机械制造基础简答题答案Word文档下载推荐.docx
《机械制造基础简答题答案Word文档下载推荐.docx》由会员分享,可在线阅读,更多相关《机械制造基础简答题答案Word文档下载推荐.docx(8页珍藏版)》请在冰豆网上搜索。
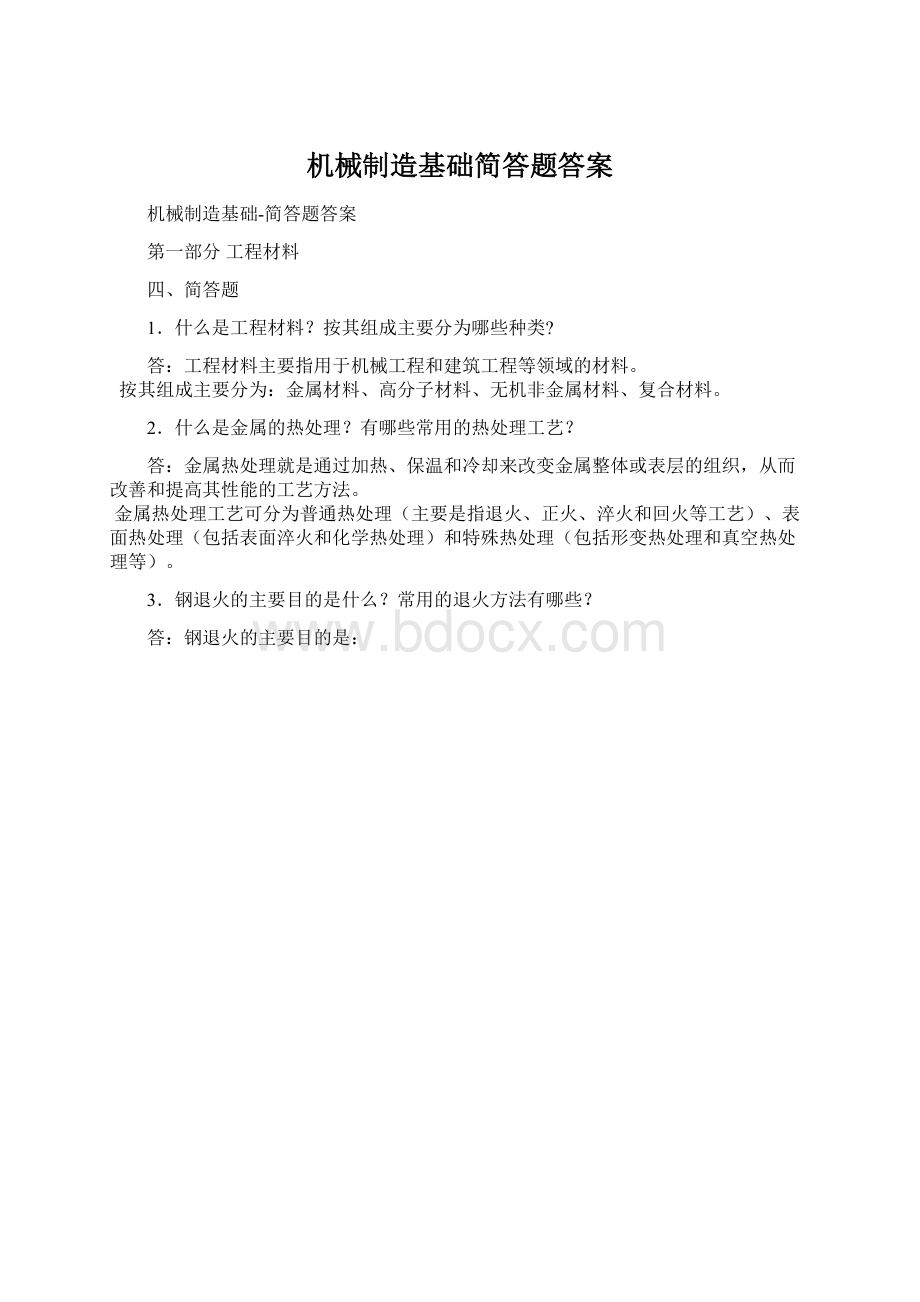
由于回火后钢的力学性能取决于回火后的组织与结构,而回火后的组织与结构是由回火温度而不是由冷却速度决定的。
7.回火的目的是什么?
