高炉料车上料自动控制原理毕业设计Word格式文档下载.docx
《高炉料车上料自动控制原理毕业设计Word格式文档下载.docx》由会员分享,可在线阅读,更多相关《高炉料车上料自动控制原理毕业设计Word格式文档下载.docx(52页珍藏版)》请在冰豆网上搜索。
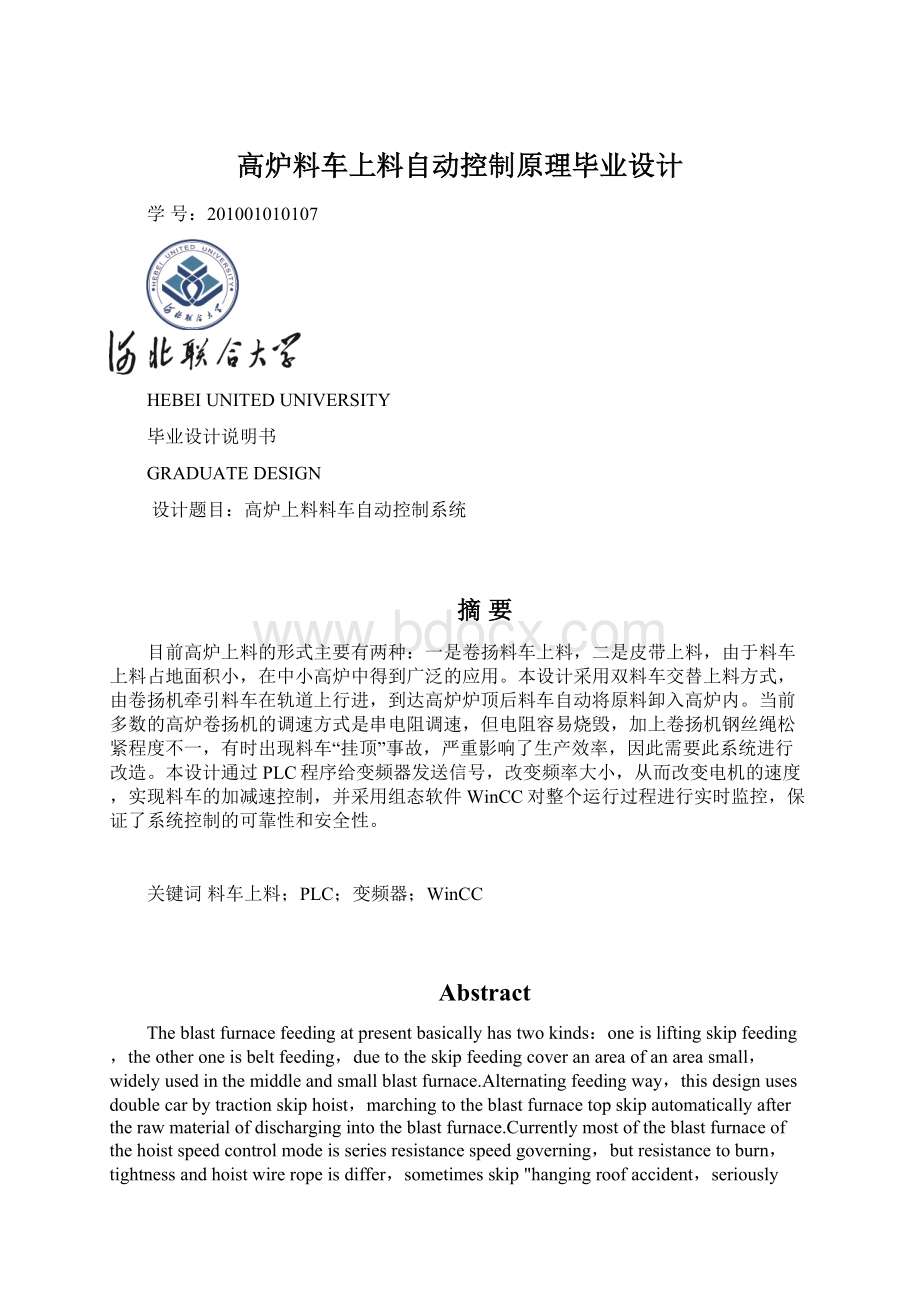
本设计通过PLC程序给变频器发送信号,改变频率大小,从而改变电机的速度,实现料车的加减速控制,并采用组态软件WinCC对整个运行过程进行实时监控,保证了系统控制的可靠性和安全性。
关键词料车上料;
PLC;
变频器;
WinCC
Abstract
Theblastfurnacefeedingatpresentbasicallyhastwokinds:
oneisliftingskipfeeding,theotheroneisbeltfeeding,duetotheskipfeedingcoveranareaofanareasmall,widelyusedinthemiddleandsmallblastfurnace.Alternatingfeedingway,thisdesignusesdoublecarbytractionskiphoist,marchingtotheblastfurnacetopskipautomaticallyaftertherawmaterialofdischargingintotheblastfurnace.Currentlymostoftheblastfurnaceofthehoistspeedcontrolmodeisseriesresistancespeedgoverning,butresistancetoburn,tightnessandhoistwireropeisdiffer,sometimesskip"
hangingroofaccident,seriouslyaffectedtheproductionefficiency,soneedtomodifythesystem.ThisdesignthroughthePLCprogramdesignsize,sendasignaltofrequencyconvertertochangefrequencytochangethespeedofthemotor,tocontrolthedecelerationoftheskip,andusestheconfigurationsoftwareWinCCreal-timemonitoringofthewholeoperationprocess,ensurethereliabilityandsecurityofthesystemcontrol.
