汽车轻量化技术分析Word格式文档下载.docx
《汽车轻量化技术分析Word格式文档下载.docx》由会员分享,可在线阅读,更多相关《汽车轻量化技术分析Word格式文档下载.docx(6页珍藏版)》请在冰豆网上搜索。
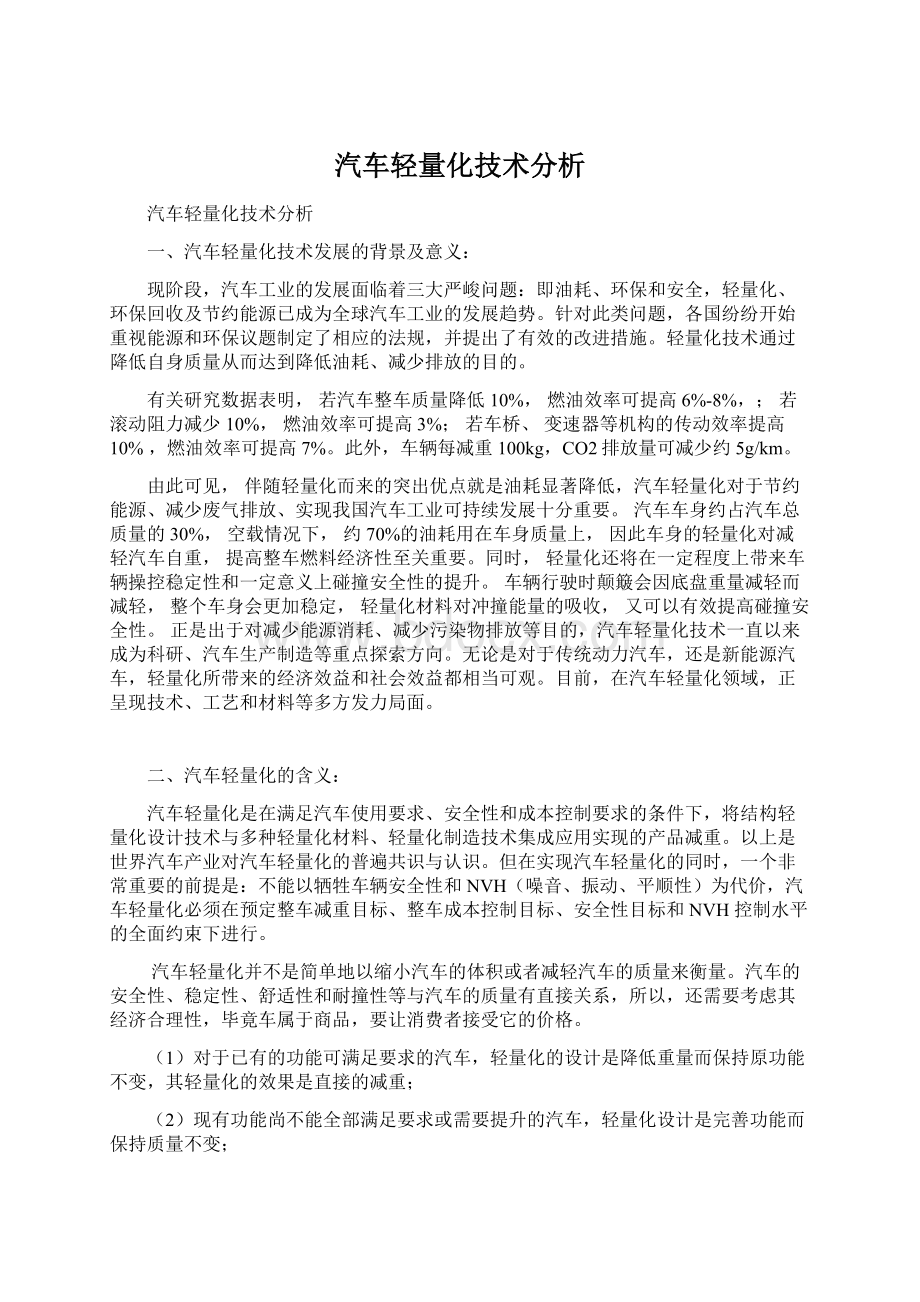
同时,轻量化还将在一定程度上带来车辆操控稳定性和一定意义上碰撞安全性的提升。
车辆行驶时颠簸会因底盘重量减轻而减轻,整个车身会更加稳定,轻量化材料对冲撞能量的吸收,又可以有效提高碰撞安全性。
正是出于对减少能源消耗、减少污染物排放等目的,汽车轻量化技术一直以来成为科研、汽车生产制造等重点探索方向。
无论是对于传统动力汽车,还是新能源汽车,轻量化所带来的经济效益和社会效益都相当可观。
目前,在汽车轻量化领域,正呈现技术、工艺和材料等多方发力局面。
二、汽车轻量化的含义:
汽车轻量化是在满足汽车使用要求、安全性和成本控制要求的条件下,将结构轻量化设计技术与多种轻量化材料、轻量化制造技术集成应用实现的产品减重。
以上是世界汽车产业对汽车轻量化的普遍共识与认识。
但在实现汽车轻量化的同时,一个非常重要的前提是:
不能以牺牲车辆安全性和NVH(噪音、振动、平顺性)为代价,汽车轻量化必须在预定整车减重目标、整车成本控制目标、安全性目标和NVH控制水平的全面约束下进行。
汽车轻量化并不是简单地以缩小汽车的体积或者减轻汽车的质量来衡量。
汽车的安全性、稳定性、舒适性和耐撞性等与汽车的质量有直接关系,所以,还需要考虑其经济合理性,毕竟车属于商品,要让消费者接受它的价格。
(1)对于已有的功能可满足要求的汽车,轻量化的设计是降低重量而保持原功能不变,其轻量化的效果是直接的减重;
(2)现有功能尚不能全部满足要求或需要提升的汽车,轻量化设计是完善功能而保持质量不变;
(3)既要提高改进性能,同时也使汽车减重。
正因如此,汽车轻量化设计实际上是功能改进,质量降低,结构优化和合理价格的结合。
三、汽车轻量化技术的发展历史与现状:
汽车结构的创新化设计和特殊材料的使用是汽车轻量化技术的重要组成部分。
如果汽车车身结构设计合理,不仅可以减少材料的使用量,还能达到轻量化的目的。
要想实现汽车轻量化,车身材料是非常重要的。
相关研究表明,汽车轻量化技术主要可以分为以下四个方面:
①轻量化材料:
实现汽车轻量化必须集成利用多种新材料和相关应用技术。
目前,汽车轻量化材料使用的主要是高强度钢,其次是铝镁合金、复合材料及塑料。
其中,高强材料主要用于降低钢板厚度,保证汽车结构和安全性能;
低密度材料主要用于非结构件替换和减轻汽车质量。
1)高强钢是轻量化的关键材料,它的大量使用既实现了整车轻量化,又保证了汽车的安全性和可靠性,因此,高强钢使用面广且量大。