常用的回火操作有哪些?
试指出各种回火操作得到的组织、性能及应用范围。
回火的目的是:
①消除淬火时产生的残余内应力;
②提高材料的塑性和韧性,获得良好的综合力学性能;
③稳定组织和工件尺寸。
常用的回火方法有以下三种:
(1)低温回火(250℃以下)
组织:
回火组织为回火马氏体。
性能:
基本上保持了淬火后的高硬度(一般为58~64HRC)和高耐磨性。
应用:
主要用于高碳工具钢、模具、滚动轴承、渗碳、表面淬火的零件及低碳马氏体钢和中碳低合金超高强度钢。
(2)中温回火(350~500℃)
回火组织为回火屈氏体。
回火屈氏体的硬度一般为35~45HRC,具有较高的弹性极限和屈服极限。
它们的屈强比(σs/σb)较高,一般能达到0.7以上,同时也具有一定的韧性。
主要用于各种弹性元件。
(3)高温回火(500~650℃)
回火组织为回火索氏体。
其综合力学性能优良,在保持较高强度的同时,具有良好的塑性和韧性。
硬度一般为25~35HRC。
广泛用于综合力学性能要求高的各种机械零件,例如轴、齿轮坯、连杆、高强度螺栓等。
8.什么是调质处理?
调质的主要目的是什么?
钢在调质后是什么组织?
通常在生产中将各种钢件淬火及高温回火的复合热处理工艺称为调质处理。
调质的主要目的是提高零件的综合机械性能。
钢在调质后的组织是:
回火索氏体
9.说明下列零件毛坯进行正火的主要目的及正火后的组织:
(l)20钢锻造的齿轮毛坯;
(2)45钢锻造用的机床主轴毛坯;
(3)T12轧制而成的锉刀毛坯(组织为网状Fe3CⅡ和片状珠光体)。
(1)20钢齿轮正火后的组织为:
S+F
目的:
提高硬度,避免粘刀,改善切削加工性。
(2)45钢锻造用的机床主轴毛坯正火后的组织为:
(正火代替完全退火,节约时间和能源)细化晶粒,改善组织,改善机械性能。
(3)T12钢轧制而成的锉刀毛坯正火前的组织为网状Fe3CⅡ和片状珠光体,正火后的组织为:
S+Fe3CⅡ
细化晶粒,改善组织,减少或消除网状渗碳体,为后续工序(球化处理)做好组织准备。
10.指出下列工件的淬火及回火温度,并说明其回火后获得的组织及其大致硬度。
(l)45钢小轴(要求综合性能);
(2)60弹簧钢;
(3)T12锉刀。
工件
淬火温度
回火温度
回火后的组织
回火后的硬度
45钢小轴
Ac3+30~50℃
500~650℃
S回
HRC25~35
60弹簧钢
350~500℃
T回
HRC45~50
T12锉刀
Ac1+30~50℃
150~250℃
M回
HRC55~65
11.45钢轴的生产工艺过程如下,试说明其中各热处理工序的目的。
锻造正火粗加工调质精加工
局部表面淬火+低温回火磨削
正火:
消除锻造时产生的内应力或调整材料的硬度,使其便于切削加工。
调质处理:
提高材料的综合机械性能。
局部表面淬火+低温回火:
局部表面淬火是为了局部提高材料表面的硬度,从而提高其耐磨性;
低温回火是为了消除残余内应力,防止工件变形开裂,同时保持材料淬火后的高硬度。
