数控铣削加工工艺设计与编程加工Word下载.docx
《数控铣削加工工艺设计与编程加工Word下载.docx》由会员分享,可在线阅读,更多相关《数控铣削加工工艺设计与编程加工Word下载.docx(20页珍藏版)》请在冰豆网上搜索。
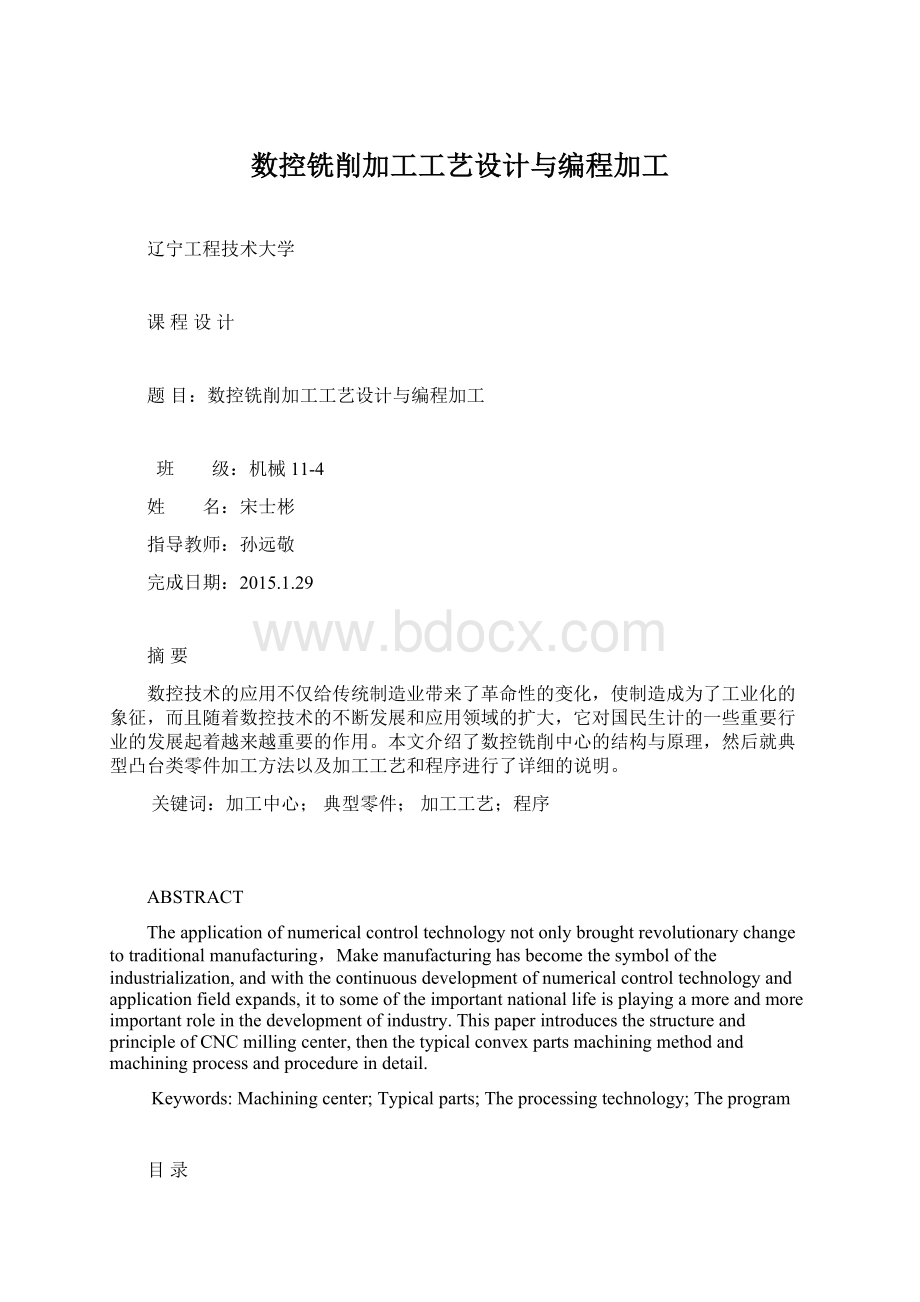
Keywords:
Machiningcenter;
Typicalparts;
Theprocessingtechnology;
Theprogram
目录
一.设计说明2
二.图样分析2
1.图面分析2
2.精度分析3
(1)尺寸精度3
(2)形位精度3
(3)表面粗糙度3
三.工艺分析及处理3
1.数控铣削加工零件与加工4
(1)机床与毛坯4
(2)数控铣削加工分析4
2.数控铣削加工工件的安装方式4
3.数控铣削加工刀具5
(1)刀具的选用5
4.数控铣削加工工序7
1)数控铣削加工工序的划分7
2)工步顺序的安排原则7
3)工序顺序的安排原则7
四.加工用量的选择与确定9
五.编程参数的计算9
1切削参数的选择9
(1)主轴转速(n)9
(2)进给速度(f)9
(3)切削深度和切削宽度9
2基点的计算9
六.编程加工10
1建立工件坐标系10
2程序编制的原则11
3数控加工程序编制11
一.设计说明
根据如图1所示的零件图,通过图样分析、工艺分析、加工用量的选择、程序的编制完成工件的数控程序设计。
图1零件图
1.工件表面去毛倒棱
2.加工表面粗糙度侧平面及孔Ra1.6µ
m.底平面为Ra3.2µ
m
3.材料45钢
图2立体图
二.图样分析
在图样分析中,首先要正确分析零件图,确定零件的加工部位与顺序,并根据零件图的技术要求,分析零件的形状、基准面、尺寸公差和粗糙度要求等。
1.图面分析
如图1-1所示的零件是典型的方圆结合类零件,通过对此零件图的分析可知道:
此零件的外轮廓圆台、正方圆弧凸台、三角凸台,中心有一个通孔。
虽然该零件轨迹曲线不太复杂,但有着严格的几何精度要求,必须保证其尺寸精度和几何精度,所以加工难度较大。
2.精度分析
(1)尺寸精度如图1-1所示的零件中精度要求较高的尺寸主要有四方体尺寸加工误差为0.03mm、六边形和整圆尺寸的加工误差为0.04mm、深度尺寸为0.05mm、孔的尺寸为Ф10H8等。
对于尺寸精度要求,主要通过加工过程中的精确对刀,正确选用刀具的磨损量和正确选用合适的加工工艺等措施来保证。
(2)形位精度如图1-1所示的零件中主要的形位精度有四方体、六方体、整圆相对于外形中心线的对称度,加工表面相对于工件底平面的平行度等。
对于形位精度的要求,在对刀精确的情况下,主要通过工件在夹具中的正确安装等措施来保障。
(3)表面粗糙度如图1-1所示的零件中,所加工表面底面的表面粗糙度R3.2µ
m,所加工表面侧平面和孔的表面粗糙度要求均为R1.6µ
m。
对于表面粗糙度要求,主要通过选用正确的粗、精加工路线,选用合适的切削用量等措施来保证。