KeywordsTheskiploading;
Frequencyconverter;
WinCC
第1章绪论
1.1高炉上料系统
1.1.1高炉上料系统简介
高炉上料是整个高炉冶炼生产的关键环节,担负着为炼铁高炉提供原料的功能。
高炉上料系统将来自料仓的各种原料按一定的配料比送到高炉内进行冶炼,整个上料过程大部分是顺序逻辑控制,涉及到一些模拟量控制,但没有反馈,不构成闭环过程控制,故而多采用可编程控制器(PLC)进行控制。
一是卷扬料车上料,二是皮带上料。
高炉上料方式应以满足总图布置要求和满足上料能力为前提来选择合理的上料方式,对750至1500级高炉来说,料车上料与皮带上料均能满足上料能力的要求,在这种情况下,若在总图布置与工艺布置上无优势,如无地形高差优势,无物料输送短捷优势,则宜采用料车上料方式。
因此,在《高炉炼铁工艺设计技术规定》中也明确750级高炉应采用料车上料,1200级至2000级高炉可采用料车上料方式,也可采用皮带上料方式。
1.1.2国内外高炉上料方式比较
表1-1列出了国内外750~1500级高炉上料方式的部分实例,从表中可看出,大部分为料车上料,其中攀钢4BF和重钢5BF,水钢1BF和2BF,均因利用了地形高差而采用皮带上料,其余高炉的皮带上料为无地形高差,矿槽地平面与高炉地平面处于同一水平。
表1-1国内外750~1500高炉上料方式
厂名
炉号
炉容
出铁厂及铁口个数
上料方式
攀钢
1
1200
料车上料
4
1350
2
皮带上料
重钢
5
宣钢
8
1260
首钢
1036
梅钢
1080
1250
水钢
788
本钢
2000
酒钢
1000
武钢
1386
1536
3
1513
邯钢
日本新日铁室兰
1249
日本新日铁釜石
1150
德国蒂森公司
1445
法国索拉克帕塔拉尔
6
1275
英国雷文斯克雷格
1414
巴西沃尔塔雷东达
1160
1378
澳大利亚纽卡斯尔
1075
1/2
1288
1.1.3皮带上料与料车上料投资比较
采用皮带上料时,由于矿槽布置远离高炉,当球团矿用量高于10%,皮带机倾角不应超过12°
,因此在无地形高差优势条件下,750~1500级高炉炉顶皮带机头轮标高分别为50m和56m,则上料主皮带机水平长度分别为245m和275m。
采用料车上料时,矿槽布置紧靠高炉,750和1500高炉矿槽中心距高炉中心分别为48m和55m,因此750和1500高炉皮带上料与料车上料相比,矿槽距高炉中心要远197m和220m,折合成占地,则要多占1180和1400。
由于皮带上料方式与料车上料方式相比,矿槽距高炉中心更远,因此,皮带上料方式的钢结构量和设备质量更重。
以某厂750高炉为例:
在矿槽地坪比高炉地坪高12m,主皮带机尾轮距高炉中心约200m的前提下,皮带上料方案比料车上料仍要多685万元投资。
1.1.4皮带上料与料车上料运行费用比较
皮带上料与料车上料相比,电机功率大,运行时间长,因此,运行费较高。
皮带为连续运转,而料车运行时间正常只有60%左右,因此即使在功率相同情况下,皮带上料运行费也比料车上料高40%。
以750高炉为例:
皮带上料传动装置为4×
110kW,料车上料传动装置为2×
190kW,电价按0.153元/kWh计,料车上料每天142批,每批上料时间为4×
41秒,则皮带上料年运行费要比料车上料高出10517万元/a,电耗高出19914万kWh。
按高炉利用系数214t/m3∙d计算,则皮带上料比料车上料吨铁耗电要高出3104kWh。
以上比较仅仅是对上料主皮带机与料车运行的比较,由于皮带上料矿槽布置远离高炉,因此一般情况下,上高炉矿槽的运料皮带要比料车上料方式的长,若加上这些皮带的运行费,则总运行费还要增加。
