单轴两级真空泵气动设计报告.docx
《单轴两级真空泵气动设计报告.docx》由会员分享,可在线阅读,更多相关《单轴两级真空泵气动设计报告.docx(41页珍藏版)》请在冰豆网上搜索。
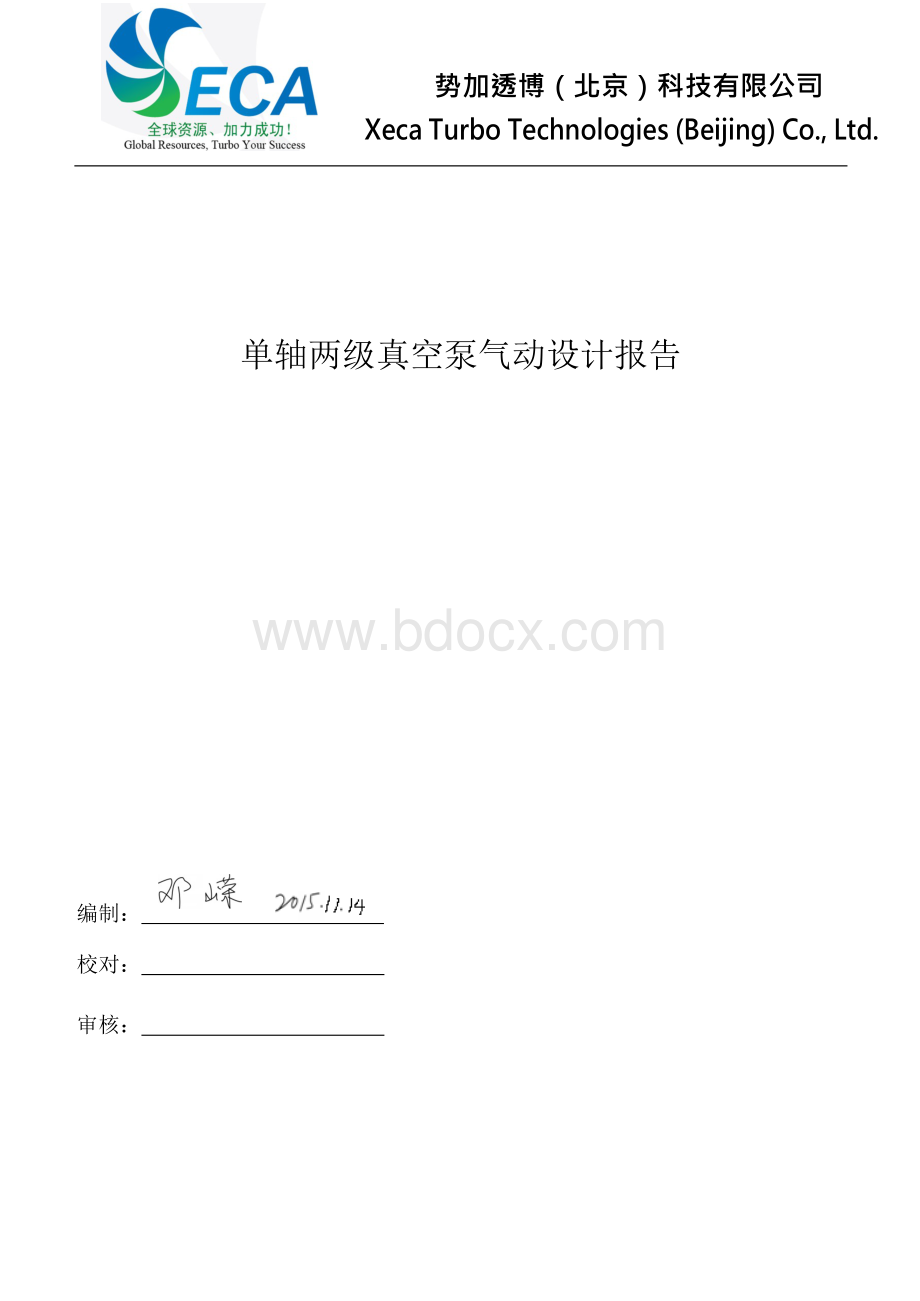
势加透博(北京)科技有限公司
XecaTurboTechnologies(Beijing)Co.,Ltd.