加工完成后需要进行清根操作,同时还要对整个零件进行手动去毛倒棱,自检自查。
三.工艺分析及处理
数控铣削加工工艺的实质,就是在分析零件精度和表面粗糙度的基础上,对数控铣削的机床选择、毛坯选择、加工方法、装夹方式、切削加工进给路线、刀具选择以及切削用量等工艺内容进行正确而合理的选择。
1.数控铣削加工零件与加工
(1)机床与毛坯
如图1-1所示的零件选用的机床为FANUC-0i系统的数控铣床,毛坯材料选用45钢,尺寸为Φ80mm*35mm的圆钢。
(2)数控铣削加工分析
为了保证零件的各项精度需求,本工件采用对整个零件进行先粗加工,在精加工的加工方案。
粗加工主要用于去除工件余量,对于粗加工后的精加工余量,在保证加工余量的基础上,应尽量减少精加工余量。
粗加工时,应以保证加工效率为主,因此粗加工一般使用大直径刀具。
数控铣床加工零件时,粗加工和精加工一般采用顺铣即左刀补的加工方式。
2.数控铣削加工工件的安装方式
由于该工件为单件加工,所以在加工过程中选用通用夹具进行定位与装夹。
根据加工要求选用三爪卡盘为夹具,工件装夹后,首先找正工件侧母线与主轴方向平行,然后找正工件中心,并将该点设为工件坐标系的原点。
夹具的要求,在数控铣削加工过程中,夹具是用来装夹被加工工件的,因此必须保证被加工工件的定位精度,并尽可能做到装卸方便、快捷。
选择夹具时应优先考虑使用通用夹具,使用通用夹具无法装夹、或者不能保证被加工工件的定位与加工工序的定位精度时,才采用专用夹具,专用夹具的定位精度较高,成本也较高。
对于本设计凸台类零件铣削加工的夹具选择三角卡盘。
3.数控铣削加工刀具
在零件加工中,刀具的选择是一项非常重要的工艺内容。
刀具选择的好坏,将直接影响到工件的精度和质量。
在加工时,主要根据工件材料、工序内容、机床的加工能力等。
传统的机床加工对刀具的要求比较低,而数控机床对刀具的要求则特别高。
现代数控机床转速高,加工精度高,加工性状多种多样,而且加工的很多的零件的部位都是微细窄小表面,需要的刀具很小,因此,数控机床上的刀具就要有很高的要求。
数控机床刀具一般要有高的强度、高刚度、高耐热耐磨性和硬度。
在加工时要仔细选择刀具。
在数控铣床上,铣削零件侧面时一般用高速钢圆柱立铣刀,铣削上表面时多用硬质合金端面铣刀,加工沟槽时一般用硬质合金立铣刀,而对于一些底面圆或圆弧型的沟槽要用球头铣刀,钻孔时一般用的是高速钢钻头。
数控铣削表面时一般速度较高。
(1)刀具的选用
数控机床必须有与其相适应的切削刀具配合,才能充分发挥作用。
数控加工中所用的刀具,必须适应数控机床所特有的工作条件,才能与机床在最佳配合条件下工作,从而充分发挥数控机床应有的作用。
由于数控机床具有多把刀具连续生产的特点,如果刀具设计、选择使用不合理,就会造成断屑、排屑困难或刀刃过早磨损而影响加工精度,甚至发生刀刃破损而无法进行正常切削,产生大量废品或被迫停机,数控机床所用刀具不仅数量多,而且类型、材料、规格尺寸及采取的切削用量和切削时间也不相同,刀具耐用度的相差很悬殊。
