第一章模具机械加工基础DOC.docx
《第一章模具机械加工基础DOC.docx》由会员分享,可在线阅读,更多相关《第一章模具机械加工基础DOC.docx(32页珍藏版)》请在冰豆网上搜索。
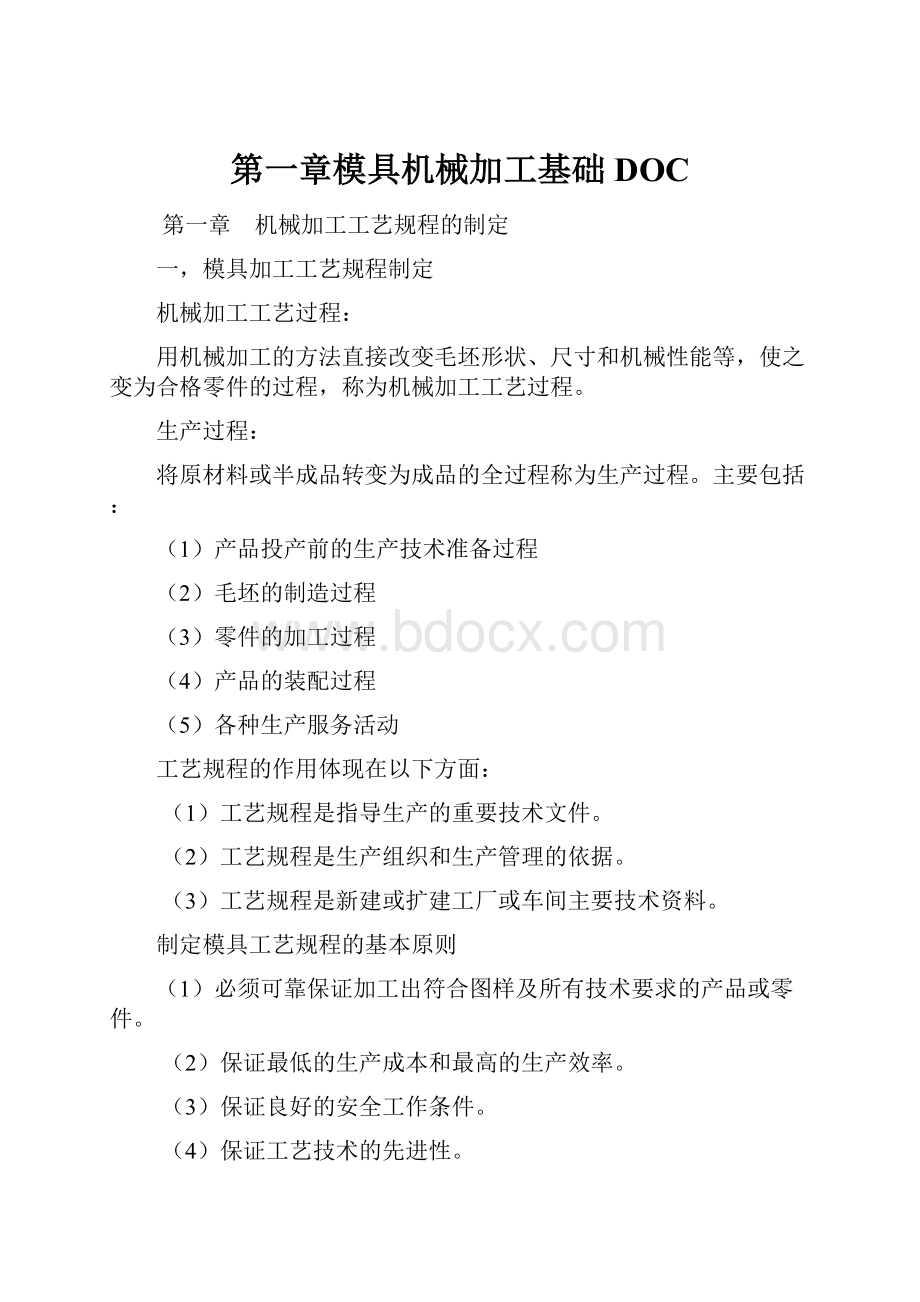
第一章模具机械加工基础DOC
第一章 机械加工工艺规程的制定
一,模具加工工艺规程制定
机械加工工艺过程:
用机械加工的方法直接改变毛坯形状、尺寸和机械性能等,使之变为合格零件的过程,称为机械加工工艺过程。
生产过程:
将原材料或半成品转变为成品的全过程称为生产过程。
主要包括:
(1)产品投产前的生产技术准备过程
(2)毛坯的制造过程
(3)零件的加工过程
(4)产品的装配过程
(5)各种生产服务活动
工艺规程的作用体现在以下方面:
(1)工艺规程是指导生产的重要技术文件。
(2)工艺规程是生产组织和生产管理的依据。
(3)工艺规程是新建或扩建工厂或车间主要技术资料。
制定模具工艺规程的基本原则
(1)必须可靠保证加工出符合图样及所有技术要求的产品或零件。
(2)保证最低的生产成本和最高的生产效率。
(3)保证良好的安全工作条件。
(4)保证工艺技术的先进性。
制定工艺规程所需的原始资料
主要有:
产品装配图、零件图;产品验收质量标准;产品的年生产纲领;毛坯材料与毛坯生产条件;工厂的生产条件;工艺规程设计、工艺装备设计所用设计手册和有关标准;国内外先进制造技术资料等。
制定工艺规程的步骤
(1)研究产品的装配图和零件图,进行工艺分析。
(2)由零件生产纲领确定零件生产类型。
(3)确定毛坯的种类、技术要求和制造方法。
(4)拟订零件加工工艺路线。
(5)确定各工序的加工余量,计算工序尺寸及其公差。
(6)确定各工序的技术要求及检验方法。
(7)选择各工序使用的机床设备及刀具、夹具、量具和辅助工具等工艺装备。
(8)确定各工序的切削用量及时间定额。
(9)填写工艺文件。
二.模具零件的工艺分析
零件结构的工艺性:
是指所设计的零件在满足使用性能要求的前提下制造的可行性和经济性。
当某个零件的结构形状在现有的工艺条件下,既能方便地制造,又有较低的制造成本,这种零件结构的工艺性就好。
零件的技术要求包括:
尺寸精度、几何形状精度、各表面的相互位置精度、表面质量、零件材料、热处理及其它要求。
分析时应注意以下两点:
(1)零件的技术要求既要满足设计要求,又要便于加工。
(2)在满足产品使用性能的条件下,零件图上标注的尺寸精度等级和表面粗糙度要求应取最经济值。
零件机构工艺性要求有六点:
1.零件的整体结构、组成各要素的几何形状尽量统一。
2.尽量减少切削用量,材料及切削刀具的消耗量
3.尽量采用普通刀具、量具加工
4.要便于装夹,装夹次数少
5.加工部位要有足够的刚性
6.尽量采用标准件、通用件、借用件和相似件。
三.毛坯的选择
1.毛坯的种类
模具零件所用的毛坯种类主要有:
型材、铸件、锻件和半成品件四种。
2.选择毛坯的原则:
(1)零件材料对加工工艺性能和力学性能的要求。
(2)零件的形状结构和尺寸。
(3)生产类型。
(4)生产条件。
3.选择毛坯要总和考虑以下因素的影响:
1.零件材料及力学性能
