减少合成石英玻璃中的气泡的研究文档格式.docx
《减少合成石英玻璃中的气泡的研究文档格式.docx》由会员分享,可在线阅读,更多相关《减少合成石英玻璃中的气泡的研究文档格式.docx(9页珍藏版)》请在冰豆网上搜索。
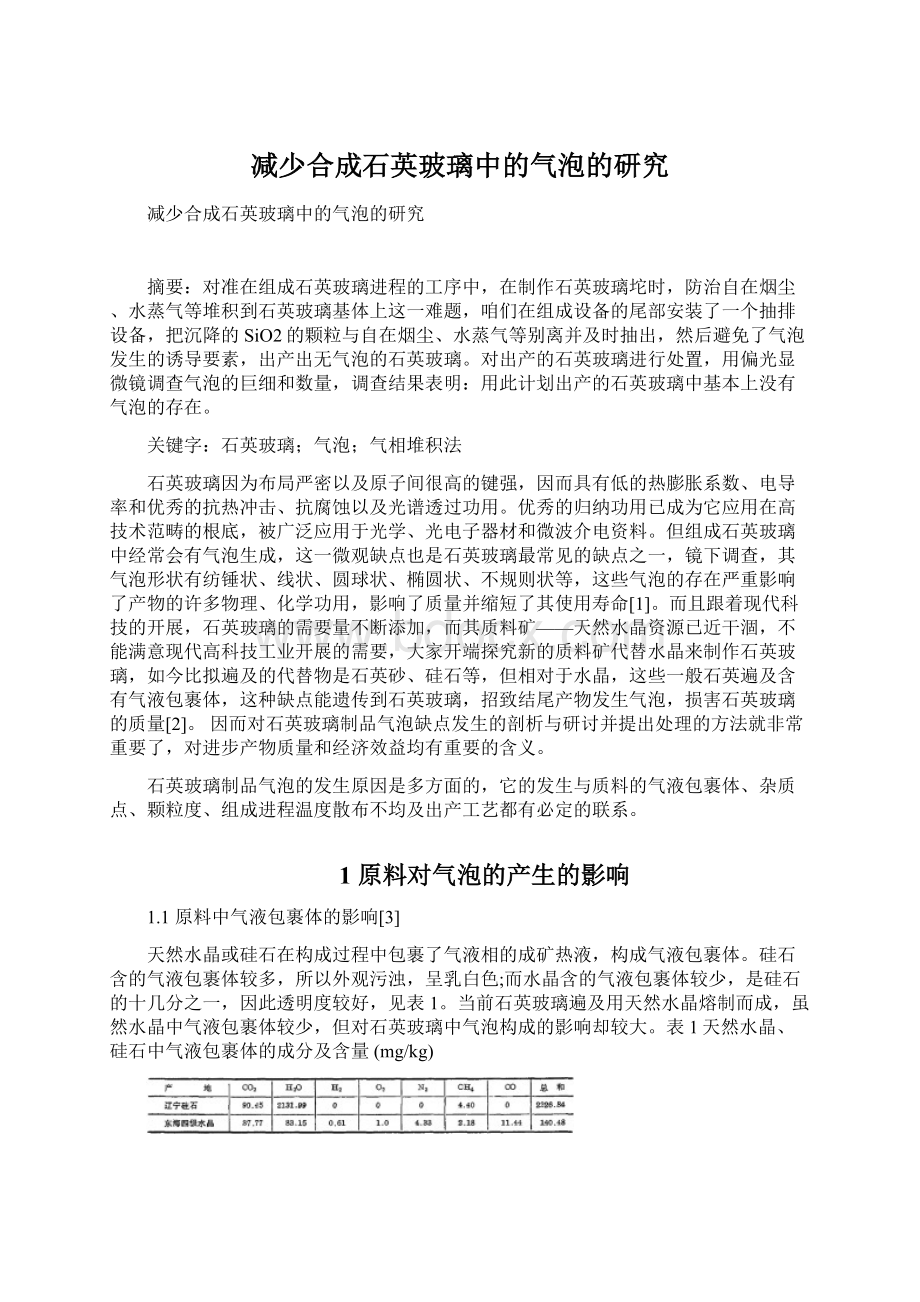
但组成石英玻璃中经常会有气泡生成,这一微观缺点也是石英玻璃最常见的缺点之一,镜下调查,其气泡形状有纺锤状、线状、圆球状、椭圆状、不规则状等,这些气泡的存在严重影响了产物的许多物理、化学功用,影响了质量并缩短了其使用寿命[1]。
而且跟着现代科技的开展,石英玻璃的需要量不断添加,而其质料矿——天然水晶资源已近干涸,不能满意现代高科技工业开展的需要,大家开端探究新的质料矿代替水晶来制作石英玻璃,如今比拟遍及的代替物是石英砂、硅石等,但相对于水晶,这些一般石英遍及含有气液包裹体,这种缺点能遗传到石英玻璃,招致结尾产物发生气泡,损害石英玻璃的质量[2]。
因而对石英玻璃制品气泡缺点发生的剖析与研讨并提出处理的方法就非常重要了,对进步产物质量和经济效益均有重要的含义。
石英玻璃制品气泡的发生原因是多方面的,它的发生与质料的气液包裹体、杂质点、颗粒度、组成进程温度散布不均及出产工艺都有必定的联系。
1原料对气泡的产生的影响
1.1原料中气液包裹体的影响[3]
天然水晶或硅石在构成过程中包裹了气液相的成矿热液,构成气液包裹体。
硅石含的气液包裹体较多,所以外观污浊,呈乳白色;
而水晶含的气液包裹体较少,是硅石的十几分之一,因此透明度较好,见表1。
当前石英玻璃遍及用天然水晶熔制而成,虽然水晶中气液包裹体较少,但对石英玻璃中气泡构成的影响却较大。
表1天然水晶、硅石中气液包裹体的成分及含量(mg/kg)
实验中测定了气泡气体成分(见表2),气泡中大多含有CO2,CO和H2S,这三种气体成分是水晶气液包裹体带入的,大气泡中的H2O、CH4及小气泡中的SO2等也是由天然水晶气液包裹体带入的,文献报道,天然水晶中普遍含有H2S和SO2气相杂质;
N2、O2是水晶粉体间隙裹入的空气成分;
H2是水晶粉体裹入的燃烧气体。
从表2可以看出,水晶中气液包裹体在石英玻璃气泡中的含量约占70多以上,是形成石英玻璃中气泡的主要气体。
表2气炼石英玻璃中气泡气体成分及含量(mol%)
水晶的水淬温度对石英玻璃中气泡形成的影响见表3。
可以看出,900℃水淬料产生的平均气泡密度是550℃的一半,因为900℃缎烧水晶比550℃缎烧时排除气液包裹体更充分。
岩相分析结果,东海一级水晶气液包裹体含量为0.01%左右,而东海四级水晶在4%~5%,包裹体最大尺寸70μm,最小约1μm,一般为十几μm左右,由于气液包裹体太小,所以用煅烧和机械粉碎方法消除气液包裹体是有限的。