1994年,为提高钢铁材料相比其它材料在车身上应用的竞争地位,国际钢铁协会组织世界18个国家35家钢铁公司并委托Porche公司,持巨资开展了超轻质钢车ULSAB(UltralightSteelAutoBody)项目。
开发出的超轻质钢车身质量为203kg,比同级别轿车车身质量平均减轻25%,与此同时车身扭转刚度提高了80%,弯曲刚度提高52%,车身第一阶固有频率上升到60Hz,并且完全满足碰撞安全性法规要求。
1997年开始,又开展了超轻钢汽车附件ULSAC(UltralightSteelAutoClosures)
项目。
通过将车门结构改用无框架形式,同时车门外板和车门管件均采用高强度钢制造,在满足所有结构性能要求的前提下减轻车门质量36%,而制造成本仅为133美元。
2)铝合金是轻质材料,具有良好的抗腐蚀性,应用前景良好。
近年来,铝材在汽车上应用量增加很快,主要是板材、挤压材、铸铝及锻铝,在车身结构、空间框架、外覆盖件和车轮等处均有大量应用。
HONDA公司1989年面市的NSX是一体式的铝车身结(单体构造车身),车身在融入轻量化设计理念之后,重量仅1270公斤。
采用此种结构的还有美洲豹新款“XJ”型轿车和福特公司的AIV轿车,AIV汽车总共使用铝台金270kg,比传统钢制汽车减轻200kg。
综合ASF与单体构造车身结构的优点,本田公司开发了Insight复合结构全铝车身,最大限度的发挥铝合金的优势。
与铝合金单壳体车身(NSX车)相比,Insight铝复合车身所用的零件少15%,焊点少24%。
此外,与三门钢车身Civic车相比,白车身的质量减小47%而扭转刚度提高38%,弯曲刚度提高13%,同时具有很好的碰撞安全性。
通用汽车公司开发的五座轿车Precept使用铝合金制造车身。
车身使用了49kg铝挤压型材、64kg铝合金板及32kg铝压铸件,与传统钢结构车身相比,Precept的车身质量减轻45%。
3)镁合金是比铝更轻的材料,其体积质量仅为1.8kg/m3,轻量化效果更明显。
起初是用于壳体类、气缸盖罩盖和方向盘骨架等件,现在已经扩展到座椅骨架、车门、车顶、仪表盘骨架和支架类零件。
20世纪90年代,奔驰公司首先在SL Roadster中采用了镁合金座椅,使车重明显减轻。
4)塑料及纤维复合材料在汽车工业的应用也日趋增加,汽车上应用塑料件已达数百个。
在重型卡车上塑料和复合材料的应用已超过150kg,由普通的塑料到高强度复合材料均有应用。
其中尤以SMC和GMT的应用最为广泛。
5)金属基复合材料是20世纪60年代发展的新材料,80年代之后进展很快。
汽车工业应用的MMC主要是纤维增强及颗料增强铝基复合材料。
