年产300万吨生铁高炉设计指导书讲诉Word文档下载推荐.docx
《年产300万吨生铁高炉设计指导书讲诉Word文档下载推荐.docx》由会员分享,可在线阅读,更多相关《年产300万吨生铁高炉设计指导书讲诉Word文档下载推荐.docx(43页珍藏版)》请在冰豆网上搜索。
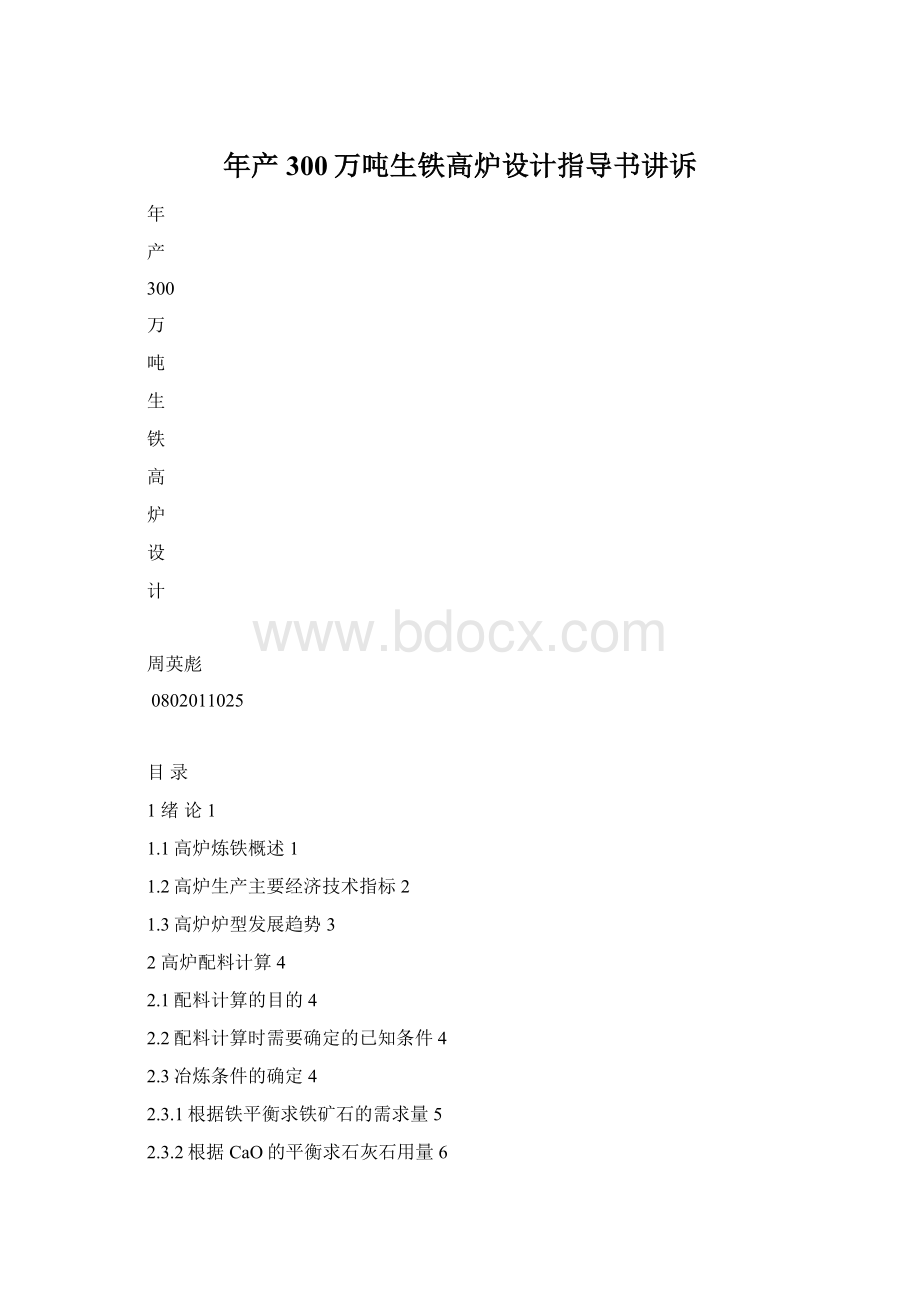
2.5.2热量支出项的计算15
2.5.3热平衡表及能量利用评定18
3高炉炉型设计19
3.1高炉容积的确定19
3.2高炉炉型及尺寸确定19
参考文献23
1绪论
1.1高炉炼铁概述
1、高炉结构
高炉是一种竖式的反应炉。
现代高炉内型一般由圆柱体和截头圆锥体组成,由下而上分为炉缸、炉腹、炉腰、炉身和炉喉五段。
由于高炉炼铁是在高温下进行的,所以它的工作空间是用耐火材料围砌而成,外面再用钢板作炉壳。
图1-1高炉的结构
1—炉底耐火材料;
2—炉壳;
3—生产后炉内砖衬侵蚀线;
4—炉喉钢砖;
5—煤气导出管;
6—炉体夸衬;
7—带凸台镶砖冷却壁;
8—镶砖冷却壁;
9—炉底碳砖;
10—炉底水冷管;
11—光面冷却壁;
12—耐热基墩;
13—基座
2、高炉炼铁原理及工艺流程示意图
高炉生产是连续进行的。
一代高炉(从开炉到大修停炉为一代)能连续生产几年到十几年。
生产时,从炉顶(一般炉顶是由料种与料斗组成,现代化高炉是钟阀炉顶和无料钟炉顶)不断地装入铁矿石、焦炭、熔剂,从高炉下部的风口吹进热风(1000~1300℃),喷入油、煤或天然气等燃料。
装入高炉中的铁矿石,主要是铁和氧的化合物。
在高温下,焦炭中和喷吹物中的碳及碳燃烧生成的一氧化碳将铁矿石中的氧夺取出来,得到铁,这个过程叫做还原。
铁矿石通过还原反应炼出生铁,铁水从出铁口放出。
铁矿石中的脉石、焦炭及喷吹物中的灰分与加入炉内的石灰石等熔剂结合生成炉渣,从出铁口和出渣口分别排出。
煤气从炉顶导出,经除尘后,作为工业用煤气。
现代化高炉还可以利用炉顶的高压,用导出的部分煤气发电。
高炉炼铁工艺流程示意图见图1-2。
图1-2高炉炼铁工艺流程示意图
1.2高炉生产主要经济技术指标
1、高炉有效容积利用系数(η)
指高炉每立方米有效容积一昼夜生产合格铁水的吨数,单位为t/(m3•d)。
η是高炉冶炼的一个重要指标,η越大,其高炉生产率越高。
小型高炉利用系数可达2.8~3.2,大型高炉一般为2.0~2.5。
2、焦比(K)
每炼一吨生铁所消耗的焦炭量,单位为Kg/t-Fe。
先进高炉焦比为300~400公斤/吨生铁。
焦炭价格昂贵,降低焦比可降低生铁成本。
3、燃料比(i)
高炉采用喷吹煤粉、重油或天然气后,折合每炼一吨生铁所消耗的燃料总量,单位为kg/t-Fe。
每吨生铁的喷煤量和喷油量分别称为煤比和油比。
此时燃料比等于焦比加煤比加油比。
根据喷吹的煤和油置换比的不同,分别折合成焦炭(公斤),再和焦比相加称为综合焦比。
燃料比和综合焦比是判别冶炼一吨生铁总燃料消耗量的一个重要指标。