单轴两级真空泵气动设计报告
编制:
校对:
审核:
目录
一、设计要求 1
二、设计分析 1
三、一维设计 2
三、三维详细设计 3
3.1第一级三维详细设计 3
3.1.1第一级叶轮 3
3.1.2第一级蜗壳 3
3.2第二级三维详细设计 4
3.2.1第二级叶轮 4
3.2.2第二级蜗壳 4
四、设计工况CFD分析 5
4.1第一级设计工况CFD计算结果 5
4.2第二级设计工况CFD计算结果 6
五、叶片强度与模态分析 8
5.1第一级叶轮强度与模态分析 8
5.2第二级叶轮强度与模态分析 9
六、真空泵性能预估 10
6.1第一级性能预估 10
6.2第二级性能预估 11
6.3整机性能预估 13
七、结论 15
八、附表 16
附表一第一级叶轮子午面型线坐标 16
附表二第二级子午面型线坐标 18
附表三第一级主叶片型线坐标 20
附表四第一级分流叶片型线分布 25
附表五第二级主叶片型线分布 30
附表六第二级分流叶片型线分布 35
一、设计要求
本项目设计的单轴两级真空泵将应用造纸行业用于替代传统的水环真空泵。
设计要求见表
1。
表1真空泵设计要求
设计要求
工质
空气
进气温度(℃)
25
相对湿度(%)
100
进气压力(kPa)
-67(表压)
进气流量(m3/min)
310
出口总压(kPa)
5(表压)
环境压力(kPa)
100
机组形式
单轴两级
叶轮形式
三元叶轮
叶轮外径(mm)
约500
设计转速(r/min)
12000
电机功率(kW)
315
轴功率(kW)
300
设计点单级总总多变效率
≥82%
级间压损(kPa)
3kPa
二、设计分析
由于真空泵进口压力低,雷诺数较小,效率会低于进口常压的压气机,因此设计难度增加。
此新型单轴两级真空泵拟采用具有国际先进水平的离心真空泵气动设计方法,使用S型后弯叶片,优化叶轮子午流道和叶轮载荷分布,有效调控离心叶轮内部的二次流动,提升气动性能,确保真空泵在宽广工况范围内高效运行。
为了降低制造成本,通过调整压比分配,使两级叶轮能采用相同的轮径。
该真空泵转速偏低,流量系数偏小,所以采用了长短叶片来提升机组性能。
由于该真空泵的工况变化范围尚不确定,所以采用了无叶扩压器,使机组获得更好的流量范围。
由于两级之间仍处于真空状态,并且只有管道直接相连,没有中冷器等设备,所以级间损失一般不会超过1.5kPa。
即使在实际运行时,级间管道损失略大于1.5kPa,只要在设计时留
三、一维设计
有足够的压力裕度,都能满足使用要求。
按照1.5kPa的级间损失计算,两级压比分别选取了1.9和1.67。
根据轴功率300kW反算后,流量为1.985kg。
设计计算时,忽略了叶根倒角等对流量的影响,所以机组流量一般略小于计算值,所以选择了2kg作为了设计流量。
一维设计结果见表2、3。
表2第一级子午面几何尺寸
名称
单位
数值
进口叶根半径
mm
53
进口叶尖半径
mm
147
叶轮轴向长度
mm
148.5
叶轮出口半径
mm
253
叶轮出口宽度
mm
27.6
扩压器出口半径(蜗壳进口
半径)
mm
400
扩压器出口宽度
mm
23
转速
rpm
12000
叶片数
组
9
进口叶尖间隙
mm
0.5
出口叶尖间隙
mm
0.8(装配间隙)
表3第二级子午面几何尺寸
名称
单位
数值
进口叶根半径
mm
50
19
进口叶尖半径
mm
129
叶轮轴向长度
mm
114.4
叶轮出口半径
mm
253
叶轮出口宽度
mm
22.4
扩压器出口半径(蜗壳进口
半径)
mm
390
扩压器出口宽度
mm
19
转速
rpm
12000
叶片数
组
11
进口叶尖间隙
mm
0.5
出口叶尖间隙
mm
0.6+轴向窜动量
三、三维详细设计
一维设计完成后,结合CFD软件,对子午面型线分布、叶片角度分布和蜗壳截面进行设计和优化。
由于该真空泵属于偏大型的机组,为了降低蜗壳损失,采用了等内径蜗壳。
3.1第一级三维详细设计
3.1.1第一级叶轮
叶轮子午面型线分布和叶片型线分布见附表一、三、四
3.1.2第一级蜗壳
蜗壳子午面示意图见图1,各截面几何尺寸见表4。
蜗壳出口扩压锥管(360°截面到出口法兰区域)扩张角可以在7°到9°之间,由结构设计人员根据选取的法兰尺寸确定。
图1蜗壳截面示意图
表4第一级蜗壳截面几何数据
截面角度
360
330
300
270
240
210
180
150
120
90
60
30
蜗壳进口半径R5
400
400
400
400
400
400
400
400
400
400
400
400
进口宽度B5
23
23
23
23
23
23
23
23
23
23
23
23
R1
104
99.2
94.3
89.2
83.8
78.1
72.2
65.8
58.8
50.9
41.7
30.5
3.2第二级三维详细设计
3.2.1第二级叶轮
