衬筒注塑模具设计说明书塑料模具设计及制造课程设计大学论文Word文档格式.docx
《衬筒注塑模具设计说明书塑料模具设计及制造课程设计大学论文Word文档格式.docx》由会员分享,可在线阅读,更多相关《衬筒注塑模具设计说明书塑料模具设计及制造课程设计大学论文Word文档格式.docx(19页珍藏版)》请在冰豆网上搜索。
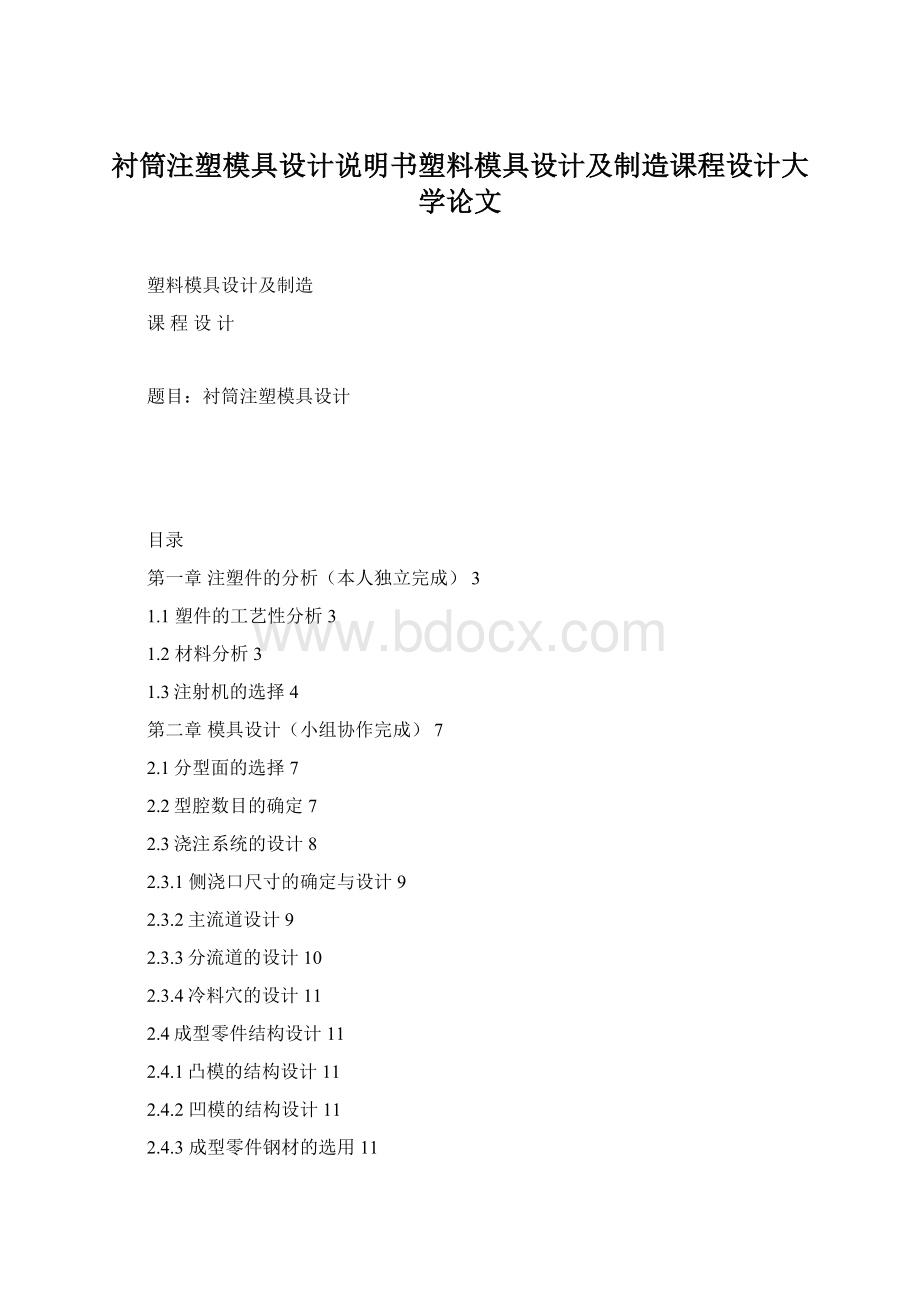
2.4.3成型零件钢材的选用11
2.4.4模具型腔壁厚的确定11
2.4.5成型零件的尺寸计算11
2.4.6型腔底板厚度的尺寸计算14
2.5导向机构的设计14
2.6推出方式的确定15
2.7模架的选用16
第三章装配图的绘制和注塑机校核17
3.1装配图的绘制(本人独立完成)17
3.2注塑机校核(小组协作完成)18
3.2.1最大注塑量的校核18
3.2.2锁模力的校核18
3.2.3模具闭合高度的校核19
3.2.4模具安装尺寸的校核19
3.2.5模具开模行程的校核19
总结20
参考文献20
第一章注塑件的分析
1.1塑件的工艺性分析
本文设计的是衬筒注塑模,衬筒零件图见图1-1,设计要求为:
1.材料:
PA1010
2.收缩率:
0.4%-0.8%
3.外观要求:
光滑,无明显制件缺陷(如缩痕、气泡、翘曲)。
4.生产批量:
大批量
图1-1衬筒零件图
1.2材料分析
PA1010塑胶原料熔程较窄,一般为3~4℃。
熔融流动性较好。
适合注射成型、挤出成型和吹塑成型。
PA1010(尼龙1010)塑料是半透明、轻而硬、表面光亮的结晶形白色或微黄色颗粒,相对密度和吸水性比尼龙6和尼龙66低,机械强度高,冲击韧性、耐磨性和自润滑性好,耐寒性比尼龙6好,熔体流动性好,易于成型加工,但熔体温度范围较窄,高于100℃时长期与氧接触会逐渐呈现黄褐色,且机械强度下降,熔融太时与氧接触极易引起热氧化降解。
PA1010(尼龙1010)塑料还具有较好的电气绝缘性和化学稳定性,无毒。
不溶于大部分非极性溶剂,如烃、脂类、低级醇等,但溶解于强极性溶剂,如苯酚、浓硫酸、甲酸、水合三氯乙醛等,耐霉菌、细菌和虫蛀。
1.3注射机的选择
注塑机的主要参数有公称注射量,注射压力,注射速度,塑化能力,锁模力,合模装置的基本尺寸,开合模速度,空循环时间等。
这些参数是设计,制造,购买和使用注塑机的主要依据。
1.公称注塑量。
指在对空注射的情况下,注射螺杆或柱塞做一次最大注射行程时,注射装置所能达到的最大注射量,反映了注塑机的加工能力。
2.注射压力。
为了克服熔料流经喷嘴,浇道和型腔时的流动阻力,螺杆(或柱塞)对熔料必须施加足够的压力,我们将这种压力称为注射压力。
3.注射速率。
