大型非标设备施工方案Word格式.docx
《大型非标设备施工方案Word格式.docx》由会员分享,可在线阅读,更多相关《大型非标设备施工方案Word格式.docx(23页珍藏版)》请在冰豆网上搜索。
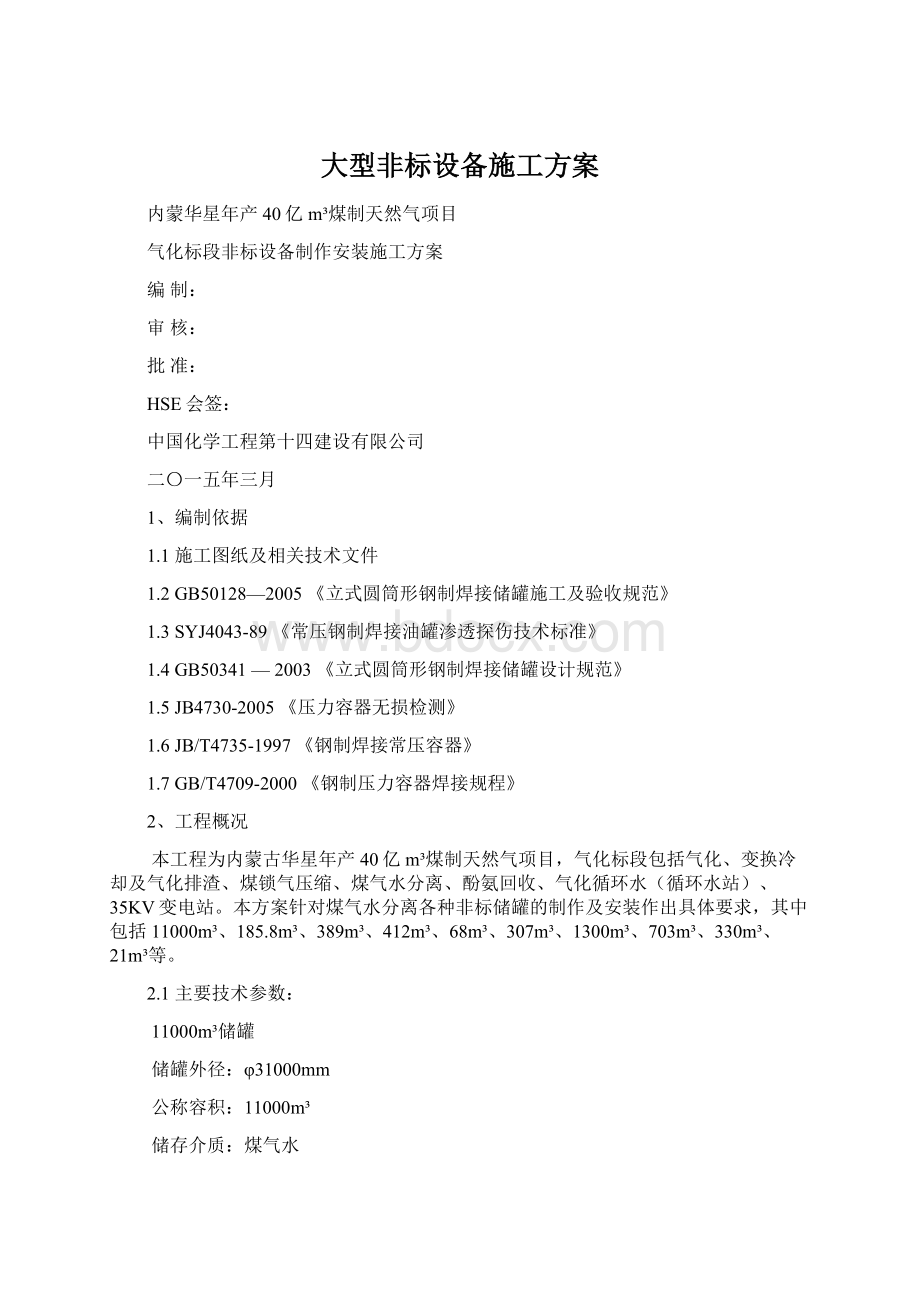
、307m³
、1300m³
、703m³
、330m³
、21m³
等。
2.1主要技术参数:
11000m³
储罐
储罐外径:
φ31000mm
公称容积:
11000m³
储存介质:
煤气水
罐壁高度:
18657mm
主体材质:
Q235A
设计压力:
-0.5~4KPa
设计温度:
70℃
罐体质量:
351690kg(单台)
2.2工程特点、难点
本工程属于非标储罐制作安装工程,与土建、地管及钢结构工程同时施工,施工过程中不免会有相互影响的情况,对工程进度有很大影响。
3、施工准备
3.1根据现场实际情况,材料集中抛砂防腐后由防腐厂运送到施工现场,并合理安排预制厂地与材料堆放场地。
3.2施工机具准备
序号
名称
单位
数量
1
电焊机
台
30
2
配电箱
个
6
3
半自动切割机
4
角向磨光机
36
5
气割工具
套
10
卷板机
7
10T电动葫芦
50
8
Φ159*3500吊杆
根
9
胀圈
螺旋千斤顶
11
Φ450切割机
12
气刨空压机
13
试压泵
14
真空箱
15
烘烤箱
16
恒温箱
17
保温桶
40
18
平板车
辆
19
16T吊车
20
25T吊车
21
大钢卷尺
22
简易龙门吊
3.3施工人员准备(详见人力计划表)
工种
人数
备注
铆工
/
焊工
下料气割工
起重工
电工
卷板机操作工
安全员
普工
管理人员
3.4材料验收
储罐用钢材、配件等必须符合设计和规范要求,具有产品质量证明书或检验报告。
储罐用钢板应逐张进行外观检查,其表面不得有气孔、裂纹、拉裂、夹渣、重皮现象。
钢板厚度要求:
板厚为5~8mm,钢板允许偏差:
±
0.6mm;
板厚为9mm~15mm,钢板允许偏差:
0.65mm;
板厚为16~25,钢板允许偏差:
0.75;
板厚为26~40,钢板允许偏差:
0.8。
3.5基础的验收及中间交接
我方只对基础进行几何尺寸的复验,和土建进行中间交接。
其具体要求如下:
储罐中心标高允许偏差为±
20mm。
支承罐壁的基础表面,每隔10m弧长内任意两点的高度差≤6mm,整个圆周长度内任意两点的高度差≤12mm。
沥青砂层表面应平整密实,无突出的隆起,凹陷及贯穿裂纹。
沥青砂层表面凹凸度的检查方法应为:
以基础中心为圆心,以1/4D、1/2D、3/4D为直径作同心圆,在圆周上分别均分为8、16、24等分点。
同一圆周上的测点其测量标高与计算标高之差≤12mm。
4、施工方法的确定
4.1施工方法:
本方案拟采用葫芦提升倒装法施工。
4.2工艺原理
本工艺先按排版图铺设底板,完成后组装顶圈壁板和罐顶,利用电拉葫芦提升装置提升罐体上段,然后逐圈组焊罐体下段。
储罐除底板和最底下一圈壁板外,重量大约250T,拟用28只10T电动葫芦来提升,计算如下:
底板重量为61.6T,除最底下一圈壁板后其余壁板重量为40.4T,需提升重量为351.69-61.6-40.4≈250T。
