金属设备及建筑钢结构防腐涂装工艺标准Word文件下载.docx
《金属设备及建筑钢结构防腐涂装工艺标准Word文件下载.docx》由会员分享,可在线阅读,更多相关《金属设备及建筑钢结构防腐涂装工艺标准Word文件下载.docx(4页珍藏版)》请在冰豆网上搜索。
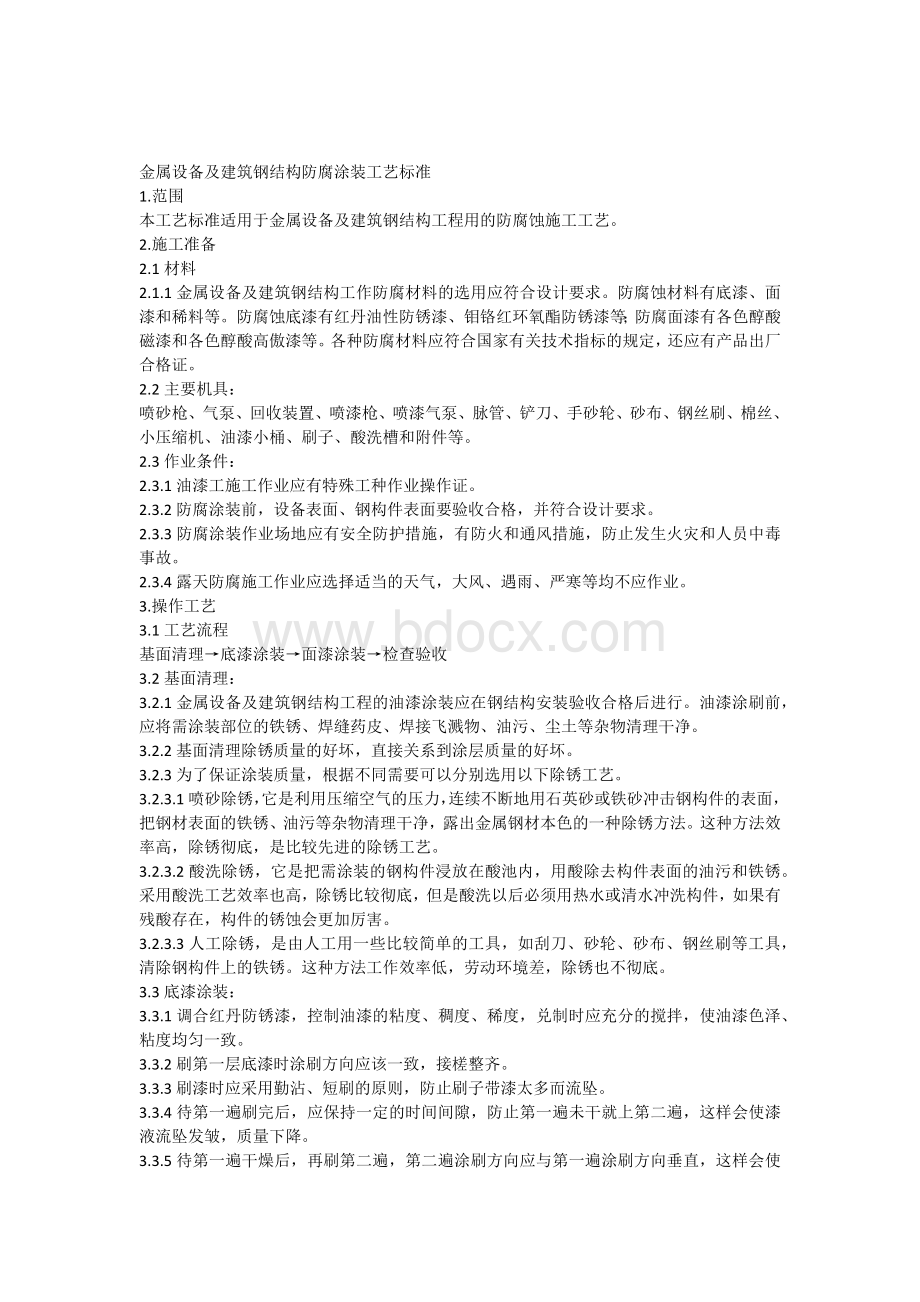
2.3.2防腐涂装前,设备表面、钢构件表面要验收合格,并符合设计要求。
2.3.3防腐涂装作业场地应有安全防护措施,有防火和通风措施,防止发生火灾和人员中毒事故。
2.3.4露天防腐施工作业应选择适当的天气,大风、遇雨、严寒等均不应作业。
3.操作工艺
3.1工艺流程
基面清理→底漆涂装→面漆涂装→检查验收
3.2基面清理:
3.2.1金属设备及建筑钢结构工程的油漆涂装应在钢结构安装验收合格后进行。
油漆涂刷前,应将需涂装部位的铁锈、焊缝药皮、焊接飞溅物、油污、尘土等杂物清理干净。
3.2.2基面清理除锈质量的好坏,直接关系到涂层质量的好坏。
3.2.3为了保证涂装质量,根据不同需要可以分别选用以下除锈工艺。
3.2.3.1喷砂除锈,它是利用压缩空气的压力,连续不断地用石英砂或铁砂冲击钢构件的表面,把钢材表面的铁锈、油污等杂物清理干净,露出金属钢材本色的一种除锈方法。
这种方法效率高,除锈彻底,是比较先进的除锈工艺。
3.2.3.2酸洗除锈,它是把需涂装的钢构件浸放在酸池内,用酸除去构件表面的油污和铁锈。
采用酸洗工艺效率也高,除锈比较彻底,但是酸洗以后必须用热水或清水冲洗构件,如果有残酸存在,构件的锈蚀会更加厉害。
