模具使用培训Word格式.docx
《模具使用培训Word格式.docx》由会员分享,可在线阅读,更多相关《模具使用培训Word格式.docx(13页珍藏版)》请在冰豆网上搜索。
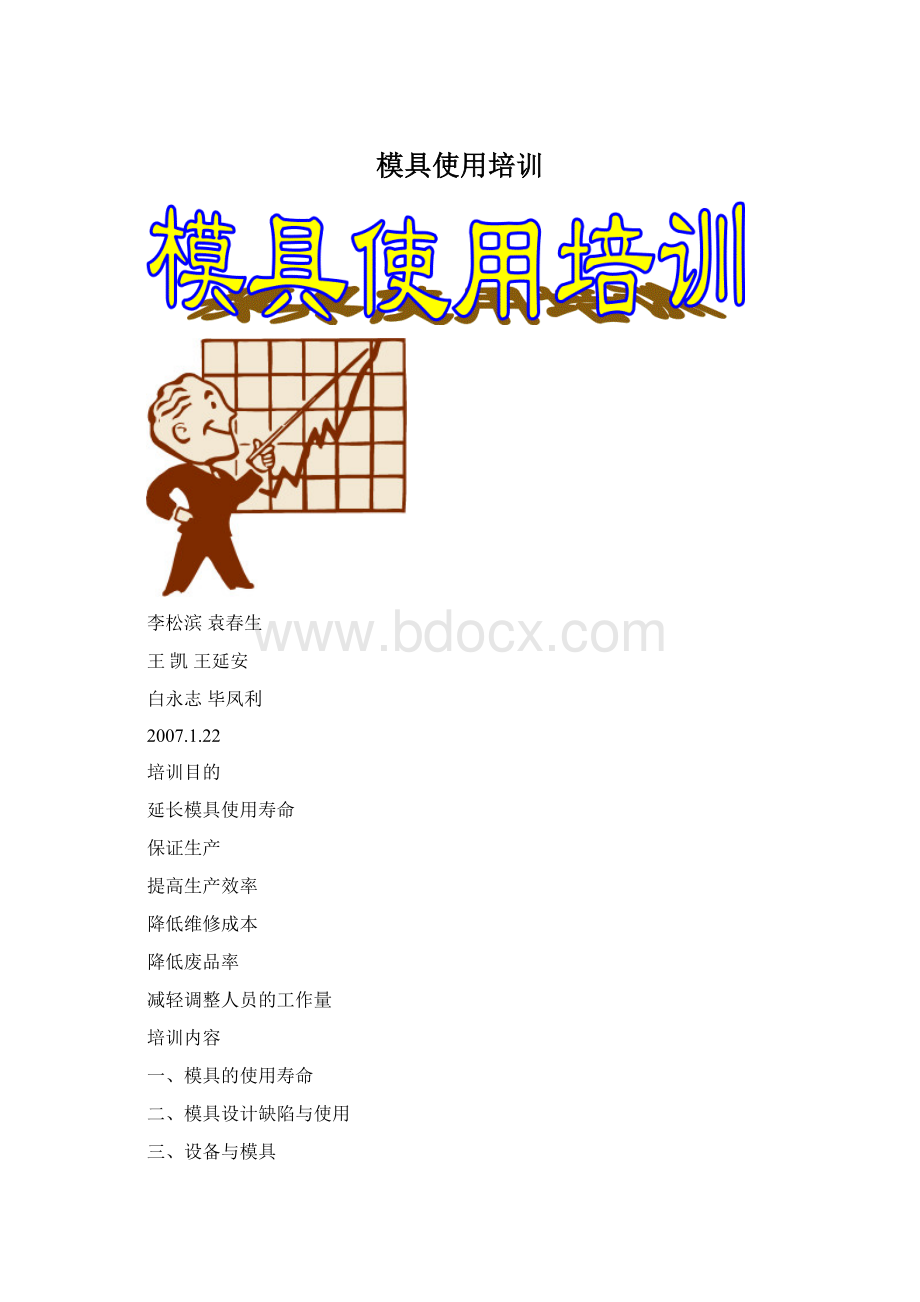
五、工艺参数与模具
六、TPM与模具维修管理
七、模具维修与保养
八、换模要求
九、生产中对模具造成损坏的常见情况
十、模具的使用原则
十一、模具常见故障的检查
十二、对模具使用的一些规定
一、模具使用寿命
1、国产模具的使用寿命相当于国外的1/3~1/5
1)模具生产方面:
50%
热处理不当45%
选材不合适、模具结构不合理25%
机械加工工艺不合理10%
模具滑润不好、设备问题20%
2)设计水平:
30%
3)使用不当20%
模具型腔表面粗糙度改善一倍,就可使模具使用寿命提高50%,所以模具在生产过程中加工要非常精细,使用时也必须保持模具表面光洁。
二、模具设计缺陷与使用
1、模具设计要求有一定的强度,强度不够,给使用增加难度。
红旗衬框,滑块多,导柱细,结构复杂,能体现技术水平,但对使用要求注意的事项就多。
稍不注意,模具就被损坏
2、同心度:
挂头位置,顶出的位置也是在受力中心点上。
导柱,模具导向不平衡,易损坏模具。
打单腔的坏处
3、保证由模具生产出来零件符合设计要求,避免应力集中,应力集中,件容易开裂,遇到有机溶剂,显现特别明显
4、脱模角度不合理:
开模时形成真空,拔模,制件留在定模,模具打不开;
脱模划伤(丰田雾灯壳体,宝来A5尾灯1反射镜)
5、顶出位置不合理,生产中易造成制件顶白、顶漏,顶针易损坏(C6尾灯面罩)
因此对模具的主要工作零件,注塑模的动、定模,要求其导向精度高、同心度和中性好。
设备的状态直接影响模具的使用,其对模具的影响如下:
1、开合模压力与速度:
2、低压保护:
如果设备不设置低压保护,一旦出现问题,对模具的损害是致命的,直接造成的后果轻则分型面堆,重则模具型腔损坏,即使能修理好,模具的使用寿命至少要减少50%,同时打出的件会出现毛边,通过再次修模,很难去除的毛边。
3、射台压力与速度:
射台压力太小,注嘴易跑料,压力和速度大,在射台前进时容易损坏模具浇口套和注塑机嘴,最好的办法是用低压中速前进射台,机嘴与浇口套接触上后,在把射台压力加到合适值。
大家在实际操作中往往都忽视这个参数,不经意间就造成模具和设备的损坏。
4、设备参数配置:
每台设备在采购之初都根据我们生产的实际需要,做好了配型,有些功能是我们特意要求的,可能有些功能我们没有要求,所以即使同样的设备,配置和功能也不完全相同。
我们常常关注的只是温度范围、最大、最小注射压力、最大、最小注射速度,其他的如螺杆直径及罗纹的深浅,设备的最大注射量、最大顶出距离、容模量等等,实际工作中很少考虑到。