应用于发动机与刹车系统零部件。
发动机零件有缸套、活塞、连杆、活塞销、摇臂和气门挺柱。
在刹车系统应用于刹车盘和刹车毂。
复合材料在整车车身上有一些应用,如通用公司的Johnson等研制成功一款复合材料白车身,在满足包括静刚度、耐久性、碰撞安全性等结构性能要求前提下,比传统钢车身质量减轻了60%。
1994年,克莱斯勒推出了复合材料概念车CCV(CompositeConceptVehicle),在节省加工时间约70%的同时,CCV质量减轻20~50%。
新型的奔驰S级车上总共使用了
180kg塑料及复合材料,其中有36kg的车身外零部件。
②优化设计:
随着汽车工业设计水平的不断提高,很多汽车开始采用超轻悬架结构、高刚性结构来减轻其质量,常采用优化并排焊点、加强筋、减重孔等方式来达到轻量化目的;
1)结构构建:
汽车的优化设计主要针对车身与关键零部件总成2个方面。
优化设计中可以:
1>
优化车身的空间结构,满足各种工作载荷;
2>
减小或减少车身多余的尺寸、零件数量和零部件厚度;
3>
优化零部件形貌,减少不必要的结构或用于增强的加强件数目。
2)材料选择:
优化设计的核心是通过对汽车产品的合理设计,在满足整车使用性和经济性各项要求的情况下,选择并使用适当的轻量化材料,需要利用设计者的经验和CAE技术。
前者的实质是轻量化数据库建设,设计者的经验可以通过积累获得转化,成为轻量化数据库专家系统的一环。
同时,从设计的静动力学分析,到关重件生产工艺模拟,再到整车性能研究,CAE技术的利用可以给出材料选择的合理预判。
3)工艺预置:
汽车结构复杂,它的工艺实现对整车能否达到轻量化目标有着至关重要的影响。
汽车业的发展,使高强钢、铝镁合金和复合材料不断推出,也对应用工艺提出了新要求。
如:
界别越高的高强钢,在成形性上要求越高,热成形技术是个好办法;
有的部件如轿车的副车架,形状复杂且生产困难,液压成形能提供一个解决途径。
而通过CAE技术可以分析出这些工艺的可行性和路径。
4)试验仿真:
一切车辆的好坏,免不了试验的验证。
在轻量化的发展中,国外的汽车检测法规甚至已经用CAE分析替代部分试验测试,其结果得到各界确认而成为标准要求。
对汽车轻量化影响最大的几项总体和零部件的试验包括:
白车身弯扭试验、白车身NVH试验、白车碰撞试验及保险杠碰撞试验等,都可以通过CAE技术得到良好的仿真结果。
③制造工艺:
成形方法和联接技术不断创新,如柔性化板材辊轧、剪拼焊接工艺技术、薄壁制造技术等,大大减轻了整车的重量。
1)热成形技术的应用:
既要轻量化又要提高汽车性能的一个手段就是采用高强度的轻量化材料。
其优点有:
通过快速冷却淬火,热成形后制件强度得到大幅提高;
成形性优良;