G=28只×
10T×
0.9(安全系数)=252T>
250T安全
故提升装置采用28台10吨电动葫芦,当壁板对接组焊完毕后,落下提升装置,再进行下一圈壁板的组对提升。
185.8m³
储罐重量为20.8T,拟采用5只5T葫芦提升,计算如下:
G=5只×
5T×
0.9=22.5T>
20.8T安全
389m³
储罐重量为25T,拟采用6台5T葫芦提升,计算如下:
G=6只×
0.9=27T>
25T安全
412m³
储罐重量为26T,拟采用6台5T葫芦提升,计算如下:
26T安全
307m³
储罐重量为33.4T,拟采用8台5T葫芦提升,计算如下:
G=8只×
0.9=36T>
33.4T安全
1300m³
储罐重量为86.7T,拟采用20台5T葫芦提升,计算如下:
G=20只×
0.9=90T>
86.7T安全
703m³
储罐重量为70T,拟采用16台5T葫芦提升,计算如下:
G=16只×
0.9=72T>
70T安全
330m³
储罐重量为38.3T,拟采用9台5T葫芦提升,计算如下:
G=9只×
0.9=40.5T>
38.3T安全
21m³
储罐重量为4T,68m³
储罐重量为10T,均可用吊车整体吊装。
4.3针对基础的处理方法
本方案拟采用倒装提升法,为了施工便利及安全等多方面考虑,需对基础做适当的修改,待罐体安装完成后恢复原样。
具体做法如下:
在煤气水贮槽的基础环形墙上,开1m*1m的施工人行及安全通道,罐底部开Φ650的圆洞,具体位置见附图一。
环形墙凿开后,顶部两排钢筋保留,下排钢筋在距一端150mm处截断,热弯以保证人员通行。
安装完成后,截断处使用钢筋搭接焊,支模后用C30混凝土浇筑,恢复基础环形墙原样。
图二开洞做法及恢复
5、组装工艺及要求
5.1施工程序框图
a.11000m³
储罐施工程序见图三
图三储罐制作安装施工程序图
5.2组装程序及技术要求
5.2.1罐底板的铺设
铺板前技术人员必须会同作业班长、质检员共同对底板进行排板,绘制出排板图,并报设计人员确认。
要求任意相邻两焊缝间的距离应>300mm。
底板铺设前,板下表面应按设计要求涂刷沥青防腐层2遍,但沿板周边50mm不涂刷。
铺设底板时,按底板排板图及预制时的编号、划线位置及储罐中心线,先组配中心板,然后向两侧序铺设相邻诸中幅板及边缘底板,底板铺设时的实际尺寸应比设计尺寸大35~45mm,以补偿焊缝收缩量。
在基础上铺设底板时,边缘板的对接焊缝其间隙应是外端小内端大,以防止焊缝焊接收缩而引起的底板变形。
对三组板重叠上层板进行切角,并与下二层板相贴。
伸缩缝的固定不应使用点焊方法,而应采用装配卡具,待所有焊接工作完毕后才能进行伸缩缝的点焊及其焊缝的施焊。
5.2.2储罐罐顶预制
罐顶系组合件,先根据图纸及来料尺寸确定顶板的块数,绘制排版图,排版图在绘制时应保证顶板任意相邻焊缝间距不小于200mm,然后按排板图进行下料拼接。
组装罐顶前,先进行顶圈壁板的拼焊,再进行包边角钢的焊接,程序见图四:
图四罐顶施工顺序
中心支架及圈梁支架Ф273*8钢管用∠63×
63×
5角钢斜撑固定在底板上,其上安放环形圈梁,圈梁采用δ=18mm钢板,圈梁安装时需用水平仪或连通管找平。
5.2.3顶圈壁板和罐顶的组装