叶轮子午面型线分布和叶片型线分布见附表二、五、六。
3.2.2第二级蜗壳
蜗壳子午面示意图见图1,各截面几何尺寸见表5。
蜗壳出口扩压锥管(360°截面到出口法兰区域)扩张角可以在7°到9°之间,由结构设计人员根据选取的法兰尺寸确定。
表5第一级蜗壳截面几何数据
截面角度
360
330
300
270
240
210
180
150
120
90
60
30
蜗壳进口半径R5
390
390
390
390
390
390
390
390
390
390
390
390
进口宽度B5
19
19
19
19
19
19
19
19
19
19
19
19
R1
86.1
82.2
78.1
73.9
69.5
64.8
59.8
54.4
48.5
41.9
34.2
24.5
四、设计工况CFD分析
4.1第一级设计工况CFD计算结果
第一级真空泵子午面静压分布(图2)显示,叶轮通道内静压分布沿流向方向逐渐上升,其等值线与流线方向基本垂直,能还好的满足真空泵性能的要求。
图3中的叶片表面静压分布显示,叶片载荷分布均匀,叶轮出口根、中、尖的静压基本一致。
图2第一级子午面静压分布 图3第一级叶片表面静压分布
图4、5、6分别是10%、50%、90%叶片高度速度矢量分布。
图中显示,流场分布较好,无气流分离。
90%叶片高度靠近叶片出口位置的低速区是由于叶尖泄露涡造成的,属正常现象。
图7是蜗壳表面静压分布。
图中显示蜗壳内静压分布均匀,蜗壳进口静压分布除靠近喉口位置有变化外,其余位置基本一致,说明蜗壳内流场分布较好,蜗壳损失低,能使机组获得较大的流量范围。
设计工况蜗壳损失系数约0.36。
图4第一级10%叶片高度速度矢量分布 图5第一级50%叶片高度速度矢量分布
图6第一级90%叶片高度速度矢量分布 图7第一级蜗壳表面静压分布
4.2第二级设计工况CFD计算结果
第二级真空泵子午面静压分布(图8)显示,叶轮通道内静压分布沿流向方向逐渐上升,其等值线与流线方向基本垂直,能还好的满足真空泵性能的要求。
图9中的叶片表面静压分布显示,叶片载荷分布均匀,叶轮出口根、中、尖的静压基本一致。
图8第二级子午面静压分布 图9第二级叶片表面静压分布
图10、11、12分别是10%、50%、90%叶片高度速度矢量分布。
图中显示,流场分布较好,无气流分离。
90%叶片高度靠近叶片出口位置的低速区是由于叶尖泄露涡造成的,属正常现象。
图13是蜗壳表面静压分布。
图中显示蜗壳内静压分布均匀,蜗壳进口静压分布除靠近喉口位置有变化外,其余位置基本一致,说明蜗壳内流场分布较好,蜗壳损失低,能使机组获得较大的流量范围。
设计工况蜗壳损失系数约0.35
图10第二级10%叶片高度速度矢量分布 图11第二级50%叶片高度速度矢量分布
图12第二级90%叶片高度速度矢量分布 图13第二级蜗壳表面静压分布
五、叶片强度与模态分析
5.1第一级叶轮强度与模态分析
第一级叶轮应力分布见图14。
转速12000rpm时,叶片最大应力不到140MPa。
对钛合金来说,具有非常大的安全系数,叶片强度性能非常好。
第一级叶轮模态分析结果见图15。
前三阶是整个叶轮的摆动和绕轴转动,在评估叶片频率时,可以不用专门考虑。
整个叶轮的摆动受连接方式和链接处的几何尺寸影响较大,但是叶片的振动受连接方式相对较小。
计算结果中的第四阶频率是叶片的一阶频率。
叶片一阶频率达到也叶轮额定转速转频的6.4倍频,能后很好的满足变转速工作的要求。
图14第一级叶轮应力分布 图15第一级叶轮模态分析
5.2第二级叶轮强度与模态分析
第二级叶轮应力分布见图16。
转速12000rpm时,叶片最大应力不到140MPa。
对钛合金来说,具有非常大的安全系数,叶片强度性能非常好。
第二级叶轮模态分析结果见图17。
从计算得到的阵型来看,第五阶频率才是叶片振动,是叶片的一阶频率。
该频率下的振动不光是叶片,还伴随着轮盘的摆动。
叶片一阶频率达到也叶轮额定转速转频的6.55倍频,能后很好的满足变转速工作的要求。
图16第二级叶轮应力分布 图17第二级叶轮模态分析
六、真空泵性能预估
6.1第一级性能预估
8
7
6
5
4
流量m3/s
3
2
1
0
1.1
1
6000
1.2
1.7
1.6
1.5
1.4 9000
1.3
12000
2
1.9
1.8
压比
设计完成后,利用CFD软件,采用全通道叶轮加蜗壳组合计算的方法对真空泵性能进行了预估。
第一级计算进口总温25℃,进口总压33kPa。
图18、19为真空泵压比和效率的性能曲线。
图中显示,第一级真空泵效率达到了0.84以上。
图18第一级压比流量MAP图
效率
8
7
6
5
4
流量m3/s
3
2
1
0
0.1
0
6000
0.4
0.3
0.2
9000
0.7
0.6
0.5
12000
0.9
0.8
图19第一级效率流量MAP图
6.2第