中控室窑系统操作规程.docx
《中控室窑系统操作规程.docx》由会员分享,可在线阅读,更多相关《中控室窑系统操作规程.docx(62页珍藏版)》请在冰豆网上搜索。
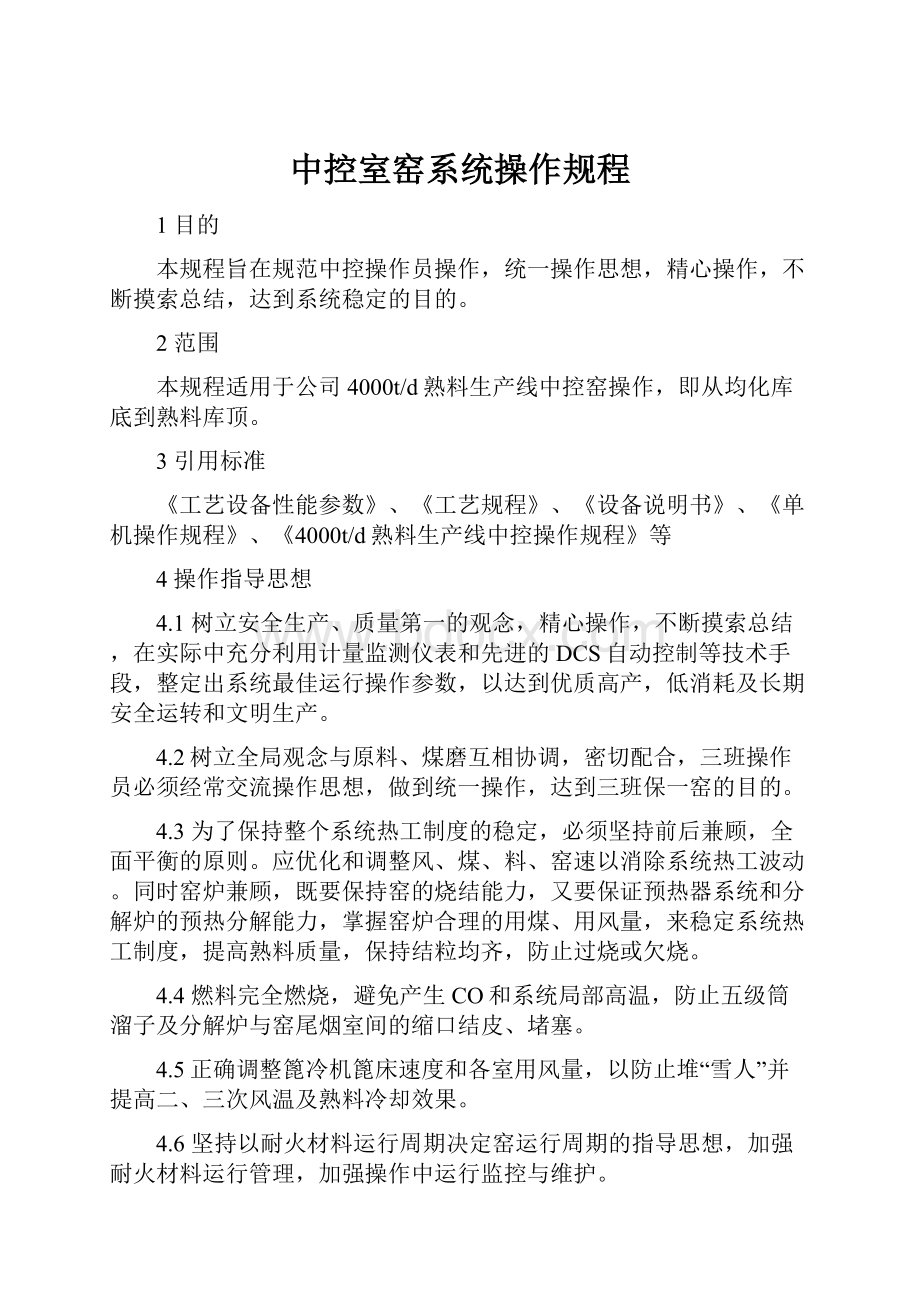
中控室窑系统操作规程
1目的
本规程旨在规范中控操作员操作,统一操作思想,精心操作,不断摸索总结,达到系统稳定的目的。
2范围
本规程适用于公司4000t/d熟料生产线中控窑操作,即从均化库底到熟料库顶。
3引用标准
《工艺设备性能参数》、《工艺规程》、《设备说明书》、《单机操作规程》、《4000t/d熟料生产线中控操作规程》等
4操作指导思想
4.1树立安全生产、质量第一的观念,精心操作,不断摸索总结,在实际中充分利用计量监测仪表和先进的DCS自动控制等技术手段,整定出系统最佳运行操作参数,以达到优质高产,低消耗及长期安全运转和文明生产。
4.2树立全局观念与原料、煤磨互相协调,密切配合,三班操作员必须经常交流操作思想,做到统一操作,达到三班保一窑的目的。
4.3为了保持整个系统热工制度的稳定,必须坚持前后兼顾,全面平衡的原则。
应优化和调整风、煤、料、窑速以消除系统热工波动。
同时窑炉兼顾,既要保持窑的烧结能力,又要保证预热器系统和分解炉的预热分解能力,掌握窑炉合理的用煤、用风量,来稳定系统热工制度,提高熟料质量,保持结粒均齐,防止过烧或欠烧。
4.4燃料完全燃烧,避免产生CO和系统局部高温,防止五级筒溜子及分解炉与窑尾烟室间的缩口结皮、堵塞。
4.5正确调整篦冷机篦床速度和各室用风量,以防止堆“雪人”并提高二、三次风温及熟料冷却效果。
4.6坚持以耐火材料运行周期决定窑运行周期的指导思想,加强耐火材料运行管理,加强操作中运行监控与维护。
5工艺流程及主机设备主要性能参数
5.1工艺简介
均化库的生料通过气动截止阀、电动流量阀、进入喂料缓冲仓,入窑生料均从喂料缓冲仓卸出,经气动截止阀、电动流量阀,经冲击固体流量计计量后至喂料斜槽再经斗提提升至预热器顶斜槽经分料阀分料喂入预热器内。
在预热器A列、B列中,生料和热气流进行热交换,在达到A列、B列四级筒后进入分解炉内,入炉生料经过充分混合与分解,然后进入五级旋风预热器进行料气分离,入窑煅烧,熟料经篦冷机急冷后进入锤式破碎机破碎后由裙板输送机输送到熟料库。
5.2主机设备性能参数
5.2.1入窑斗提(1428)
型号:
H-GBW1000×99500
用途:
生料入预热器
头尾轮中心高:
99.5m
输送物料:
生料
物料容重:
0.8kg/m3
物料水分:
<1%
物料温度:
正常:
80℃最大:
120℃
输送能力:
正常:
380t/h、最大:
450t/h
电机功率:
200kW
5.2.1.1开机前的准备
a)确认各部分螺栓、壳体是否组装到位、有无松动及漏缝;
b)确认斗提内部有无异物、积料、积水;
c)确认胶带接头连接情况是否完好及传动张紧链的张紧度是否适度;
d)确认各部润滑油是否符合要求;
e)确认传动及防倒转装置是否完好;
f)确认液偶是否完好;
g)确认下游设备是否运行正常;
h)检查斗提保护装置是否完好。
