典型垫片冲压模具说明书Word文档格式.docx
《典型垫片冲压模具说明书Word文档格式.docx》由会员分享,可在线阅读,更多相关《典型垫片冲压模具说明书Word文档格式.docx(13页珍藏版)》请在冰豆网上搜索。
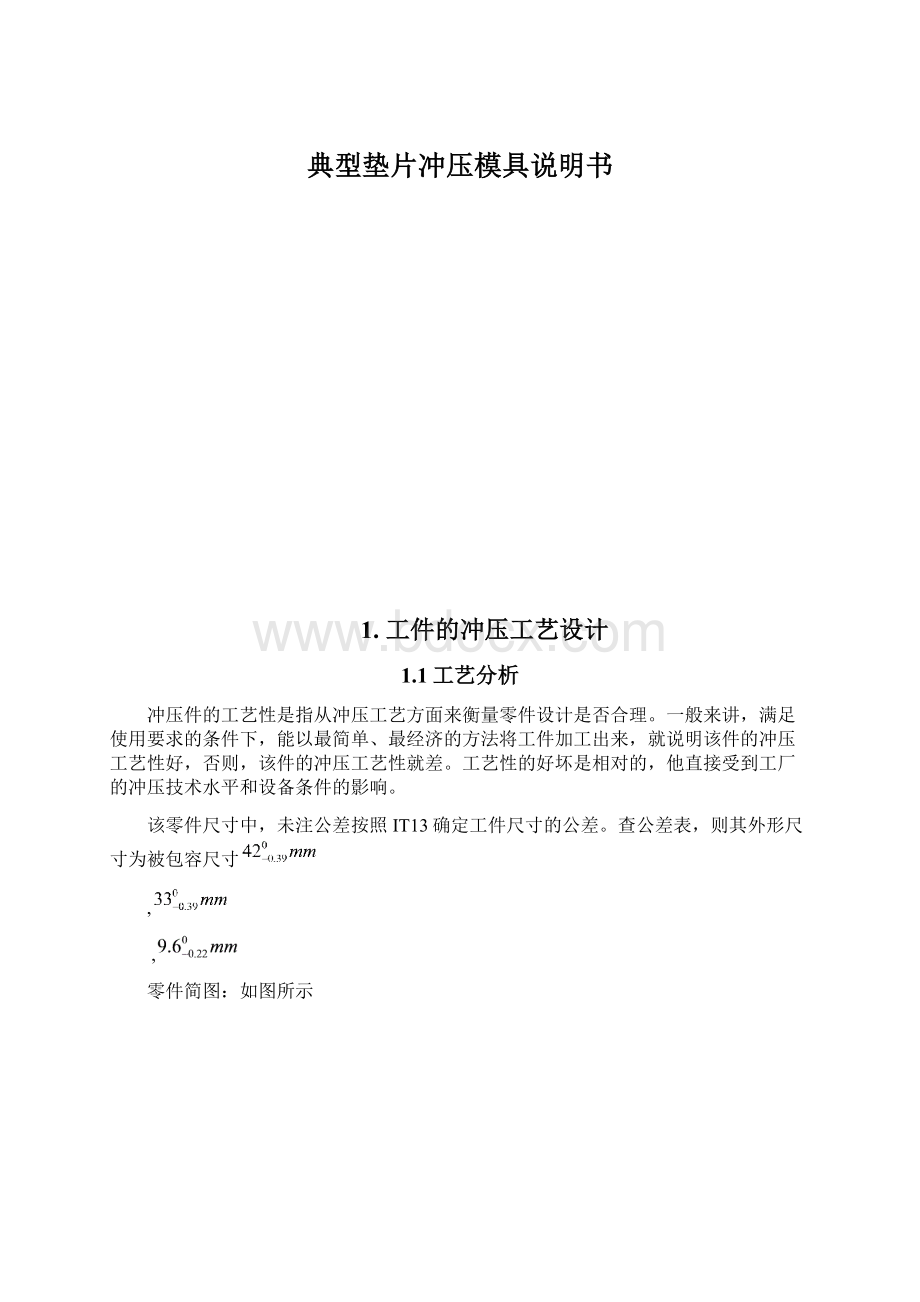
确定工艺方案就是确定冲压件的工艺路线,主要包括冲压工序数、工序的组合和顺序等。
确定合理的冲裁工艺方案应对不同的工艺方案进行全面的分析与研究。
在选择工艺时,一般要考虑模具的结构形式,比较其综合的经济技术效果,选择一个合理的冲压工艺方案。
在确定冲压件的工艺路线时,应主要考虑以下几个方面:
冲压零件的几何形状、尺寸大小、精度等级、生产批量、加工零件时操作的难易程度、模具的加工成本及时间等。
经分析该零件属于大批量生产,形状简单,工艺性较好、冲压件尺寸精度较高。
冲压该零件需要的基本工序有落料和冲孔。
方案一:
先落料,再冲孔,采用单工序模生产。
方案二:
落料和冲孔复合冲压,采用复合模生产。
方案三:
冲孔落料连续冲压,采用级进模(连续模)生产。
方案一单工序模具结构简单,但需要两道工序、两套模具才能完成零件的加工,生产效率较低,难以满足零件大批量生产的需求。
由于零件结构简单,为提高生产效率,主要应采用复合冲裁或级进冲裁方式。
方案二复合模能在压力机一次行程内,完成落料、冲孔等多道工序,所冲压的工件精度较高,不受送料误差影响,内外形相对位置重复性好,由于压料冲裁的同时得到了校平,冲件平直且有较好的剪切断面。
方案三级进模可以加工形状复杂、宽度很小的异形冲裁件,且可冲裁比较厚的零件,但级进模冲裁受压力机工作台面尺寸与工序数的限制,冲裁件尺寸不宜太大。
另外级进模冲裁中、小型零件时零件平面度不高,高质量工件需校平。
根据冲压模工艺原理,结合该零件结构的特点,通过对比以上三种方案,采用复合模结构简单实用,冲压工艺过程稳定可靠,比较适合该零件了生产制造。
1.3工艺计算
1.3.1排样及确定条料尺寸
(1)调料宽度
条料宽度B用式(1-1)进行计算
B=(L+2
+C)(1-1)
式中,L是制件长度(mm);
是是工件与边缘的搭边值
(mm);
C是条料与导料板之间的间隙(mm)。
查表得,材料厚度t=2mm自动送料时,工件与工件之间的搭边值
=3mm,工件与边缘之间的搭边值
