天然气管道输送管线工艺设计Word格式文档下载.docx
《天然气管道输送管线工艺设计Word格式文档下载.docx》由会员分享,可在线阅读,更多相关《天然气管道输送管线工艺设计Word格式文档下载.docx(88页珍藏版)》请在冰豆网上搜索。
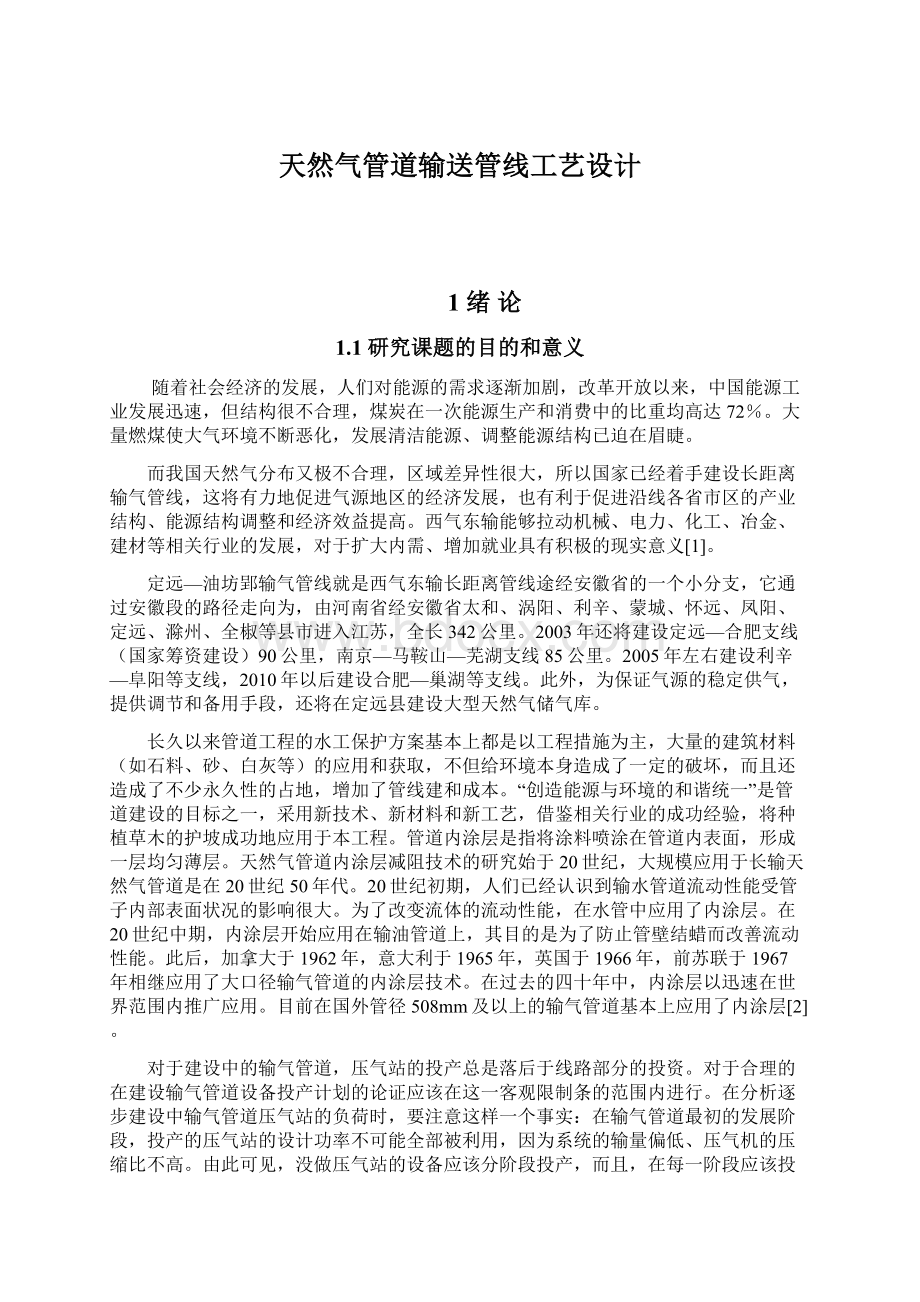
此外,为保证气源的稳定供气,提供调节和备用手段,还将在定远县建设大型天然气储气库。
长久以来管道工程的水工保护方案基本上都是以工程措施为主,大量的建筑材料(如石料、砂、白灰等)的应用和获取,不但给环境本身造成了一定的破坏,而且还造成了不少永久性的占地,增加了管线建和成本。
“创造能源与环境的和谐统一”是管道建设的目标之一,采用新技术、新材料和新工艺,借鉴相关行业的成功经验,将种植草木的护坡成功地应用于本工程。
管道内涂层是指将涂料喷涂在管道内表面,形成一层均匀薄层。
天然气管道内涂层减阻技术的研究始于20世纪,大规模应用于长输天然气管道是在20世纪50年代。
20世纪初期,人们已经认识到输水管道流动性能受管子内部表面状况的影响很大。
为了改变流体的流动性能,在水管中应用了内涂层。
在20世纪中期,内涂层开始应用在输油管道上,其目的是为了防止管壁结蜡而改善流动性能。
此后,加拿大于1962年,意大利于1965年,英国于1966年,前苏联于1967年相继应用了大口径输气管道的内涂层技术。
在过去的四十年中,内涂层以迅速在世界范围内推广应用。
目前在国外管径508mm及以上的输气管道基本上应用了内涂层[2]。
对于建设中的输气管道,压气站的投产总是落后于线路部分的投资。
对于合理的在建设输气管道设备投产计划的论证应该在这一客观限制条的范围内进行。
在分析逐步建设中输气管道压气站的负荷时,要注意这样一个事实:
在输气管道最初的发展阶段,投产的压气站的设计功率不可能全部被利用,因为系统的输量偏低、压气机的压缩比不高。
由此可见,没做压气站的设备应该分阶段投产,而且,在每一阶段应该投入的工作机组数要视输气管道再改发展阶段的需要而定,需要多少台,就投入多少台,换句话说,如果建设中的压气机车间的部分设备已足以满足输气的要求,那么就应该将其投入运行,而不必等待该压气站所有的全部投产。
分阶段投产增加了逐步建设中的输气管道的动力装备程度,并提高了其在起动运行阶段的输量[3]。
输气管道系统是一个统一、密闭、连续的水力系统,其中一处工况的变化必然带来全线工况的变化。
特别是随着天然气开发规模和使用规模的不断扩大,天然气管网系统也日趋庞大和复杂。
一方面,使得人们更难于了解和掌握管道系统的运行规律,论证和提出合理的设计方案和运行方案的难度增大,难于分析和处理管道系统的事故工况;
