内径磨削的理论与实际操作Word格式.docx
《内径磨削的理论与实际操作Word格式.docx》由会员分享,可在线阅读,更多相关《内径磨削的理论与实际操作Word格式.docx(13页珍藏版)》请在冰豆网上搜索。
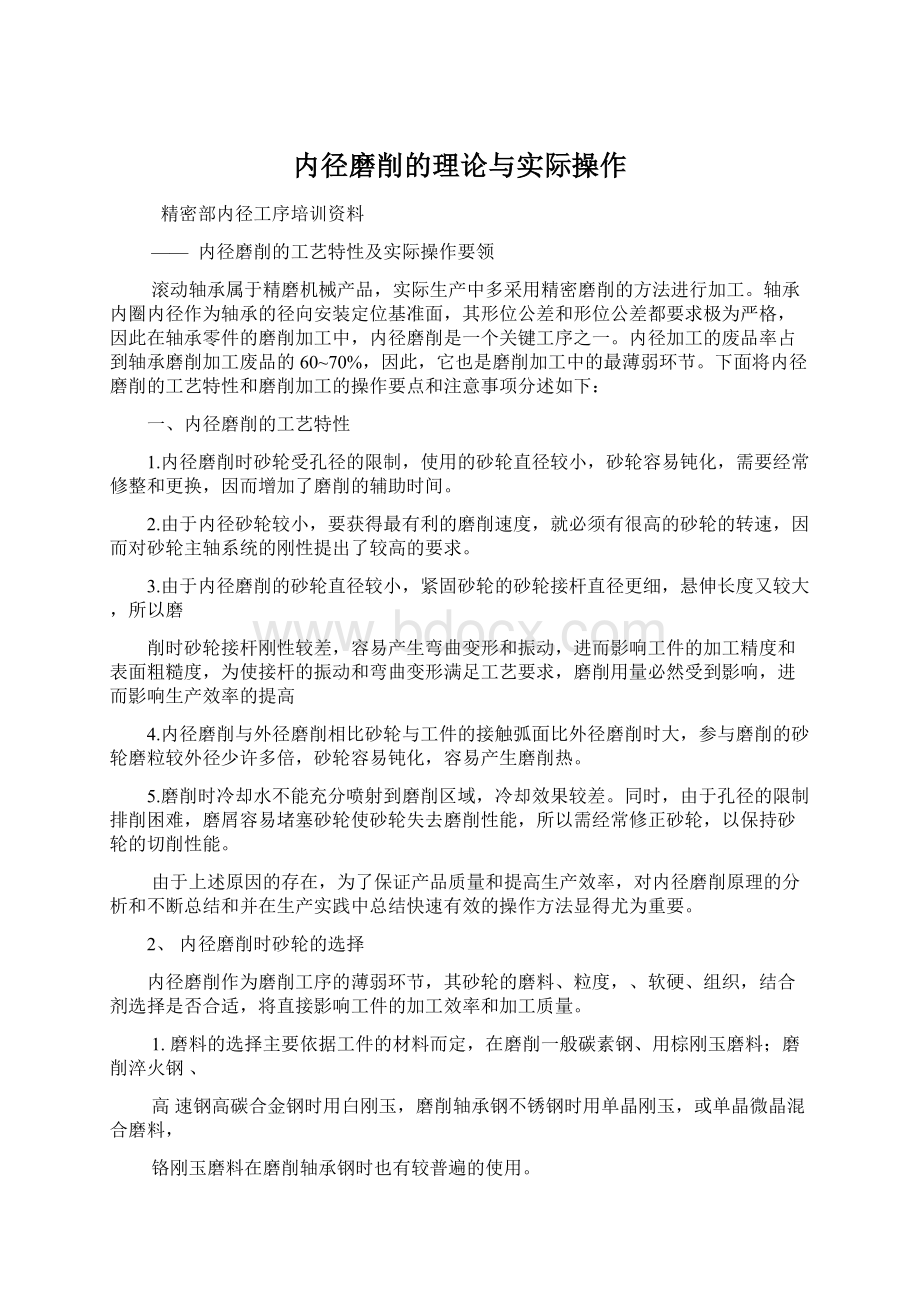
同时,由于孔径的限制排削困难,磨屑容易堵塞砂轮使砂轮失去磨削性能,所以需经常修正砂轮,以保持砂轮的切削性能。
由于上述原因的存在,为了保证产品质量和提高生产效率,对内径磨削原理的分析和不断总结和并在生产实践中总结快速有效的操作方法显得尤为重要。
2、内径磨削时砂轮的选择
内径磨削作为磨削工序的薄弱环节,其砂轮的磨料、粒度,、软硬、组织,结合剂选择是否合适,将直接影响工件的加工效率和加工质量。
1.磨料的选择主要依据工件的材料而定,在磨削一般碳素钢、用棕刚玉磨料;
磨削淬火钢、
高速钢高碳合金钢时用白刚玉,磨削轴承钢不锈钢时用单晶刚玉,或单晶微晶混合磨料,
铬刚玉磨料在磨削轴承钢时也有较普遍的使用。
2.砂轮粒度的选择,一般在材料相同的情况下粗磨时选择60~80粒度的砂轮,精磨时选择
80~120粒度的砂轮。
3.砂轮的软硬则依据材料的硬度及工件磨量的大小进行选择,对于磨量大、材料硬工件,
为避免烧伤和增加其自锐性能应选择砂轮的硬度稍软一些J或K级的硬度。
而对于被
磨削材料较软或磨量小的工件,可采用硬度稍硬的砂轮,K或L级硬度的砂轮。
4.砂轮的组织在磨削轴承内径时一般选择偏疏松8~10级的组织号,以利于容屑和散热。
5.结合剂方面一般选择陶瓷结合剂,以利于砂轮形成更多的空隙,改善内径加工磨削性能。
3、内径磨削对砂轮接长轴的要求
砂轮接长轴作为连接砂轮主轴和紧固砂轮、进而实现对工件加工的连接件,在磨削加工中的作用不可小视,其材料选择、结构设计,加工精度的好坏直接影响产品的加工质量及表面精度。
1.从工艺上要保证接长轴自身外圆与其中心线的同轴度,从而保证最低限度的旋转平衡性;
2.砂轮接杆圆柱面与电主轴圆柱孔紧密配合,以保证砂轮接杆与砂轮主轴的结合刚性和同
轴度;
3.为了提高砂轮接杆的刚性,其伸出磨头主轴外的杆体长度应在满足加工工艺的情况下尽量
粗而短。
杆身的长短取决于被磨削孔的长度,砂轮在孔端的伸出量。
同时还应满足工作台
在作往复运动时应保证磨头、接长轴、与机床的其他装置不碰撞。
4.接长轴的粗细由工被加工工件孔径的大小、砂轮质量大小及旋转时的离心力大小,还有其
悬出砂轮主轴的长度来决定。
在满足工艺要求的情况下应尽量是粗一些。
5.接长轴的材料可以选用中碳合金钢或中碳钢制造,并经调质处理,硬度在HRC38-52度之
间选择。
4、机床加工前一般准备和调整工作
1.确定要加工的工件型号、规格、抄写工艺卡片,校对本工序的工艺要求,确保准确无误。
2.领取标准件,和测量使用的仪表,根据标准件尺寸和工艺要求尺寸两者的差确定对表位置。
3.根据工件内外径尺寸大小,选用合适的磁极,并与螺钉固定牢固。
4.修磨磁极
换上修磨磁极专用的砂轮,或将磨削砂轮前端修内凹的蝶形,缓慢移动工作台和磨架使砂轮左端面接近磁极并与磁极呈圆弧的线状接触,使砂轮外径边缘悬出磁极外径边缘约2~3个毫米,将磨架上的螺钉与死挡块用螺钉顶死,调整磨架液压缸压力,使得磨架能保持缓慢移动。
伺服电机控制的工作台和磨架进给对待机床,使用电子手轮控制进给,并将速度放在较低的档位缓慢进给。
修磨磁极时要加水冷却,待火花均匀后光磨3到5分钟,当火花接近消失后快速退回磨架和工作台,停止砂轮、工件轴,关闭冷却水,观察磁极的修磨情况,磁极表面应平滑光整,砂轮花分布均匀,端面跳动不大于,说明吃惊已经修磨合格。
5..工件偏心的调整
根据工件外径的大小调整偏向量及上下支撑的夹角,偏心量一般在20~35um之间,支撑夹角水平支点在0到5度,下支撑在90到125度之间选取。
具体调整方法,将工件放置在磁极右端,调整磁力使工件刚刚能吸附到磁极上,启动工件,用其中的一个支点轻顶工件,使得工件由跳动状态,逐渐恢复到和磁极同轴的稳定状态。
用手推动工件向预定的方向偏出~,固定上下支撑,并用刮色法检查支点与工件的接触情况,调整接触良好后,将工件推离支点2~3mm,开动工件,看工件是否快速归位
靠向支点,并保持稳定。
如有飞出或跳动情况应按上述情况重新调整一次,直至稳定旋转为止。
对于较大的工件也可以用磁力吸住工件,将磁力表架和百分表打在工件外径,旋转并轻轻敲击工件,使工件的偏心量控制在预定的值,一般在~毫米,然后,在最高点左一个记号,上磁状态将其旋转到第四象限,距离支点约10毫米左右,固定支点,检查接触情况并做适当调整,使得工件与支点接触宽度在80%以上即可。
6.磁力大小的调整
偏向调整好后,应该精细调整磁极的磁力大小,一般用手径向稍用力顶工件时,工件应能
轻松离开工件,当手松开时,工件能很快自动靠向两支点并稳定旋转说明磁力调整基本合适,
再根据具体试磨情况在进行微调即可,一般当工件在磨削过程中有停转现象时稍调大一点磁
力,当工件椭圆不好时,应再适当调小磁力。
7.机械手和上下料道的调整
根据工件型号,规格,选用合适的机械手,一般机械手大小和料道宽度应和工件保持1~2mm的间隙,以保持上下料准确、顺畅不卡顿且不与相关部件、仪表干涉为标准。
8.更换砂轮,调整工件与砂轮的轴向和径向磨削位置以及金刚笔和砂轮的修整位
启动液压系统,或使用伺服手轮,使砂轮轴能进入工件内孔且不与其他部件相干涉,然后调整砂轮轴轴向位置使得砂轮悬出工件的左右位置相等,约有2~3mm,再调整砂轮与工件径向位置,使得砂轮刚刚接触工件后再后退~毫米空程,以避免撞击工件。
退出磨架至最右端,倒下修正器,缓慢左移磨架,使金刚笔靠近砂轮至刚刚接触后紧固金刚笔,然后移动修整信号器控制砂轮修正左右位,依据砂轮接杆长度,使得左右两端各空出2~5mm空程,以消除修正时的换向震动。
9.试磨工件
初步测量工件余量,据此设定要磨削的量,例如,初测磨量35um,先在快跳量~后,按10/1或3/6/1的比例设置粗细精磨磨量,并根据经验设定粗细磨的速度,一般粗磨15/10,精磨3/2每秒。
设定完成后,长修砂轮。
将砂轮修整平整,能进入工件内孔而且有15%以上的空隙,以利于冷却水进入和排屑。
然后,按循环启动,试磨工件一般与到尺寸量预留20~30um的量,为试磨时的尺寸控制值。
试磨完成后,通过测量仪器检验工件的尺寸,椭圆,壁厚,垂直差,粗糙度等是否符合工艺要求,如不符合要求重新调整磨削参数直至满足工艺要求后。
10.首件制作
在开始批量生产前,应制作首件,并填写好首件检查的相关内容,由检查员对首件质量进
行确认签字后方可进行批量生产。
以避免首件合格确认不准确,工件不具备批量生产条件而开
工生产,而造成批量废品出现。
首件的定义及使用规定;
1.首件是指生产加工中,拟进行批量生产前连续3件合格产品中,尺寸特性均分布在上下公差带1/3区域内时,选取其中实测值最差的那一个合格品。
2.加工中变更产品型号,更换工卡具,仪器仪表和操作者有变化,以及设备故障维修后需
要重新制作首件。
3.首件检验合格后,应放在作业台的指定区域。
5、内径主动测量仪的调整
将主动测量仪器的测杆装到测量以上,使得两个测杆和测爪头在一条垂线上,将仪表测
爪伸入工件内径,首先将仪表拨到Ⅱ档,调整流量分配的四个电位器,设置粗、细、精磨和
到尺寸的位置,然后拨到T档调整仪表“0”位,调整两个弹性调整螺钉使得上下测爪的压
力显示值误差在2~5um以内。
在实际的操作中,内径主动测量仪的调整往往不是采用仪表说明书的标准工件调整法。
而是采用倒算试调法。
例如:
1.粗略测量工件的实际磨量为,2.在仪表上分别
在上下两个测爪上各压的的量,然后,对工件砂轮,砂轮金刚石位置,长修后试磨工件,
3.磨完后用仪器测得实际留量,例如测得实际剩余磨量为,再次将测爪,伸入工件,
调整上下测爪压力,或用尺寸微调旋钮,将仪表示值跳到左右,4.二次对工件进行磨削
然后测量实际尺寸进行,例如实际测量值为,但工艺要求~,不符合要
求,5.再次利于微调旋钮向上调整,使得加工实际尺寸在左右,刚好在公
差范围之内,然后,可以进行正常的磨削。
6、D923内径检测仪器的调整及标准件的对表方法
一、标准件的计算和对表
1.首先,填写工艺卡片。
记录工艺基本尺寸,上下偏差,各项精度要求。
2.根据工艺要求尺寸选择标准件,尽量使标准件的尺寸和工艺的基本尺寸一致,偏差越
小越好。
3.按照下列公式,计算标准件的实际对表位置
标准件的实际对表位置=标准件实际尺寸—工件基本名义尺寸
例如:
标准件实际尺寸,工件的基本名义尺寸25mm,两者相减的值是
-,如果仪表刻度值为,即“零”线位左边2格的位置即是标
准件对表位置,
4.当工件实际尺寸与标准件实际尺寸差超出仪表的正负刻度时需要向“+”“-”方向借位确
定对表“零”位。
标准件实际尺寸,工件基本尺寸,标准件比工件小,
如果使用的是“+”“-”的千分表,减方向只有的示值范围,需要在仪表盘正
方向借的示值范围,才能满足标准件尺寸的对表要求。
因此,在仪表盘最
左下方刻度开始向右上方属15个大格到+处,+的表盘位置即为标准
件对表“零”位。
5.调整仪器的两个相对固定测点,使其大约等于标准件的尺寸,轻轻固定;
装上仪表,调整
弹簧力使得仪表指针显示在仪表中间位置;
左右移动工件寻找工件的最大点,然后,固定两
个固定支点;
再次左右移动工件,确认工件的最大点。
根据标准件的检测高度,调整仪器基准面,使得仪器测量三个测量点的高度与标准件高
度一致。
按照上述3、4的方法对标准件尺寸在仪表上的示值。
7、内径仪器检验时的注意事项
1.终磨尺寸的检验时,一定要注意,标准件,工件,仪器仪表恒温时间的一致性,且保证
恒温时间温度符合标准要求。
2.磨削测量时,要注意磨削工件在放置恒温一段时间的温差变化,及时调整控制尺寸。
3.在工序间磨削时,最后备用1~2个替代标准件,防止正式标准件过度使用造成磨损严重。
失去使用价值。
4.测量时必须将工件旋转一周以上,以保证工件圆周方向测量位无盲区测量。
5.具体测量时用力应尽量轻柔一些,以保证测量时表针示值的稳定性。
6.每批工件,先进行外观检测,再进行各部尺寸的仪表测量。
7.检验一定数量的工件以后,要校对标准件在仪表的位置是否发生偏移,保证检测点在被
测量工