矿物加工溉论烧结工艺.ppt
《矿物加工溉论烧结工艺.ppt》由会员分享,可在线阅读,更多相关《矿物加工溉论烧结工艺.ppt(69页珍藏版)》请在冰豆网上搜索。
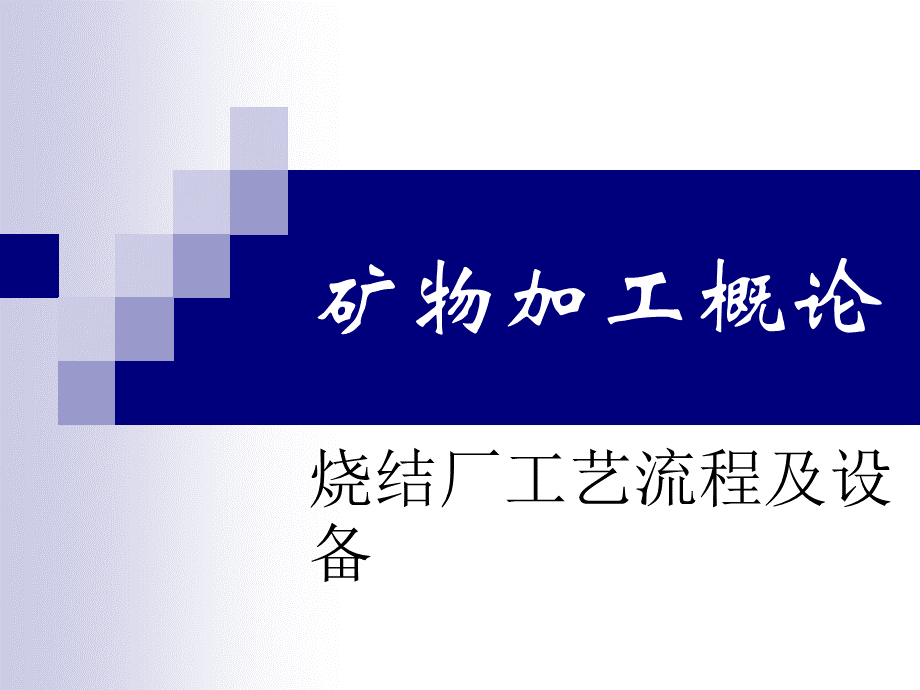
矿物加工概论,烧结厂工艺流程及设备,烧结工艺3.1烧结工艺与分类近代烧结生产是一种抽风烧结过程,将混合料(铁矿粉、燃料、熔剂及返矿)配以适量的水分,混合、制粒后,铺在带式烧结机的炉篦上,点火后用一定负压抽风,使烧结过程自上而下的进行。
烧结矿从烧结台车上卸下,经破碎、冷却、整粒筛分,分出成品烧结矿、返矿和铺底料。
图3-1所示为现行常用的烧结生产工艺流程。
典型的烧结生产工艺流程可分为8个工序系统:
图3-1烧结生产工艺流程,
(1)受料工序系统。
主要包括翻车机系统、受料槽、精矿仓库、熔剂仓库、消燃仓库等,其任务是担负进厂原料的接受、运输和储存。
(2)原料准备工序系统。
包括含铁原料的中和、燃料的破碎、熔剂的破碎和筛分,其任务是为配料工序准备好符合生产要求的原料、熔剂和燃料。
(3)配料工序系统。
包括配料间的矿槽、圆盘给料机、称量设施等;根据规定的烧结矿化学成分和使用的原料种类,通过计算,各原料按计算的质量进行给料,以保证混合料和烧结矿化学成分稳定及燃料量的调整。
(4)混合、制粒工序系统。
主要包括一次混合、二次混合等工序,其任务是加水、润湿混合料,完成混合料混匀,成型过程,为烧结提供透气性良好的制粒小球。
(5)烧结工序系统。
包括铺底料、布料、点火、烧结等。
主要任务是将混合料烧结成合格的烧结矿。
(6)抽风工序系统。
包括风箱、集尘管、除尘器、拍风机、烟囱等。
(7)成品处理工序系统。
包括热破碎、热筛分、冷却、冷破碎、冷筛分及成品运输系统。
该工序的任务在于分出550mm的成品烧结矿,1020mm铺底料,小于5mm冷返矿。
(8)环保除尘工序系统。
主要是用电除尘器系统将烧结机尾部卸矿处、热筛、冷却、返矿及整粒系统各处扬尘点的废气,经过除尘器净化后,废气排入大气,粉尘经过润湿后加入烧结混合料中再烧结,其任务是担负烧结生产的环境保护。
烧结法按照烧结设备和供风方式不同,大致可划分为抽风烧结法、鼓风烧结法、烟气烧结法三类,见图3-2。
图3-2烧结法分类,国内外铁矿粉烧结生产中,广泛采用连续带式抽风烧结机,它具有劳动生产率高,原料适应性强,机械化程度高,劳动条件好,便于实现大型化和自动化特点,见图3-3。
图3-3连续带式抽风烧结机系统1离心抽风机;2桥式起重机;3机头电收尘器;4水封拉链机;5带式输送机;6烧结机;7带式布料器;8点火器、保温炉;9圆辊给料机;10冷风吸入阀;11单辊破碎机;12热矿振动筛;13鼓风带式冷却机;14板式给矿机;15冷却鼓风机,间歇式抽风烧结机(盘),具有投资省、建设快、易掌握的优点,但其生产能力低,劳动条件差,在我国一些地方的小型钢铁企业中仍继续在发挥作用。
鼓风烧结法,其特点是炉篦不黏结且不易烧坏、动力消耗少,风机寿命长,特别适合于有色金属硫化矿烧结,但劳动条件应很好维护以防止S2溢出。
