模具检验验证规范Word下载.doc
《模具检验验证规范Word下载.doc》由会员分享,可在线阅读,更多相关《模具检验验证规范Word下载.doc(13页珍藏版)》请在冰豆网上搜索。
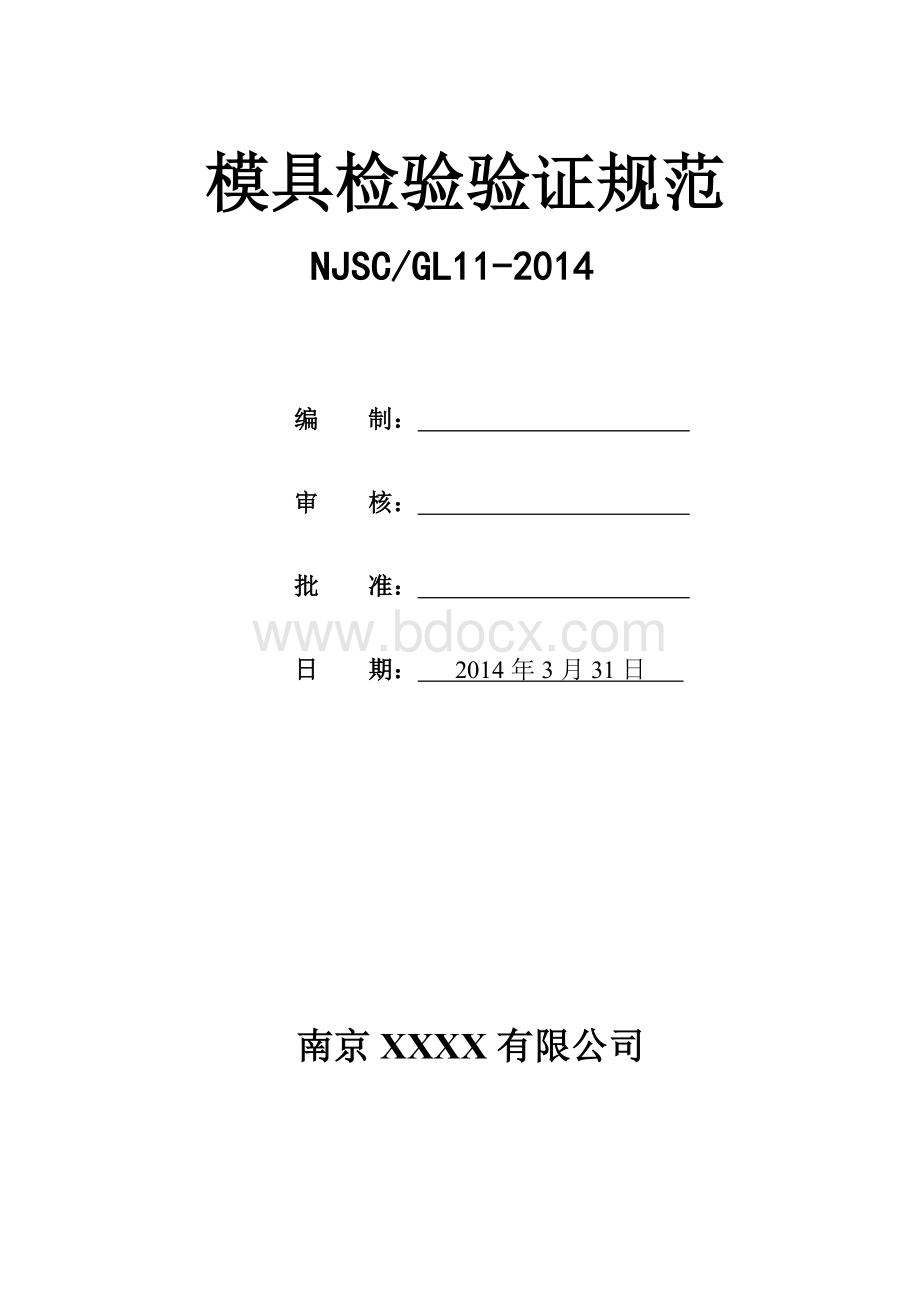
3.3.2模具总成后的检验,包括模具外观、可成形性、成形产品等的检验。
四、职责
4.1技术部负责相关检验要求数据的提供。
4.2质量部负责对物料、部品以及模具实施来料检验、过程检验和最终检验。
4.3采购部对采购物资质量负责,并配合质量部做好来料检验工作。
4.4生产部协助做好过程检验,并确保未经检验或检验不合格的物资不投入使用。
五、检验验证流程
5.1来料检验
5.1.1作业流程图
检测并记录
相关方检讨
办理入库
NG
暂放
物料进入
OK
检查
修整
特采标识
拒收、隔离
出不合格品处置单
合格标识
退回供方
报检
5.1.2作业流程
5.1.2.1仓管员在接收到外来的物料时,对物料种类、供应商、数量等信息进行确认,确认无误后将物料存放在暂放区域,并以“待检品”予以标识同时通知质检。
5.1.2.2质量部接到报检信息后在二个工作日内对物料名称、规格、供应商、包装、标识等与相应的采购文件进行核对,无误后进行抽样或全数检查,并将检验结果填入《进货检验记录》。
如遇到特殊情况,生产急需使用物料,质量部应在半个工作日内完成检查工作。
5.1.2.3检验合格的物料贴上“合格”标签,仓管人员办理入库手续。
5.1.2.4检验不合格的物料,填写《不合格品处置单》,质量部会同技术部相关人员进行检讨,可接受的以“特别采用”进行标识,无法采用的贴上“不合格”标签并予以隔离。
5.1.2.5项目部将不合格物料的信息反馈给供应商,无法采用的物品予以退回。
5.1.2.6如特别采用的物料要修整的,修整后须检验合格方能投入使用。
5.2过程检验
5.2.1作业流程图
过程加工
下道工序
报废
不合格报告
特采
完工自检
5.2.2作业流程
5.2.2.1各工序作业者完工后按图纸或工艺卡质量要求进行自检;
若自检不合格则重新返工,本工序无法返工的按不合格处理。
5.2.2.2质量部接到报检信息后进行全数检查,并将检验结果填入《零件卡片(检验)记录》。
5.2.2.3检验合格的零/部件以“合格”进行标识,检验员签字、盖章后,移交下一道工序。
5.2.2.4检验不合格的零/部件,质量部会同技术部相关人员进行检讨,可接受的以“特别采用”进行标识,无法采用的贴上“不合格”标签并予以隔离。
5.2.2.5对于不合格项质量部开《不合格品处置单》,有重大质量事故质量部开《质量事故处理报告》。
相关部门对问题点分析、纠正和预防,同时对预防措施进行确认。
5.2.2.6特别采用的部品对其它工序有影响的,技术部需立即办理相关文件更改手续并及时通知相关方;
