电阻焊工艺设计规范方案和质量控制Word格式文档下载.docx
《电阻焊工艺设计规范方案和质量控制Word格式文档下载.docx》由会员分享,可在线阅读,更多相关《电阻焊工艺设计规范方案和质量控制Word格式文档下载.docx(14页珍藏版)》请在冰豆网上搜索。
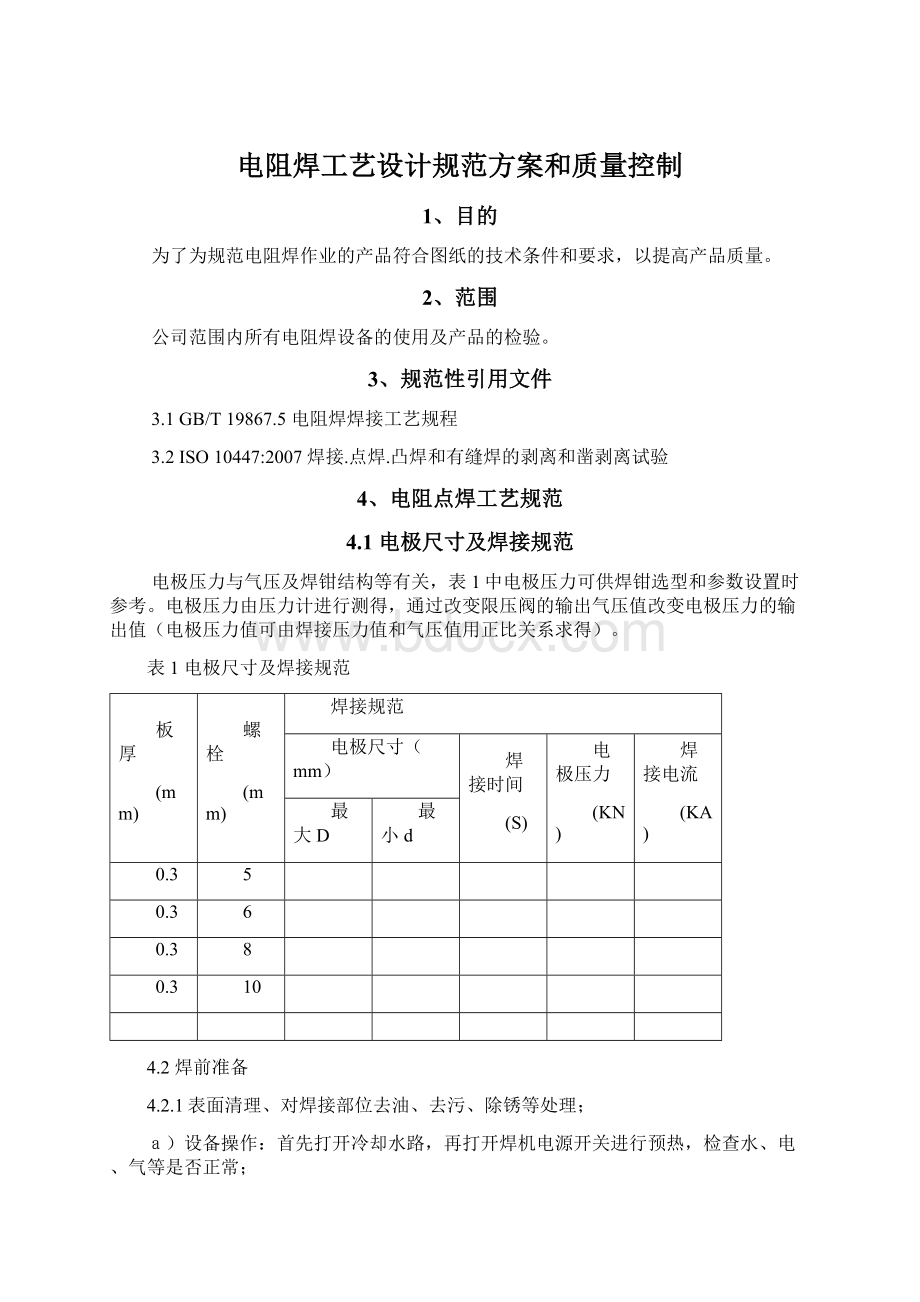
(KA)
最大D
最小d
0.3
5
6
8
10
4.2焊前准备
4.2.1表面清理、对焊接部位去油、去污、除锈等处理;
a)设备操作:
首先打开冷却水路,再打开焊机电源开关进行预热,检查水、电、气等是否正常;
b)电极是否更换或已经修复并且符合标准,参考表1;
c)检查气压是否正常,气管、电缆、绝缘防护等是否良好;
d)以下几种情况需重新确定焊接规范,工艺验证合格后,方可进行焊接:
——对于新购置的、停用3个月以上的、故障排除后的焊机;
——板材的材质、厚度发生变化;
——出现焊接质量问题时。
5点焊焊接强度检验及质量控制
5.1焊点质量接收准则
5.1.1焊点尺寸
一个焊点其熔核尺寸应该大于或等于表2相应数值才是可接受的,实际尺寸小于规定值则被判定为不合格。
表2焊点熔核尺寸
板厚(mm)
螺栓(mm)
熔核直径(mm)
5.1.2熔核尺寸的计算和测量
熔核为焊点的部分,包括整个或部分熔核,会在破坏试验中撕裂而得到,熔核的直径由长轴测量数值加上与长轴垂直轴的测量数值再除以2计算得到,测量数据要在接触面上测量得到,图1为熔核尺寸计算方法,图2为量具测量方法。
图1熔核尺寸的计算
注:
1为带刃口的检测量具
图2熔核尺寸的测量
5.1.3裂缝
周边有裂缝的焊点是不合格的焊点,由电极留在表面的压痕区域内的裂缝是允许的。
5.1.4孔
含孔的点且由各种原因被击穿的视为不合格。
5.1.4焊接区域
点焊区域为电极焊接后压痕所在区域,点焊区域应该包含在金属边缘之内,否则视为不合格,如图3所示:
图3焊接区域极限
5.1.5位置公差
按照工艺文件中内容焊点位置进行焊接须在偏差0.3mm范围以内,超出则视为不合格。
5.1.6压痕深度
由电极压力引起的,导致点焊区域金属厚度比本身厚度变薄超过50%的视为不合格(以薄板为基准),必须调整工艺以减少压痕深度如图4所示:
图4压痕深度计算方法
5.1.7漏焊
实际焊接数量少于规定的焊点数量时或被遗漏的焊点为不合格。
5.1.8焊接变形
焊接变形需控制在25°
范围之内,否则视为不合格,如图5所示:
图5焊接面变形极限
6.点焊焊接强度质量检验
6.1车间试验
6.1.1凿裂试验
6.1.1.1试验方法
