产品结构设计全册配套最完整精品课件1PPT资料.pptx
《产品结构设计全册配套最完整精品课件1PPT资料.pptx》由会员分享,可在线阅读,更多相关《产品结构设计全册配套最完整精品课件1PPT资料.pptx(256页珍藏版)》请在冰豆网上搜索。
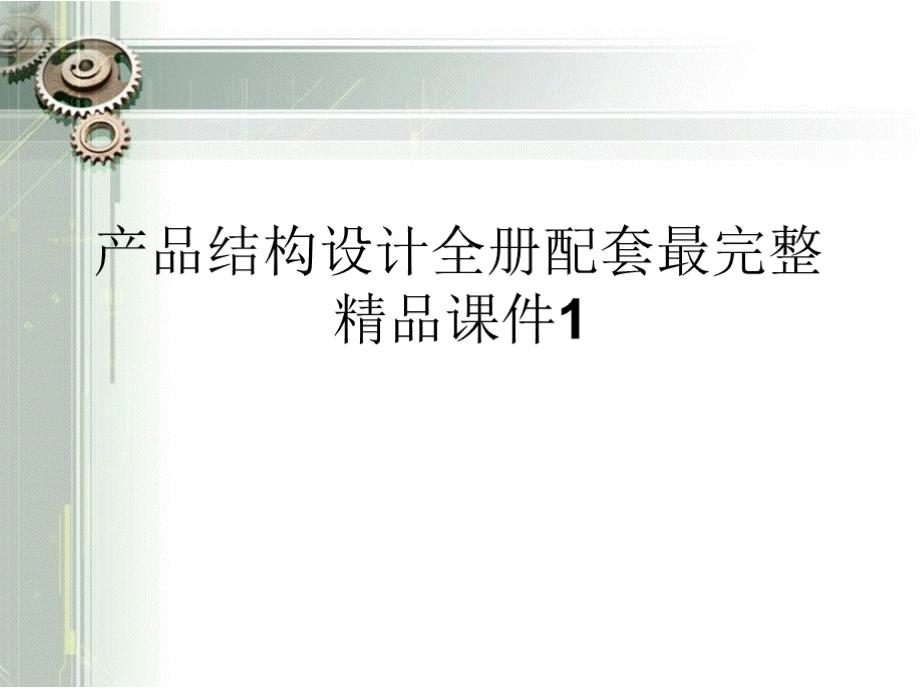
,定位零部件:
以图1-2为例,固定的零部件与运动的零部件在结构上有所不同。
便于拆、装:
以图1-3、4为例,考虑产品的组装、拆卸和维修、维护,箱体多设计成分体结构,各部分通过螺丝、锁扣等进行组合连接。
考虑拆卸的设计:
以图1-5为例,不考虑拆卸的设计。
考虑材料及加工、生产方式:
产品功能和使用目的决定外壳材料,生产成本和批量决定加工、生产方式,进而决定壳体、箱体的结构设计。
考虑装饰与造型装饰与造型的设计应结合产品的功能、构件的材料及加工、生产方式进行。
三、壳体、箱体的设计准则与程序,保证刚度、强度、稳定性及加工性的设计准则刚度:
对于承受较大载荷及作为支撑和其他零部件定位的壳体和箱体,刚度是主要设计准则。
强度:
强度时考虑壳体、箱体的防护和保护性能进行设计的基本准则,分静态和动态两方面考虑。
稳定性:
受压及受压弯结构都存在失稳问题,特别是薄壁腹部还存在局部失稳问题,必须校核。
加工性:
铸造、注塑构件应考虑液体的流动性、填充线和脱模,冲压件应考虑材料延展性和拉伸能力,并做相应的计算。
壳体、箱体的通常设计步骤与程序初步确定形状、主要结构和尺寸。
常规计算。
静动态分析、模型或实物试验及优化设计。
制造工艺性和经济性分析。
详细结构设计,1.2、铸造壳体、箱体,一、铸造壳体、箱体的特点有较高的刚度、强度:
铸造构件一般壁厚较大,适合对刚度强度要求较高的产品外壳;
也可以在铸件上制作部分其他结构部件。
造型适应性强:
可制作比较复杂和变化不规则外形,以图1-6、7、8为例。
表明粗糙,尺寸精度低。
封闭性好:
以图1-9为例。
工艺灵活性打、成本低。
铸铁材料具有减震、抗震性能和耐磨、润滑性能。
造型适应性强:
可制作比较复杂和变化不规则外形,造型适应性强:
可制作比较复杂和变化不规则外形,封闭性好,铸造成型的主要缺点:
铸造组织的晶粒比较粗大,且内部常有缩孔、缩松、气孔、砂眼等缺陷,力学性能一般不然锻件。
铸造生产工序繁多,工艺过程较难控制,废品率较高。
工作条件较差,劳动强度比较大。
二、铸造壳体、箱体常用材料铸铁:
铸铁流动性好,体收缩和线收缩小,容易获得形状复杂的铸件,在铸造时加入少量合金元素可提高耐磨性能。
铸铁分类:
灰铸铁、球墨铸铁、蠕墨铸铁、可锻铸铁。
铸造碳钢:
铸钢熔点高、流动性差、收缩率大,吸震性低于铸铁,弹性规模较大。
铝合金:
纯铝强度低、硬度小,因此,制造产品壳体常采用铝合金材料。
常用铝合金有:
铝硅合金、铝铜合金、铝镁合金、铝锌合金。
三、铸造工艺流程砂型铸造:
砂型铸造时应用最广泛的铸造方法,其生产过程如图1-10所示。
砂型的结构组成如图1-11所示。
砂型铸造有适应性强、生产简单等优点,但砂型铸造生产的铸件尺寸精度较低、表面粗糙、内在质量较差,且生产过程较复杂。
与砂型铸造比较,有以下几个特点:
铸件精度及表面质量高。
能够铸造各种合金铸件。
生产批量不受限制。
熔模铸件的形状可以比较复杂。
熔模铸件的重量不宜太大。
熔模铸造:
熔模铸造的工艺流程如图1-12所示。
与砂型铸造比较,金属铸造有以下的特点:
实现了“一型多铸”。
铸件的力学性能提高。
精度及表面质量高。
金属型的制造成本高、周期长;
铸型透气性差、无退让性,易产生冷隔、浇不足、裂纹等铸造缺陷。
金属型铸造:
用金属制成的铸造型腔,进行浇注获得铸件的铸造方法,如图1-13所示。
与砂型铸造比较,有如下优点:
铸件尺寸精度、表面质量高。
铸件的强度和表面硬度高。
可铸造形状复杂的薄壁铸件。
生产效率高。
压力铸造的缺点:
设备投资大,压型成本高。
压铸高熔点合金时,压型的寿命低。
压力铸造:
如图1-14所示,在高压下,使液态或半液态金属以较高的速度填充铸型的型腔,并在压力作用下凝固而获得铸件的方法。
离心铸造:
如图1-15所示,将液态合金浇入高速旋转的铸型中,使金属在离心力的作用下填充铸型并凝固成型。
与砂型铸造比较,有如下特点:
工艺过程简单,节约金属和其他原材料。
铸件组织致密,无缩孔、气孔、夹渣等缺陷,力学性能好。
铸造合金的种类不受限制。
铸件的内表面质量差,孔的尺寸不易控制。
四、铸造壳体、箱体结构设计,在设计铸造壳体、箱体结构时,除考虑壳体设计的总体要求与准则,还应重点结合铸造生产的工艺特点,考虑相关的工艺性。
在此,结合一些典型设计实例进行有关讨论。
铸造时处于水平位置,易造成气孔和夹渣,如图1-16所示。
尽量减少凹凸部分,简化制造工艺,如图1-17所示。
考虑出模工艺,应在结构上设计拔模斜度,包括内腔结构,如图1-18所示。
对于砂型铸造,尽量减少活块部分,简化制造工艺,如图1-19所示。
凸台距离分型面较近时,为避免使用活块,可将凸台延长至分型面或取消凸台,如图1-20所示。
如图1-21所示,修改一些局部结构,保证砂型牢固。
如图1-22图1-24所示,修改不合理凸台,达到保护砂型进而保证铸件质量的目的.,如图1-25、图1-26所示,修改结构避免使用型心或减少型心数量。
铸造零件一般存在一定内应力,经过一段时间,内应力消除,零件会产生一定变形,影响几何精度与使用性能,尺寸越大的铸件,影响越大。
一般铸件在机加工前,要经过一定处理。
铸铁铸件消除内应力的方法:
时效处理,热处理,机械振动法。
铸钢件一般都需要热处理。
壳体、箱体铸件的关键部位一般需要精加工。
主要部位包括:
壳体、箱体分离部分之间的连接部位。
壳体、箱体与内部零部件的定位与连接部位。
壳体、箱体与外部其他零部件的连接部位及地脚部位。
五、铸造零件的处理与加工,1.3、焊接壳体、箱体,一、焊接壳体、箱体的特点焊接壳体、箱体有以下特点:
适用范围广。
使用灵活。
生产周期短。
强度高。
焊接的主要缺点是:
造型能力较差。
加工精度较低。
焊接部位表面质量较差。
焊接产生一定的内应力,造成成品变形。
电弧焊:
利用电弧作为热源的熔焊方法,称为电弧焊。
手工电弧焊:
设备简单,使用灵活、方便、通用,但对操作人员的技能要求较高。
不适宜焊接活泼金属及难熔合低熔点金属。
埋弧自动焊:
利用连续送进的焊丝在焊剂层下产生电弧而自动进行焊接的方法,如图1-27、1-28所示。
埋弧自动焊的主要特点:
生产效率高,焊缝质量好,焊接规范自动控制。
适用于大批量生产,可焊接中、厚钢板(660mm)。
气体保护焊:
用外加气体作为电弧介质并保护电弧和焊接区的电弧焊。
保护气体主要有两种:
惰性气体(氩气和氮气)和活性气体(二氧化碳),其中氩弧焊,应用比较广泛。
二、焊接的方法与适用场合,埋弧自动焊,埋弧自动焊,电阻焊:
利用电流通过工件及焊接接触面间所产生的电阻热,将焊件加热至塑性或局部熔化状态,再施加压力形成焊接接头的焊接方法。
有点焊、缝焊、相对焊三种形式。
点焊:
其基本结构如图1-29所示,适用于焊接4mm以下薄板广泛用于汽车、飞机、电子、仪表和日常生活用品生产。
缝焊:
焊接厚度3mm以下的薄板搭接,主要应用于生产密封容器和管道等,如图1-30所示。
三、焊接壳体、箱体的设计,焊接结构材料的选择:
选用焊接性好的材料来制造焊接结构壳体、箱体。
含碳量低的碳钢和合金钢具有良好的焊接性。
焊接方法的选择:
根据材料的焊接性、工件厚度、生产率要求、各种焊接方法的适用范围和设备条件等综合考虑。
焊接接头工艺设计:
手工电弧焊接头基本形式有四种,如图1-31所示。
除搭接接头外,其余接头在焊件较厚时需开坡口。
坡口的基本形式如图1-32所示。
焊缝布置应遵循以下原则:
便于施焊:
焊缝设置必须具有足够的操作空间以满足焊接工艺需要。
如图1-33、1-34所示。
有利于减少焊接应力与变形:
尽量选用尺寸规格较大的板材、型材。
避开最大应力区和应力集中部位。
避开或远离机械加工面。
便于施焊,1.4、冲压壳体,一、冲压壳体的特点板料冲压制造产品壳体具有下列特点:
生产率高、操作简单。
产品质量好。
材料利用率高。
造型能力强适用广泛。
主要缺点:
集中在模具方面。
冲模设计、制造复杂,成本高,且一件一模,局部更改,也要更换模具。
小批量生产成本较高,图1-35的模型就是例子。
二、冲压工艺与模具,冲压设备主要有剪床和冲床两大类。
常用小型冲床的结构如图1-36所示。
冲压基本工序如图1-37所示。
冲压模具按冲床的每一次冲程所完成工序的多少划分为简单冲模、连续冲模及复合冲模。
简单冲模在冲床的一次冲程内只能完成一道工序。
如图1-38所示,简单冲模的结构简单,成本低,生产率低,主要用于简单冲裁件的生产。
连续冲模在冲床的一次冲程中,在模具的不同位置上可以同时完成两道以上的工序,如图1-39所示。
连续冲模生产率高,易于实现自动化,但结构复杂、成本高,适于大批量生产精度要求不高的中、小型零件。
复合冲模在冲床的一次冲程内,在模具的同一位置上可以同时完成两道以上的工序,如图1-40所示。
复合冲模生产效率高,零件加工精度高,但模具制造负责,成本高,适用于大批量生产。
在设计冲压壳体结构时,须综合考虑产品结构需要、零件结构强度、材料特性与成型能力、冲压模具复杂性及冲压工艺等因素。
如图1-41、1-42所示。
冲压壳体设计,往往易关注结构造型和功能,而忽视生产加工工艺,使得模具结构复杂、生产成本加大,特别是对于结构上需要弯曲和拉伸成型部分。
三、冲压零件的设计,板料弯曲时,内侧金属受切向压应力,产生压缩变形;
外层金属受切向拉应力,产生伸长变形。
当拉应力超过材料的抗拉强度时,即会造成金属破裂。
坯料厚度越大、弯曲半径越小,材料所受的内应力就越大,越容易弯裂,所以必须控制弯曲半径,通常取为板厚的0.25-1倍以上,材料塑性好时取下限。
弯曲时尽可能使弯曲线与坯料纤维方向垂直,如图1-43所示。
设计弯曲件时应加强变形部位的刚性,如图1-44所示。
在设计拉伸壳体时,应注意拉伸变形的影响,如图1-45所示。
1.5、注塑壳体、箱体,一、注塑壳体、箱体的特点注塑壳体、箱体有以下特点,如图1-46为例。
生产周期短,生产效率高,易于实现大批量、自动化生产。
可使用材料丰富,适应性强。
产品质量较高,一致性好、互换性强,成本低。
几何造型能力强,可生产现状、结构复杂的产品。
功能性与装饰性结合好。
明显的缺点:
注塑模具成本较高,不适于单件、小批量生产。
强度、表面硬度较低,扛冲击、磨损性能差,局部细小结构在维修过程易损坏。
材料存在老化问题,耐久性差。
二、注塑工艺与模具,典型注塑工艺过程如图1-47所示。
注塑模具在结构组成上是比较复杂的,按功能、作用分以下几个部分:
成型部分:
模具的核心部分,由可分合的两部分组成,类似于凸模和凹模。
浇注系统排溢、引起系统冷却系统脱模机构模架,三、注塑壳体、箱体设计,注塑壳体、箱体的结构设计应综合考虑产