5.2.1.2运行中的检查
a)检查各部分螺栓、壳体是否有漏灰漏风现象;
b)检查运行中皮带的跑偏情况;
c)检查各部润滑情况是否正常及设备各部温升情况;
d)检查斗提运行中是否平衡有无异常振动声音;
e)检查入斗提物料温度;
f)检查电机运转是否异音、振动、温度情况。
5.2.2预热器(1501):
:
一级筒
二级筒
三级筒
四级筒
五级筒
内径×柱体(m)
ф5.0×9.75
ф6.9×5.592
ф6.9×5.542
ф7.2×6.476
ф7.2×6.614
数量
4套
2套
2套
2套
2套
材质
Q235A
Q235A
Q235A
Q235A
Q235A
内筒规格
(内径×高)(m)
ф2.175×3.130
ф3.165×3.2
ф3.3×3.35
ф3.54×3.92
ф3.665×3.4
材质
16Mn
1Cr18Ni9Ti
ZG40Cr25Ni20
ZG40Cr25Ni20
ZG40Cr25Ni20
下料溜管(mm)
ф710×6
ф900×6
ф900×6
ф900×6
ф900×6
材质
1Cr18Ni9Ti
1Cr18Ni9Ti
0Cr23Ni13
ZG1Cr25Ni20
ZG1Cr25Ni20
5.2.2.1开机前的准备
a)确认系统各溜子翻板阀轴承是否补加黄油,翻板动作是否灵活;
b)确认各级旋风筒及溜管内有无异物,系统的耐火砖是否完好;
c)关闭所有的人孔门及检查孔,并进行投球确认系统畅通无阻;
d)点火升温,应将预热器各级下料溜子翻板用铁丝吊起;
e)在窑开始投料前应将各级溜子上的翻板阀挡板放下;并再次投球,确认系统畅通;
f)确认供料系统设备是否正常。
5.2.2.2运转中的检查
a)系统各溜子翻板阀动作是否灵活,配重是否调整在合适位置;
b)检查所有的检查孔及人孔门是否有漏气跑灰现象,并进行堵漏处理;
c)检查系统空气炮的气源压力(≥4.5kg)及转换开关是否转到工作状态,气源阀是否打开及运行是否正常;
d)注意观察各级旋风筒差压变化,防止堵塞;
g)观察预热器外壳体温度变化,看是否有局部耐火材料脱落现象;
h)定期对预热器清扫孔进行清理;
i)经常检查预热器各点监控温度及负压是否正常。
5.2.3分解炉(1509)
设备名称:
NST-I分解炉
规格:
ф7.5(内径)×31×0.01
容积:
1368.8m3
分解炉主截面风速:
8m/s
气体停留时间:
3.9s
压力损失:
400Pa
喷煤嘴数量:
2套
5.2.3.1开机前检查
a)检查耐火衬料是否完好;
b)检查分解炉内的积料情况,根据需要进行清扫;
c)检查分解炉喷煤嘴烧损、磨损情况,结碳需要进行清扫;
d)检查分解炉三次风入口积料情况;
e)校正分解炉三次风挡板实际开度与中控对应关系;
f)所有的人孔门是否关闭。
5.2.3.2运转中的检查
a)检查系统是否有漏风、漏灰现象;
b)观察分解炉缩口结皮情况,根据需要进行清扫;
c)检查分解炉喷煤管工作是否正常,管道是否漏气;
d)检查分解炉各差压是否正常;
e)检查分解炉炉壁、炉中及锥部温度是否正常;
f)出口温度及负压是否正常。