表3水晶水淬温度对石英玻璃中气泡形成的影响
1.2原猜中杂质富集点的影响[4]
杂质富集点对石英玻璃中气泡构成的影响有两种状况:
①易蒸发的有机物杂质在高温时变成蒸气而构成一个气泡,在石英玻璃中能够见到有的气泡外围富含未彻底蒸发的云雾状黑点。
②不易蒸发的杂质点(如天然杂质矿藏、金属等)在石英玻璃熔体中易诱发析晶,因为方石英体积比石英玻璃小,析晶点处发作体积缩短而发作气泡,这种气泡又名真空气泡,它可能是因为石英玻璃熔体内部分发作析晶,体积缩短而发作负压,使溶解的气体又释放出来而构成气泡。
能够观察到石英玻璃中析晶点外围常呈球面,这是因为内部富含气体的原因。
1.3质料粉体颗粒度的影响
水晶粉颗粒度决议了水晶粉体的活动性及孔隙率。
活动性及孔隙率对熔制中发作气泡的影响较大。
一般说来,水晶粉体活动性愈好,孔隙率愈小,对熔制工艺愈有利。
图1标明,粒度愈细,静摩擦角愈大,愈不易活动。
图2标明,无论是严密堆积仍是松懈堆积,都显示出粉体颗粒度愈细,孔隙率愈大的趋势。
图1水晶粉体静摩擦角与颗粒度的关系
图2水晶粉体孔隙率与颗粒度的关系
1.紧密堆积;
2.松散堆积
粒度在100~150目时,水晶粉孔隙率是低谷,当粒度大于100目时,因为杆状料较多,孔隙率增大。
别的,水晶粉体对错金属粉末,在破坏过程中因彼此冲突而带静电,其间带正电粒子占42.5%,带负电粒子占53.1%,不带电粒子占4.4%。
颗粒度愈细,表面积愈大,带静电愈多,愈简单集合成团球,团球的颗粒细,团球表面熔化快,且因为石英玻璃熔体表面张力较大(约300dyn),团球表面的熔体向内缩短,包住内部未熔化的颗粒及颗粒之间的气体,待悉数颗粒熔化后,孔隙气体就构成气泡。
综上剖析,水晶粉体颗粒度太细,活动性差,易堵在送料管内,促进水晶粉体集合成团,加之颗粒度愈细,孔隙率愈大,水晶粉团球内包裹的气体愈多,因而构成气泡的几率也愈大。
图3表明晰水晶粉体活动状况与石英玻璃毛坯坨中气泡含量的联系。
当水晶粉体流通时,坨中气泡较少;
水晶粉体不流通时,坨中气泡较多,实验结果与上述剖析共同。
从消除气液包裹体方面思考,颗粒愈细,气液包裹体被破坏得愈多,愈能削减气泡的构成。
但从熔制工艺视点思考,颗粒愈细,愈不利于气泡的消除。
因而熔制工艺应对颗粒度有必定需求,颗粒度的最佳值需求经过比照实验断定。
图3水晶粉体流动性与蛇中气泡含量的关系
2不同工艺制备方法对气泡的影响[4]
目前,相关领域对石英玻璃的纯度及质量要求越来越高,如何从制备工艺上提高石英玻璃纯度、减少结构缺陷成为研究重点。
2.1石英玻璃制备方法
1)Ⅰ类石英玻璃管天然水晶粉在石墨增竭中电熔,高温下直接将石英熔体拉制成管。