首钢2号高炉(1327)采用皮带上料,而4号高炉(1200)采用料车上料,实测耗电结果是2号高炉比4号高炉每吨铁多耗电815kWh。
综上所述,由于本设计是对小型高炉上料系统进行设计改造,为了节省了占地面积和减少运行成本,所以采用料车上料方式。
1.2料车上料简介
本设计采用料车上料方式。
在工作过程中使用两个料车交替上料。
两个料车由同一台卷扬机通过钢丝绳牵引,当装满炉料的料车上升时,空料车下行,空车重量相当于一个平衡锤,平衡了重料车的车箱自重。
由于电动机始终处于电动状态运行,免去了电动机处于发电运行状态所带来的种种问题。
料车上料系统的机械构成主要包括料坑、料车、斜桥、卷扬机,结构如图1-1所示。
图1-1料车上料系统简图
第2章整体设计方案
在高炉料车上料系统中,对料车运行速度的精确控制是关键。
传统的调速方案采用在电动机电路中串接电阻的方法,这种老式做法的含有许多缺点,例如速度控制精度差、不容易重新设置电动机转速和电阻容易烧坏等。
因此本设计采用可编程控制器(PLC)与变频器的组合方案,极大的提高了料车运行速度控制的精度,重新设定料车的运行速度大小也很方便,只需在变频器的参数设置面板中设定即可。
系统运行时,左右两个料车由同一根钢绳牵引,运动速度大小相同,方向相反,以左料车为例进行说明:
左料车斜桥上面依次装有四个行程开关,料车在斜桥桥底时首先触碰到“高速上行行程开关”,行程开关通过数字量输入模块将信号送入PLC中,经过PLC运算处理后又将输出量信号通过数字量输出模块送入变频器中,变频器与电动机直接相连,通过对其设定不同的频率值,可以改变电动机的运行转速。
左料车高速上行至“中速上行行程开关”处,PLC再次将中速上行信号送入变频器中,变频器通过降低频率值进而降低电动机转速,实现料车第一次减速。
当料车将要到达高炉炉顶时,料车触碰“低速上行行程开关”进行最后一次减速。
左料车以低速上行到炉顶后撞击到“上行极限开关”,极限开关将停车信号送入PLC中,随后PLC向变频器发出停车信号,变频器将电动机转速降低为零,同时PLC向抱闸继电器发出抱闸信号,左料车停车并自动开始向高炉上料。
上料持续10s,然后PLC向变频器发出电机反转信号同时打开抱闸,开始右车上料。
根据料车的运行速度,可画出变频器频率曲线,如图2-1所示。
图中OA为重料车启动加速段,加速时间为3s;
AB为料车高速运行段,频率为50Hz,电动机转速为740r/min,钢绳速度1.5m/s;
BC为料车的第一次减速段,由行程开关发出第一次减速信号给PLC,PLC控制变频器使频率从50Hz下降到20Hz,电动机转速从740r/min下降到296r/min,钢绳速度从1.5m/s下降到0.6m/s;
DE为第二次减速段,频率为6Hz,钢绳速度由由0.6m/s下降到0.18m/s。
当料车运行至高炉顶时,限位开关发出停车命令,由PLC控制变频器完成停车。
左右料车运行速度曲线一致。
图2-1变频器频率曲线
在设备需要检修或出现故障需要人工排除时,需要操作人员对上料系统进行手动操控。
因此在PLC程序设计中除自动运行方案外还需要加入手动运行方案。
在手动操控时,按下控制面板上面相应的运行状态按钮,料车会按程序设定的相应的动作运行。
除此之外,为防止出现“松绳故障”,“变频器故障”时造成人身伤害,还需设计出在故障发生时系统自动抱闸的程序。
除了在生产现场可以通过控制面板上的按钮对上料系统进行操控外,本设计添加了上位机监控模式,使得工程人员可以在主监控室内通过在个人电脑中安装的上位机监控软件对整个系统进行实时监控,并可以通过监控界面上的虚拟按钮操控整个上料系统。
整个设计方案的系统结构框