为了使熔料及时充满型腔,除了必须有足够的注射压力外,熔料还必须有一定的流动速率,描述这一参数的为注射速率或注射时间或注射速度。
表1.1所示为注射量与注射时间的关系。
表1.1注射量与注射时间的关系
注射量/CM125250500100020004000600010000
注射速率/CM/S125200333570890133016002000
注射时间/S11.251.51.752.2533.755
4.塑化能力;
单位时间内所能塑化的物料量。
塑化能力应与注塑机的整个成型周期配合协调,若塑化能力高而机器的空循环时间长,则不能发挥塑化装置的能力,反之则会加长成型周期。
5.锁模力;
注塑机的合模机构对模具所能施加的最大夹紧力,在此力的作用下模具不应被熔融的塑料所顶开。
6.合模装置的基本尺寸;
包括模板尺寸,拉杆空间,模板间最大开距,动模板的行程,模具最大厚度与最小厚度等,这些参数规定了机器加工制件所使用的模具尺寸范围。
7.开合模速度;
为使模具闭合时平稳,以及开模,推出制件时不使塑料制件损坏,要求模板在整个行程中的速度要合理,即合模时从快到慢,开模时由慢到快在到停。
8.空循环时间;
在没有塑化,注射保压,冷却,取出制件等动作的情况下,完成一次循环所需的时间。
选择注射机
(1)由公称注射量选定注射机
计算塑件体积和质量
塑件的体积
V=45176㎜³
计算塑件的质量
查相关手册得ABS的密度为1.16g/㎝³
则塑件的质量为m=45176㎜³
×
10-3×
1.16g/㎝³
≈52g
流道凝料V’=0.2V(流道凝料的体积(质量)是个未知数,根据手册取0.2V来估算,塑件越大则比例可以取的越小);
单个产品实际注射量为:
V实=1.2V=1.2×
45.176=54.2cm;
由于客户要求一模2腔以及根据书本上所说:
实际注射量应小于0.8倍公称注射量原则,即:
0.8V公≧V实×
2
V公=V实×
2/0.8
=135.5cm3
(2)由锁模力选定注射机
FF=A·
P
=2×
·
P
=2×
3.14×
26²
90≈191(KN)
P型腔压力,取P=90MP;
D取的是塑件的平均直径,D=52mm;
结合上面两项的计算以及模具的总高度H=298mm,初步确定注塑机为XS-ZY-125(A)型注射机,
其参数如下:
额定注射量:
192
螺杆直径:
42mm
注射压力:
150Mpa
锁模力:
900KN
模板行程:
300mm
模具最大厚度:
300mm
模具最小厚度:
200mm
模板尺寸:
330×
440mm
拉杆空间:
360×
360mm
定位孔直径:
100mm
合模方式:
液压—机械
第二章模具设计
2.1分型面的选择
选择分型面时,应有以下几项基本原则:
5.分型面应选在塑件外形最大轮廓处
6.分型面的选择应有利于塑件的顺利脱模
7.分型面的选择应保证塑件的精度要求
8.分型面的选择应满足塑件的外观面的要求
9.分型面的选择应要便于模具的加工制造
10.分型面的选择应有利于排气
该塑件为衬筒,外形表面质量要求一般。
在选择分型面时,根据分型面的选择原则,考虑不影响塑件的外观质量,便于清除毛刺和飞边,有利于排除模具型腔内的气体,分模后塑件留在动模一侧,便于取出塑件等因素,分型面应选择塑件外轮廓最大处。
如图2-1所示。
图2-1分型面
2.2型腔数目的确定
注塑模的型腔数目,可以是一模一腔,也可以是一模多腔,在型腔数目的确定时主要考虑以下几个有关因素:
(1)塑件的尺寸精度;
(2)模具制造成本;
(3)注塑成型的生产效益;
(4)模具制造难度。
在保证产品的精度要求前提下,冷却系统要便于设置,同时冷却效果要好。
又因为该产品大批量生产,所以本模具选择一模2腔。
型腔的分布:
由于型腔的排布与浇注系统密切相关的,所以在模具设计时应该综合加以考虑,型腔的排布应使每个型腔都能通过浇注系统从总压力中均等地分得所需要的足够压力,以保证塑料熔体能同时均匀的充填每个型腔。
该模具中2个产品平衡布局如图所示:
图2-2型腔布局
2.3浇注系统的设计
注塑模的浇注系统是指模具中从注塑机喷嘴开始到型腔入口为止的塑料熔体的流动通道,它由主流道,分流道,冷料穴和浇口组成。
它向型腔中的传质,传热,传压情况决定着塑件的内在和外表质量,它的布置和安排影响着成型的难易程度和模具设计及加工的复杂程度,所以浇注系统是模具设计中的主要内容之一。
对浇注系统进行设计时,一般应遵循如下基本原则:
1.了解塑料的成型性能。
2.尽量避免或减少产生熔接痕
3.有利于型腔中的气体排出
4.防止型心的变形和嵌件的位移
5.尽量采用较短的流程充填型腔
6.流动距离比和流动面积比的校核
2.3.1侧浇口尺寸的确定与设计
由于该塑件外观要求一般,浇口位置和大小以不影响塑件的外观质量为前提,同时,也应尽可能使模具结构更简单。
根据对塑件的分析,并结合确定分型面位置,选择矩形浇口进料方式,进料位置设计在塑件边缘。
具体尺寸如图所示:
2.3.2主流道设计
主流道是连接注塑机的喷嘴与分流道的一段通道,通常和注塑机的喷嘴在同一轴线上,断面为圆形,有一定的锥度,目的是便于冷料的脱模,同时也改善料流的速度,因为要和注塑机相配,所以其尺寸与注塑机有关。
将主流道设计成圆锥形,其斜度为2°
,同时为了使熔料顺利进入分流道,在主流道端设计r=16mm的圆弧过渡。
主流道衬套采用可拆卸更换的浇口套,浇口套的形状及尺寸设计采用推荐尺寸的常用浇口套;