烧结原料准备与配料1.烧结原料准备烧结原料数量大,品种繁多,粒度及化学性质极不均一。
为保证获得高产、优质的烧结矿,精心准备烧结原料是十分重要的生产环节。
原料准备一般包括:
接受、储存、中和混匀、破碎、筛分等作业。
图3-4是钢铁企业原料厂平面布置示意。
图3-4钢铁联合企业原料厂工艺平面布置示意图1主原料码头;2副原料码头;3码头栈桥;4取制样系统;5贮煤场;6混匀配料槽;7混匀场;8汽车受料槽;9二次贮矿场;10一次贮矿场;11整粒车间;12原料控制中心;13炼焦煤一次粉碎室;14供料系统;15用户厂受料点;16烧结矿外运系统;17石灰石、白云石焙烧,
(1)原料接受、储存及中和。
根据烧结厂所用原料来源及生产规模的不同,原料接受方式大致分为四种:
处在沿海并主要使用进口原料的大型烧结厂,其所需原料用大型专用货轮运输。
因此,应有专门的卸料码头和大型、高效的卸料机,卸下的原料由皮带机运至原料场。
卸料机一般为门式,有卷扬滑车、绳索滑车、抓斗滑车和水平牵引式卸料车等。
距选矿厂较远的内陆大型烧结厂,可采用翻车机接受精矿、富矿粉和块状石灰石等原料。
中型烧结厂(年产100万200万吨烧结矿),可采用接受与储存合用的原料仓库。
这种原料仓库的一侧,采用门形刮板、桥形抓斗式或链斗式卸料机,接受全部原料。
如果原料数量品种较多时,可根据实际情况,采用受料槽接收数量少和易起灰的原料。
小型烧结厂(年产20万吨以下的烧结厂),对原料的接受可因地制宜,采用简便形式,如用电动手扶拉铲和地沟胶带机联合卸车,电耙造堆,原料棚贮存;或设适当形式的容积配料槽,以解决原料接受与贮存问题。
也可以在铁路的一侧挖一条深约2m的地沟,安装皮带机,用电动手扶拉铲直接将原料卸在皮带机上,再转运到配料矿槽或小仓库内。
来自冶金厂的高炉灰、轧钢皮、碎焦及无烟煤、消石灰等辅助原料,以及少量的外来原料则用受料槽接收,受料槽的容积能满足10h烧结用料量即可。
受料槽常用螺旋卸料机卸料。
生石灰可采用密封罐车或风动运输。
(2)含铁原料储存、中和混匀。
烧结厂用含铁原料种类多、数量大、原料基地远且分散。
为了保证烧结生产连续稳定进行,烧结厂都设有原料场或原料仓库,储存原料并进行中和混匀。
原料场的大小根据其生产规模、原料基地远近、运输条件及原料种类等因素决定。
图3-5所示为上海宝钢原料场的堆存、中和混匀作业示意图,它包括如下作业:
图3-5宝钢原料场中和混匀示意图18配料槽;9、10中和混匀矿堆场;11入槽皮带机系统;12定量给料装置;13、14堆料机,设有一次堆料场。
各种物料从原料码头卸下后,直接用皮带运往一次料场,按品种、成分不同分别堆放并初步混匀。
设有中和料槽。
由取料机并通过皮带运输机将一次料场中的各种原料送入中和料槽,起贮存、配料、控制送料量提高混匀作业的效果的作用。
设有混匀料场。
通过配料槽进行中和作业的混合料,送往混匀料场,由堆料机沿料场的长度方向进行平铺堆积,堆积层数为2581(堆料机单程行走次数同时切出槽数)。
然后沿料堆垂直面,用取样机切取。