另一方面,由于管道系统的运行状况直接影响着天然气的产、供、销之间的关系。
因此,必须对输气管道的运行进行优化管理,使输气管道将气体保质、保量、安全、经济的输送到终点,在满足气源和用户要求的前提下,带来巨大的经济效益和社会效益[4]。
输气管道经历了由小口径到大口径,由低压到高压,由手工焊到自动焊等一系列的技术革新。
现在国外又出现了很多新技术,例如:
复合加强型管线用管,灵巧清管器,配备有超声波计量设备的输气监测计量技术等。
而且人们对天然气需求量的不断增长所以有必要对输气管道进行深入的研究,进一步提高输量以及使管道运行更加安全和智能[5]。
1.2国内外研究现状
到目前为止,我国已建成长输管道4.3×
104km,其中天然气干线管道2.4×
104km。
已形成纵横东西、贯通南北、连接海外的管网。
到2020年油气长输管道干线将达8×
104km,其中天然气管道干线将达到5×
目前管道建设趋向于长距离、大口径、大输量、高压力、高钢质。
施工质量与水平逐年提高,保证了管道运行的安全。
通常情况下,长输管线的建设涉及管道的施工以及管道运行过程中所面临的无损检测和管道防腐技术。
1.2.1管道施工技术
在埋地管道的施工中,遇到穿越河流、公路、铁路与障碍物时,常规的开挖方法存在许多问题,“非开挖”敷设地下管道是当今国际管道工程推行了一种先进施工方法,在国内得到了广泛使用。
我国近年来在长输管道的建设中大量采用盾构穿越技术,已有多条大型河流进行了盾构穿越。
目前采用的盾构法穿越施工采用的主要设备是泥水加压平衡盾构机。
我国20世纪70年代末开始使用顶管穿越技术进行短距离的管道穿越。
传统意义上的顶管施工以人工挖掘、千斤顶顶进为主。
后来发展到用螺旋钻挖掘和输送顶管内的土,继而由盾构法派生出的土压平衡法、泥水平衡法等大型顶管穿越技术,穿越距离可达到lkm以上。
由液压来控制顶管前的切土帽以保证顶管的方向性,同时采用了中继顶进、激光测距、机头导向纠偏等手段用于顶进施工作业,解决了顶管的长距离和方向性的问题。
我国1985年首次从美国引进定向钻用于长输管道黄河穿越施工。
近20年来,非开挖管道定向穿越在我国发展迅速。
技术上日臻成熟,定向钻在非开挖管道穿越技术行业中得到了广泛的应用。
定向钻用于敷设管道项目取得巨大成果。
在我国,有2002年2月以一次穿越总长为2308m、直径273m的穿越钱塘江的记录,列于创世界最长穿越记录,载人吉尼斯世界记录,著名的西气东输工程共使用定向钻穿越河流36条,其中最长的穿越是在吴凇江的穿越,一次穿越长度为1150m、直径为1016mm。
管道定向穿越施工技术是一项由多学科、多技术、不同设备集成运用于一体的系统工程,在施工过程中任何一个环节出问题,都可能导致整个工程的失败,造成巨大的损失。