要修整的部品,修整后须检验合格方能投入使用。
5.3最终检验
5.3.1作业流程图
5.3.1.1模具零部件的成品最终检验作业流程图
返工或返修
检验
不合格品标/识隔离
报检
最终产品
记录存
入库
合格品检验报告ianyanbaogao
不合格品报告
让步接收
不合格品评审
5.3.1.2模具总成后的检验作业流程图
修模联络
检验并记录
产品检测、送样
零部件组装复合
试作
总装实配复模
试模联络
验收移交
修正
OK
5.3.2作业流程
5.3.2.1模具零部件制造完成后,质检人员对所有零部件做最终成品检验。
零部件都检验合格后,装配钳工人员担当对各部件进行组装、复合,实配合格后再进行总装实配复模,并确认各部件功能运作正常,不符合要求的及时修正。
装配钳工负责将装配过程中发现的问题及时记录于《钳工装配表》,并及时与技术部沟通。
5.3.2.2总装实配后装配钳工按《模具组装质量检查表》相关内容进行检验。
自检完成后,将《模具组装质量检查表》交质量部主管报检,由质量部主管召集技术部主管、分管工艺员、钳工组组长、装配钳工,对模具进行试模前的检查。
检查合格,检查人员在《模具组装质量检查表》上签字,质量部负责保存《模具组装质量检查表》,并通知生产部安排试模。
试模工作由分管工艺员负责、试模员参加、检验员配合。
试模过程中,试模人员须按规定及时填写《试模单》。
5.3.2.3试模后,质量部对产品进行检测并及时将试模样件的检测报告发给相关人员。
技术部负责对质量部提供的检测数据进行分析、判定,对不符合图纸要求或试作中的问题点以及要求设计更改、模具调整的内容向生产部提出修正。
5.3.2.4模具验证合格,由分管工艺员在《试模单》上填写模具验证结论,经分管工艺员、试模员、技术部主管签字,交质量部主管签批后,方可交付。
六、检验和试验
6.1取样
同一规格的外购件(五金件、标准件)按每批3~5件抽取样本或由质检担当确定,小于5件的批次进行全检,有公差标准的关键尺寸在现有资源可以测量的情况下要全部测量。
对原材料、所有自制零部件及外协制作零部件全检。
6.2检验要求
6.2.1质检人员抽取样本后,先分别对外观、尺寸进行判定。
6.2.2外观检查环境要求:
采用常态照明,待测量物品测量面与检验人员肉眼距离25~35cm,观察角度要求垂直于待测量物品被测面的±
45º
角,观察时间为10±
5秒。
6.2.3监视和测量装置要求:
卡尺精度等级不低于0.02mm,千分尺精度等级不低于0.01mm,标准规精度等级不低于0.01mm,其它或自制的检具等装置要满足相关的工艺、检验文件或工程图纸上的测量要求。
6.2.4圆形零件的外径检查:
公差要求在±
0.05以下的,测量工具为:
游标卡尺;
0.05以上的,测量工具为千分尺或数显卡尺;
6.2.5内孔检查:
圆形内孔的检查量具为:
公差在0.05以下的用游标卡尺检查;
公差在0.05以上的用内径千分尺、内径表或数显卡尺。
方孔的检查量具为:
公差在0.03以上的用千分尺、数显卡尺或塞规检查。
6.2.6方形零件的外形检查:
公差要求在0.05以下的用游标卡尺检查;
公差在0.05以上的用千分尺或数显卡尺检查。
6.2.7成品模具的检查:
外观无划痕、无碰伤、无癍点;
上、下模合模顺畅、无干涉;
落料冲孔模必须经过切纸检验后间隙均匀;
符合上述要求的则视为合格;
否则为不合格。
6.2.8判定:
6.2.8.1检查结果误差在允许的公差范围内,则判为合格;
6.2.8.2检查结果误差超出公差允许的范围(不含允许公差的上限或下限),则判定为不合格。
6.2.8.3客户有具体要求的按客户的要求进行检查。
6.3检验内容
6.3.1五金类(螺丝、弹簧等)
性质
检验项目
检验方法
检验要求
缺陷类别
外观
表面外观
目视
无色差、无混料、无氧化、无毛边
一般
无机械损伤、无缺损、变形等不良
重要
功能
适配性
配合产品
配合应满足图纸或规格说明书
使用功能
测试
按规定测量其机械要求项目
尺寸
尺寸测量
卡尺
符合规格要求
包装
包装状况
包装无破损,标签字迹清楚
6.3.2模具零/部件类(含毛坯和成品及委外加工的零/部件)
无机械损伤,无缺损及扭曲变形,无开裂
重要
无氧化现象,表面光洁,倒角均匀无锐边,编号正确、清晰
一般
材质
供方检测
供方提供的质保书(或物性表)满足规格要求
硬度
硬度计
硬度满足规格要求
加工性
工艺验证
使用部门试用确认
2D尺寸
卡尺,深度尺,高度尺,
满足设计图纸要求(孔、槽可用塞规、芯棒测量)
千分尺/机床
3D值
三坐标/机床
满足造型数据要求
垂直度
满足设计图纸要求
斜度
三坐标/角度尺
实配
滑动部滑动顺畅,产品面间隙≤0.03mm,其它间隙≤0.05mm
6.3.3原材料入厂
无氧化现象,表面光洁,编号正确、清晰
卡尺,卷尺,
6.3.4零/部件热处理后入厂
无缺损及扭曲变形,无开裂
编号正确、清晰
卡尺,深度尺,高度尺
3D尺寸
6.3.5模具装配检验
6.3.5.1试装模具,修配销孔,检查零件的基本尺寸,外形是否与图纸一致,是否有干涉或不合理的结构。
6.3.5.2模板处理,表面突起部位要修平,避免磕碰,划伤模板。
6.3.5.3所有零件在安装前要进行消磁处理,检验标准,用0.02mm塞尺靠近不吸。
6.3.5.4选择螺丝。
零件的旋合长度应达到螺钉外径的1.5-2倍。
在装配时,同一个工装或项目所用的同一规格螺钉应一致,同一件上螺丝长短应一致。
6.3.5.5选择销子。
销子深入工件的长度应为销子直径的2倍左右对于淬火件,渗氮件来说,应用手压入或者用铜棒轻轻敲入即可,不可大力的砸入;
对于软料来说,应用小锤敲入即可。
当两连接件的销孔都是通孔时,要控制销子