料堆成对配制,一个在铺堆时,另一堆取样送烧结厂配矿槽。
设置原料场,可以简化烧结厂的储矿设施及给料系统,也取消了单品种料仓,使场地和设备的利用率得到改善。
没有原料场而采用原料仓库的烧结厂,其中和作业则借助于移动漏矿皮带车和桥式起重机抓斗,将来料在指定地段逐层铺放,当铺到一定高度后,再用抓斗自上而下垂直取样,把中和料卸入料斗送往配料室,见图3-6。
图3-6原料仓库平铺截取示意图1漏矿皮带;2桥式吊车;3抓斗;4中和料堆;5卸料斗;6运输皮带,(3)熔剂和燃料的破碎、筛分。
烧结生产对熔剂和燃料的粒度都有严格要求,一般要求30mm的含量应大于85,而入厂的熔剂和燃料粒度上限大于40mm,所以都需要在烧结厂内进行破碎与筛分,有关破碎与筛分的流程与设备详见第2章。
熔剂的破碎与筛分。
烧结厂常用石灰石、白云石均需破碎,常用的两种破碎工艺流程为:
(a)一段破碎与检查筛分组成闭路流程,筛下为合格产品,筛上物返回与原矿一起破碎;(b)设预先筛分与破碎组成闭路流程,原矿首先经过预先筛分分出合格的细粒级,筛上物进入破碎机破碎后返回与原矿一起进行筛分。
目前烧结厂多采用(a)流程破碎熔剂。
我国烧结厂的石灰石破碎大多在厂内进行,日本、美国和法国等国则多在矿山进行,破碎后的石灰石转运烧结厂料场。
燃料的破碎与筛分。
烧结厂所用的固体燃料有碎焦和无烟煤,其破碎流程是根据进厂燃料粒度和性质来确定的。
当粒度小于25mm时可采用一段四辊破碎机开路破碎流程,如果粒度大于25mm,应考虑两段开路破碎流程。
我国烧结用煤或焦粉的来料都含有相当高的水分(大于10),采用筛分作业时,筛孔易堵,降低筛分效率。
因此,固体燃料破碎多不设筛分。
四辊破碎机是破碎燃料的常用设备。
当给料粒度小于25mm时,能一次破碎到3mm以下,无需进行检查筛分。
当给料粒度大于25mm时,常用对辊破碎机作粗碎设备,把固体燃料破碎到15mm后,再进入四辊破碎机碎至小于3mm。
宝钢烧结用固体燃料为干熄焦,其含水低,不堵筛孔。
破碎采用设有预先筛分和检查筛分的两段破碎流程。
第一段由反击式破碎机与筛子组成闭路;第二段采用棒磨机,可减少过粉碎,但劳动条件较差。
2.配料
(1)配料的目的和要求。
烧结厂处理的原料种类繁多,且物理化学性质差异也甚大。
为使烧结矿的物理性能和化学成分稳定,符合冶炼要求,同时使烧结料具有良好透气性以获得较高的烧结生产率,必须把不同成分的含铁原料、熔剂和燃料等,根据烧结过程的要求和烧结矿质量的要求进行精确的配料。
烧结生产实践证明,配料发生偏差是影响烧结过程正常进行和烧结矿产质量的重要因素。
固体燃料配入量波动02,会使烧结矿的强度和还原性受到影响,烧结矿的含铁量和碱度波动就会影响高炉炉温和造渣制度,严重时,会引发高炉悬料、崩料现象。
因此各国都非常重视烧结矿化学成分的稳定性。
我国要求TFe0.5%0.1%,CaO/SiO20.050.10;日本要求TFe0.30.4,CaO/SiO20.03,FeO0.1%,SiO20.2%。