5.2.4回转窑(1511)
5.2.4.1设备规格、型号
规格:
Φ4.8×74m(胴体内径×长度)
型式:
单传动、单液压挡轮
窑支承:
3档
斜度:
4%(正弦)
转速:
主传动:
0.35~4r/min
辅助传动:
8.52r/h
功率:
主传动:
630kW/660V
窑头密封装置:
弹簧钢片片式密封
窑尾密封装置:
配重压紧端面
5.2.4.2开机前的准备
窑体:
a)确认窑出入口处密封护板及窑口护铁的安装螺栓是否松动;
b)确认窑体上人孔门是否关好,止松螺母是否拧紧;
c)窑内耐火衬料是否符合砌筑要求。
轮带:
a)确认轮带与垫板之间的间隙无异物;
b)确认轮带与垫板间是否加足石墨锂基脂;
c)确认轮带与托轮接触面之间有无异物;
d)确认轮带与托轮在旋转时是否碰到其它物体。
托轮:
a)确认各部螺母有无松动;
b)确认石墨块是否装好,托轮轴温检测装置是否完好;
c)确认润滑油位及淋油槽是否正常,冷却水阀是否打开。
窑头罩:
a)确认耐火材料是否符合砌筑要求,燃烧器入窑孔周围密封是否添加;
b)确认窑罩灰斗是否有积料,应排空保持畅通;
c)窑罩是否与旋转部件磨擦。
传动:
a)确认大牙轮与小齿轮的磨损与接合情况;
b)小齿轮轴承润滑油路是否畅通;
c)齿面润滑是否正常;
d)液压挡轮是否正常。
5.2.4.3运转中的检查
a)注意窑体各部温度变化,并做好记录;
b)检查大牙轮与小齿轮的啮合和润滑情况,运行是否平稳有无异常振动;
c)注意窑轮带与托轮在整个宽度的相接触;
d)确认轮带与窑体是否保持直角状态;
e)检查托轮轴温及温升情况,并做好记录;
f)检查托轮轴润滑油的油质、油量、渗漏等情况;
g)冷却水是否常开;
h)窑尾、窑头密封装置的旋转是否与固定部分之间有无接触及异常响声;
i)主电机有无异音、异味、异常振动,冷却风机是否正常,主电机碳刷是否打火;
j)主减速器油位、油质、油泵压力、油温是否正常;
k)窑罩灰斗是否堵料;
l)确认各挡轮带滑移量是否在可控范围(5-10mm);
m)窑罩冷却风机运行是否正常。
5.2.5燃烧器(1526)
5.2.5.1设备规格、参数
煤粉/空气的浓度:
4~6kg/m3
型式:
NC-15Ⅱ型三风道燃烧器
喷煤管总长度:
11214mm
喷煤管的用煤量:
正常15t/h、最大18t/h
一次风比例:
约7.5%
一次风机(罗茨风机)风量:
约11000m3/h;
风压:
16000Pa;
数量:
1台
柴油燃烧装置工作压力:
2.5~5.5MPa
5.2.5.2开机前的准备
a)确认燃烧器的耐火材料是否剥落,本体有否变形头部磨损及烧损情况,通道是否畅通,各部间隙是否符合要求;
b)确认燃烧器与窑内的位置是否合适,防止烧坏火砖;
c)确认燃烧器各处调节挡板是否灵活自如,指示值是否正确;
d)确认燃烧器活动小车是否自如,燃烧器可否在下车口上下左右调整;
5.2.5.3运转中的检查
a)检查燃烧器耐火浇注料是否烧损;
b)及时清扫燃烧器头部积料,以保持正常的火焰;
c)调整燃烧器内、外流比例,伸缩节范围,保证良好的燃烧条件,使火焰长度适当,又不冲刷窑皮;