2)Ⅱ类石英玻璃棒水晶粉在H2-O2火焰中熔制成玻璃锭,中频炉将玻璃锭加热软化而拉制成棒。
3)Ⅲ石英玻璃棒高纯SiCl4气相原料在H2-O2:
火焰中水解、熔制成玻璃锭,再经冷加工制成棒。
4)Ⅳ类石英玻璃棒高纯SiCl4在无氢的等离子火焰中高温氧化、熔制,玻璃锭在高温下拉制成棒。
其中Ⅰ、II、Ⅲ类由中国建筑材料科学研究总院制备,Ⅳ类由前苏联生产。
Ⅲ、Ⅳ类皆由化学气相沉积(CVD)工艺制成,统称合成石英玻璃。
2.2气泡缺陷测试方法
II、III、IV类玻璃样品按测试要求双面抛光。
用Leitz偏光显微镜(单偏光)观察玻璃中的气泡、气线。
2.3气泡缺陷
气泡是石英玻璃中的气态不均匀体,形状以圆球和椭圆形为主,大小从几个μm至几十μm甚至更大尺度。
图4为偏光显微镜下观察到的石英玻璃结构中典型的气泡缺陷,显微镜多量观察结果表明,Ⅰ、II类玻璃中气泡含量较多,而III、IV类玻璃中气泡相对较少。
对于I、II类石英玻璃,其水晶原料颗粒间充满气体,高温熔制过程中水晶粉烧结、液化并逐步排出颗粒间隙中的气体。
但烧结温度控制不当或温度场不均匀时,高温区粉料熔化成为高粘度的SiO2熔体,而低温区粉料仍处于烧结排气阶段,当高温区SiO2熔体包封低温区粉料的气体出口,颗粒间隙中的气体不能排出时将产生气泡。
气泡通常需上升到玻璃液面后才能排出,气泡在液体中的上升速度与液体粘度的关系式为:
(1)
式中,v为气泡上升速度,cm/s;
Δρ为液体与气体的密度差,g/cm3;
g为重力加速度,cm/s2;
η为液体粘度,Pa·
s;
r为气泡半径,cm。
按式
(1)计算,对于高粘度的石英熔体(1800℃时η=104.7Pa·
s),半径0.1mm的气泡上升速度数量级只有10-6cm/s,实践中很难依靠如此慢的速度澄清石英玻璃,所以若熔制工艺控制不当,极易导致工、II类玻璃中形成气泡。
在Ⅰ类玻璃管中还观察到线状气泡(即气线,见图5)。
气线主要由拉管工艺造成,其它几类玻璃中未发现气线。
对于合成石英玻璃,由于是在气相中反应熔制,一定温度下气体在玻璃中的溶解达到平衡,但温度波动时,平衡遭到破坏,气体就可能扩散聚集形成气泡。
因此,温度不稳定是产生合成石英玻璃气泡缺陷的重要因素。
图4石英玻瑞中的气泡缺陷
图5
I类石英玻瑞中的气线
3采用高频等离子体化学气相沉积(PCVD)方法合成超纯石英玻璃
3.1试验
用高频等离子发生器,通过感应线圈祸合灯具,使灯具内的气体电离产生等离子体。
利用等离子体火焰对石英基体加热,SiCl4气体分子由载流气体携带通过加料管喷射进入等离子火焰,在高温环境中发生如下反应
SiCl4+O2=SiO2+2Cl2
(2)
作为反应产物的SiO2微粒沉积在石英基体表面合成石英玻璃,实验装置示意见图6.