2.零件材料的工艺性
3.零件的结构形状和尺寸
4.生产类型
5.工厂生产条件
四.定位基准的选择
基准:
用来确定生产对象上的几何要素所依据的那些点、线、面。
基准按其功用不同可分为设计基准和工艺基准。
(1)设计基准
在零件图上用来确定其它点、线、面位置的基准,称为设计基准。
(2)工艺基准
在加工、测量和装配过程中使用的基准,称为工艺基准。
工艺基准按用途不同可分为工序基准、定位基准、测量基准和装配基准。
定位基准:
在加工时,为了使零件相对于机床和刀具占据的正确位置(即将零件定位),所使用的基准称为定位基准。
测量基准:
测量时所采用的基准。
装配基准:
它是装配时用来确定零件或部件在产品中的相对位置。
工序基准:
在工序图上用来确定本工序所加工表面加工后的尺寸,形状,位置的基准。
(1)粗基准的选择原则
1.应选不加工表面作粗基准。
2.需要保证某重要加工表面的加工余量均匀,应选该表面作粗基准。
3.应选择毛坯余量小的表面作粗基准
4.选作粗基准的表面,应尽可能平整,不能有飞边、浇口、冒口或其它缺陷,以确保零件定位准确、夹紧可靠。
5.一般情况下粗基准不重复使用。
(2)精基准的选择
1)基准重合原则。
2)基准统一原则。
3)自为基准原则。
4)互为基准原则。
5)保证零件安装准确、可靠,操作方便的原则。
五.零件工艺路线的拟定
(1)选择定位基准
(2)表面加工方法的选择
(3)加工阶段的划分
(4)工序的集中与分散
(5)加工顺序的安排
选择零件表面加工的方法和依据:
1)零件材料性质及热处理要求。
2)零件表面加工的尺寸公差等级和表面粗糙度。
3)零件表面加工的位置精度要求。
4)零件的形状和尺寸。
5)生产类型。
6)具体条件。
加工顺序的安排
1.机械加工工序的安排原则:
p57
概括为十六字诀:
基准先行,先主后次,先粗后精,先面后孔。
2.热处理工序的安排p57
1)预备热处理:
目的是改善加工性能,为最终热处理作好准备和消除残余应力,如:
正火、退火、时效处理。
工序安排:
粗加工前、后和需要消除应力处。
2)最终热处理:
提高力学性能,如调质、淬火、渗碳淬火、渗氮等。
工序安排:
安排在半精加工之后,精加工之前。
3.加工阶段的划分
一般分为:
粗加工、半精加工、精加工和光整加工四个阶段。
a)粗加工阶段:
切除加工表面上的大部分余量,使毛坯接近成品。
b)半精加工阶段:
为主要表面的精加工做好必要的精度和余量准备,并完成一些次要表面的加工。
c)精加工阶段:
使精度要求高的表面达到规定的质量要求。
d)光整加工阶段:
提高表面的尺寸精度和减少表面粗糙度。
加工余量的确定
1.为了保证零件的质量,在加工过程中,需要从加工表面上切除的金属层厚度,称为加工余量
加工余量一般有两种分类方法:
(1)总加工余量和工序余量。
(2)基本加工余量、最大加工余量、最小加工余量。
2.影响加工余量的因素
(1)上道工序后的表面粗糙度和 表面缺陷层深度。
(2)上道工序的尺寸公差Ta。
(3)上道工序各表面之间相互位置的空间误差ρa。
(4)本工序加工时的安装误差εb
3.确定加工余量的方法
(1)分析计算法
以一定的实验数据资料和计算公式为依据。
(2)经验估计法