降低压机吨位;
尺寸精度较高;
零件表面硬度、抗凹性和刚度好。
目前,乘用车达到Uncap碰撞4星和5星级水平的车型,在主要的安全件中(A,B,C3柱和保险杠防撞梁、门防撞杆及保险杠防冲柱等)普遍采用了抗拉强度为1500MPa,屈服强度为1200MPa的马氏体钢,如此高的强度之所以能够实现,在于热成形钢材与工艺技术的发展,。
材料的加工成形性与屈服强度和延伸率有密切关系,而材料的断裂应变和屈服强度与材料的温度有密切关系。
在900℃时,热成形钢屈服强度下降至150MPa,断裂应变达到50%以上,具有良好成形性和可加工性,在热成形之后,随之进行冷却淬火达到高的强度,并固定了热成形状态下的零件形状。
2)液压成形技术的应用:
液压(内高压)成形是指采用液态物质作为施力介质,使坯料在施力介质作用下,贴合凸模或凹模面成形。
它是一种柔性成形技术,可以为一些形状复杂、强度高和成形性差的材料提供理想成形工艺。
液压成形分为板材液压成形和管材液压成形,在汽车工业中,应用较多的是管材内高压成形。
与冲压焊接件相比,管材液压成形的优点是:
节约材料;
减少后续工作量;
由于焊接减少,可提高构件的强度与刚度;
4>
与冲焊件相比,材料利用率为95%~98%;
5>
降低生产成本和模具费用达30%。
3)激光拼焊板技术的应用:
由于激光焊接技术的特殊性,焊接速度快,热影响区小,因此,激光拼焊板材的成形性良好。
激光拼焊板技术将不同厚度、不同强度或不同表面处理状态的板材通过激光拼焊集成一个大的板坯进行冲制,这样可使模具的数量和后续生产工序减少,从而降低了生产成本,并提高了零部件的质量,优化了零件结构,充分发挥了不同强度和不同厚度板材的特性。
在汽车中采用激光拼焊板材后,可使零件质量减轻24%,零件数量减少19%,焊点数下降49%,生产时间缩短21%,其典型构件为:
车门内板、侧围板、地板和一些车身高强度结构件。
4)金属半固态成形技术的应用:
金属半固态成形技术的特点是高效、高性能、低成本与节能环保,该技术经过多年不断发展,日趋成熟。
20世纪90年代,西方国家就已进入产业化应用阶段,并对铝合金在汽车结构零件中的推广起到重要作用。
目前,德国EFU,法国Pechiney,美国Alunax公司,瑞士Alusuisse公司和意大利Stampal公司等,均已形成相当规模的产业,大量用于汽车零部件的制备。
铝合金半固态成形件单件尺寸与质量也不断加大,意大利Stampal和Fiat公司生产的半固态铝合金零件重达7kg。
5)连续变截面辊轧板:
续变截面辊轧板(TRB)轧制属柔性轧制技术,其原理是在轧制过程中通过计算机实时控制和调整轧辊间距,获得沿轧制方向上按预定的厚度连续变化的板材,以取代应用日益广泛