d)检查有无磨通冒灰漏气现象;
e)燃烧器上各仪表显示是否正常。
5.2.6篦冷机(1528)
5.2.6.1设备规格、参数
型式:
NC39325控制流篦冷机
型号:
3.9×32.5m
能力:
5000--5500t/d
熟料温度:
入料:
1400℃
出料:
环境温度+65℃
熟料粒度:
≤25mm占90%
篦床有效面积:
121.2m2
传动段数:
3段
冲程次数:
4~25次/min
冲程:
130mm(正常)140mm(最大)
单位冷却用风量:
≤2.2Nm3/kg.cl
5.2.6.2开机前的准备
a)检查空气梁风道是否有积料;
b)检查篦板前后的缝隙,一般在4±2mm的范围内,篦板固定螺栓锁紧螺母是否点焊,篦板型号是否符合图纸要求,篦板安装与侧铸件的间隙,大梁支架托辊与斜铁的配合及固定螺栓是否符合要求;
c)十字传动轴气封是否完好,润滑油路是否畅通;
d)检查各空气室之间的密封是否完好,壳体密封是否完好;
e)检查内部耐火材料是否完好;
f)各冷却风机是否正常;
g)润滑系统是否正常;
h)各液压传动循环泵是否具备开机条件;
i)检查弧形阀是否正常,冷却机链幕是否完好;
j)检查破碎机及破碎腔是否正常、畅通。
5.2.6.3运转中的检查
a)通过观察孔检查篦床上的物料分布是否均匀及红河现象来判断用风量的比例大小;
b)在各部听听有无异音,从各空气室观察孔观察各室的漏料粒径情况,判断篦板的磨损、烧损及脱落情况;
c)检查集中供油管的各路分配阀动作情况及供油量的大小;
d)检查壳体是否有漏料、漏风现象;
e)检查破碎机入料口是否有大块物料卡住;
f)各传动装置和油泵站是否运行正常(负荷及冲程次数情况);
g)监控冷却机壳体有无变形或烧红,判断内部耐火材料是否正常;
h)各室压力是否在正常范围内;
i)检查冷却机内是否有“雪人”。
5.2.7裙板输送机(1701)
5.2.7.1设备规格参数
型号:
KZB250-1000/300/5
输送量:
230t/h(max:
360t/h)
输送速度:
0.299m/s
环境温度:
max400℃
熟料粒度:
0-50mm
填充系数:
53.5%(MaX:
83.8%)
物料容重:
1.45t/m3
链条型号:
AU-625
滚筒直径:
¢140mm
头尾轮中心距离:
172325mm
水平距离:
159380mm
垂直距离:
51110mm
滚筒间距:
1500mm
倾角:
29o
电动机:
功率:
110kW
转速:
1482r/min
电压:
380V
5.2.7.2运转前的检查
a)检查链节、链轮滴油润滑油量是否充足,滴油点是否正确;
b)检查托棍销有无松动、脱落;
c)检查裙板上的杂物、裙板有无变形;
d)检查张紧装置张紧度是否合适;
e)检查减速机润滑油油量、油质;
f)检查各地脚螺栓、固定螺栓是否松动、脱落;
g)检查输送机头、尾轮磨损及螺栓是否松动、脱落;
h)检查裙扳机下料口是否畅通;
i)检查逆止器是否完好;
j)检查液力偶合器是否完好。
5.2.7.3运转中检查
a)检查电机、减速机有无异音、异振、异温、异味;
b)检查链条与齿轮啮合情况,链条润滑状况是否良好;