依靠经验采用类比法估算确定加工余量的大小。
(3)查表修正法
以有关工艺手册和资料所推荐的加工余量为基础。
第二章模具的特种加工方法
3.1模具电火花成形加工
电火花加工:
是在一定介质中,通过工具电极和工件电极之间脉冲火花放电时的电腐蚀现象,对工件进行加工,从而达到图纸规定的形状、尺寸和表面粗糙度要求的一种工艺方法。
电火花加工的原理图如图3-1所示
工具电极4与工件1分别与脉冲电源2的两个输出端连接,并且都浸在工作液里,自动进给调节装置3使工具电极与工件之间保持一定的放电间隙(一般约为0.01~0.2mm)。
脉冲电源不断发出脉冲电压加在工具电极与工件之间,当脉冲电压增大到间隙中工作液的击穿电压时,将会发生火花放电,放电区的高温把该处的电极和工件材料熔化,甚至汽化,在电极和工件表面都被蚀除一小块材料,形成小的凹坑
3.1.2电火花加工必须具备的条件
(1)必须使工件电极和工具电极之间经常保持一定的间隙,一般为0.01~0.2mm。
(2)电火花放电必须是脉冲性和间歇性的,放电延续时间一般为10-7~10-4s。
(3)电火花放电必须在具有一定绝缘性能的液体介质中进行。
液体介质没有一定绝缘性能,就不能击穿放电,形成火花通道。
3.1.3电火花加工的特点
(1)可以加工用一般机械加工方法难以加工或无法加工的材料。
(2)工具电极和工件在加工过程中不接触,不存在明显的机械作用力,工件不会受力变形,便于加工小孔、深孔、薄壁、窄缝以及各种型面和型腔零件。
(3)直接利用电能进行加工,便于实现加工过程的自动控制。
(4)脉冲参数调节方便,在同一台机床上可以连续进行粗加工、半精加工和精加工。
(5)电极材料不必比工件材料硬,可以以柔克刚。
(6)只能对导电材料进行加工,且加工过程中有电极损耗,对加工精度有影响。
3.1.4电火花成型加工机床
(1)主机
主机包括:
主轴头、床身、立柱、工作台、工作液槽等。
(2)脉冲电源。
(3)自动进给调节系统。
(4)工作液净化及循环系统。
电火花机床的组成:
电火花成型加工机床本体的主要组成部分:
脉冲电源、间隙自动进给调节系统、工作液及循环过滤系统、主机等四部分组成。
脉冲电源:
工频交流电转化为一定频率的单向脉冲电源,提供电火花加工所需能量。
自动调节系统:
测量环节、比较环节、放大环节和执行环节等四部分组成。
自动调节系统的作用:
为了使加工过程连续进行,电极必须不断、及时地调节进给速度,以维持所需的放电间隙。
工作液及循环过滤系统的作用:
采取强迫循环的办法把清洁工作液由液压泵加压,强迫冲入工具电极与工件之间的放电间隙,排出间隙产物,稳定加工。
可分为:
冲油式和抽油式。
循环过滤系统的组成:
电动机、液压泵、过滤器、工作液槽、管道、阀门及测量仪等。
机床主体部分:
主轴头、床身、立柱、工作台及工作液槽。
4.影响加工质量的主要因素:
电火花加工后的表面质量包括:
表面粗糙度、表面变化层、显微裂纹及表面层的力学性能。
1)表面粗糙度
2)表面变化层(凝固层和热影响层)
3)显微裂纹
4)表面变化层的力学性能
5.影响加工精度的主要因素:
放电间隙的大小、工具电极的损耗及其稳定性。
6.影响电火花加工速度的因素:
电参数、极性效应、工件材料的热物理常数、工作液等。
热物理常数:
比热容、熔化潜热、汽化潜热、熔点、沸点、热导率。
7.极性效应:
电火花加工时,无论是正极还是负极都会受到不同程度的腐蚀,即使两个电极材料相同,也往往会出现正、负极的腐蚀速度不一样,这种现象为极性效应。
正极性效应:
把工件接脉冲电源正极时的加工。
负极性效应:
把工件接脉冲电源负极时的加工。
8.工作液的作用是:
1)具有介电性:
击穿时能形成火花放电通道,结束后迅速恢复间隙绝缘状态。
2)绝缘性强度比较高
3)压缩火花放电通道,使放电通道的截面积很小,电流密度很高,提高生产率。
4)急剧气化,产生局部高压有利于电蚀产物的排出
5)冷却工具电极,防止热变形
电火花穿孔加工的特点:
1)能加工出各种高硬度、高强度、高韧性的金属材料
2)能有效加工一般机械加工难以加工的形孔
3)加工表面粗糙度为0.8-3.2,单面放电间隙为0.01-0.15
4)冲模的配合间隙均匀,刃口耐磨,提高了模具质量;对于复杂的凹模可以不用镶拼式机构,提高了模具强度
电火花穿孔加工的方法为:
直接配合法,混合加工法,凸模修配法和二次电极。
3.1.5电火花加工在模具制造中的应用
1.凹模型孔加工
对于型孔形状复杂的凹模,采用电火花加工可以不用镶拼结构,而采用整体结构。
这样既简化了模具的结构,又提高了模具的寿命。
(1)保证凸、凹模配合间隙的方法
1)直接配合法
2)混合法
3)修配凸模法
4)二次电极法
(2)电极设计
1)电极材料
常用电极材料包括:
钢、铸铁、石墨、黄铜、紫铜、铜钨合金。
2)电极结构
a.整体式电极
b.组合式电极
c.镶拼式电极
3)电极尺寸
电极尺寸包括长度尺寸和横截面尺寸。
a.电极的长度尺寸
L=KH+H1+H2+(0.4~0.8)(n-1)KH
b.电极的横截面尺寸
当按照凹模型孔尺寸和公差确定电极的横截面尺寸时,则电极的轮廓应比型孔均匀地缩小一个放电间隙值。
2.型腔加工
(1)型腔加工的工艺方法
1)单电极加工法
单电极加工法指用一个电极加工出所需型腔的方法。
2)多电极加工法
3)分解电极法
(2)电极和工件的定位
型腔模电极和工件装夹校正后,必须相互定位,以保证型腔在模具上的位置精度。
常用的定位方法如下:
a.量块角尺定位法
b.十字线定位法
c.定位板定位法
型腔模的有:
锻模、压铸模、胶木模、塑料模、玻璃模、橡胶模。
型腔模加工的特点:
1.不仅侧面形状和尺寸精度较高,而且形状和尺寸精度要求也较高。
2.属于三维曲面加工,蚀除量较大,要求粗精加工速度快。
3.电极损耗小
4.粗加工后的侧面修光较难
型腔电火花加工工艺方法:
单电极平动加工法,多点极更换加工法及分解电极更换法。
电火花线切割加工
电火花线切割加工的工作原理与电火花加工基本相同,都是利用电火花放电使金属熔化或气化。
但是电火花线切割加工与电火花加工相比有一些突出的优点,在应用范围上也有所不同。
电火花线切割加工的工作原理、特点和应用
原理:
电火花线切割加工利用细钼丝或细铜丝5作工具电极,穿过工件3上预先钻好的小孔(穿丝孔),由导向轮6由贮丝筒9带动,相对工件作上下往复运动。
加工能源由脉冲电源4供给,工件接脉冲电源的正极,电极丝接负极。