=2mm。
查表得条料宽度
B<
100mm时,送料间隙取C=0.5mm。
零件外形为圆形,可以采用单排、交叉双排或多排;
考虑到零件为中等批量生产,如果采用交叉双排或多排,则模具尺寸和结构就会相应增大,从而增加模具生产成本,所以本设计决定采用单排结构即直排(如图所示)。
由于每张钢板的尺寸都是长度为2000mm,宽度为1000mm。
每张钢板剪裁1000/48.5
20条;
每条能冲裁(2000-2
2)/63
31.所以每张钢板能生产20
31=620个零件。
考虑定位公差及裁剪公差后,条料宽度按式(1-2)计算
(1-2)
式中,
是条料宽度偏差(mm),查表得
=0.5
即
(2)步距
(3)材料利用率
式中,n是一个步距内冲裁件数目
A是冲裁面积(包括图形结构废料)
S是步距长度(mm)
B是调料宽度(mm)
取n=1,冲裁图形近似为平行四边形
求的其底边长约为54,高为44
则其面积
S=63mm,B=48.5mm
1.3.2冲压力计算及设备选择
(1)冲裁力的计算
落料及冲孔时的冲裁力按式(1-3)计算
(1-3)
式中,P是冲裁力(N);
L是冲裁周边长度(mm);
t是材料厚度(mm);
是材料的抗剪强度(MPa);
K是修正系数,一般取K=1.3。
由于
,所以式
(1-3)也常常表达为
(1-4)
其中,
是冲压材料的抗拉强度(MPa);
查表得,Q235钢的抗拉强度
=400MPa
落料所需冲裁力
冲孔所需冲裁力
(2)卸料力、顶件力、推料力的计算
从凸模上卸下箍着的材料所需的力称为卸料力;
逆冲裁方向将板料从凹模内顶出所需的力称为顶件力;
从凹模内向下推出制件或废料所需的力,称为推料力。
一般按以下公式计算
式中,F是冲裁力(N),
是卸料力系数,查表取
=0.04;
是顶件力系数,查表取
=0.06,n是塞在凹模内的制件或废料数量,n=h/t.
h为凹模直刃高度,取h=8,t为板厚,t=2,则n=8/2=4,
为推料力系数,查表取
=0.055。
经计算得
(3)总冲压力的计算
(4)压力中心的确定
、
是压力中心在X、Y轴上的坐标,
是各简单图形的压力中心在X轴、Y轴上的坐标与其冲裁周边长度乘积之和(
),
是各简单图形的冲裁周边长度之和(mm)。
可以看出零件在X、Y轴上方向上是对称的,因此压力中心必在零件的中心线上。
所以
.
