冲裁工艺与模具设计Word文档下载推荐.docx
《冲裁工艺与模具设计Word文档下载推荐.docx》由会员分享,可在线阅读,更多相关《冲裁工艺与模具设计Word文档下载推荐.docx(46页珍藏版)》请在冰豆网上搜索。
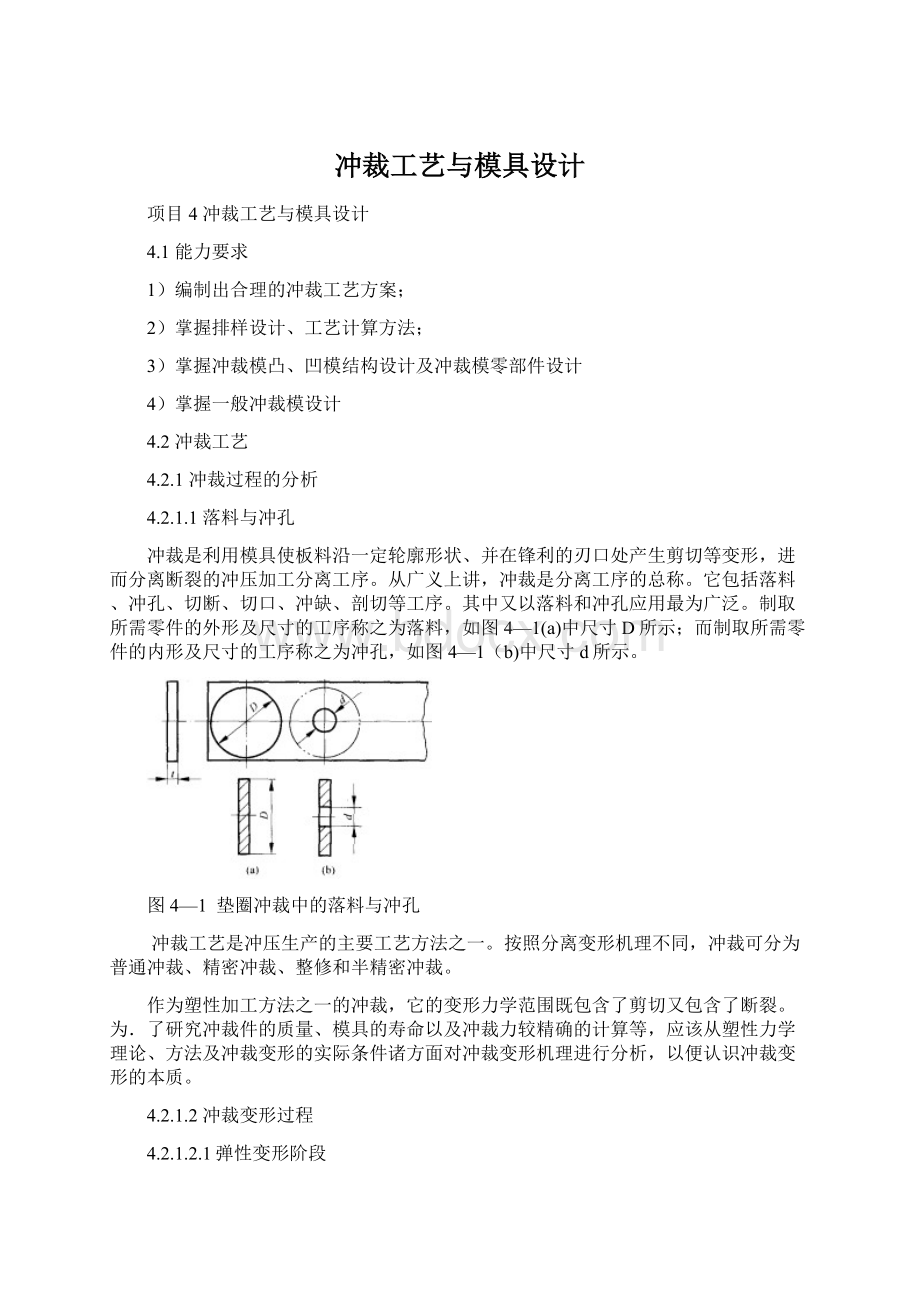
图4—1垫圈冲裁中的落料与冲孔
冲裁工艺是冲压生产的主要工艺方法之一。
按照分离变形机理不同,冲裁可分为普通冲裁、精密冲裁、整修和半精密冲裁。
作为塑性加工方法之一的冲裁,它的变形力学范围既包含了剪切又包含了断裂。
为.了研究冲裁件的质量、模具的寿命以及冲裁力较精确的计算等,应该从塑性力学理论、方法及冲裁变形的实际条件诸方面对冲裁变形机理进行分析,以便认识冲裁变形的本质。
4.2.1.2冲裁变形过程
4.2.1.2.1弹性变形阶段
如图4—2(a)所示,当凸模下压接触板料时,凸模与凹模刃口周围的板料产生应力集中现象,使材料产生弹性压缩、弯曲、拉伸等复杂的变形。
板料略有挤入凹模洞口的现象。
此时,凸模下的材料略有弯曲,凹模上的材料则向上翘。
间隙愈大,弯曲和上翘愈严重。
随着凸模继续压人,直到材料内的应力达到弹性极限。
此阶段材料将产生短暂的、轻微的弹性变形。
图4—2冲裁变形过程分析
(a)弹性变形(b)塑性变形(c)出现裂纹(d)裂纹贯通(e)断裂分离(f)剪切断面
在板料的冲裁过程中,变形区主要集中在凸、凹模刃口连线附近。
这个变形区属于圣维南(Saint·
Venant)区,其应力分布规律无法用数学—力学方法求得。
板料冲裁光弹试验可以通过等色线了解某一截面内主剪应力的分布规律,通过等色线配合等倾线可进一步了解该截面内各点的剪应力和两个主应力的数值、主应力迹线及主剪应力迹线等。
通过改变试验模具的间隙可以得出不同冲裁间隙对板料内应力分布规律的影响。
而且通过冻结光弹试验还可以了解不同截面内的应力分布规律。
总之,通过光弹试验可以有效地观察、分析板料冲裁弹性变形阶段的力学特征,并对冲裁过程的理论分析进行验证。
4.2.1.2.2塑性变形阶段
如图4—2(b)所示,凸模继续下压,板料变形区的应力将继续增大。
当应力状态满足屈服准则时,材料便进入塑性变形阶段。
这一阶段突出的特点是材料只发生塑性流动,而不产生任何裂纹。
由于凸模切入板料,板料挤入凹模洞口。
在板料剪切面的边缘产生弯曲、拉伸等作用形成塌角,同时由于塑性剪切变形,在切断面上形成一小段光亮且与板面垂直的断面。
纤维组织产生更大的弯曲和拉伸变形。
随着凸模的下压,应力不断加大,直到分离变形区的应力达到抗剪强度,塑性变形阶段结束。
塑性变形阶段的实质按现代金属物理学的观点,金属内部存有大量的位错,金属塑性变形的实质就是位错的运动,材料的屈服极限就是开动位错使之运动所需的临界应力值。
