压铸课程设计说明书资料Word格式.docx
《压铸课程设计说明书资料Word格式.docx》由会员分享,可在线阅读,更多相关《压铸课程设计说明书资料Word格式.docx(17页珍藏版)》请在冰豆网上搜索。
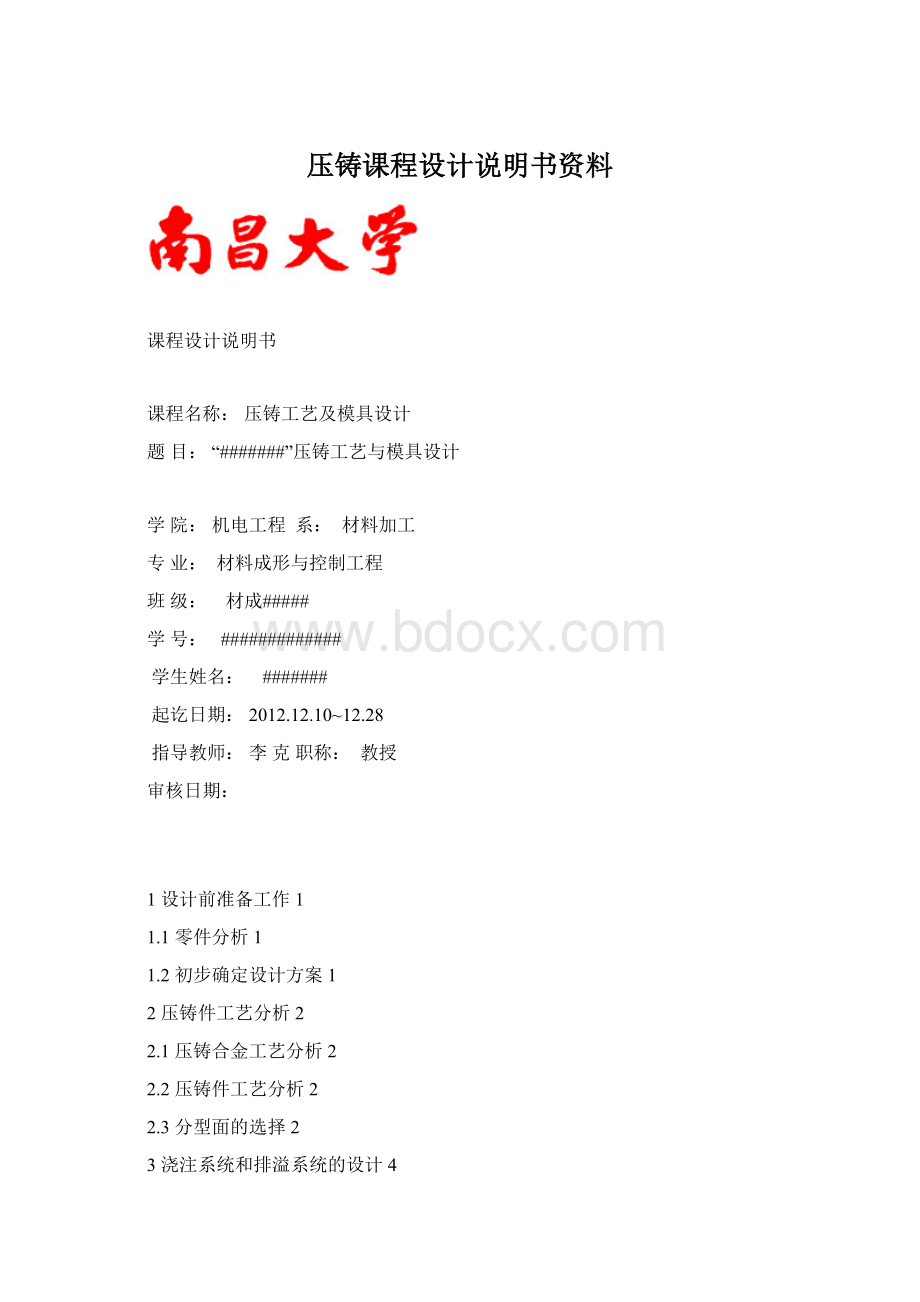
1.1零件分析1
1.2初步确定设计方案1
2压铸件工艺分析2
2.1压铸合金工艺分析2
2.2压铸件工艺分析2
2.3分型面的选择2
3浇注系统和排溢系统的设计4
3.1浇注系统的设计4
3.2排溢系统的设计6
3.2.1溢流槽的设计要点6
3.2.2溢流槽位置的选择6
4压铸模结构设计8
4.1压铸机的选择8
4.1.1确定模具分型面上铸件的总投影面积8
4.1.2确定压射比压9
4.1.3根据铸件的材料、结构、壁厚:
9
4.2型腔和型芯尺寸的设计9
4.3镶块、型芯、模板的设计11
4.3.1镶块的设计11
4.3.2模板的设计12
4.4导柱、导套的设计13
4.5推出机构、复位机构的设计14
5压铸模总装技术要求15
5.1结构零件的公差和配合15
5.2压铸模总装技术要求15
5.3压铸模的材料选择和热处理15
6压铸工艺流程17
参考文献18
1设计前准备工作
1.1零件分析
金属压铸成型是将熔融的金属液在较高的压力下,以高速的填充入压铸模型腔,并使金属液在高压状态下凝固而形成金属压铸件的过程。
它是目前所有金属铸造成型方法中效率最高的一种。
随着金属压铸成型技术的发展,金属压铸成型技术与塑料注射成型、金属板的冲压成型并列为三大成型体系。
金属压铸成型的显著特点是:
可以成型形状复杂、壁薄的有色金属结构件,是一种高效率、高精度、高互换性、低消耗的精密零件成型技术。
金属压铸成型的过程是将熔融的金属液注入压铸机的压室,在压射冲头的高压作用下,高速度地推动金属液经过压铸模具的浇注系统,注入并充满型腔,通过冷却、结晶、固化等过程,成型相应的金属压铸件。
1.2初步确定设计方案
1、此铸件的材料为ZL102,应在适当的温度下流动性较好是浇注,使能充满型腔。
2、铸件的精度为6级,采用压力铸造的方法能达到此精度。
3、确定压铸工艺及模具制造能力。
4、确定压铸模结构(包括型腔数目,模板的尺寸设计,导柱、导套尽量使用国标能缩短制造周期,以及采用型芯、型腔镶块节约贵重金属)。
5、模具设计是要留收缩率尺寸。