即压力中心的位置(0,0)
(5)设备选择
经计算,总冲压力为374KN
则选取J23-40型开式可倾压力机
公称压力(KN):
400
最大闭合高度(mm):
330
立柱距离(mm):
340
工作台尺寸(mm):
460×
700
1.4凸模凹模凸凹模刃口及结构尺寸计算
1.4.1凸凹模刃口尺寸
模具采用复合模结构,计算刃口尺寸时宜采用尺寸转换法计算。
零件上包含三类尺寸:
落料尺寸
冲孔尺寸
位置尺寸
查得冲裁模刃口双间隙
mm,
mm。
(1)落料刃口尺寸计算
则取
其中x是为与冲裁件精度有关的系数,查表,取x=0.5
同理,对于尺寸
(2)冲孔刃口尺寸计算
则取
(3)位置尺寸
1.4.2落料凹模结构尺寸
(1)凹模壁厚C
凹模厚度H=Kb≧15mm
凹模壁厚C=(1.5~2)H≧30~40mm
式中,b是冲裁件的最大外形尺寸(mm),K是凹模厚度系数。
查表得K=0.40
则H=Kb=0.40×
40=16mm,取H=20mm;
C=(1.5~2)H=(1.5~2)×
20=24~32mm,取C=30mm
(2)凹模板外形尺寸
1.4.3冲孔凸模结构尺寸
冲孔凸模长度
查表5-27由d=24
查表得h=3mmD=25mm
D1=30mmL=50mm
1.4.4凸凹模结构尺寸
落料凸模和孔的凹模考虑到该副模具的结构和精度,及加工、装配方面等因素,可选用整体式凸凹模。
凸凹模高度
确定
mm
式中
—卸料板厚度,取
;
—凸凹模固定板厚度,
(0.6~0.8)
=(0.6~0.8)
12~16mm,取
mm
1.5其他模具零部件的选择
1.5.1模架
本例中采用后侧导柱模架
后侧导柱模架的特点是导向装置在后侧,横向和纵向送料都比较方便,但如有偏心载荷,压力机导向又不精确,就会造成上模偏斜,导向零件和凸、凹模都容易磨损,从而影响模具寿命,一般用于较小的冲模。
因为该制件压力中心在对称线上,其无偏心载荷,之间精度要求也不是很高且制件较小,所以由模具成本等因素考虑该副模具模架选用后侧导柱模架。
1.5.2凸模固定板
凸模固定板将凸模固定在模座上,其平面轮廓尺寸与凹模板外形尺寸相同,但还应考虑紧固螺钉及销钉的位置。
固定板的凸模安装孔与凸模采用过渡配合H7/m6、H7/n6,压装后将凸模端面与固定板一起磨平。
凸模固定板为圆形,厚度一般取凹模厚度的0.6~0.8倍,材料为Q235
14mm
2.装配图
3.小结
正向老师说得一样,模具设计的课程设计没有那么简单,你想照搬或者你想自己胡乱蒙两个数据上去是制作不出来的,因为你的每一个数据在模具装配中应用得到。
虽然种种困难我都已经克服,但是还是难免我有些疏忽和遗漏的地方。
完美总是可望而不可求的,不在同一个地方跌倒两次才是最重要的。
抱着这个心理我一步步走了过来,最终完成了我的任务。
4.参考文献
(1).王孝培.冲压手册.北京:
机械工业出版社,2000
(2).史铁梁.模具设计与指导.北京:
机械工业出版社,2006
(3).姜奎华.冲压工艺与模具设计.北京:
机械工业出版社,200
(4).丁松聚.冷冲模设计.北京:
(5).瞿平.飞机钣金成形原理与工艺.西安:
西北工业大学出版社。
2009