12.用45钢制车床主轴,要求轴颈部位硬度为56~58HRC,其余地方为20~24HRC,其加工工艺路线为:
锻造→正火→机械加工→轴颈表面淬火→低温回火→磨加工。
请说明以下问题。
(1)正火的目的及大致热处理工艺参数。
(2)表面淬火及低温回火的目的。
(3)使用状态下轴颈及其他部位的组织。
答:
(1)主轴正火的目的是为了细化晶粒,改善组织,消除内应力,同时,改善切削加工性,保证主轴心部的力学性能。
加热到850℃,保温一定的时间,出炉后在空气中冷却。
(2)表面淬火的目的是为了获得马氏体组织,提高主轴的硬度,改善耐磨性;
低温回火的目的是为了消除淬火应力,防止变形和开裂,同时,保持高的淬火硬度。
(3)使用状态下轴颈表面的组织是回火马氏体M回,轴颈心部的组织是回火索氏体和铁素体S回+F,其他部位的组织是索氏体和铁素体S+F。
15.试分析下列零件的工作条件和主要力学性能要求,选择相应的材料(写出2—3种材料的牌号):
(1)弹簧
(2)汽车变速箱小齿轮(3)机床传动用大齿轮
(4)轻载载货汽车发动机曲轴(5)钳工用的锉刀(6)高速切削刀具
(7)机床主轴(8)机床床身
(1)弹簧:
60、65、70、65Mn、60Si2MnA
(2)汽车变速箱小齿轮:
40、45、40Cr、40Mn、20Cr、20CrMnTi、35CrMo
(3)机床传动用大齿轮:
35、45、50、HT200、HT250、HT300、HT350
(4)轻载载货汽车发动机曲轴:
40Cr、35CrMo、QT600-3、QT700-2、QT800-2
(5)钳工用的锉刀:
T10、T11、T12、T13
(6)高速切削刀具:
W18Cr4V、W6Mo5Cr4V2
(7)机床主轴:
45、40Cr、35CrMo
(8)机床床身:
HT200、HT250、HT200、HT350
第十三章切削加工基础知识
1、何谓切削运动?
刀具与工件之间的相对运动称为切削运动。
它包括主运动和进给运动。
主运动是切下切屑所需的最基本的运动。
与进给运动相比,它的速度高、消耗机床功率多。
主运动一般只有一个。
进给运动是多余材料不断被投入切削,从而加工出完整表面所需的运动。
进给运动可以有一个或几个。
主运动和进给运动的适当配合,就可对工件不同的表面进行加工。
2、试述刀具材料应具备的性能。
刀具材料应具备的性能为:
1)高的硬度。
刀具材料的硬度必须高于工件材料的硬度。
在常温下,刀具材料的硬度一般应在HRC60以上。
2)足够的强度和韧性。
以便承受切削力和切削时产生的振动,防止刀具脆性断裂和崩刃。
3)高的耐磨性。
即抵抗磨损的能力。
一般情况下,刀具材料硬度越高,耐磨性越好。
4)高的耐热性。
指刀具材料在高温下仍能保持硬度、强度、韧性和耐磨等性能。
5)良好的工艺性和经济性。
为便于刀具本身的制造,刀具材料应具有好的切削性能、磨削性能、焊接性能及热处理性能等,而且要追求高的性能价格比。
3、切削过程中有哪些物理现象?