脉冲电压将电极丝和工件之间的间隙(放电间隙)击穿,产生瞬时火花放电,将工件放电区局部熔化或气化,从而实现切割加工。
2.电火花线切割加工的特点
1)不需要制作成型的工具电极,可节约电极设计、制造费用,缩短生产周期。
2)由于电极丝比较细,可以加工微细异形孔、窄缝和形状复杂的工件。
3)加工过程中,电极损耗极小,有利于加工精度的提高。
4)对工件轮廓进行加工,余料仍可利用。
5)加工电流小,属于中、精加工范围,采用正极性加工。
6)自动化程度高,操作方便,加工周期短,成本低。
7)不能加工盲孔类或阶梯类成形表面
3.电火花线切割加工的应用
(1)加工模具零件
适用于加工淬火钢、硬质合金模具零件、各种形状的细小零件、窄缝等。
(2)加工电火花成型加工用的电极
适用于加工一般电火花加工型孔时用的电极,以及加工带锥度型腔时用的电极。
。
(3)加工零件
适用于加工品种多、数量少的零件,特殊难加工材料的零件等。
1.快速走丝线切割机床
快速走丝线切割机床是我国生产和使用的主要机种。
它采用钼丝(φ0.08~0.2mm)或铜丝(φ0.3mm左右)作电极。
电极丝在贮丝筒的带动下通过加工缝隙作往复循环运动,一直使用到断线为止。
走丝速度约为8~10m/s,加工精度较低,目前能达到的加工精度为±0.01mm,表面粗糙度为Ra=2.5~0.63μm。
2.慢速走丝线切割机床
慢速走丝线切割机床是国外生产和使用的主要机种。
它采用紫铜、黄铜、钨、钼等作为电极丝,直径约为φ0.03~0.35mm。
一般走丝速度低于0.2m/s。
电极丝单方向通过加工缝隙,不重复使用,可避免电极丝损耗对工件加工精度的影响。
慢速走丝电火花线切割机床的加工精度可达到±0.001mm,表面粗糙度可达到Ra<0.32μm。
电火花线切割加工:
机床主体、脉冲电源、数控系统。
机床主体:
床身、坐标工作台、运丝机构以及工作液循环系统。
脉冲电源:
晶体管脉冲电源。
数控系统的主要作用:
按加工要求自动控制电极丝相对工件的运动轨迹和进给要求,实现工件尺寸的加工。
电火花线切割加工的工艺路线:
1)电极丝的准备
2)工作液的选配
3)工件的准备
4)工件的装夹
5)电规准的选择
2.毛坯准备
电火花线切割加工所用的毛坯一般是经过下料→锻造→退火→机械粗加工→淬火与回火→磨削加工等工序后获得。
应合理确定切割起点和加工路线,否则会大大降低加工精度。
同时毛坯也应尽量选择锻造性能好、淬透性好、热处理变形小的材料制作,如CrWMn、Cr12MoV、GCr15等,并制定严格的热处理规范。
3.工艺准备
(1)检查机床走丝架的导轮、保持器和拖板丝杆副的间隙,不符合要求的应及时调整更换,以免影响加工精度。
(2)选择脉冲参数
(3)选配工作液
(4)选择电极丝
(5)开机试运行,观察走丝是否正常。
4.零件装夹和调整
(1)零件的装夹
电火花线切割机床一般在工作台上配备安装夹具,常用的装夹方式有以下几种:
1)悬臂式装夹
2)简支式装夹
3)桥式支撑方式装夹
4)板式支撑方式装夹
(2)零件的调整
1)用百分表找正
2)划线法找正
(3)调整电极丝起始位置
1)目测法
2)火花法
3)电阻法
3.3电化学及化学加工