c)检查裙板运转是否平稳,托轮T形销是否脱落;
d)检查每个托辊与轨道接触是否良好;
e)检查液压连轴节传动状况是否良好;
f)检查托辊及测速开关是否正常;
g)检查各下料口是否畅通,是否磨通;
h)检查各地脚螺栓、连接螺栓是否松动、脱落;
i)当锤破及篦冷机输送系统跳停后恢复时,注意观察输送机上的物料量,并及时调整篦速,防止下游设备跳停。
5.2.8大型排风机(1506、1538)
5.2.8.1设备规格参数
1506高温风机
型号
W6-2×39№31.5F双吸单出双支承
进风口
逆135°
出风口
逆45°
处理风量
900000m3/h
全压
>7200Pa
进口静压
>7200Pa
工作温度
290℃max:
450℃(15min)
主轴转速
300~950r/min
废气密度
1.41kg/Nm3
主电机型号
YKK710-6
主电机规格
2500kW/6000V
主电机转速
994r/min
1538窑头风机
型号
Y4-73-11№31.5F
单吸单出双支承
进风口
逆135°
出风口
逆45°
处理风量
580000m3/h
全压
2000Pa
工作温度
200~250℃max:
350℃
主轴转速
580r/min
主电机型号
YRKK500-10
主电机规格
560kW/6000V
5.2.8.2运转前的检查
a)检查风机内杂物是否清理干净,风叶是否有积料;
b)检查人孔门是否密封好,运转部位与静止部位是否接触;
c)检查冷却水阀门是否打开,轴承、稀油站油量、油质是否正常;
d)检查各检测装置是否完好;
e)检查液力偶合器油量是否足够,水电阻是否正常;
f)检查入口挡板动作是否灵活,是否能关闭到位,指示中控显示是否一致;
g)检查各地脚螺栓,连接螺栓是否紧固,脱落;
h)检查慢转是否脱开;
i)开机前对高压电机绝缘进行检查。
5.2.8.3运转中检查
a)检查水、油系统是否泄漏,流量、温度是否正常;
b)检查液力偶合器油温、油压是否正常,系统是否泄漏;
c)检查风机、电机运转是否平稳,声音、振动是否正常;
d)检查主电机碳刷是否打火;
e)挡板开度是否与中控显示一致,检查液力偶合器开度是否与中控显示一致;
f)检查各地脚螺栓,连接螺栓是否松动、脱落;
g)检查轴承温度是否正常。
6点火升温操作
6.1点火前的检查准备工作
a)现场检查各有关设备的润滑情况及螺栓是否松动;
b)检查预热器、窑及冷却机内的耐火衬完好情况,有关人员、支架、工具、杂物等是否已全部撤离和清理干净,以及三次风管的积料情况;
c)将预热器各翻板阀吊起,确认管道畅通无阻后,关闭整个系统的人孔门及捅料孔盖,并保证密闭良好;
d)确认各阀门处于正常运行状态;
e)校准燃烧器角度及距窑口距离,并做好记录(依据生产过程中窑皮、胴体温度情况、耐火材料状况、熟料质量、燃烧器型式综合考虑后进行燃烧器校正);
f)根据工艺要求向窑操提供升温曲线图;
g)确认窑头喂煤仓内有足够的煤粉,确认柴油泵站有足够的油量满足点火升温要求,检查油枪是否正常,并做好点火棒;
h)各专业人员进入岗位并完成各项准备工作;