为了能与塑料注射机的定位圈相配合,采用外加定位环的方式,这样不仅减小了浇口套的总体尺寸,还避免了浇口套在使用中的磨损。
见图2-3所示为浇口套的设计尺寸。
图2-3浇口套
2.3.3分流道的设计
分流道的形状及尺寸,应根据塑件的体积,壁厚,形状的复杂程度,注射速率,分流道长度等因素来确定。
该模具是一模2腔,分流道平衡布局。
模具的浇注系统如图2-4所示
图2-4浇注系统
2.3.4冷料穴的设计
冷料穴是为了防止冷料进入浇注系统的流道和型腔,从而影响注塑成型和塑料件质量而开设的容纳注射间隔所产生的冷料井穴,本设计中冷料穴开设在主流道和分流道的交界处。
图2-5冷料穴示意图
2.4成型零件结构设计
2.4.1凸模的结构设计
模具的型芯采用组合式。
组合式的型芯是和模板分开的,容易更换清洗,使用中不易发生变形。
2.4.2凹模的结构设计
型腔采用整体式该塑件尺寸适中,最大处也只有Φ52mm,型腔加工容易实现。
2.4.3成型零件钢材的选用
根据所成型塑料的种类、制品的形状、尺寸精度、制品的外观质量及使用要求、生产批量大小等,兼顾材料的切削、抛光、焊接、蚀纹、变形、耐磨等各项性能,同时考虑经济性以及模具的制造条件和加工方法,以选用不同类型的钢材
本套模具成型零件采用CrWMn,热处理HRC50-55.
2.4.4模具型腔壁厚的确定
采用经验数据法,直接查阅设计手册中的有关表格,得该型腔的推荐壁厚为30-50mm,这样模具的冷却水道容易起到作用。
2.4.5成型零件的尺寸计算
该塑件的材料是一种收缩范围较大的塑料,因此成型零件的尺寸均按平均值法计算。
查手册得ABS的收缩率为0.4%~0.8%,故平均收缩率为0.6%。
成型零件的工作尺寸是指凹模和凸模直接构成塑件的尺寸,通常包括凹模和凸模的径向尺寸(包括零件的长和宽)、凹模和凸模的高度尺寸及位置尺寸,故零件的工作尺寸计算主要是凹模和凸模的尺寸计算。
1、产生偏差的原因:
①塑料的成型收缩
成型收缩引起制品产生尺寸偏差的原因有:
预定收缩率(设计算成型零部件工作尺寸所用的收缩率)与制品实际收缩率之间的误差;
成型过程中,收缩率可能在其最大值和最小值之间发生的波动。
σs=(Smax-Smin)×
制品尺寸
σs:
成型收缩率波动引起的制品的尺寸偏差。
Smax、Smin:
分别是制品的最大收缩率和制品的最小收缩率。
②成型零部件的模具制造偏差
工作尺寸的制造偏差包括模具的加工偏差和装配偏差。
加工偏差就是模具在制造过程中所产生的尺寸偏差,装配偏差主要是模具在分型面上的合模间隙以及组合模具的配合偏差。
③成型零部件的磨损
成型零部件的摩损相对于精度要求不高的大型零部件来说,可以不考虑,但对于精度要求较高的小型零部件,就必须要对其进行考虑。
2、该塑件的材料是一种收缩范围较大的塑料,因此成型零件的尺