电化学加工(ElectrochemicalMachining简称ECM)包括从工件上去除金属的电解加工和向工件上沉积金属的电镀、涂覆加工两大类。
几个基本概念:
电极电位:
金属浸于电解质溶液中,显示出电的效应,即金属的表面与溶液间产生电位差,这种电位差称为金属在此溶液中的电位或电极电位。
电极的极化:
当有外电场作用时,相对平衡的电极电位数值将发生变化。
通常把在—定电流密度作用下的电极电位与相对平衡的电极电位的差值,称为电极极化。
常见的有电化学极化、浓差极化等。
钝化:
钝化是使金属表面转化为不易被氧化的状态,而延缓金属的腐蚀速度的方法。
电化学反应:
在阳极阴极表面产生得、失电子的化学反应。
电化学加工:
通过电化学反应从工件上去除或镀覆金属材料的特种加工方法。
电解加工:
利用金属在电解液中产生阳极溶解的原理去除工件材料的加工方法。
电解加工的生产率:
单位时间内电解蚀除的金属量。
电解加工的原理与特点:
1.1电化学加工的原理与特点
1.电化学加工的原理:
图1-1所示为电化学加工的原理。
两片金属铜(Cu)板浸在导电溶液,例如氯化铜(CuCl2)的水溶液中,此时水(H2O)离解为氢氧根负离子OH-和氢正离子H+,CuCl2离解为两个氯负离子2Cl-和二价铜正离子Cu+2。
当两个铜片接上直流电形成导电通路时,导线和溶液中均有电流流过,在金属片(电极)和溶液的界面上就会有交换电子的反应,即电化学反应。
溶液中的离子将作定向移动,Cu+2正离子移向阴极,在阴极上得到电子而进行还原反应,沉积出铜。
在阳极表面Cu原子失掉电子而成为Cu+2正离子进入溶液。
溶液中正、负离子的定向移动称为电荷迁移。
在阳、阴电极表面发生得失电子的化学反应称为电化学反应。
这种利用电化学反应原理对金属进行加工(图1-1中阳极上为电解蚀除,阴极上为电镀沉积,常用以提炼纯铜)的方法即电化学加工。
电化学加工分类:
3.电化学加工的适用范围
电化学加工的适用范围,因电解和电镀两大类工艺的不同而不同。
电解加工可以加工复杂成型模具和零件,例如汽车、拖拉机连杆等各种型腔锻模,航空、航天发动机的扭曲叶片,汽轮机定子、转子的扭曲叶片,齿轮、液压件内孔的电解去毛刺及扩孔、抛光等。
电镀、电铸可以复制复杂、精细的表面。
1.电解加工的原理及特点
1)基本原理:
电解加工是利用金属在电解液中的“电化学阳极溶解”来将工件成型的。
如图2-1所示,在工件(阳极)与工具(阴极)之间接上直流电源,使工具阴极与工件阳极间保持较小的加工间隙(0.1~0.8mm),间隙中通过高速流动的电解液。
这时,工件阳极开始溶解。
开始时,两极之间的间隙大小不等,间隙小处电流密度大,阳极金属去除速度快;而间隙大处电流密度小,去除速度慢。
随着工件表面金属材料的不断溶解,工具阴极不断地向工件进给,溶解的电解产物不断地被电解液冲走,工件表面也就逐渐被加工成接近于工具电极的形状,如此下去直至将工具的形状复制到工件上。
2)电解加工与其他加工方法相比较,它具有下列特点:
(1)能加工各种硬度和强度的材料。
只要是金属,不管其硬度和强度多大,都可加工
(2)生产率高,约为电火花加工的5~10倍,在某些情况下,比切削加工的生产率还高,且加工生产率不直接受加工精度和表面粗糙度的限制。