2压铸件工艺分析
2.1压铸合金工艺分析
铝合金具有良好的压铸性能,导电性和导热性都很好。
铝合金的密度小比强度和比刚度高是其突出的优点。
铝合金的高温力学性能也很好,在低温下工作是同样保持良好的力学性能,且铝合金熔铸工艺简单,成形和切削加工性能良好,有较高的力学性能和耐蚀性,但在熔炼的时,铝液要在溶剂保护下进行熔炼和保温,以防合金液吸气和产生氧化夹杂物。
2.2压铸件工艺分析
为了从根本上防止压铸件产生缺陷,比以低成本,连续不断地生产高质量的压铸件,必须使压铸件的结构适合于压铸。
主要对铸件的壁厚、圆角、筋、出型斜度,孔,螺纹、加工余量、文字、标志、图案等进行分析。
对次铸件壁厚均匀适合压铸。
铸件本身有斜度且能减少出型时与型壁的摩擦。
铸件边缘有孔且与型芯方向一致,所以在铸造时铸出。
铸件上有螺纹与型芯方向垂直,不宜在铸造时铸出,且螺纹的铸造模具加工时相当的困难,所以螺纹在铸件铸出后进行加工。
1)该压铸件尺寸比较小,一般精度等级,为降低设计难度和设计周期,应采一模一腔,且需要对压铸件去除浇口废料。
2)为了节约成本和方便加工与热处理,型腔型芯均采用镶块式结构。
3)零件的密度为2.65,重量约为25.94g。
4)为了提高生产效率并且考虑到铝合金的熔点,选用冷室卧式压铸机用铸模。
2.3分型面的选择
在分型面选择的时候有两种方案:
首先考虑模具起模时,铸件留在动模上,所以有(图1)所视Ⅰ与Ⅱ两种方案。
方案Ⅰ:
方案Ⅰ容易起模,易使铸件留在动模上,起模方便,适合本铸件的起模方式。
方案Ⅱ:
易留在定模上,不适合。
综上所述,选用方案Ⅰ,分型面形式见图
(1)。
(图1)零件图
3浇注系统和排溢系统的设计
3.1浇注系统的设计
经过对铸件的结构分析,铸件是板件,对浇注系统的选择可选择侧浇口,在浇注时金属液从型腔侧面导入,然后自下而上推向进型腔,有利于金属液的充填和排气。
浇注系统的结构见(图2)。
(图2)铸件图
对浇注系统尺寸的选择
如(图3)
L2+3L1h2>
2hh3=2L1
(图3)横浇道与内浇口和铸件之间的连接方式
H铸件平均壁厚为2.7
取h1=1.2;
L1=2;
h2=4
(图4)横浇道尺寸
根据铸件结构和尺寸,b取3.5,h取4。
3.2排溢系统的设计
3.2.1溢流槽的设计要点
(1)正确布置溢流槽在模具中的位置
1)是金属液在横浇道内或进入型腔后最先冲击的部位。
