浸出作业指导书Word文件下载.docx
《浸出作业指导书Word文件下载.docx》由会员分享,可在线阅读,更多相关《浸出作业指导书Word文件下载.docx(6页珍藏版)》请在冰豆网上搜索。
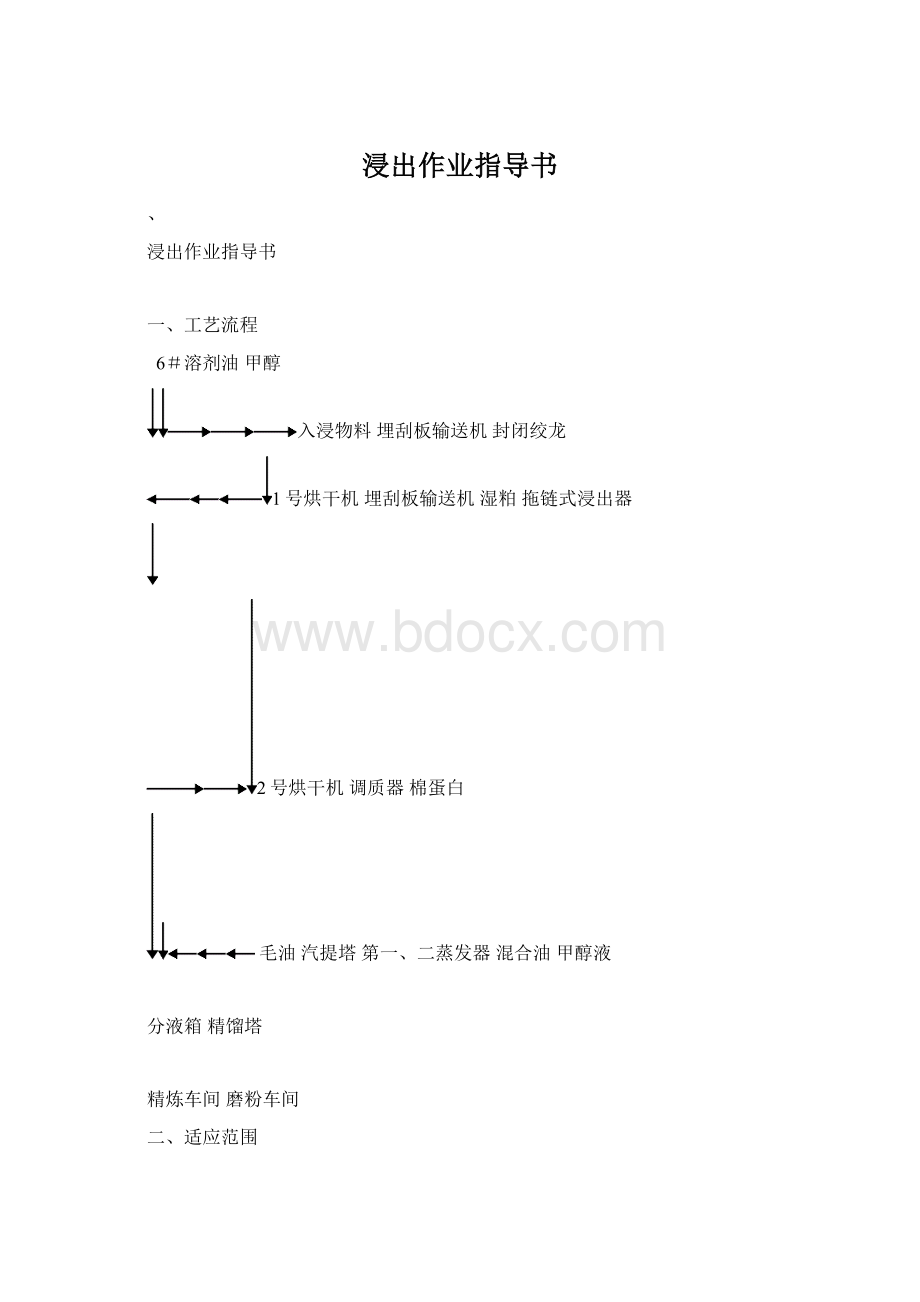
本规定适用于脱酚车间浸出过滤系统(拖链式浸出器、甲醇、混合油过滤机)、烘干系统(1、2号烘干机、调制器)、蒸发系统(1、2号蒸发器、汽提塔、溶剂周转管、蒸煮罐)、甲醇精馏系统(精馏塔、废水暂存罐、1、2、3号分液箱)、冷凝回收系统(冷凝器、冷却塔、循环水泵、石蜡回收系统)等附属设备设备操作。
三、开机操作
1、操作步骤
开机前准备
1.1打开浸出车间的所有通风门窗,保持车间空气充分对流。
天冷时可关闭墙体上端窗户,下端窗户要保持开启。
1.2检查所有消防器材是否完好,是否安置在规定的位置、试运行消防报警系统,检查是否完好。
1.3检查车间内所有电器及设备运行及安全状况,对电器设施及各台单机设备进行保养和空试运行、清理容器内所有工具、杂物,并检查设备安装是否正确,各轴承部位是否加注润滑油。
各设备安全防护措施是否到位。
1.4检查各设备使用的压力表、温度表、电流表是否完好灵敏;
认真检查所有管道、阀门是否正确开启、关闭;
检查所有容器、视镜、人、孔设备密封位置是否完好
1.5开启车间电源,启动冷却系统,开启水泵,检查所有设备有否滴漏,调整各冷凝器的水量(水温≤35℃),分水箱内加注足量清水,启动冷冻机组,开启1、2号真空泵,观察真空表,保持设备内负压状态。
1.6开启引风机及石蜡回收设备
1.6通知锅炉车间供气,检查供汽系统是否跑、冒、滴、漏。
a、打开用汽设备的排汽阀,排空冷凝水。
b、打开用汽设备的进汽阀预热,由小到大慢慢开启。
1.7打开溶剂、甲醇计量箱进口阀门,开启溶剂、甲醇库阀门及油泵,泵入溶剂及甲醇,计量后方可打入浸出器内,浸出器内集油格应保持足量溶剂和甲醇。
1.8待浸出前后工序准备完备,通知前路开始送料。
2、浸出器开机
2.1开启进料刮板给存料箱存料,正常存料高度不小于1.4米。
2.2气温在零下时,应给溶剂、甲醇进行预热,(溶剂油温度预热到45—50oC)。
2.3开启拖链式浸出器,封闭绞龙,1#刮板输送机给浸出器送饼料。
2.4待物料进入后,开启新鲜溶剂泵及新鲜甲醇泵给浸出器供溶剂油和甲醇,采用大喷淋和喷淋滴干方式,溶剂油和甲醇不得进入滴干段。
2.4.1料层厚度≥500mm。
2.4.2入料温度50—55OC。
2.4.3浸出器气相温度50—55OC,溶剂温度50-55OC,甲醇预热温度45~50OC。
2.4.4浸出器的周转为180—210分钟。
2.4.5正常进料状态下,溶剂用油量比为0.6~1.2:
1(溶剂油/料),新鲜甲醇油量比1.0~1.8:
1(溶剂油/料),混合油浓度为15~28%,浸出器内保持微负压。
2.4.6按顺序开启溶剂油、甲醇循环泵、混合油泵、过滤机等设备。
2.4.7存料箱料层高度应保持在视镜高度的60%,料层不够时应停止向浸出器送料,保持料封作用。
2.4.8经常观察料层的渗透情况是否正常,若发生渗透不畅或筛条堵塞现象,要及时查找原因,及时排除。
防止料面混合油有溢流现象。
2.4.9经常检查喷淋头是否正常,若堵塞应及时排除。
若堵塞严重泵入口无溶剂或甲醇进入,应及时停机排除,待排除故障后方可开车。
2.4.10经常检查浸出器物料状况,防止因喷淋过大引起混合液串流或流到下料口。
每半小时检查各个过滤器过滤效果,注意观察旋液分离器及沉降箱、混合油过滤机过滤效果,及时排放以上设备沉淀渣滓,保证液体过滤匀速通畅。
2.5各设备运转过程中要“勤看、勤摸、勤闻”发现异常现象及时处理,杜绝各视镜、阀门、法兰、密封部位跑、冒、滴、漏。
2.6及时与品管部门沟通,掌握粕中残油及棉酚含量情况,及时根据粕残油及含棉酚情况调整溶剂及甲醇喷淋量。
粕中残油小于1%,粕中游离棉酚小于400ppm
2.7溶剂集油格内冲渣装置每班次应及时冲渣一次,以免集油格内堵塞。
3湿粕脱溶工序
3.1在浸出器出料前顺序开启1、2号蒸烘机、调质器及输送设备(3、4号刮板、密封绞龙、出粕绞龙)
3.2调整蒸烘机温度,保持温度在70OC,物料烘干时间≥20分钟,间接供蒸汽压力调节为0.2—0.4mpa。
自由汽体出口温度≥70OC,出粕温度小于80OC,粕中残溶小于1000ppm。
3.3严格按工艺要求控制蒸烘机及调质器的烘干温度,时间、蒸汽压力。
保证出粕的温度、水分、残溶,若未达到要求,应及时采取措施解决。
3.4粕中残油超标时,应及时停止进料,待正常后方可在进料,进料要均匀,若有堵塞及时排除。
3.5调质器蒸脱层进料高度达到时,打开直接蒸汽阀调节压力0.03—0.1mpa,以喷不散料层为宜,溶剂蒸汽温度控制在70—80℃。
3.6注意观察调质器蒸料层自动控制门,防止假象下料后患。
底层始终要保持一定高度,起料封作用,防止粉末四溅,混合蒸汽乱窜。
3.7棉粕水份控制在8%左右,水份过高,调节进汽阀门保持压力0.5—0.7mpa,勤通排汽,保持畅通;
水份过低,调节蒸汽压力小些或者关闭底层和几层烘干层蒸汽阀门。
3.8粕中含溶达不到要求,粕温超过60℃时,不得包装出车间。
4混合油蒸发工序
4.1开启混合油泵给混合油罐供混合油当混合油进入储罐容量的20%时,蒸发器放空积水,徐徐开启间接蒸汽,加热5~10分钟;
当混合油进入储罐的50%时,混合油即可向第一蒸发器进油。
a、经过旋液分离器混合油初过滤。
b、沉降过滤(利用混合油罐,自然沉降,定期排除沉淀余渣)。
