整理金属表面防护技术Word格式文档下载.docx
《整理金属表面防护技术Word格式文档下载.docx》由会员分享,可在线阅读,更多相关《整理金属表面防护技术Word格式文档下载.docx(18页珍藏版)》请在冰豆网上搜索。
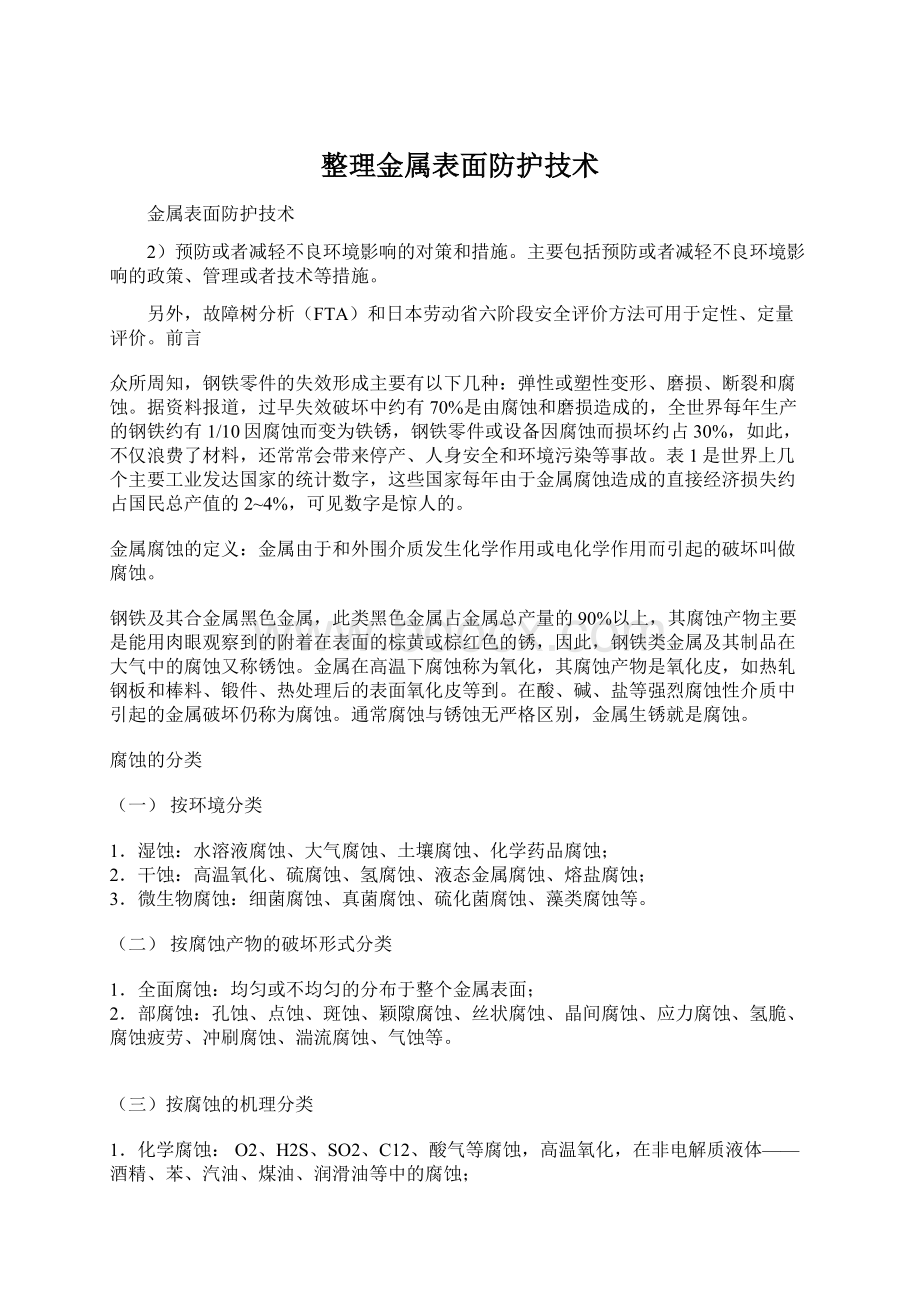
2.干蚀:
高温氧化、硫腐蚀、氢腐蚀、液态金属腐蚀、熔盐腐蚀;
3.微生物腐蚀:
细菌腐蚀、真菌腐蚀、硫化菌腐蚀、藻类腐蚀等。
(二)按腐蚀产物的破坏形式分类
1.全面腐蚀:
均匀或不均匀的分布于整个金属表面;
2.部腐蚀:
孔蚀、点蚀、斑蚀、颖隙腐蚀、丝状腐蚀、晶间腐蚀、应力腐蚀、氢脆、腐蚀疲劳、冲刷腐蚀、湍流腐蚀、气蚀等。
(三)按腐蚀的机理分类
1.化学腐蚀:
O2、H2S、SO2、C12、酸气等腐蚀,高温氧化,在非电解质液体——酒精、苯、汽油、煤油、润滑油等中的腐蚀;
2.电化学腐蚀:
(1)微电池腐蚀
(2)原电池腐蚀:
电偶腐蚀、杂散电流腐蚀、浓差电池腐蚀。
如:
潮湿空气中的大气腐蚀,酸、碱、盐溶液和海水中腐蚀,土壤腐蚀,不同金属接触处的腐蚀,其它电解质溶液中的腐蚀。
影响金属锈蚀的主要因素
(一)金属锈蚀的内部因素
从热力学角度而言,金属和它的腐蚀产物相比,具有较高的能量,是不稳定的,有自发的向低能量的腐蚀产物转化的趋势,即金属发生锈蚀是自然现象。
工业中绝大多数的金属是多组分的合金,金相组织不同、含有杂质、机加工变形不均匀、应力分布不均匀等,这些物理的、化学的和电化学的不均匀性,当表面遇到腐蚀介质或表面形成水膜,不可避免地会发生化学或电化学腐蚀。
(二)金属腐蚀的外部因素
1.相对温度的影
空气中相对湿度越高,金属表面水膜越厚,空气中的氧透过水膜到金属表面作用。
相对湿度达到一定数值时,腐蚀速度大幅上升,这个数值称为临界相对湿度,钢的临界相对湿度约为70%。
2.温度的影响
环境温度与相对湿度关联,干燥的环境(沙漠)下,气温再高金属也不容易锈蚀。
当相对湿度达到临界值时,温度的影响明显加剧,温度每增加10℃,锈蚀速度提高两倍。
因此,在湿热带或雨季,气温越高,锈蚀越严重。
3.氧气的影响
用下列反应式表示生锈过程:
Fe+H2O→Fe(OH)2
Fe(OH)2+H2O+O2→Fe(OH)3
Fe+H2O+O2→Fe(OH)3
可见没有水和氧气,金属就不会生锈,空气中20%体积是氧气,它是无孔不入的。
4.大气其它物质的影响
大气中含有盐雾、二氧化硫、硫化氢和灰尘时,会加速腐蚀,因此,不同环境下受腐蚀的大小差别是明显的,城市高于农村;
工业区高于生活区;
沿海高于内陆;
高粉尘高于低粉尘。
(三)加工过程中的锈蚀因素
原材料已锈蚀,加工后未能完成去除;
加工中接触了切削液,润滑剂等工艺材料;
酸洗后中和清洗不当;