4、高炉炼铁强度(I)
每昼夜高炉燃烧的焦炭量与高炉容积的比值,是表示高炉强化程度的指标,单位为t/(m3•d)。
5、休风率
休风时间占全年日历时间的百分数。
降低休风率是高炉增产的重要途径一般高炉休风率低于2%。
6、生铁合格率
化学成分符合规定要求的生铁量占全部生铁产量的百分数,是评价高炉优质生产的主要指标。
7、炉龄
炉龄的定义为两代高炉大修之间高炉实际运行的时间,即不计划中进行中小修而造成的休风以及封炉时间。
1.3高炉炉型发展趋势
高炉的炉型随着高炉精料性能,冶炼工艺,高炉容积,炉衬结构,冷却形式的发展而演变,高炉设计的理念也随着科学技术的进步和生产实践的进展而更新。
总结国内外同类型容积高炉尺寸,原燃料条件,强化冶炼的矮胖型炉型已成为主要的炉型,其优点如下:
1、适当矮胖,减小炉腹角,炉身角。
较小的炉身角有利于受热膨胀后炉料下降,较小的炉腹角有利于煤气流的均匀分布,减小对炉腹生成渣皮的冲刷,保护炉腹冷却壁,延长其寿命。
2、加深死铁层厚度,有利于开通死料柱下部通道,从而减少出铁时铁水环流对炉衬的侵蚀,提高炉底炉缸的寿命。
同时较深的死铁层可多贮存铁水,保证炉缸有充足的热量储备,稳定铁水的温度和成分。
3、加大炉缸的高度。
可保证风口前有足够的风口回旋区,有利于煤粉的充分燃烧及改善高炉下部中心的透气性,有利于改善气体动力学条件。
2高炉配料计算
2.1配料计算的目的
配料计算的目的,在于根据已知的原料条件和冶炼要求来决定矿石和熔剂的用量,以配制合适的炉渣成分和获得合格的生铁。
2.2配料计算时需要确定的已知条件
本设计所选混合矿的组成为烧结矿:
球团矿:
生矿=80:
16:
4。
各矿物成分及计算后的混合矿成分见表2-1。
表2-1各矿物及混合矿成分(%)
成分原料
Fe
P
S
FeO
Fe2O3
SiO2
CaO
MgO
烧结矿
52.744
0.039
0.030
15.200
58.460
9.760
10.100
3.740
球团矿
49.630
0.044
0.100
12.420
57.100
14.340
10.200
2.100
天然矿
62.546
0.052
0.110
13.96
73.84
3.96
0.74
0.29
混合矿
52.637
0.04032
14.7056
58.8576
10.261
9.742
3.340
Al2O3
P2O5
S/2
K2O
Na2O
MnO
烧损
合计
1.365
0.090
0.015
0.300
0.050
0.920
100.00
2.120
0.260
0.060
1.050
0.2
3.200
0.120
0.055
0.232
0.103
2.190
1.31
1.559
0.093
0.0222
0.291
0.054
0.992
0.084
2.3冶炼条件的确定
设计中需要的各种成分如以下各表所示。
表2-2碎铁成分表
成分
C
质量分数/%
85.00
