和低熔点化合物与型砂发生造渣反应,生成硅酸亚铁、铁橄榄石等低熔点化合物,降低金属液表面张力并提高其流动性,使低熔点化合物和金属液通过毛细管作用机制,深入砂粒间隙,并在渗透过程中,造成铸型和铸件局部过热。
浇注系统和冒口设置不当,造成铸型和铸件局部过热。
①使用耐火度高的细粒原砂。
②采用再生砂时,去除过细的砂粒、死烧黏土、灰分、金属氧化物、废金属、铁包砂及其他有害杂质,提高再生砂质量;
定期补充适量新砂。
③水是强烈氧化剂,应严格控制湿型砂水分,加入适量煤粉、沥青、碳氢化合物等含碳材料,在砂型中形成还原性气氛。
但高压造型时,应减少含碳材料加入量,以减少发气量。
④采用优质膨润土,减少黏土砂的黏土含量。
⑤型砂中黏结剂含量要适当,不宜过高。
提高混砂质量,保证砂粒均匀裹覆黏结剂膜,并有适度的透气性。
避免型砂中夹有团块。
⑥提高砂型的紧实度和紧实均匀性。
⑦浇注系统和冒口设置应避免使铸件和铸型局部过热;
内浇道应避免直冲型壁。
⑧采用防粘砂涂料,均匀涂覆,在易产生粘砂部位适当增加涂层厚度。
涂料中不得含有易产生气体、氧化及能与金属液和型砂发生反应的成分。
尽量不采用通过反应(可在铸件—铸型界面)形成易剥离的玻璃状粘砂层的涂料来解决粘砂问题,例如在铸铁件型砂和芯砂中加入赤铁矿粉。
⑨适当降低浇注温度、浇注速度和浇注高度,降低上型高度和浇口杯高度,以减小金属液动压力、静压力及