2)是受金属液冲击型芯后面或多股金属液相汇合处容易产生涡流裹气或氧化夹杂的部位。
3)是金属液最后充填的部位。
4)是型腔温度较低的部位。
5)内浇口两侧或其他金属液不能直接充填的死角部位。
6)其他需控制局部金属液流动状态以消除疵病的部位。
(2)溢流槽的溢流口总截面积应小于内浇口的总截面积。
(3)采用多个单独的溢流槽要比一个同等容积的溢流槽,更容易控制从压铸件周围任何部分外流的金属液。
(4)根据溢流槽的作用确定其容积。
3.2.2溢流槽位置的选择
溢流槽位置的选择应遵循如下的原则:
(1)溢流槽应开设在金属液最先冲击的部位,排除金属液流前头的气体和冷污金属液,稳定流态状态,减少涡流。
(2)溢流槽应开设在两股金属液流会和的地方,清除集中于该处的气体、冷污金属液和冷料残渣等。
(3)溢流槽应开设在内浇口两侧或金属液不能顺利充填的死角区域,起到引流充填的作用。
(4)溢流槽应开设在压铸件局部壁厚的地方,并且增大其容量和溢流口的厚度,以便将气体。
夹渣和缩松转移到该处,改善压铸件厚壁处的质量。
(5)溢流槽应开设在金属液昨晚充填的地方,以改善模具的热平衡状态和充填排气条件。
(6)溢流槽应的开设应防止压铸件的变形,并要求不影响压铸件的外观。
在排溢系统设计,因为此铸件是中心浇口浇注,浇注是有利于排气和充填,所以只需在分型面设置排气在浇注的槽,这样便可充满。
溢流槽可不设,在试模的时候如出现因涡流引起的缺陷时,或者是出现逐渐末段出现收缩变形可增设溢流槽,具体位置与尺寸如(图5)。
(图5)溢流槽
4压铸模结构设计
4.1压铸机的选择
合理的选择压铸机,设计压铸模时,应熟悉压铸机的特性和技术规格,通过必要的设计计算,合理的选择压铸机。
计算胀型力:
锁模力是表示压铸机最基本参数,其作用是克服压铸充填时的胀型力,使模具分型面不致张开,故设计压铸模时,首先确定胀型力的大小来选择压铸机,当压铸机的锁模力大于胀行力,则可认为该压铸机可以使用。
锁模力和胀型力的关系式见式
(1):
…………………………………………
(1)
——压铸时的反压力;
——作用与滑块楔紧面上的法向反压力;
——安全系数。
反压力的计算:
=
——铸件总投影面积
P——压射比压
4.1.1确定模具分型面上铸件的总投影面积
投影面积见公式
(2)
ΣF=F铸+F浇+F余+F溢(厘米2)……………………………………………….