图6等离子体化学气相沉积合成石英玻璃实验装置示意图
3.2沉积过程模型
通过对沉积过程研究分析,提出了沉积过程模型,见图7。
图7描述了应用PCVD方法,原料SiCl4转变为石英玻璃的过程。
模型分为5个阶段:
1)化学反应阶段,载料气体氧气携带原料SiCl4进入等离子体火焰,在火焰内部高温作用下发生氧化反应生成SiO2;
2)质量传输阶段,反应生成的SiO2分子在等离子体火焰内部成核并碰撞团聚,形成较大颗粒;
3)穿越边界层,团聚的SiO2微粒在等离子体火焰内随高温的火焰气流到达边界层,SiO2微粒穿越边界层抵达石英基体表面;
4)沉积阶段,穿过边界层的SiO2微粒沉积在石英基体表面,形成沉积层;
5)熔融及气体解吸阶段,沉积在石英基体表面的SiO2微粒在等离子火焰加热作用下熔融形成石英玻璃,同时解吸出包裹SiO2微粒的气体以及基体表面的气体。
图7
PCVD模型
3.3模型分析
表4不同温度下反应平衡常数计算结果
由计算结果可知,体系的平衡常数很大如上表1,可认为SiCl4的氧化反应将全部完成。
Kim和Pratsinis对SiCl4氧化反应的研究结论得到了大多数学者的认同。
他们在试验过程中控制氧气与SiCl4摩尔比为10:
1,在温度1100~2000范围内,当SiCl4转化率为50%、90%及99%时反应所需时间列于表2。
表5SiCl4转变为SiO2所需时间
从表5中能够看出,在温度1400℃时,SiCl4转化功率为99%时所需时刻Ta为9.0×
10-2s,温度升高到1800℃时,SiCl4转化功率为99%时所需时刻Ta仅为3.2×
10-4s。
标明温度升高到1400℃后,反响速率现已很快。
载料氧与SiCl4的混合气体在下料管口出口处速度为2.2m/s,小于等离子体火焰速度5.83m/s。
氧气与SiCl4混合气体从加料管口喷发进入等离子体火焰,因为其速度小于火焰速度,进入火焰后与火焰混合,速度逐步趋于共同,以火焰速度核算从灯具出口到石英基体时刻Tt,灯具出口距石英基体50mm,则Tt=0.0086s,火焰温度以石英基底温度1800℃核算,则Tt远大于Ta,即SiC14与氧气反响所需时刻远小于SiCl4输运时刻,故可以为SiCl4与氧气一进入火焰就完结化学反响生成SiO2。
在石英基体外表,因为吸附效果构成鸿沟薄层,鸿沟层对SiO2微粒形成壁垒,只要穿附。
依据Fick榜首规律,假定化学反响很快完结,则SiO2经过鸿沟层的流量Jm为
(3)
式中,D为SiO2扩散系数,P、U为SiO2在主气流及基体表面的分压,即浓度,R为气体常数,T为基体表面温度。
假设化学反应速率很慢,并且化学反应为一级反应,则达到基体表面的生成物流量