材料内部的位错数量越多,开动位错就越困难,屈服极限也就越高。
位错运动的结果,即金属塑性变形的结果
4.2.1.2.3断裂分离阶段
图4—2(c),(d),(e)表示了断裂分离的全过程,其中图(c)表示当凸模切人板料达到一定深度时,在凹模侧壁靠近刃口处的材料首先出现裂纹。
这表明塑性剪切变形的终止和断裂分离的开始。
图(d)表示裂纹发展与贯通的情形。
在一般情况下,在凹模附近产生的裂纹向凸模刃口方向发展的过程中,处在凸模侧面靠近刃口附近的材料也将产生裂纹,并且上下裂纹将贯通。
图(e)表示冲裁结束时板料被完全分裂分离的情形。
被冲入孔的一块料在落料时为工件,冲孔时为废料。
留在凹模面上的材料在冲孔时为工件,落料时为废料。
普通冲裁件的剪切断面状况如图4—2(f)所示,其精度一般在ITl0级以下,表面粗糙度及。
在3.2μm~50µ
m。
如图4—2(f)所示,断面明显分为四个区域:
a为圆角区,即塌角;
b为光亮带,表面光
滑,表面质量最好;
c为剪裂带,表面粗糙并略带斜度,不与板面垂直;
d为毛刺。
断裂分离阶段的实质是模具刃口附近的板料,随着板料塑性变形的发展,板料内位错数量大大增加并堆积在晶间和杂质处。
塑性变形后期形成首次微裂纹,随后内生第1条、第2条微裂纹,在微裂纹根部汇集成较宽的主裂纹,或称之为裂缝,如图4—3所示。
在主裂纹形成之后,板料弹、塑性变形阶段积蓄在板料内的应变能得到迅速地释放,使裂纹迅速向板料内扩展。
如果间隙合理,则上下两裂纹重合;
如间隙不合理,则在上下裂纹中间再产生第三条裂纹。
此种板料的断裂分离过程称为双向裂纹分离理论。
图4—3典型的裂纹产生与发展过程
4.2.3变形区的应力分析
4.2.3.1变形区受力状况
冲裁时凸、凹模刃口作用于材料的力示于图4—4。
主要包括:
PP、Pd——凸模和凹模作用于材料上的垂直压力;
FP、Fd——凸模和凹模作用于材料上的水平压力;
图4-5冲裁力引起的应力示意图
图4-4冲裁变形区受力图
1-凹模刃口2-材料3-凸模刃口
μPP、μPd——凸模端面和凹模端面作用于材料的摩擦力;
μPP、μPd——凸模侧面和凹模侧面作用于材料的摩擦力;
M——FP、Fd不在一直线上而产生的弯矩M,它使材料产生弯曲;
M'
——Fp和Fd所形成的抗弯矩,保持冲裁过程每一瞬间的平衡。
垂直压力使材料分离,摩擦力使模具刃口部分产生磨损。
4.2.3.2变形区应力状态
冲裁时的变形区是以凸模和凹模刃口连线为中心的纺锤形区,由于受冲裁时板材弯曲的影响,变形区应力状态很复杂,由冲裁力所引起的应力状态示意图如图4—5所示,而塑性变形阶段的各点的应力状态如图4—6所示。
图4-6变形区内各点应力状态
A点——三向应力状态。
σ1为凸模侧压及材料弯曲引起的压应力;
σ2为弯曲引起的压应力与侧压引起的拉应力的合成应力;
σ3为凸模下压引起的拉应力。
B点——由凸模下压和材料弯曲引起的三向压应力状态。
C点——沿材料纤维方向为拉应力σl,垂直于纤维方向为压应力σ3。
D点——材料弯曲引起径向拉应力σ1和切向拉应力σ2,凹模上平面材料受到压挤产生轴向压应力σ3。
E点——材料弯曲引起的拉应力和凹模侧压引起的压应力的合成应力σ1和σ2,应力符号一般为正;
凸模下压引起轴向拉应力σ3。
4.3冲裁件的质量分析
4.3.1断面质量
对冲裁件断面质量起决定作用的是冲裁间隙及模具刃口状态。
从冲裁变形过程分析可
知,冲裁时,裂纹不一定从凸、凹模刃口处同时发生,上、下裂纹是否重合与凸、凹模刃口间隙的大小有关。
间隙过小时,最初从凹模刃口附近发生的裂纹就指向凸模下面的高压应力区。
因此,这个裂纹的成长受到抑制,不能达到凸模刃口处,而成为滞裂纹,如图4—7所示,当裂纹口开得相当大的时候,两裂纹中间的一部分材料随着冲裁的进行将被第二次剪切,继而被凸模挤入凹模腔内。
由于凹模刃口的挤压作用,在断面上形成第二光亮带,在两光亮带间形成撕裂的毛刺和夹层,如图4—7a所示。
图4—7间隙对冲裁间断面质量的影响
(a)间隙过小(b)间隙合适(c)间隙过大
间隙过大时,由于在光亮带形成之前,板料已形成较大的圆角带,所以实际的间隙就显得更大。
在这种情况下,如图4—7(c)所示,因为上、下裂纹错开一段距离,且圆角带大,所以断面的垂直度差。
又由于加工条件的不同,裂纹也不一定在上、下两刃口处同时发生,所以有时硬可能由一个刃口发生的裂纹使材料分离。
当这个裂纹从一个刃口的尖端出发,扩展到另一个刃口的侧面时,在断面上留下很大的毛刺。
因此间隙过大时,断面上的光亮带减小,圆角、毛刺及斜度变大。
间隙合理时,上、下刃口处产生的裂纹,在冲裁切断过程中会合成一条线,如图4—7(b)所示。
在这种情况下所得冲裁件的断面光亮带较大,而圆角带及毛刺和斜度均较小,表面也比较平整,断面与平面质量均可达到理想的效果。
由上述分析可知,间隙过大或过小时,冲裁件的断面质量都较差,只有在合理间隙时,才能使冲裁件的断面质量符合标准。
间隙分布的均匀性对冲裁件的断面质量同样具有很大的影响。
当刃口沿周间隙分布不均
匀时,将使制件产生局部毛刺。
在间隙大的地方产生拉长毛刺,在间隙小的地方产生挤毛,并加快模具刃口磨损变钝,使模具寿命缩短,所以不仅要选择合理的间隙,而且在制造、安装调整冲模时,应保证间隙均匀。
当模具刃口磨钝时,在冲裁件的边缘会产生很大的毛刺。
凹模刃口磨钝时,在落料件边缘产生毛刺,凸模刃口磨钝时,在冲孔边缘产生毛刺,凸、凹模刃口都磨钝时,则在落料件及冲孔件边缘均产生毛刺。
毛刺是冲裁件的常见疵病。
若冲裁件的技术要求规定不允许毛刺存在时,则在冲裁后要设法清除。
清除毛刺的方法很多,对较厚的中小零件可用滚筒滚光或振动法去毛刺,对于较薄或较大的零件可用双轴轧辊碾平,也可用砂带磨床磨去毛刺。
一般冲裁件允许的毛刺高度见表4—1。
在冲裁过程中凸模要压入材料,材料要被挤进凹模洞口,材料对模具产生侧压力,间隙越小,侧压力越大,由此而产生的摩擦力(板料与凸模侧壁和凹模洞壁之间的摩擦力)也越大,从而使凸、凹模侧壁的磨损加剧,甚至因摩擦发热严重而使材料黏结在上面,致使摩擦力进一步增加,使模具刃口很快磨损,模具寿命大大降低。
间隙较大时,凸模侧面与材料的
表4—1一般冲裁件允许毛刺高度(mm)
摩擦力小,减少了磨损。
但间隙取得太大时,因弯矩与拉应力增大而导致刃口损坏,因此不能无限制地取大间隙。
4.3.2尺寸精度
冲裁件的尺寸精度是指冲裁件的实际尺寸与设计尺寸的差值,差值越小,精度越高。
在理想情况下,落料件的尺寸与凹模刃口尺寸相同,而冲孔件的尺寸与凸模刃口尺寸相同。
实际上,由于冲裁时工件受力而产生一定的弹性变形,冲裁结束后,工件就会发生弹性恢复现象,从而引起落料件尺寸与凹模刃口尺寸、冲孔件与凸模刃口尺寸不相符,影响了冲裁件的尺寸精度。
影响冲裁件尺寸精度的因素很多,如冲裁间隙、冲模制造精度、材料性质与厚度、冲裁件的形状和尺寸等,其中主要因素是冲裁间隙。
当凸、凹模间隙过大时,冲裁过程中材料所受的拉延作用较大,因而拉延变形大。
冲裁结束后,因材料的弹性恢复使落料件尺寸缩小,而冲孔件尺寸增大。
当间隙过小时,由于材
图4—8间隙对冲裁件精度的影响
料受凸、凹模挤压而产生压缩变形。
冲裁后因材料的弹性恢复使落料件尺寸增大,而冲孔件的尺寸缩小。
图4—8所示为间隙对冲裁件精度的影响关系图。
图中曲线与δ=0的交点为最合理的间隙值。
在合理间隙时,制件尺寸与模具刃口尺寸完全一样,交点右边表示制件与模具间是松动的。
若采用交点右边较大的间隙值,则制件与模具之间摩擦力小,所需冲裁力也小,但冲裁件拱弯大,使制件的弹性恢复也大。
因此,间隙过大或过小都会使冲裁件尺寸有较大的偏差,尺寸精度降低。
只有在合理间隙时,冲裁件尺寸最接近模具刃口尺寸。
冲裁件的尺寸精度还与材料的性质和厚度有关。
因材料的性质直接决定了板料在冲裁过程中的弹性变形量,较软的材料,弹性变形量较小,冲裁后的弹性恢复量也较小,使制件精度较高;
较硬的材料,弹性变形量较大,冲裁后的弹性恢复也较大,使制件精度低;
薄料冲裁时,弹性拱弯大,弹性恢复也大,使制件精度低。
此外,尺寸精度还与零件形状和尺寸大小有关。
零件尺寸越大,形状越复杂,模具制造调整就越困难,模具间隙不易保证均匀,故尺寸偏离就越大。
上述因素对冲裁件尺寸精度的影响是在模具制造精度一定的前提下讨论的。
若模具刃口制造精度低,则冲制出的零件精度也无法保证。
所以,凸、凹模刀口尺寸的制造公差要按工件的尺寸精度要求来决定。
冲模制造精度与冲裁件精度之间的关系见表