由于定向穿越施工应用十分广泛,使得定向钻技术得到了长足的进步与发展。
国际上已具有多种硬岩施工方法,如泥浆马达、顶部冲击、双管钻进,能进行软、硬岩层的施工。
普遍采用PLC控制、电液比例控制技术、负荷传感系统,有专门的施工规划软件。
我国的管道施工技术随着管道工业的快速发展,施工技术得到了长足的进步与发展。
形成了一整套的长输管道适用的行业、企业标准规范与施工作业规程。
在施工中大量采用新技术、新工艺。
在山区、黄土塬、戈壁、沙漠、无人区、水网地带形成了独特的施工方法与措施。
使我国管道施工水平跻身于世界先进水平。
山区、黄土塬地段,施工设备和管材运行困难,给管道施工带来诸多不便;
尤其是山区陡坡地段管道安装更为困难。
因此,有无施工便道,施工作业带的宽窄,是影响山区施工的主要问题。
应根据管道走向、山势的特点和湿陷性的土质特点,进行开辟施工便道、施工作业带,以满足钢管运输、施工机具设备的通行要求。
在满足运输的条件下,根据地形组织适宜的组焊、安装施工方式,进行管道安装作业,在管道安装完成后组织进行完善的水工保护作业[6]。
水网地段的管道敷设类型主要包括水田施工、季节性湿地施工、盐碱性沼泽和常年积水的水塘施工等。
由于地下水位高,造成作业带及施工便道的修筑困难,钢管及施工设备的运输不便,管沟开挖成型、管线下沟、回填困难。
因此必须采用合理的施工工艺,如便道修筑技术、水上运输管材、拉森板桩管沟支护工艺,深井降水施工工艺,挖泥船水下成沟施工工艺,沉管下沟施工工艺等,才能保证高效、高速、高质量地完成工程任务[7]。
1.2.2管道无损检测
对在线埋地管道进行检测的主要目的是评价管道本体的结构完整性,检测内容包括位置走向勘测、腐蚀评价、泄漏检测和缺陷检测技术四大方面。
根据其特点,检测技术又可分为内检测和外检测两大类。
内检测技术主要采用管道内部爬行器和智能管道机器人;
外检测技术根据是否需要与管体直接接触,分为开挖检测和非开挖检测技术。
管道内部机器人(即管道机器人)在管道检测中得到较为广泛的运用。
目前,美国、英国、法国和德国等已开发出了管道机器人样机,并在检测中得到成功应用。
管道机器人是一种可在管道内行走的机器,可以携带一种或多种传感器,在操作人员的远端控制下进行一系列检测作业。
一个完整的管道检测机器人包括移动载体、视觉系统、信号传诵系统、动力系统和控制系统等。
管道机器人的主要工作方式为在视觉、位姿等传感器的引导下,对管道环境进行识别,接近检测目标,利用超声波、漏磁通和涡流传感器等进行信息检测和识别,自动完成检测任务。
其核心组成为管道环境识别系统(视觉系统)和移动载体。
目前国外的管道机器人不仅能够进行管道检测,还具有管道维护与维修等功能,是综合的管道检测维修系统。