热处理氧化脱碳或残盐清洗不净;
检查、搬运和装配时操作者留下的手汗;
去应力或去氢退火不当;
工序间和封存防锈不适宜等。
防止金属生锈的主要方法
(一)选择耐蚀材料
主要是采用有色金属合金和不锈钢。
(二)金属表面预制金属(合金)或非金属覆盖层
1.转化膜:
发黑(发蓝)、磷化、阳极氧化;
2.表面合金化:
渗氮、渗锌、渗硅、渗铝、渗铬等;
3.金属覆盖层:
电镀金属、喷涂金属、热浸镀、化学镀等;
4.非金属覆盖层:
搪瓷、陶瓷、油漆、塑料、橡胶等;
5.涂覆防锈材料:
防锈水、切削液、气相缓蚀剂、可剥塑料、防锈油、防锈脂等。
(三)阴极保护法
以牺牲阳极而保护阴极的电化学法。
如在海水中,以镁块作阳极与钢板联在一起,通以电流使钢板变成阴极得以保护。
地下管道和化工设备,也是外另一个阳极并通电使钢件(阴极)得到保护。
(四)控制环境防蚀
1.采用除湿机和加湿降低温度,相对湿度控制在低于60~70%,金属锈蚀减慢;
相对湿度低于60%时,非金属不会发霉变质;
2.充氮或真空包装封存可延缓锈蚀;
3.包装内置缓蚀剂;
4.钢铁制品在电炉加热(高温)时,炉内形成保护气氛或真家加热。
综上所述,防止金属锈蚀的方法很多,应考虑诸多因素后判断选择,如:
零件的工作环境、零件的服役条件、生产的安全性、对环境的污染程度、制造成本等。
二、常用的几种表面防护技术
(一)电镀
采用电解的方法在基体(经过前处理)表面沉积所需要的覆盖层的过程称为电镀。
电镀是非常古老的传统技术,广泛应用于永久性的装饰和防护。
电镀可以分为单金属电镀,多层组合电镀,以及合金电镀等。
影响镀层质量的因素很多,如:
镀前处理、镀液的净化方式和程度、予镀方式的合理性、镀液体系建立、组合及厚度的确定、工艺参数(PH值、温度、电流密度)、添加剂(光亮剂、整平剂、除应力剂、润湿剂、分散剂)、镀液分析及补充制度、操作制度、镀后处理(去氢、封闭)等。
由于电镀三废对环境污染和影响健康,各地环保部门管理日趋严格,很多企业自己不设电镀车间,而是去专业厂(车间)委托加工。
为确保电镀件的质量,应依据有关标准和规定对镀层的外观、结合力、厚度、孔隙率、耐蚀性等提出具体的要求。
一旦验收时或使用中出现质量问题,便于质量事故分析和改进。
(二)氧化
氧化处理分为黑色金属氧化处理和有色金属氧化处理两类,这里仅涉及前者。
钢铁及合金的氧化处理,又称发蓝或发黑处理。
由于其成本低、效率高、收效快、工艺稳定、操作方便、设备简单,使用范围十分广泛。
1.碱性化学氧化法
碱性氧化法是最常用的方法,它是在较高温度下,在含有一定氧化剂的氢氧化钠溶液中进行。
氧化剂和氢氧化钢与金属铁发生化学反应,最终形成氧化铁(Fe3O4)为主要成分的氧化膜。
膜的颜色取决于零件的表面状态、合金成分和氧化处理的工艺条件,一般为黑色或兰黑色。
膜厚0.6~0.8um.