就是这些不起眼的参数,对我们工艺参数调整影响是非常大的。
我们的模具在设计时就考虑到用什么样的注塑机来生产,设计时上述设备参数是都要考虑到的,如果大马拉小车,那么锁模力太大,模具承受不起,容易损坏模具,同时也浪费资源;
如果小马拉大车,比如按90T设备设计的模具,放到60T设备上打,可能容模量达到极限,容易损坏设备和模具,或者锁模力不够,件容易涨模,工艺参数不好调整,温度控制不准,制件质量不一致。
能否不按模具设计的要选择其他设备来生产,要看模具的结构、所用原料的类型、以及之间的质量要求标准等来确定。
四、原材料与模具
模具设计时就考虑到了所用原料的特性来确定模具的材质、精度等等。
比如:
设计时是按打PC料设计的,那么实际生产中如果用PC打件没问题,如果换用PA打件,那么制件就会有毛边,原料的流动性决定模具的精密度。
原材料的熔融度:
生产中原料熔化时间太长或者温度太高,容易涨模,熔融不好,注射不充分,打不满,制件表面也不光亮。
涨模对模具的损害也很严重,涨过一次模后,下次再生产就可能出现毛边,模具的分型线就已经受到了损坏。
原材料的干燥度:
原料干燥不充分,打出件有银丝或者气泡,同时水分的蒸发,对模具有一定的腐蚀作用,容易涨模。
我们捷达的线路板模具后来只能打一腔与用不烘干的料打件有很大关系。
五、工艺与模具
搞注塑工艺,首先是设备、模具、原材料,然后才是工艺。
设备一般情况下是固定的,原材料的种类也是有限的,模具是经常变化的。
所以做好工艺,首先必须很好的了解模具结构,不是每套模具拿来都可以一样来操作调整的。
对模具了解不够,是我们实际生产中造成模具损坏的直接原因。
工艺参数的设定值与实际值一定要分清,零位不准,设定的值与实际值差距是很大的。
如下图:
工艺好做,最重要的是监控,在生产过程中如出现异常,首先应看以下几项是否正常:
1、机筒温度
2、模具温度
3、水管接的正确否
4、原料烘干
5、人员工作是否正常
6、工作环境是否异常
7、是否按要求操作
8、设备是否工作正常
9、模具是否正常
如果以上都没问题,然后才能看工艺参数是否改变了。
正常情况下,生产工艺参数在整个生产过程中是不应该改变的。
工艺参数的设定是根据所用原材料的种类以及模具结构、制件结构和壁厚大小来决定的,其中模具的结构在实际生产中是很少有人考虑的。
不同的模具结构,对生产工艺的要求有很大区别,有些模具比如:
红旗前灯衬框,滑块多且很单薄、导柱细,模具本身承受不起高的注射压力,锁模力小,模具锁不住,涨模就会损坏模具。
此模具本身的材质还可以,能承受高的锁模力,所以应采用低压高速、高锁模力来生产。
锁模松紧根据模具状况来定,模具锁的太紧容易损伤分型面,锁的松,容易涨模,这个参数设置需要根据模具结构、工艺条件来确定,不能随意。
在实际生产中,我们有些模具打件使用的注射压力达到了注塑机的最大值,这样不仅对模具损害大,对设备的损害也是非常大的。