C、开第一、第二蒸发器时,先开启蒸发器的进油阀门,当混合油进入汽提塔时,开启过热直接汽加热器,间接蒸汽要保持在0.4MPA左右。
4.2开启2号蒸发器,汽提塔间接蒸汽蒸汽阀门。
4.3第一蒸发器间接蒸汽采用蒸烘机二次蒸汽加热如果二次汽量不够时,可以通过蒸汽进行补充,使用蒸汽时,压力调节0.2-0.3mpa,混合油浓度65-75℃,混合油浓度60-65%。
4.4第二蒸发器间接蒸汽压力调节在0.2—0.3mpa,出口温度100-110℃,混合油浓度90-95%。
4.5汽提塔间接蒸汽压力0.3-0.4mpa左右,直接汽0.02-0.06mpa,在使用直接汽时,必须进行分水后才能喷入汽提塔,毛油出口温度为100-115℃,视情况调节直接蒸汽,防止毛油乳化。
4.7经常观察掌控混合油的液位、流量和温度。
防止蒸发器液泛(翻罐)和油管堵塞。
4.8定期清理高位罐、汽提塔及1、2号蒸发器底部油渣,以免影响蒸发及汽提效果。
4.9严格按照工艺技术要求掌握各设备混合油的液位,流量、温度、浓度、蒸汽压力、界面位置、保证毛油质量。
5溶剂、冷凝回收工序。
5.1经常触摸和查看冷凝器冷却情况。
5.2严格按照工艺要求调解水和温度,保持冷却水温低于≤35oC,液相温度≤40oC,调节水温或添加冷却水。
5.3溶剂液入口不许有雾化现象,溶剂液温度不得大于55oC。
5.4防止供水中断,采取应急措施,一是供水泵有配用泵,二是断水无法及时采取措施弥补,就应立即停机,关闭蒸气,减少不必要的溶剂损失。
5.5经常观察分液界面,以保证两相间不互相夹带,经常检查1、2号分液箱的甲醇、溶剂油的界面,严禁将甲醇带入浸出器及溶剂油分水箱内
5.6溶剂循环罐、甲醇循环罐及中间罐的液位要保证不低于罐的1/3。
溶剂周转罐禁止从罐底抽溶剂,防止将积水带入浸出器。
5.7定时检查封水池,发现有溶剂溢出,立即收回,检查其它设备没跑溶剂。
5.8观察一、二号蒸发器及汽提塔回收溶剂液流情况。
如发现溶剂油分液界面有混合油时,应立即检查蒸发器及汽提塔是否有液泛现象,如有,应及时关闭进油阀门,故障处理后,方可从新进油生产。
5.9各冷凝器液出口温度小于40oC,自由气体出口温度小于20oC;
蒸煮罐温度保持在92~98oC;
蒸煮罐出水含溶不得高于500ppm;
最后冷冻机排放的尾气溶剂浓度低于20g/㎡;
两种溶剂不得互相夹带。
5.10所有设备内废水需经过精馏塔精馏后,方可排放至封水池。
6甲醇精馏工序
6.1打开塔釜进水阀门,往储水罐内注入清水,启动废液泵,将清水泵入精馏塔提馏段流入塔釜,至水位没过加热管时停止泵水,同时,启动冷却循环泵。
6.1.1温塔,给塔釜加汽,蒸汽压力控制在0.1-0.15mpa,使整个精馏塔处于热机状态。
待塔顶温度达到90oC左右,冷凝器有冷凝液流出时,温塔结束。