化学反应的顺序是无形成亚铁酸纳(Na2Fe02)和铁酸纳(Na2Fe204),然后由亚铁酸钠与铁酸钠反应形成Fe304氧化膜。
反应式如下:
3Fe+Na02+5Na0H→3Na2Fe02+H20+NH3↑
6Na2Fe02+NaN02+5H20→3Na2Fe204+7Na0H+NH3↑
Na2Fe02+Na2Fe204+2H20→Fe304+4Na0H
(1)碱性氧化法溶液配方及工艺规范
1.规划环境影响评价的技术依据配方号含量
(二)安全预评价范围一次氧化
二次氧化
(6)列出选定的评价方法,并作简单介绍。
(g/L)组分及工艺规范
分类具体内容应编写的环境影响评价文件1
表四:
项目排污情况及环境措施简述。
2
3
1)采取防护措施。
4
5
(3)评价单元划分应考虑安全预评价的特点,以自然条件、基本工艺条件、危险、有害因素分布及状况便于实施评价为原则进行。
6
第一槽
第二槽
氢氧化钠
550~650
600~700
650~700
500~600
700~800
亚硝酸钠
150~250
180~220
200~250
200~220
100~150
150~200
-
硝酸钠
50~70
130~150
二氧化猛
20~25
重铬酸钾
25~35
温度(℃)
135~145
138~150
130~135
135~140
145~152
145~150
时间(min)
15
10~20
60~90
15~20
20~30
碳钢
15~45
30~35
合金钢
15~60
30~60
(2)溶液的配制
在氧化槽内加入2/3体积的水,将计算量的氢氧化钠加入槽内,使其溶解;
在搅拌下加入亚硝酸钠或硝酸钠,待全部溶解后,加水至规定体积。
氧化液先在沸腾温度下浸入钢板,或加入部分旧溶液(约20%以下)进行处理,待溶液中积累了一定的铁离子,能使样片获得黑色氧化膜后,即可用于生产。
(3)溶液的维护
1氧化
溶液在使用中消耗会使组分变化,可定期按分析结果补充,亦可按溶液的沸点和膜层质量来判定溶液需否调整。
当沸点过高时,表示浓度过高,此时易形成红色挂灰,可加水稀释。
沸点过低时,表示浓度不足,此时膜的颜色不深或不能发黑,应补加药品或蒸发多余水分。
氢氧化钠的添加量,可按溶液沸点每高1℃,每升溶液添加10~15g计算。
亚硝酸钠的加入量可参照如下比例:
一次氧化:
Na0H:
NaN02=(2~3):
1;
二次氧化:
NaN02=(2.5~3.5):
1(一槽);
NaN02=(3.4):
1(二槽)。
2停产期间溶液表面硬结,加热之前应先用铁器打碎硬皮,加水至工作液面,搅拌均匀后升温至工作温度。
3清理
漏入槽中零件应及时打捞,避免溶液中铁离子增加。
定期除渣保持溶液清洁,工作温度下投入零件前,液面浮起的大量红褐色铁氧化物应用网捞出。
亦可在100℃以下搅拌情况下,按每升溶液加入甘油5~10ml的比例加入。
4操作
氧化膜中杂质的红色挂灰,多为氧化初期形成。
进行一次氧化时,最好在零件入槽10分钟后,取出用热水冲洗,观察有无红色挂灰。
如有可用毛刷擦除,或将零件放入含150~200g/L铬酐和10~15g/L的硫酸的溶液中,浸1~1.5分后清洗,重新入槽氧化。
氧化过程中定期抖动零件也是必要的。
5槽液的使用期限
处理量和溶液的维护程度直接影响槽液使用期限,更换时,可先澄清1~2天,清除表层和沉淀的残渣后,澄清的部分用来配制新溶液。
6氧化温度和时间同钢的含碳量有密切关系,选择这些参数时,可参考下表2所列数据。
表2氧化温度、时间与含碳量的关系
(4)氧化后的处理
后处理的目的在于提高氧化膜的防锈能力,一般进行皂化或填充处理,其配方规范如表3表示。
表3钢铁氧化后处理工艺规范
经填充或皂化后,还进行封闭处理,可在100~110℃下的机油、锭子油、变压器油中浸5~10分钟。
如不进行填充或皂化处理,氧化后经清洗,可直接进入脱水防锈油。