3.2.3.3人工除锈,是由人工用一些比较简单的工具,如刮刀、砂轮、砂布、钢丝刷等工具,清除钢构件上的铁锈。
这种方法工作效率低,劳动环境差,除锈也不彻底。
3.3底漆涂装:
3.3.1调合红丹防锈漆,控制油漆的粘度、稠度、稀度,兑制时应充分的搅拌,使油漆色泽、粘度均匀一致。
3.3.2刷第一层底漆时涂刷方向应该一致,接槎整齐。
3.3.3刷漆时应采用勤沾、短刷的原则,防止刷子带漆太多而流坠。
3.3.4待第一遍刷完后,应保持一定的时间间隙,防止第一遍未干就上第二遍,这样会使漆液流坠发皱,质量下降。
3.3.5待第一遍干燥后,再刷第二遍,第二遍涂刷方向应与第一遍涂刷方向垂直,这样会使漆膜厚度均匀一致。
3.3.6底漆涂装后起码需4~8h后才能达到表面干固、表面干固前不应涂装面漆。
3.4面漆涂装
3.4.1金属设备及建筑钢结构涂装底漆与面漆一般中间间隙时间较长。
钢构件涂装防锈漆后送到工地去组装,组装结束后才统一涂装面漆。
这样在涂装面漆前需对钢结构表面进行清理,清除安装焊缝焊药,对烧去或碰去漆的构件,还应事先补漆。
3.4.2面漆的调制应选择颜色完全一致的面漆,兑制的稀料应合适,面漆使用前应充分搅拌,保持色泽均匀,其工作粘度、稠度应保证涂装时不流坠,不显刷纹。
3.4.3面漆在使用过程中应不断搅和,涂刷的方法和方向与上述工艺相同。
3.3.4涂装工艺采用喷涂施工时,应调整好喷嘴口径、喷涂压力,喷枪胶管能自由拉伸到作业区域,空气压缩机气压应在0.4~0.7N/㎜2.