(3)表面质量好,电解加工不产生残余应力和变质层,又没有飞边、刀痕和毛刺。
在正常情况下,表面粗糙度Ra可达0.2~1.25μm,平均加工精度±0.05mm左右。
(4)阴极工具在理论上不损耗,基本上可长期使用。
电解加工当前存在的主要问题是加工精度难以严格控制,尺寸精度一般只能达到0.15~0.30mm。
此外,电解液对设备有腐蚀作用,电解液的处理也较困难。
2.电解加工设备
电解加工的基本设备包括直流电源、机床及电解液系统三大部分。
1)直流电源
电解加工常用的直流电源为硅整流电源和晶闸管整流电源,其主要特点及应用见表2。
2)机床
电解加工机床的任务是安装夹具、工件和阴极工具,并实现其相对运动,传送电和电解液。
它与一般金属切削机床相比,有其特殊要求:
(1)有足够的刚性
(2)稳定的进给速度
(3)防腐绝缘与好的安全措施
3)电解液系统
电解液可分为中性盐溶液、酸性盐溶液和碱性盐溶液三大类。
其中中性盐溶液的腐蚀性较小,使用时较为安全,故应用最广。
常用的电解液有NaCl、NaNO3、NaClO3三种。
电解液的作用:
1)作为到点介质、传递电流。
2)在电场作用下进行电化学反应,使阳极溶解能顺利而有效的控制的进行。
3)排出电解产物,带走热量。
电解加工的基本工艺规律p172
电解加工的精度主要取决于:
阴极的型面精度,复制精度及重复精度。
阴极的型面精度:
设计精度和制造精度。
复制精度:
加工出的形状和尺寸与阴极尺寸和形状相符合的程度。
重复精度:
指同一个工具电极加工一批工件的形状和尺寸的一致性。
提高电解加工精度的途径:
(一)脉冲电流电解加工
(二)小间隙电解加工
(三)改进电解液
(四)混气电解加工
3.3模具电解磨削加工
1.电解磨削原理
电解磨削又称电化学磨削,是将金属的电化学阳极溶解作用和机械磨削作用相结合的一种复合磨削工艺。
电解磨削加工的原理图如图3-46所示。
与一般磨削加工相比,电解磨削具有如下特点。
①加工范围广,加工效率高。
②磨削后的表面质量好。
③砂轮损耗小。
④与普通磨削相比,电解磨削也存在不足
2.电解磨削机床
电解磨削机床由机床主体、电解电源和电解液循环过滤系统等组成。
4.电解磨削的应用
(1)电解平面磨削。
(2)电解内、外圆磨削。
(3)电解成形磨削。
3.4模具电铸成形加工
3.4.1电铸成形原理和特点
电铸成型原理如图3-52所示。
在直流电源3的作用下,阳极上的表面金属发生阳极溶解反应而变为正离子进入电铸液,而电铸液中的金属离子在阴极沉积覆盖在母模上。
2.电铸成形特点
①复制精度高。
②电铸件有良好的使用性能。
③电铸设备简单,容易操作。
④电铸效率低。
⑤电铸层结构性差。
3.4.2电铸设备
①电铸槽。
电铸槽有内热式和外热式。
②直流电源。
电铸采用低电压、大电流的直流电源,常用硅整流或晶闸管直流电源。
③搅拌系统。
搅拌的方法有循环过滤法、超声振动法和机械搅拌法等。
④恒温控制装置。
加热时可用电炉、加热管,冷却时可用冷水管或冷动机,加热和冷却一般通过温度传感器来控制。
3.4.3电铸成形工艺过程
1.母模设计
2.电铸前的预处理
3.电沉积
4.脱模与加固
超声加工
7.