9.00
3.00
100
表2-3焦炭工业分析表
固定碳
灰分
挥发分
有离水
85.02
12.94
1.17
0.87
3.2
表2-4焦炭、煤粉灰分分析表
SO3
焦炭
0.95
49.9
34.09
0.37
3.02
0.88
1.24
9.46
煤粉
1.03
48.31
35.82
0.30
3.68
2.98
0.93
6.95
表2-5焦炭挥发成分
CO2
CO
H2
CH4
N2
34.2
37.8
6
4
18
表2-6煤粉成分表
H
O
N
S
H2O
76.49
11.18
3.51
6.01
0.60
0.36
1.85
表2-7炉尘成分表
41.467
0.04
0.40
51.45
7.01
8.30
17.64
8.61
1.97
2.61
表2-8各种元素在炉渣、生铁和煤气中的分配率
产品
Mn
生铁η
0.997
0.70
1.00
炉渣μ
0.003
0.00
煤气λ
表2-9生铁成分表
成分
Si
Σ
质量分数/%
0.35
0.94
0.08
3.63
94.99
其它各种参数的选择。
1、本设计所使用混合矿组成为,烧结矿:
生矿=80:
16:
4;
2、湿焦比(1t生铁)为390kg/t;
3、煤粉喷吹量(1t生铁)为175kg/t;
4、碎铁使用量(1t生铁)为50kg/t;
5、选择炉渣碱度w(CaO)/w(SiO2)=1.05;
6、鼓风湿度ф=1.5%;
7、炉尘吹出量为(1t生铁)为30kg/t;
8、直接还原度rd=0.4;
9、焦炭与喷吹燃料中总碳量的1%和H2生成CH4;
10、喷吹条件下,进入炉内的H2有35%消耗于FeO还原成Fe的过程
11、热风温度T=1100℃,炉顶煤气温度T=200℃。
2.3.1根据铁平衡求铁矿石的需求量
1、焦炭带入的铁量
(1)Fe2O3~2Fe
160112
0.0088x故:
x=0.00616
(2)FeO~Fe
7256
0.0946y故:
y=0.0735
所以,焦炭带入的铁量
2、矿石的需求量
式中:
—矿石的需求量(1t生铁),kg\t;
—进入生铁的铁量(1t生铁),kg\t;
—进入炉渣的铁量(1t生铁),kg\t;
—进入炉尘的铁量(1t生铁),kg\t;
—碎铁带入的铁量(1t生铁),kg\t;
—焦炭带入的铁量(1t生铁),kg\t;
—煤粉带入的铁量(1t生铁),kg\t;
—矿石含铁量(1t生铁),kg\t;
其中,
的计算方法如下:
159.7111.7
0.0298x故:
x=0.021
71.7555.85
0.0695y故:
y=0.054
根据以上计算
所以
2.3.2根据CaO的平衡求石灰石用量
表2-10溶剂的成分表
0.014
0.012
52.78
1.32
1.62
0.03
42.90
根据CaO的平衡求石灰石用量,本设计的碱度w(CaO)/w(SiO2)=1.05。
石灰石的用量:
—溶剂的需要量(1t生铁),kg\t;
—炉渣