3.4.5喷涂时应保持好喷嘴与涂层的距离,一般喷枪与作业面距离应100㎜左右,喷枪与钢结构基面角度应该保持垂直,或喷嘴略为上倾为宜。
3.4.6喷涂时喷嘴应该平行移动,移动时应平稳,速度一致,保持涂层均匀。
但是采用喷涂时,一般涂层厚度较薄,故应多喷几遍,每层喷涂时应待上层漆膜已经干燥时再进行。
3.5涂层检查与验收:
3.5.1表面涂装施工时和施工后,应对涂装过的工件进行保护,防止飞扬尘土和其它杂物。
3.5.2涂装后的处理检查,应该是涂层颜色一致,色泽鲜明光亮,不起皱皮,不起疙瘩。
3.5.3涂装漆膜厚度的测定,用触点式漆膜测厚仪测定漆膜厚度,漆膜测厚仪一般测定3点厚度,取其平均值。
4.质量标准
4.1保证项目应符合下列规定:
4.1.1油漆、稀释剂和固化剂等品种、型号和质量,应符合设计要求和国家现行有关标准的规定。
检验方法:
检查质量证明书或复验报告。
4.1.2涂装前钢材表面除锈应符合设计要求和国家现行有关标准的规定:
经化学除锈的钢材表面应露出金属色泽。
处理后的钢材表面应无焊渣、焊疤、灰尘、油污、水和毛刺等。
用铲刀检查和用现行国家标准《涂装前钢材表面锈蚀等级和除锈等级》规定的图片对照观察检查。
4.1.3不得误涂、漏涂,涂层应无脱皮和返锈。
观察检查。
4.2基本项目应符合下列规定:
4.2.1涂装工程的外观质量:
合格:
涂刷应均匀,无明显皱皮、气泡,附着良好。
优良:
涂刷应均匀,色泽一致,无皱皮、流坠和气泡,附着良好,分色线清楚、整齐。
检查方法:
4.2.2构件补刷漆的质量:
补刷漆漆膜应完整。
按每类构件数抽查10%,但均不应少于3件。
4.3涂装工程的干漆膜厚度的允许偏差项目和检验方法应符合规定。
干漆膜要求厚度值和允许偏差值应符合《钢结构工作施工及验收规范》的规定。
检查数量:
按同类构件数抽查10%,但均不应少于3件,每件测5处,每处的数值为3个相距约50㎜的测点干漆膜厚度的平均值。
5.成品保护
5.1设备或钢构件涂装后应加以临时围护隔离,防止踩踏,损伤涂层。
5.2钢构件涂装后,在4h之内如遇有大风或下雨时,应加以覆盖,防止粘染尘土和水气、影响涂层的附着力。
厂房内的设备也要做好防尘措施。
5.3涂装后的设备或钢构件需要运输时,应注意防止磕碰,禁止在地面拖拉,防止涂层损坏。
5.4涂装后的设备或钢构件勿接触酸类液体,防止咬伤涂层。
6.应注意的质量问题
6.1涂层作业气温应在5~38℃之间为宜,当天气温度低于5℃时,应选用相应的低温涂层材料施涂。
6.2当气温高于40℃时,应停止涂层作业。
因构件温度超过40℃时,在钢材表面涂刷油漆会产生气泡,降低漆膜的附着力。
6.3当空气温度大于85%,或构件表面有结露时,不宜进行涂层作业。
6.4设备或钢构件制作前,应对构件隐蔽部位、结构夹层难以除锈的部位,提前除锈,提前涂刷。
附件1:
国家标准GB8923-88《涂装前钢材表面锈蚀等级和除锈等级》
附件2:
地面、墙面涂装施工工艺标准
一、钢材表面锈蚀和除锈等级标准为国家标准GB8923-88《涂装前钢材表面锈蚀等级和除锈等级》。
二、标准将除锈等级分成喷射或抛射除锈、手工和电动除锈、火焰除锈三种类型。
三、喷射和抛射除锈,用字母“sa”表示,分四个等级:
sa1——轻度的喷射后抛射除锈。