漏磁通检测(MFL)主要用于检测管道的腐蚀缺陷,提供管道上所有缺陷和管件的里程、距最近参考点的距离、周向位置、距上下游环焊缝的位置,缺陷的深度和轴向长度等信息。
目前,它被广泛地应用在长输管道、炼油厂管网、城市管网和海底管线的检测。
由于漏磁信号和缺陷之间是非线形关系,管壁的受损情况需通过检测信号间推断出来,其检测精确相对于超声波检测法较低,适用于最小腐蚀深度为20%—30%壁厚的腐蚀状况检测。
该方法要求传感器与管壁紧密接触,由于焊缝等因素的影响,管壁凸凹不平,使接触要求有时难以难道。
同时由于在测量前必须将管壁磁化,因此漏磁通法仅适合薄管壁。
但是保佑于其价格低廉,检测精度能满足我国大部分地区的要求,目前在我国使用较多。
涡流检测技术主要用于检测管壁内表面的裂纹、腐蚀减薄和点腐蚀等,是目前应用较为广泛的管道无损检测技术,分为常规、投射式和远场涡流检测。
常规涡流检测受集肤效应的影响,只适合于检测管道表面或近表面缺陷;
透射式涡流检测和远场涡流检测灵敏度。
远场涡流法具有便于自动化检测、检测速度快、适合表面检测、适用范围广、安全方便以及消耗物品少等特点,在发达国家得到广泛的重视。
由于温度和探头的提离效应、裂纹深度以及传感器的运动速度等均对涡流检测信号有一定的影响,而且由于远场涡流很难由检测信号直接确定缺陷种类,因此要考虑影响压力管道涡流检测信号的各种因素,才能取得较好的检测效果。
超声波检测技术相对于漏磁通法而言,具有直接和定量化的特点,其数据损失可由相关的软件补偿,所以有较高的精度。
但由于受超声波波长的限制,对薄壁管,同时对关内的介质要求较高。
当缺陷不规则时候,将出现多次反射回波,从而对信号的识别和缺陷信号的识别能力。
由于超声波的传导必须依靠液体介质,且容易被蜡吸收,所以超声波检测技术对含蜡高的油管线存在检测局限。
由于从发射器到管壁之间需要均相液体作为声波传播媒介,所以用于天然气管道时,需要在一个液体段(通常为凝胶)的两端运行两个常规清管器,超声波检测器放入液体段中运行。
日本钢管株式会社(NKK)研制的超声波检测清管器能再现管道壁厚和管道内壁表面的图象,探测焊缝腐蚀,检测腐蚀深度为管壁厚度10%。
该公司研制的轮式干耦合超声波检测器(用于天然气管线)不需要耦合剂,检测效果良好,目前正在开发可用于长距离天然气管道的检测器。
对埋地管道的外部检测,一般首先采用不开挖检测技术对管道本体的腐蚀状况进行快速测评,或采用在线泄露检测技术对管道的泄露状况进行诊断和评价。
对于腐蚀严重或者发生泄露的部位,还需要进行开挖,以发现管道本体裂纹和腐蚀等缺陷。
常规无损检测管道开挖后,使用最多的仍为常规超声、磁粉和渗透检测技术。
但近年来也有一些无损检测新技术应用于管道本体的检测。
超声导波检测埋地管道的开挖检测需要很大的工程量和较长的时间,但有时不开挖会使指定检测的部位与实际