生产中黑点产生的原因:
生产中零件有黑点,与模具的关系不大,主要原因有:
1)PC、PMMA用一个机筒生产,打完PC料再打PMMA料或者打完PMMA再打PC料都会出现大量黑点,最好的解决办法就是此两种料避免用一台设备生产。
2)料分解,料分解后,再生产,也会有黑点产生。
3)原料不洁净。
以上三种原因都可以通过清洗机筒的办法解决,最不好清的是第一种原因。
清机筒,方法要得当,要少上料,把料挤净后再少一点上,再挤净,反复多次,清机筒的料不能融化的太好。
4)顶出块或者滑块研了,产生的铁屑,所以在日常生产中我们要保证模具润滑和清洁,这些工作是不能依赖维修工来做的,这就要大家一起来保养维护模具,也就是需要全员参与生产维护
六、TPM全员参与生产维护
在中国企业,因为文化与传统的不同,企业员工平均文化水平不同,习惯和素养不同造成了安装TPM会更加困难。
具体表现在:
做事随意,没有规矩;
有了规矩,弄虚作假,不守规矩;
遵守规矩,却总是做不到位。
成功的TPM应解决的三个问题:
1、工人素质:
靠培训、教育,但不可能很快达到要求,制定适应员工水平的维护保养及维修行为规范,培训上岗。
2、工人愿不愿意:
靠企业文化、靠教育宣传,但有时远水解不了近渴,规范就是企业内部家法,每个人都要遵守。
制度允不允许:
制度可以改变以适应TPM的需要,也就是说,只要按照规范执行,制度就是支持(允许)的。
TPM的好处
提高产品质量
降低成本
提高设备的可靠性和正常运行时间
工作丰富化
加强操作和维护的团队协作
提高技能
更高的质量维护
安全的提高
1、维修
模具不能带病工作,有问题要及时解决,不要等毛病大了再修理,这样会严重影响模具使用寿命和制件的质量,同时也会给工艺调整带来很大难度。
维修要求:
1)模具报修时首先要填写模具维修单,内容要严格按表格的格式填写,表格里面的内容都是有用的,完整填写便于确定损坏原因,不是要追究谁的责任问题,是要准确掌握产生问题的根本原因,能更好的预防类似事情的重复发生,是为了从根本上解决问题;
掌握模具状态、维修进度以及便于和有关人员联系,有助于信息沟通。
2)要提供给维修人员正确的信息,在使用过程中模具状态以及出现的异常情况。
3)维修完毕模具在下次使用时要填写模具维修保养验收单。
2、为提高模具使用寿命,保证模具在好的状态下工作,保证产品质量,减少调整人员的工作量,模具要定期进行状态检查。
同时填写模具状态检查表,检查中发现模具附件缺失的,模具厂负责给予配备齐全,如还有其他模具问题,可以及时送交维修。
3、模具维修,很多时候需要有数据,才能加工修理,所以在使用过程中,一定要保护好模具的模具的基准面,模具基准面是模具在数控加工时定位的标准,基准面稍有变化,就能造成模具型腔加工不准,偏差大,从而打出的件尺寸不合格。
基准面在使用是要保证不能生锈,不能磕出坑。