钢材表面无可见的油脂、污垢、无附着的不牢的氧化皮、铁锈、油漆涂层等附着物。
sa2——彻底的喷射或抛射除锈。
钢材表面无可见的油脂、污垢,氧化皮、铁锈等附着物基本清除。
sa21/2——非常彻底的喷射或抛射除锈。
钢材表面无可见的油脂、污垢、氧化皮、铁锈、油漆涂层等附着物,任何残留的痕迹仅是点状或条状的轻微色斑。
sa3——使钢材表面非常洁净的喷射或抛射除锈。
钢材表面无可见的油脂、污垢、氧化皮、铁锈、油漆涂层等附着物,该表面显示均匀的金属色泽。
手工除锈等级:
St2彻底的手工和动力工具除锈
钢材表面应无可见的油脂和污垢,并且没有附着不牢的氧化皮、铁锈和油漆涂层等附着物。
St3非常彻底的手工和动力工具除锈
除锈应比St2更为彻底,底材显露部分的表面应具有金属光泽。
1.刮涂
刮涂是采用抹刀、刮板.或油灰刀刮补腻子或厚质涂料的方法。
刮涂的要点是实、平光。
即腻子与基层接触紧密、粘结牢固、表面平整光滑以减少打磨的工作量。
刮涂的注意事项如下:
1.1基层吸收性强时,应在刮补腻子前用底涂进行封闭,以免腻子中的胶料被基层过多地吸收影响腻子的附着性。
1.2掌握好刮涂时工具的倾斜度,用力均匀,以保证腻子饱满。
1.3为避免腻子收缩过大,出现开裂和脱落,一次刮不要过厚,根据不同腻子的特点,厚度以每遍0.5~1.0㎜为宜。
1.4不要过多地往返刮涂,以免出现卷落或将腻子中的胶料挤出封住表面造成不易干燥。
1.5根据涂料的性能及基层状况选择适当的腻子刮涂工具。
修补裂缝最好选弹性腻子,否则易产生裂纹。
用油灰刀填补基层孔洞及裂缝时,食指压紧刀片,用力将腻子压进缺陷内,要填满、填实,将四周的腻子收刮干净,使腻子的痕迹尽量减少。
2.打磨
打磨是指用研磨材料对被涂物面进行研磨的过程。
它对涂层的平整光滑、附着及基层菱角、线条都有较大影响。
要达到打磨的预期效果。
必须根据不同工序的质量要求,选择适当的打磨方法和工具。
打磨杳应注意以下几点:
2.1打磨必须在基层或腻子干燥后进行,以免粘附砂纸影响操作。
2.2不耐水的基层及腻子不能湿磨。
2.3砂纸的粗细要根据被磨表面的硬度来定,砂纸粗了会产生砂痕,影响涂层的最终装饰效果。
2.4打磨后应清除表面的灰尘,以利下道工序的进行。
2.5手工打磨应将砂纸(布)包在打磨垫上,往复用力推动垫块,不能只用一两个手指压着砂纸打磨,以免影响打磨的平整度。
机械打磨常用电动打磨机,将砂纸夹在打磨机上,轻轻在基层面上推动,严禁用力按压以免电机过载受损。
2.6检查基层的平整度在侧面光照下无明显凹凸和推刮痕迹、无粗糙感觉、表面光滑为合格。
3.刷漆
3.1面漆的调制应选择颜色完全一致的面漆,兑制的稀料应合适,面漆使用前应充分搅拌,保持色泽均匀,其工作粘度、稠度应保证涂装时不流坠(墙面),不显刷纹。
3.2刷漆时应采用勤沾、短刷的原则,防止刷子带漆太多而流坠或堆积,不易干。
3.3面漆在使用过程中应不断搅和,刷第一层底漆时涂刷方向应该一致,接槎整齐。
3.4待第一遍刷完后,应保持一定的时间间隙,防止第一遍未干就上第二遍,这样会使漆液流坠发皱,质量下降。
3.5待第一遍干燥后,再刷第二遍,第二遍涂刷方向应与第一遍涂刷方向垂直,这样会使漆膜厚度均匀一致。
4.注意事项
4.1基层处理要按要求施工,以保证表面油漆涂刷不会失败。
4.2清理周围环境,防止尘土飞扬。