试述积屑瘤的产生对切削加工的影响。
切削过程中的物理现象有积屑瘤和加工硬化现象。
积屑瘤的存在有利也有弊。
积屑瘤的不稳定使切削深度和厚度不断发生变化,影响加工精度,并引起切削力的变化,产生振动、冲击,而且脱落的积屑瘤碎片粘附在已加工表面上,使加工表面粗糙。
因此,在精加工过程中,应采取改变切削速度、选用适当的切削液等措施避免积屑瘤的产生。
由于积屑瘤的硬度高于刀具,可以代替切削刃进行切削,起到保护刀具的作用,同时积屑瘤的存在,增大了刀具的实际工作前角,使切削过程轻快。
因此,粗加工时积屑瘤的存在是有利的。
4、简述合理选用切削用量三要素的基本原则。
选择切削用量的原则是:
在保证加工质量,降低成本和提高生产率的前提下,使ap、f、v的乘积最大,即使基本工艺时间最短。
粗加工时,要尽可能提高金属切除率,同时还要保证规定的刀具耐用度。
在机床功率足够时,应尽可能选取大的背吃刀量,除留下精加工的余量外,最好一次走刀切除全部粗加工的余量。
其次,根据工艺系统的刚度,按工艺装备及技术条件选择大的进给量。
最后再根据刀具耐用度的要求,针对不同的刀具材料和工件材料,选择合适的切削速度v,以保证在一定刀具耐用度条件下达到最高生产率。
精加工时,首先应保证零件的加工精度和表面质量,同时还要保证必要的刀具耐用度和生产率。
精加工往往采用逐渐减小背吃刀量的方法来逐步提高加工精度。
为了既可保证加工质量,又可提高生产率,精加工时常采用专门的精加工刀具并选用较小的背吃刀量和进给量,以及较高的切削速度将工件加工到最终的质量要求。
第十四章零件表面的加工方法
1、加工细长轴时,容易产生腰鼓形(中间大、两头小),试分析产生的原因及应采取的措施。
加工细长轴时,由于工件径向刚性较差,在切削受力的过程中,引起较大的径向变形,使中间部位的切削深度较两端小,从而产生腰鼓形变形。
为减小腰鼓形变形,可采用较大的主偏角,减小切削深度,采用中心架、跟刀架等方法。
3、简述钻孔时,产生“引偏”的原因及减小“引偏”的措施。
钻孔时,产生“引偏”是由于横刃较长又有较大负前角,使钻头很难定心;
钻头比较细长,且有两条宽而深的容屑槽,使钻头刚性很差;
钻头只有两条很窄的螺旋棱带与孔壁接触,导向性也很差;
由于横刃的存在,使钻孔时轴向抗力增大。
因此,钻头在开始切削时就容易引偏,切入以后易产生弯曲变形,致使钻头偏离原轴线。
钻头的引偏将使加工后的孔出现孔轴线的歪斜、孔径扩大和孔失圆等现象。
减小“引偏”的措施包括预钻锥形定心坑;
采用钻套为钻头导向;
刃磨时,尽量将钻头的两个半锋角和两条主切削刃磨得完全相等。
6、何为顺铣和逆铣?
试分析一般采用逆铣而很少采用顺铣的原因。
周铣铣平面又分为逆铣和顺铣两种方法。
当铣刀和工件接触部分的旋转方向与工件的进给方向相反时称为逆铣;
当铣刀和工件接触部分的旋转方向与工件的进给方向相同时称为顺铣。
顺铣忽大忽小的水平分力FH的方向与工作台的进给方向相同,由于工作台进给丝杠与固定螺母之间一般都存在间隙,当水平分力FH值较小时,丝杠与螺母之间的间隙位于右侧,而当水平分力FH值足够大时,就会将工件连同丝杠一起向右拖动,使丝杠与螺母之间的间隙位于左侧。
在这种情况下,水平分力FH的大小变化会使工作台忽左忽右来回窜动,造成切削过程不平稳,严重时会打刀甚至损坏机床。
逆铣时,水平分立FH与进给方向相反,因此,工作台进给丝杠与螺母之间在切削过程中始终保持一侧紧密接触,工作台不会窜动,切削过程平稳。
铣床工作台的进给丝杆和螺母无消除间隙装置时,一般采用逆铣。
8、磨削加工为什么可以获得较高的精度及较低的粗糙度?
由于磨粒的刃口半径ρ小,能切下一层极薄的材料;
又由于砂轮表面上的磨粒多,磨削速度高(30~35m/s),同时参加切削的磨粒很多,在工件表面上形成细小而致密的网络磨痕;
再加上磨床本身的精度高、液压传动平稳和微量进给机构,因此,磨削的加工精度高(IT8~IT5)、表面粗糙度小(Ra=1.6~0.2μm)。
9、什么是特种加工?
它与传统的切削加工相比有何特点?
特种加工不是采用常规的刀具或磨具对工件进行切削加工的工艺方法,而是利用电能、光能、化学能、声能、磁能等物理、化学能量或几种复合形式直接施加在被加工的部位,从而使工件改变形状、去除材料、改变性能等。
与传统的切削加工相比