通过用凿子强迫砸入焊缝中,判断焊点是否开焊或裂纹,方法如图6所示:
图6凿裂试验方法
6.1.1.2凿入深度及规范
以錾子头部距离焊点10—15mm,凿入至焊点焊接末端为准,如图7所示:
图7凿入深度尺寸
6.1.1.3錾子尺寸的选择
表3錾子尺寸的选择
錾子图样
检测形式(破坏性或非破坏性)
焊点直径D/mm
板厚/mm
图8a)
均适用
D<8
-
图8b)
D<13
图8c)
非破坏性
t≤2.0
图8d)
图8錾子式样
6.1.2焊点剥离试验
6.1.2.1单点破坏手动扭转试验
将焊接式样,按照如图9所示的方法进行操作,将焊接试样沿一个方向连续旋转扭绞直至焊点破裂,通过测量残留在其中一个板材上的凸台的尺寸(参照表2)及撕裂效果来判定焊接质量是否合格。
图9手动扭转操作方法
6.1.2.2多点连续剥离破坏
按照焊接式样选取规范,焊接焊点以30mm为点距一般焊接5-10点,将试样其中一板材加入虎钳中,用专用工具进行旋转扭绞,以进行多点连续破坏,如图10所示,以下两种方法均能得到相同的试验效果。
a)专用工装b)夹钳拉斯
图10连续破坏方法
6.1.2.3试片及试件尺寸
用于扭转试验的样品单独进行焊接,距离边缘的点焊最短距离应大于10mm对于不同的板厚,其尺寸应以较薄的板为基础,也可以按照试验设备来调整样品尺寸,但应能足以保证试件的刚性,焊点应该位于试样的中心,如图11推荐尺寸:
6.2实验室试验
6.2.1拉伸试验:
将焊接好的试片装夹在拉伸试验机上,在室温下进行拉伸,并输出试验报告。
试验报告应该包含一下信息:
——试验报告
——焊接工艺
——焊接条件与设备
——材料及其条件
——试件与样品的尺寸
——撕裂力的单个值、平均值以及标准偏差
——失效类型(母材撕裂、焊点撕裂、熔核残留)
——焊接直径的单个值、平均值以及标准偏差
表4不同板厚抗剪切强度对照表
板厚(mm)
抗剪强度(KN) ±
14%
0.6
3.0
0.8
4.4
1.0
6.1
1.2
7.8
1.6
10.6
1.8
13.0
2.0
14.5
2.3
18.5
3.2
31.0
6.2.2金相试验(宏观)
6.2.2.1试样规格
将焊接好的标准试样通过线切割或其它的切割方法将焊点正中切开,以便于试样镶嵌及金相检验操作,试样规格如下:
图12金相试验式样规格
6.2.2.2 试验方法
a)对切割后的试样断面进行镜面抛光;
b)用2%~5%的硝酸酒精溶液进行腐蚀;
c)将式样放置于显微镜下进行观看并拍摄宏观照片;
d)输出试验报告,试验报告应该包含以下内容:
——熔核尺寸
——显微组织情况
——焊点外貌状态
6.2.2.3超声波探伤
试样要求:
焊点无飞溅物、无毛刺、单板厚度小于等于3mm。
试验报告应包含以下内容:
——焊透率
——气孔
——过烧
6.2.2.4 整车破坏
车间应按照1台/30000台,2次/年的频次进行整车破坏,以掌握整车焊点合格率。
7 凸焊工艺规范
7.1凸焊参数的选取规范和一般原则
a)首先按照表4中规定的参数规范进行设置,在生产现场可根据实际情况,对焊接规范进行调整,焊接时间缩短10%~50%,焊接电流增大5%~20%,通过试焊选取合适的工艺参数;
b)对于镀锌板等防锈板的焊接,焊接电流应增大20%~40%;
对于高强度板的焊接,随着其强度的增加,焊接压力应增大10%~30%,焊接电流延长2CY;
C)电极压力与焊机气压有关,通过改变限压阀的输出气压值改变电极压力的输出值(电极压力值可由焊接压力值和气压值用正比关系求得)。
表4凸焊焊接规范
螺栓或螺母型号
板厚
通电时间
mm
KA
CY
KN
M5螺母
0.8-1.5
9000
2.8
M6螺母
0.8-2.0
9100
13
3.7
M8螺母
1200
15
3.8
M10螺母
0.8-1.8
13200
4.0
7/16螺母
1.5-2.2
14500
M6螺栓
1.4-1.8
2.5
M8螺栓
0.8-2.2
11500
M10螺栓
8 凸焊焊接强度检验与质量控制
8.1凸焊过程接受准则
8.1.1裂缝
凸焊焊点周边有裂缝视为不合格,由电极留在表面的压痕区域内的裂缝是允许的。
8.1.2孔
8.1.3焊接位置
螺栓凸焊后螺栓螺纹部分垂直板材焊接面为合格,螺母焊接以不挡孔为合格。
8.1.4 螺纹质量
螺栓、螺母焊接完毕后螺纹有烧蚀、焊渣、变形、螺距变短等视为不合格,要求用国标制螺纹规进行检验。
8.2 质量控制
8.2.1剥离试验(计量型)
按照图13所示的方法进行剥离扭矩测试,以满足表5中的最小剥离扭矩。
图13凸焊螺母螺栓剥离扭矩试验方法
表5不同螺母螺栓型号最小剥离扭矩值对照表
螺纹规格
最小剥离扭矩(N·
m)
M4
24.5
M8
44.1
M5
25.5
M10(7/16〞)
58.8
M6
34.3
M12
78.4
8.2.2 锤击试验(计数型)
在工程内检验螺母栓强度时可以按照图16所示的方法用1磅的锤子对螺母或螺栓进行敲击,以落母螺栓不脱落为合格。
图16锤击方法
8.2.3剔试试验(计数型)
用錾子凿入焊接凸点部位直至母材破坏停止,以焊点无开焊为合格。
图17剔试方法
您好,欢迎您阅读我的文章,本WORD文档可编辑修改,也可以直接打印。
阅读过后,希望您提出保贵的意见或建议。
阅读和学习是一种非常好的习惯,坚持下去,让我们共同进步。