6.1.2将精馏塔釜内中泵入适量甲醇,开启蒸汽阀门,使精馏塔进行全回流操作。
操作稳定后,等待泵废甲醇。
当废液达到一定量时,开启甲醇泵,泵入废甲醇,调整回流比,进入正常操作。
,
6.1.3当甲醇酚液暂存罐液位达到要求后,启动甲醇精馏回收系统。
将甲醇从一号中间罐泵入精馏塔提馏段,流量从0.5m3/h逐渐增至2m3/h左右,观察冷凝液的流动是否正常。
当精馏回收的甲醇在2号中间罐有一定液位时,启动2号甲醇泵将甲醇泵入塔顶精馏段,根据塔顶的温度变化,调整流量在0.5m3~1m3左右,控制塔顶温度稳定在69oC~71oC间,塔釜温度100~105oC进料温度68~70oC,再沸器蒸汽压力0.1~0.3MPa,塔釜压力0.01MPa。
6.2当在沸器和塔釜的液面较高,液面较粘稠时,就要准备排放废液,塔釜排除的酚水溶液含溶剂小于0.5%。
每班应排放一次。
排放前做好如下准备
6.2.1通知控制台做好排放准备;
6.2.2降低三个中间罐的液位,时停止精馏后有足够的蓄液空间
6.2.3停止进液以提升再沸器温度,必要时打开直接蒸汽阀以加速升温速度,此时仍要使回流控制塔顶温度不超过72oC。
6.2.4塔釜温度达到95oC以上时,停止回流;
当塔釜温度超过99oC时,关闭蒸汽阀门,打开塔釜底阀排放废液。
禁止在温度不够时排放废液。
6.31号分液箱出来的两种溶液严禁互相夹带,发现互相夹带现象要从新分液。
6.4定期清理精馏塔,再沸器。
生产中发生效果降低,不能达到生产要求,必须停车清洗后再生产。
7停机操作
7.1通知预处理车间停止进料,按顺序依次停止各输送设备的运转。
如是短期停车,存料箱内应保留1.4m高度的物料。
7.2走空浸出器内物料,其间溶剂及甲醇继续喷入,待物料走尽后,停止浸出器,开启放空阀门。
7.3蒸烘机、调质器物料走空后,继续运转10~15分钟,然后依次停车。
7.4混合油蒸发完毕,依次关闭第一、第二长管蒸发器的进油阀,然后关闭蒸汽阀,放空设备内积水和存汽,待汽提塔的混合油全部走空后,停止供汽(间接、直接汽),关闭毛油泵。
7.5精馏塔内的物料全部蒸发完毕后,待塔顶塔釜再沸器的温度达到要求后,停供蒸汽,放掉设备内冷凝水及存汽,排出塔釜液。
7.6待混合蒸发、烘干系统、精馏系统的溶剂全部蒸发完毕30分钟后,才能停止冷却水循环泵,排空冷凝系统内积水。
7.7长期停车时,应用水压空各个设备内溶剂及甲醇,使其回收溶剂、甲醇至总溶剂库。
7.8回收完毕后,排空设备内积水,并开启所有人孔、视镜、阀门等部位进行消溶处理(消溶时间为3~5天),消溶完毕后,应检查消溶效果。
7.9车间停车处理完毕后,由车间负责人组织人全面检查各处是否符合安全要求,检查达到要求后,关闭车间所有门窗,上锁。
新疆塔里木震企生物科技
有限公司
脱酚车间
作业指导书
2010年10月1日