罐底周边标高找平后,在顶圈壁板和罐顶的组装装配前在底板上画出该圈板安装直径(留有收缩量,取定直径增大10mm)的圆周标志线,并打上样冲眼,标志线内侧每隔0.5~0.8m在底板上焊接50×
50×
8mm的三角形档块作为圈板固定档圈,顶圈壁板即紧靠其上进行组装。
档块外侧40mm焊接∠50×
5mm,L=30~50mm的角钢,便于围板时贴紧上一圈壁板和临时固定外围圈板。
按围板排板图及编号选好弧度板,组装完后应检查钢板的垂直度、对接头的间隙、错边量、圆弧度,其尺寸偏差应在规定值内。
以罐底弓形板事先划出的圆周线和拱顶环为基准组对顶圈板,为了避免焊缝收缩使半径减小,在罐壁最后闭合封口的立缝预留,待其它立缝焊接后再进行封口切割焊接,然后进行壁板上口与顶环的焊接。
顶圈壁板组装完毕,因刚性较差,在每条立缝上均布三块龙门板并点焊牢固,待包边角钢组焊完毕再拆除。
罐顶的组装
a、在罐底中心立好安装用的临时施工支架,圈板位置下均匀分布8根临时支架,其支架要求刚性较大,不易变形,支架安装后四周用角钢支撑在底板上,增加施工支架刚性。
具体见图五:
图五临时支架位置
b、施工支架中心应与罐底中心重合,其支架顶标高要高于设计标高150mm左右,作为安装完毕撒除支架后罐顶中心下垂量。
c、顶板组装时,先铺外圈包边角钢到环形圈之间的顶板,完成后再铺环形圈到中心柱之间的顶板,具体尺寸及块数见排版图。
根据定位用25吨吊车两边对称同时逆时针进行吊装,顶板吊上后,用销子固定,以防止移位或滑落。
5.2.4罐壁的倒装
在第n圈壁板外侧围上第n-1圈壁板,除封口立缝外,其余立缝全部焊完,然后提升第n圈壁板到预定高度,并使第n-1圈壁板与第n圈壁板环缝对接,用同样方法提升第n-2,……,1圈壁板。
在每圈壁板组对时必须复测其壁板的垂直度、周长尺寸及上口的水平度,发现问题及时纠正,以使罐壁在焊接后保持竖向垂直,水平度和直径均符合要求。
第一圈壁板与罐底弓形板组焊时,必须保证其罐体的总垂直度,水平度,并与划好的底板圆周线重合,焊接时应采取适当措施,防止角变形。
提升每圈板时在下圈板围板前应在上圈板外表面圆周上均布10个左右位置的观察标志,把壁板外侧高度均分成若干等份(50~100mm间隔即可)从下往上标记1,2,3,…….,以便提升时罐外人员清楚了解提升高度和控制上升速度。
倒装提升时为防止到位后,收活口时造成上下错口,给点焊组对带来困难,提升前在下圈板上口圆周均匀点焊挡块,其间距为300~500mm左右。
倒装提升时要防止杂物卡住,罐顶应经常保持清洁。
组对要求:
a.纵缝错边量:
不应大于板厚的1/10,且不应大于1.5mm。
b.环缝错边量:
当上圈板厚<8mm时,≤1.5mm;
当圈板厚≥8mm时,不得大于板厚的1/5,且不应大于3mm。
c.组焊后的焊缝角变形用1m长的弧形样板检查。
当δ≤12mm时,不得大于10mm;
当12<δ≤25时,不得大于8mm。
5.2.5胀圈设施
胀圈可增加罐体的环向强度,防止环向焊接变形。
并可用它来设储罐提升装置,为确保提升装置提供吊点,用[22a煨制而成。
煨制的弧度与罐体相配,安装和拆除方便灵活,与罐间有足够的张紧力,胀圈采用挡块固定在罐壁上,胀圈之间用上下两块导向板连接,导向