以前我们在使用过程中几乎不注意这个问题。
4、维护保养,模具保养是变被动维修为主动预防,因而减少因模具问题带来的生产不及时和质量损失。
模具保养的好,会给生产带来很大的便利。
保养可以保证模具一直在好的状态,减轻生产调整工作量;
保养好可以延长模具使用寿命,提高模具使用率;
可以降低废品率;
模具保养包括日常保养和定期保养,日常保养需要使用部门在使用时保持模具清洁,监控模具状态。
定期保养需要卸模时间和开模数,所以要求调整工及时把卸模信息提供给有关人员。
1、装卸模具首先要检查吊环、吊钩是否安全可靠,模具吊装点是否能保证模具平衡,确认可靠后才可装卸模具。
2、吊装模具时不能吊得过高,只有到设备跟前才可吊到规定高度。
3、往设备上把模时要检查压板、螺丝、垫铁是否合适,不合格的螺丝、压板严禁使用。
4、把模时螺丝必须拧入螺纹直径的1.5-2倍,并要确保拧紧,垫铁要压在压板一端,不得紧靠螺丝,要保证支点的距离。
5、把模的压板应根据模具具体情况确定数量,确保对模具有足够的压紧力。
6、装卸一半模具时,必须把设备开大,千万注意不得碰撞另一半模具。
7、装卸模具时,要保持吊车与设备步调一致,要用慢速对定位环,对模。
8、连杆、挂头要上好,保证连接可靠。
9、当动模、定模单独上时,必须将动模顶出退到位,滑块放到规定位置,以防损坏模具
10、上水管时,定模必须保护好,不允许溅上水点。
试水时要合模试,以免水管漏水溅到型腔里。
11、有液压抽芯的模具,进出油管要连接正确,确保不漏油,开机设定好抽芯压力、速度、控制方式,注射时,抽芯要保持,设定好后,用手动试验抽芯动作是否正确,正确后连接电信号再试抽芯,电信号正确后,开合模试验抽芯动作,正确后可开机生产。
12、有热流道的模具要连接好热流道控制器,按工艺卡规定设定好温度。
13、油管、水管、电信号线必须固定好,防止开机造成损坏。
14、调模时,模具不要锁太紧,合模要慢,避免撞伤模具。
15、调顶出,不得调得过长、过紧。
16、卸模具时,先合模把模具外表面擦净,然后吹净模具水道内水,再卸水管,如果卸一半模具,也要把水吹净再卸水管,同时另一半必须保护好,不允许溅上水点或碰伤。
17、保持模具清洁,导柱、导套上高温润滑油,要少量多次。
18、换完模后,必须把水试好,如果当时不打件,把模具合上,不要合死,然后关机。
19、使用机械人或机械手取件时,要将取件抓具上好,开模位置调好。
20、卸下的状态完好模具要放到规定的模具存放区,有问题的模具放到模具维修区。
21、所有上模、卸模、模具维修、模具保养都要按规定填写记录。
九、生产过程中对模具造成损坏的常见情况
1、注塑工艺参数不合理
2、调模不当
3、带件合模:
由于制件脱模不良或者参数不合理,造成制件留到定模上,出现这种情况,一般情况下是绝对不允许带件合模的,如果是有经验的人员可以视模具状况、模具结