因此,在选用数控机床的刀具时,必须考虑到与刀具相关的各种问题。
数控机床对刀具的要求:
1)适应高速切削要求,具有良好的切削性能
2)高的可靠性
3)较高的刀具耐用度
4)高精度
5)可靠的断屑及排屑措施
6)精确迅速的调整
7)刀具标准化、模块化、通用化及复合化
对于本设计凸台类零件铣削加工的刀具及其参数选择见表2。
在刀具的选用中,粗加工选用直径较大的刀具,本零件加工中选用Ф16mm的立铣刀进行加工,为减少换刀次数,粗、精加工中采用同一种刀具。
这个零件先用Ф16mm的立铣刀、Ф9mm的钻、Ф16mm的立铣刀进行粗铣,再用Ф16mm的立铣刀进行精铣,用Ф2.5mm的钻钻定位孔,用Ф10mm的铰刀对定位孔进行精加工。
数控刀具明细表如表2
表2数控刀具明细表及数控刀具卡
零件图号
零件名称
材料
数控刀具
明细表
程序编号
车间
使用设备
45#钢
数控铣床
刀具号
刀位号
刀具名称
刀具
换刀方式
加工部位
直径
长度
手动/自动
设定
补偿
T1
1号刀位
Φ16mm立铣刀
20mm
10.2
20
手动
外形轮廓
T2
2号刀位
Φ2.5mm钻
14.5mm
15
中心孔定位
T3
3号刀位
Φ9mm钻头
10mm
5
25
钻孔
T4
4号刀位
Φ10H8铰刀
8.5mm
12
铰孔
T5
5号刀位
9mm
外轮廓
编制
审核
批准
第1页
共1页
表3工艺过程卡
零件材料
毛坯种类
毛坯硬度
毛重/kg
净重/kg
工序号
工序名称
设备名称及型号
夹具
进给量(mm/r)
主轴转速
切削速度
冷却液
1
粗铣外形轮廓
数控加工中心
三爪卡盘
0.25mm/r
600r/min
113m/min
乳化液
2
中心钻定位
0.025mm/r
2000r/min
376m/min
3
0.1mm/r
18m/min
4
1000r/min
31m/min
精铣外形轮廓
251m/min
6
手动去毛倒棱,自检自查
4.数控铣削加工工序
1)数控铣削加工工序的划分
①以一次安装能够进行的加工为一道工序
②以一个完整的数控程序能够连续进行加工的内容为一道工序
③以零件的类同结构内容使用一把刀具进行加工为一道工序
④以粗加工、精加工划分工序
2)工步顺序的安排原则
①先粗后精
②先近后远
③内外交叉
④保证工件加工刚度原则
⑤同一把铣刀尽量连续加工原则。
3)工序顺序的安排原则
①先加工定位面,即前道工序的加工能够为后面的工序提供精加工基和合适的装夹表面。
制定零件的整个工艺路线实质上就是从最后一道工序开始从后往前推,按照前道工序为后道工序提供基准的原则来进行安排。
②先加工平面后加工孔,先加工简单的几何形状,后加工复杂的几何形状。
③对于零件精度要求高,粗、精加工需要分开的零件,先进行粗加工,后进行精加工。
④以相同定位、夹紧方式安装的工序,应该连续进行,以便减少重复定位次数和夹紧次数。
⑤加