(2)
F铸——铸件在分型面上的投影面积;
F浇——浇道内浇口在分型面上的投影面积;
F余——余料在分型面上的投影面积;
F溢——溢流槽在分型面上的投影面积。
4.1.2确定压射比压
选450~600公斤/厘米2此件选用压射比压为500公斤/厘米2
根据要求选择J1113A型卧室冷室压铸机。
压室为D=40mm
4.2型腔和型芯尺寸的设计
型腔尺寸计算见公式(3):
Y+a=(Y0+KY0-n△)+a…………………………………(3)
型芯尺寸计算见公式(4):
Y-a=(Y0+KY0+n△)-a……………………………….(4)
Y0——铸件的公称尺寸;
n——补偿和磨损系数。
取n=0.7;
△——铸件偏差;
(如表1)
a——模具成型部分的制造偏差;
K——压铸件的计算收缩率。
(如表2)
表1按铸件公差所推荐的模具制造公差(GB6级)
公称尺寸
1~3
3~6
6~10
10~18
18~30
30~50
50~80
△
0.060
0.080
0.100
0.120
0.140
0.170
0.200
a
0.012
0.016
0.020
0.024
0.028
0.034
0.040
表2铸件计算收缩率推荐值
收缩条件
阻碍收缩
混合收缩
自由收缩
计算收缩率(%)
铝合金
0.4~0.6
0.6~0.8
0.8~1.0
型腔成型尺寸计算:
(单位:
mm)
(图6)铸件成型尺寸标号
型腔尺寸
1、77+0.200→77.32+0.040
2、27+0.140→27.06+0.028
3、14+0.120→14.00+0.024
4、12+0.120→11.99+0.024
型腔深度尺寸
5、13+0.120→12.99+0.024
6、7+0..100→6.97+0.020
7、6+0.100→5.97+0.020
型芯尺寸
8、73-0.200→73.58-0.040
9、9-0.100→9.06-0.020
10、5.5-0.080→5.59-0.016
11、23.5-0.140→23.74-0.028
型芯高度尺寸
12、3.5-0.080→3.58-0.016
13、6-0.100→6.12+0.020
4.3镶块、型芯、模板的设计
4.3.1镶块的设计
为了节约贵重金属,所以在与金属液接触的部分制作成镶块,型芯,型腔按照上述尺寸才用H13制造,浇道与金属液接触部分也有H13制作成镶块。
(图7)镶块尺寸
如(图7)所示,具体尺寸如下:
h=30C=3.5
H=8H2=20
4.3.2模板的设计
模板设计是要合理,能使模具制造出来安装在所选的压铸机上。
并且要满足:
H行程≥H1+H2+b+
H行程压铸机开模行程;
H1动模零件高度;
H2定模零件高度;
b铸件浇道总厚度;
a取件时铸件与动、定模之间的最小距离。
1)套板尺寸:
套板的壁厚根据镶块的尺寸来确定,取套板的壁厚为75mm
2)动模支撑板厚:
选择20mm
3)推杆固定板的尺寸:
根据压铸机的型号选,厚为20(单位:
4)模座的设计:
①定模座板:
根据套板尺寸选为(单位:
②动模垫块与座板:
具体尺寸如(图9)所示
(图9)积木式模座
4.4导柱、导套的设计
尺寸如(图10)所示
(图10)导柱与导套
4.5推出机构、复位机构的设计
根据零件的具体结构,选择推杆推出方式为推杆推出,推杆的总数为5。
推杆形式