i)窑操作员、巡检工应对本系统全面检查了解,以做到胸有成竹,并将准备工作、检查情况及结果全面真实地写入交接班记录,并将存在的问题向分厂主管领导汇报;
j)相关专业和部门点火会签后,接点火指令,通知原料、烧成、煤磨、电气、自动化等专业人员将各设备、仪器仪表送电,通知水泵房送水;
k)通知现场巡检人员将本系统所有设备的现场控制转入中控位置,检查各设备、仪器是否备妥;
l)通知空压机站启动各有关空压机,中控启动窑尾排风机润滑系统,启动窑减速机润滑系统,并通知原料操作员检查电收尘排风机情况,准备开机;
m)确认单机试车及联动试车正常。
6.2升温操作
a)启动窑尾排风机慢转,打开燃烧器上内外流手动挡板,中控将变频调速器调至最低(带变频器),启动一次风机,并适宜调节转速;
b)启动点火油泵(冬天时油泵需提前打入循环运行状态),调整供油油站出口压力为2-3.5MPa,开始向窑内喷油,将点火棒点着,从窑头点火孔伸入,使点火棒前端靠近燃烧器喷咀前下端,进行点火;
c)确认柴油点燃后,调整内外流风挡板开度,以期得到较理想的燃烧状况;
d)升温曲线:
(每次升温前由工艺专业技术人员提供);
e)喂煤
e.1)当窑尾温度达到250℃时(或根据升温曲线要求),通知原料操作员启动618排风机,调整各风机入口挡板开度,使窑罩压力在-20~-40Pa左右,启动窑头喂煤系统;
e.2)喂煤设定0.5-1t/h,刚开始喂煤时,要避免熄火,操作要平衡,注意调整各风机挡板及燃烧器内、外流开度,做到既保证煤粉充分燃烧,风量又不过大。
注意:
窑内温度过低时,不得随意单独用煤粉升温;
e.3)注意观察预热器系统各点温度及窑尾温度是否正常;
e.4)根据升温曲线及现场观察,进行加煤、减油,同时调整风量,使得充分燃烧,并保持火焰正常,尽量避免烟囱冒黑烟,严格控制预热器出口CO含量在0.1%以下。
f)升温中窑的慢转:
(见表一)
窑尾温度℃
旋转量(度)
间隔时间(min)
0~150
0
不慢转
150~300
120
60
300~450
120
30
450~600
120
15
600~850
120
10
850~950
连续慢转
950℃以上
投料
注:
①雨天气时,应根据实际情况相应缩短慢转窑时间(间隔时间比正常时减半);
②预热器出口气体温度达150℃以上时,窑尾排风机必须慢转;
③通知润滑人员对各挡轮带内抹油,并在慢转过程中给托轮轴淋油。
g)首次升温(新窑)或当主烧成带大面积换砖,需从窑口向内铺适宜熟料层,厚度为200mm,防止未完全燃烧的煤粉及柴油落入砖中,破坏耐火砖;
h)当窑内大面积换砖时,在尾温升至650℃,可进行预投料:
投料量30t/h,时间:
20-30min;预投料时,窑必须连续慢转并注意预热器各点温度变化情况;
i)在冷却机前端固定板上部铺200mm厚结粒较好的熟料;
j)升温曲线:
k.1)窑内砖进行挖补或换砖<10m且系统浇注料修复不多,升温14h,曲线如下:
油煤混烧
k.2)窑内烧成带换砖10m≤L<20m,或者40m以后换砖长度L≥20m时,升温16h,曲线如下:
油煤混烧