首先根据冶炼对烧结矿化学成分的要求进行配料计算,以保证烧结矿的含铁量、碱度、S含量、FeO等主要成分控制在规定范围内,然后选择适当的配料方法袖设备,以保证配料的精确性。
(2)配料方法。
配料的精确性在很大程度上取决于所采用的配料方法。
目前有两种配料方法,即容积配料法和质量配料法。
容积配料。
假设物料堆积密度一定的情况下,借助于给料设备控制其容积达到配料所要求的添加比例。
为了增加其精确性,经常辅助以质量检查。
该法的优点是设备简单,操作方便,因此我国曾有不少烧结厂采用此法。
但由于物料的堆积密度随粒度和湿度等因素的变化而发生波动,致使配料产生较大误差。
为了提高容积配料的准确度,各烧结厂采取许多措施,如安装给料圆盘的中心与料仓中心应相吻合;保持料仓的料位在一定高度,且物料应均匀分布,严格控制物料粒度和水分波动等,基本上可满足烧结生产的要求。
由于容积配料法是靠入工调节圆盘给料机闸门开口度的大小来控制料量的、准确度差,且调整时间长,对配料精确度影响大,质量检查的劳动强度亦相当大,难于实现自动配料。
因此在质量严格管理的今天,此种配料方法已不能适应技术进步和形势发展的要求。
质量配料法。
是按原料的质量来配料,它借助于电子皮带秤和调速圆盘,通过自动调节系统来实现。
图3-7为质量配料系统控制图,由电子皮带秤给出称量皮带的瞬时料量信号,信号输入圆盘调整系统,调节部分根据给定值和电子皮带秤测量值的偏差,通过自动调节圆盘转速以达到给定的料量。
与容积配料比较,质量法易实现自动配料,精确度高。
生产实践证明,当负荷50时,质量配料法精确度为1.0,而容积配料法为5。
我国近期新建的大型厂多采用质量配料法。
图3-7质量配料系统方块图目前国外已有按化学成分配料法,此法是用X射线荧光分析仪对原料进行化学成分分析,根据化学成分确定各种物料的最佳配比。
烧结料的混合与制粒混合作业的目的有二,一是将配合料中的各组分仔细混匀,从而得到质量较均匀的烧结矿;二是加水润湿和制粒,得到粒度适宜,具有良好透气性的烧结混合料。
混合作业一般采用两段式混合。
两段混合是将配合料依次在两台设备上进行。
一次混合的主要任务是加水润湿和混匀,使混合料中的水分、粒度及物料中各组分均匀分布,当加入热返矿时,它还可以将混合料预热。
二次混合除有继续混匀的作用外,主要任务是制粒,同时还可通入蒸气预热混合料。
加强混合过程中的制粒,使细粒物料黏附在该粒子上,形成粒度大小一定的粒子,可改善烧结料层的透气性,获得较高的烧结生产率。
混合作业大都采用圆筒混合机,图3-8是二次混合室圆筒混合机配置示意图。
图3-8二次混合室圆筒混合机配置示意图(尺寸单位:
mm,高程单位:
m)1进料皮带;2圆筒;3偏车,2影响混合料制粒的因素
(1)原料的性质。
对烧结料混合制粒过程有影响是矿物的润湿性、粒度与粒度组成和颗粒的形状等。
在混合制粒过程中,依靠颗粒间的毛细水作用,使粒子相互聚集成小球,易润湿的矿物在颗粒间形成的毛细力强、制粒性能好。
铁矿物的制粒性能依次是褐铁矿、赤铁矿、磁铁矿,含泥质的铁矿物易成球。
对烧结混合料制粒小球的结构研究表明,球粒一般是由核颗粒和黏附细粒组成,称之为“准颗粒”。
“准颗粒