k.3)窑内烧成带换砖≥20m,或窑口、窑尾(含舌形板)更换浇注料时,升温18h,曲线如下:
油煤混烧
k.4)窑内未换砖且停窑在24-48h以内,升温10h(停窑期间,遇阴雨、雪天气,升温时间可适当延长至12h),曲线如下:
油煤混烧
k.5)临停24h以内升温:
1临停4-12h小时以内,窑按1/2停机时间升温;
2临停12-24h,窑按1/3停机时间进行升温。
k.6)备注:
①烘烤温度以窑尾温度为基准;
②当窑尾温度升至250-300℃时,可考虑油煤混烧;喷煤初期,操作应平稳,避免燃烧器熄火;
③严格按升温曲线进行升温,做到均衡上,不回头,由前向后升的原则;
④根据用煤量及升温时间,合理调整一次风机转速和燃烧器内、外流开度,保证油煤完全燃烧,避免CO出现;
⑤严格按规程进行窑慢转;
⑥慢转过程中,注意托轮温度变化情况,及轮带与托轮啮合情况;
⑦更换窑口浇注料时,烧油烘烤期间,慢转窑每30分钟一次;油煤混烧初期,每20分钟转窑一次。
7投料至满负荷操作
7.1投料前的准备
a)检查预热器各部位的温度,投料前1h放各翻板阀,投球确认预热器是否畅通,同时使空气炮进入正常运行状态;
b)启动窑辅助运行设备;
c)启动冷却机空气梁风机,调节余风风机挡板,保持窑头微负压,(必要时启动余风风机,并通知给窑头电收尘荷电);
d)启动熟料输送及窑头回灰系统;
e)启动528篦冷机系统;
f)启动供料系统袋收尘及喂料机组。
7.2投料操作
a)窑尾温度升到950℃、预热器出口温度>350℃开始投料;
b)启动冷却机二、三段空气室风机(其中一段空气室风机在前面若已启动,则在此保持运行);
c)开窑前一小时左右,脱开窑尾排风机慢转启动窑尾排风机,并通知原料操作员注意调整系统负压;
d)通知将窑头电收尘荷电,关闭余风风机挡板,启动余风风机注意调整好窑头负压;
e)调整各有关挡板,窑罩压力为-30Pa~-80Pa;
f)停止窑慢转,断开离合器,切换主马达,窑速初设定值为0.5rpm;
g)煤粉仓料位可供生产所需,启动分解炉喂煤机组,然后适当开启三次风挡板,向炉内适当加煤,炉出口800℃左右;
h)调整窑尾排风机挡板及转速使预热器出口抽力在-1500~-2000Pa左右投料,喂料量100~150t/h,适当增加冷却机一段风量;
i)注意观察窑内情况,重点监控窑尾负压、温度,预热器出口压力与温度;五级筒出口温度,五级筒锥体负压差及溜子温度>800℃左右。
注意两系列各对应点的温度、压力,并进行比较,判断是否正常;
j)投料过程中注意检查托轮温度变化情况;
k)联系现场关注翻板阀运行情况。
7.3加料操作
a)根据窑内及预热器情况。
逐渐加料到330~400t/h,进行满负荷生产,在加料时相应逐渐加快窑速至3.5~3.95rpm左右,窑头加煤至11~13t/h左右,分解炉加煤至16~25t/h左右,加煤操作应缓慢稳定;
b)加大窑排风机排风量,使预热器出口抽力在–4500~-6500Pa,预热器出口气体CO小于0.1%,Nox在400~700ppm;
c)加料的同时,增加冷却机各室风量,当喂料量在330~400t/h时,同时调整篦冷机各段篦速,控制好各室压力;
d)几点说明: